Automatically translated by AI, read original
La qualité et le service sont les clés du succès sur le marché espagnol de l'électricité
11 juillet 2024

En 2022, Diesel Progress International, alors connue sous le nom de Diesel Progress International, a publié un rapport basé sur une tournée de plusieurs entreprises espagnoles du secteur des machines et de l'énergie. À cette époque, ces industries commençaient tout juste à émerger des effets de la pandémie de COVID-19 et des difficultés d'approvisionnement en pièces détachées liées aux confinements nationaux. Aujourd'hui, deux ans plus tard, Power Progress International est de retour en Espagne pour évaluer l'évolution du marché et découvrir les dernières technologies en développement.
Roquet Hydraulics , dont le siège social est situé à Tona, près de Barcelone, est spécialisé dans la conception et la production de pompes à engrenages, de vérins, de moteurs et de vannes pour systèmes hydrauliques destinés aux engins mobiles et aux applications agricoles. Dans ce cadre, l'entreprise dispose d'installations d'essais pour déterminer des paramètres tels que la fatigue des pièces et la résistance à la corrosion, tout en proposant des conseils sur les meilleures pratiques de fabrication.
À proximité du siège social de l'entreprise, l'usine de Centelles fabrique une large gamme de vérins pour applications hydrauliques. Exploitées sous la marque Dinacil (filiale du groupe Roquet), ces pièces sont utilisées dans les engins de chantier et agricoles, ainsi que dans de nombreuses autres applications industrielles.
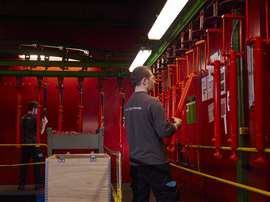
Toutes les pièces des cylindres sont produites en Europe par Roquet ; Dinacil possède une usine sœur en Roumanie qui produit également des cylindres. Dans ce contexte, il est surprenant d'apprendre que Roquet n'a aucun projet actuel, ni futur, de production en Chine.
« On entend souvent cette question sur les salons : "Fabriquez-vous les pièces en Chine ?" », explique Ruth Martinez, du service Ventes et Marketing. « [En Chine], ils ont de très grandes installations, des machines et du personnel. Mais tout ce que nous produisons est fabriqué en Europe et, dans la mesure du possible, en interne par Roquet. Nos concurrents fabriquent leurs pièces en Chine et la différence de prix est non négligeable. Nous misons donc sur la qualité de nos produits. »
L'accent mis sur la qualité est tel qu'il faut parfois jusqu'à deux ans pour commercialiser un nouveau modèle de cylindre. Une fois en production, un cycle de test complet garantit que chaque cylindre fini est prêt pour une longue durée de vie sur le terrain.
Roquet exploite également plusieurs entrepôts de pièces détachées dans le monde entier. Selon Martinez, ceux-ci contribuent à la livraison rapide des composants aux équipementiers, tout en améliorant le service client de l'entreprise. « Notre entrepôt en Thaïlande livre de nombreux clients locaux. De plus, en cas de problème sur un composant, nous pouvons rapidement l'identifier et trouver un remplacement. »
Roquet a récemment ouvert un bureau aux États-Unis. Si ce site permettra d'explorer de nouvelles opportunités, Arnau Bellapart, directeur du développement commercial, affirme que l'objectif principal est de soutenir les clients existants. Il précise que de nombreuses entreprises européennes implantées localement continuent d'utiliser les pièces Roquet et que le nouveau bureau permettra d'offrir le même niveau de support qu'en Europe.
« Nous devons être proches pour pouvoir répondre à tout problème ou conseiller sur les spécifications. Grâce à ce nouveau site, nous pourrons proposer les mêmes délais d'approvisionnement qu'en Europe », explique-t-il. À l'avenir, il est probable qu'une production limitée soit réalisée aux États-Unis, du moins pour les pièces de moindre personnalisation en volume.
À l'origine, Roquet n'était pas un fournisseur de composants. L'origine de l'entreprise remonte à une fonderie produisant des pièces pour d'autres fabricants de composants. Aujourd'hui, le site de fonderie fournit environ 30 % de sa production à Roquet, tandis qu'une grande partie de la capacité restante est destinée au marché plus large, notamment à d'autres fabricants de systèmes hydrauliques.
Qu'il s'agisse de volumes ou de personnalisation, la qualité reste le principal critère. « Nos vérins sont plus chers car nous y avons intégré des fonctionnalités de haute technologie. Mais nous devons maintenir la qualité, ce qui se traduit par la fiabilité, la capacité de nos composants à effectuer plus d'un demi-million de cycles sur chantier », explique Bellapart.
Service client
La qualité joue également un rôle clé dans la production de Dicsa , fournisseur spécialisé de flexibles et raccords hydrauliques. Située dans une zone industrielle près de Saragosse, l'entreprise ressemble à beaucoup d'autres du même secteur : ses entrepôts regorgent de pièces de toutes formes et de toutes tailles, prêtes à être expédiées.
La liste des fournisseurs de Dicsa est un véritable concentré de l'industrie hydraulique internationale. « Dans de nombreux cas, nous faisons office d'entrepôt pour nos clients », explique Pilar Marin, responsable médias. « Nous pouvons gérer leurs stocks et livrer les volumes de pièces nécessaires au fur et à mesure de leurs besoins. » Outre le site de Saragosse, qui dispose d'environ 20 000 mètres carrés d'espace d'entreposage, Dicsa exploite désormais des sites similaires en Italie, en Allemagne et aux États-Unis.
Dicsa fabrique également certains de ses propres raccords en acier inoxydable. Marin : « Nous avons toujours été très à l'écoute de nos clients. C'est pourquoi, dans les années 1990, face à des difficultés pour répondre à certaines demandes, nous avons démarré l'usine afin de pouvoir livrer les pièces dont nos clients avaient besoin. »
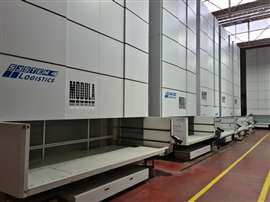
L'impression 3D permet de produire des prototypes, comme l'explique Sergio Miguel, chef de produit sur le site de Saragosse. « Avant de configurer une machine pour une production, nous pouvons livrer des échantillons validés par le client. Cela représente un gain de temps et d'argent considérable. » Les pièces sont personnalisables à tel point que même l'hélice d'un raccord fileté peut être modifiée pour s'adapter au mieux à l'application.
En passant par les halls de production, Miguel explique que chaque zone produit des pièces de même type et de même taille, ce qui réduit les temps de changement. « Selon la pièce et sa complexité, nous pouvons configurer la machine en environ trois heures », explique-t-il. « Une seule machine intègre une série de postes pour réaliser différents processus, jusqu'à la pièce finale. Nous disposons également d'opérations d'assemblage pour combiner différentes pièces ; certaines sont manuelles, d'autres entièrement automatisées. »
Miguel explique plus en détail les tests des pièces finales. « Nous utilisons généralement de l'acier 316L, une nuance à faible teneur en carbone essentielle à la longévité des pièces. Nous pouvons tester la nuance et la composition de l'acier grâce à un test d'étincelle. La machine projette une étincelle sur le matériau et l'onde produite peut être analysée pour déterminer la composition, le pourcentage de carbone, de chrome et d'autres éléments. »
Évolution du pouvoir
Un court voyage à travers la campagne ensoleillée qui entoure Saragosse nous amène à Carod , une entreprise qui se concentrait à l'origine sur les pompes motorisées pour l'agriculture et la protection contre les incendies, mais qui propose désormais une gamme de groupes électrogènes, de nettoyeurs haute pression et de compresseurs pneumatiques.
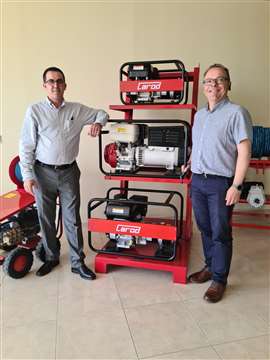
« L'usine d'origine se trouvait à environ 11 kilomètres d'ici, mais en 2011, nous avons acheté ce terrain et construit ce nouveau siège social », explique Mohamed Mohinah, responsable export. Il ajoute que si des pièces comme les fermetures en acier des groupes électrogènes sont actuellement livrées par des fournisseurs, il est prévu d'agrandir l'usine et de les produire en interne. « La COVID a été difficile pour nos fournisseurs et les délais de livraison ont atteint près d'un an. Nous allons donc mettre en place notre propre production pour éviter que cela ne se reproduise. »
Depuis l'achèvement de la nouvelle usine, Carod augmente régulièrement la puissance de ses générateurs. « Nous sommes passés d'environ 250 kVA à 800 kVA », explique Mohinah. « Nous avons des projets à venir, dont notre premier groupe électrogène de 1 MW. » Il ajoute que la production de Carod est répartie à environ 60 % pour les groupes électrogènes, les 40 % restants étant constitués de tous les autres produits.
L'énergie des générateurs provient de divers fournisseurs, dont Deutz, Volvo Penta, FPT, Honda et Kohler. Outre ces fournisseurs habituels, on retrouve MWM International, filiale du groupe Navistar, dont le siège social est à São Paulo, au Brésil. « Les moteurs MWM sont entièrement mécaniques, sans ordinateur. Cela les rend très fiables et très robustes. »
Autour de la salle d'assemblage, des étagères abritent des centaines de moteurs en boîte. Mohinah explique que leur stock de moteurs s'élève à plus de 6 millions de dollars. « C'est une autre conséquence de la COVID. Nous stockons des moteurs pour pouvoir honorer rapidement les commandes des clients. Si le moteur est en stock, je peux honorer une commande de groupe électrogène en quatre à six semaines environ. » Le stock comprend des moteurs Stage 2, 3 et 5 d'une puissance allant jusqu'à 500 kVA.
De l'autre côté du couloir, Mohinah me montre une pompe à eau haute pression récemment construite ; il s'agit d'une unité autonome équipée d'un moteur Deutz, d'une pompe, d'un réservoir de carburant, etc., le tout soigneusement rangé dans une remorque. « C'est pour un client ici en Espagne. Ces pompes servent à maîtriser les incendies, mais aussi à enlever les graffitis. C'est très courant ici. »
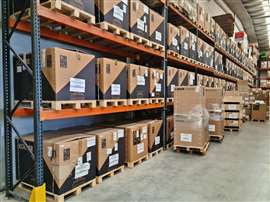
Développement technologique
L'Espagne possède une longue tradition de fabrication de machines pour la construction, l'agriculture, l'exploitation minière, les transports et la production d'énergie. Mais le pays abrite également une série d'instituts techniques et d'universités qui, en partenariat avec des agences gouvernementales et des groupes connexes, cherchent à développer de nouvelles technologies visant à améliorer l'efficacité opérationnelle de ces secteurs et d'autres.
Fondé en 1984, l'ITA (Instituto Tecnológico de Aragón) est un centre technologique basé à Saragosse. En collaboration avec le ministère de l'Économie, de l'Emploi et de l'Industrie du gouvernement d'Aragon, ses équipes travaillent sur des projets liés à la production d'énergie propre, à l'agroalimentaire numérique et à la mobilité durable.
À titre d'exemple, une équipe de l'ITA travaille sur le projet Ephyra, ou Production européenne d'hydrogène à partir d'énergies renouvelables. Ce projet prévoit l'intégration d'une usine de production d'hydrogène renouvelable de 30 MW à une raffinerie de Corinthe exploitée par Motor Oil of Hellas. L'hydrogène vert sera ainsi fourni à la raffinerie et à d'autres utilisateurs externes, testant ainsi l'économie circulaire de l'hydrogène.
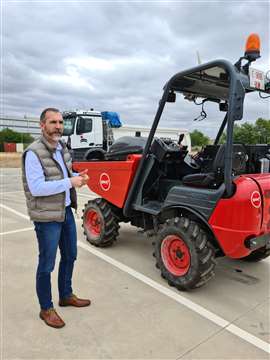
Tandis que le développement de ce mégaprojet se poursuit, ITA poursuit le développement de systèmes mécatroniques pour véhicules routiers et tout-terrain, comme l'explique Carlos Bernad, chef de projet R&D chez ITA : « Nous étudions l'intégration de la mécanique, de l'électronique et de la robotique dans les machines afin d'améliorer les fonctionnalités dans tous les domaines. Nous recherchons des synergies entre ces domaines, en nous concentrant sur la manière dont la mécatronique peut soutenir la robotique et vice versa. C'est une approche légèrement différente de la vision traditionnelle. »
Alors que les travaux se concentraient initialement sur l'amélioration des composants et des machines existants, Bernad explique qu'il s'implique dès le départ dans un projet qui permettra d'optimiser les fonctionnalités et les performances. Par exemple, un projet initialement axé sur la robotique a permis le développement de nouveaux capteurs et de logiciels associés, que l'ITA utilise désormais pour développer des systèmes à diverses fins.
Dans une zone d'essai extérieure, Bernad présente une série de machines d'essai, dont un tombereau et un camion de poids moyen. Chacune est équipée d'un système de conduite autonome spécifique, développé spécifiquement pour les environnements où les véhicules pourraient travailler.
Les systèmes de conduite autonome étant déjà disponibles pour ces véhicules, on demande à Bernad ce qui les différencie de ceux développés par l'ITA. « Ces systèmes ont été adaptés aux environnements difficiles et à des tâches spécifiques », explique-t-il avec un enthousiasme évident. « Grâce aux avancées en matière de capteurs et de puissance de calcul, ils peuvent traiter beaucoup plus de données, ce qui les rend plus efficaces. Cette capacité de données renforce également la sécurité des véhicules et leur permet de réagir aux situations dangereuses en prenant de meilleures décisions. Les nouveaux capteurs collectent les données, puis nos algorithmes les exploitent pour prendre les meilleures décisions. »
Nouvelles opportunités de marché
Après une nuit près de Pampelune, nous poursuivons notre périple jusqu'à Ibarra, petite ville située à environ 30 km au sud de Saint-Sébastien. Nous arrivons chezObeki , fabricant de moteurs électriques jusqu'ici principalement utilisés pour diverses applications de levage dans les secteurs de la construction, de la marine et autres.
« Entre 80 et 90 % de la production mondiale de moteurs électriques est réalisée dans des pays à bas coûts », explique Javier Múgica, directeur commercial. « Cela signifie qu'en Europe, l'activité repose principalement sur la logistique, l'entreposage et la distribution. Obeki n'intervient pas dans ces domaines ; nous proposons des solutions spécialisées avec des fonctionnalités non standard, comme des systèmes de freinage et un couple plus élevé. »
Dans ce cadre, Obeki cherche à accroître sa capacité de R&D, grâce à des conceptions de produits astucieuses favorisant de nouvelles opportunités commerciales. « Nous cherchons à développer des produits pour des clients exigeants, plus exigeants que ceux qui utilisent des moteurs électriques standard », explique-t-il.
Selon Múgica, Obeki produit environ 4 200 unités par an. « Ce n'est rien pour une entreprise chinoise », explique-t-il. Mais pour ces moteurs, l'entreprise développe environ 700 modèles uniques chaque année. « Une production de 10 moteurs n'est pas inhabituelle pour nous, même si certains clients pourraient même n'en vouloir qu'un seul. »
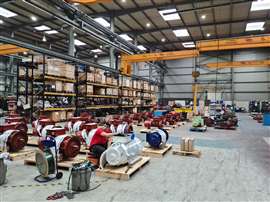
Cette personnalisation présente deux avantages. Premièrement, le moteur est spécifique à l'usage auquel il est destiné, ce qui signifie qu'il est parfaitement adapté à l'application – et garanti comme tel. De plus, en cas de problème, Obeki garantit chaque moteur qu'il produit. « En cas de problème, les grandes entreprises essaieront simplement de vous vendre un autre moteur. Nous économiserons du temps et de l'argent, dans la mesure du possible, en réparant le moteur déjà en place. »
Fort de cette expertise, Múgica affirme que la prochaine étape consiste à élargir le nombre de marchés utilisant les moteurs Obeki. « Nous travaillons actuellement sur des projets de captage d'énergie renouvelable des océans. Nos moteurs font partie de systèmes qui captent l'énergie des vagues. » Cela nécessite non seulement un rendement moteur optimal (basé sur le choix des matériaux et la conception) pour minimiser les pertes d'énergie, mais aussi des conceptions robustes capables de résister aux conditions difficiles.
Ces systèmes de collecte d'énergie sont encore au stade de prototype. Cependant, grâce aux recherches menées sur cette technologie en Espagne, au Royaume-Uni et en Australie (entre autres), l'objectif est de créer un réseau d'entreprises capables de fournir régulièrement les composants nécessaires.
Sur cette base, Múgica explique qu'Obeki prévoit de fournir des moteurs pour des applications soumises à des conditions encore plus extrêmes. « Les centrales nucléaires sont équipées de moteurs alimentant diverses fonctions, de ventilateurs et de pompes pour les systèmes de refroidissement, etc. Si ces moteurs sont situés à proximité du réacteur, ils doivent être certifiés pour résister à diverses conditions, comme un tremblement de terre, et utiliser des matériaux résistants à la radioactivité. Nous souhaitons participer au développement de moteurs sophistiqués pour ce type d'application. »
Des défis demeurent
Alors que la Chine est devenue le premier pays mondial à produire en volume des machines et des composants, les entreprises européennes des mêmes secteurs d'activité ont été contraintes de trouver des arguments de vente uniques au-delà du simple faible coût pour attirer et fidéliser leurs clients.
Ces visites montrent clairement que les défis posés par la COVID et les difficultés d'approvisionnement qui en ont résulté touchent à leur fin ; dans un cas au moins, un stock plus important sert désormais de tampon de production. Mais si les effets de la pandémie s'estompent, de nouveaux défis nécessiteront une surveillance constante et la mise en œuvre de solutions agiles.
Dans chacun des cas décrits dans cet article, de Roquet à Obeki, les entreprises ont réussi à maintenir (ou à accroître) leur part de marché en s'appuyant sur l'expertise requise dans un domaine d'activité spécifique, qu'il s'agisse de la qualité, de la personnalisation ou du service client.
Il est évident qu'il existera toujours un marché pour des solutions économiques. Mais lorsqu'une pièce est nécessaire dans les plus brefs délais, que la qualité (et la disponibilité garantie) sont essentielles, ou qu'une nouvelle solution doit être développée pour une application spécifique, une entreprise plus réactive est probablement le meilleur choix.
Cet article a été réalisé avec le soutien de l'ICEX , l'Institut espagnol du commerce extérieur, et de l'ANMOPYC , l'organisation représentative en Espagne des entreprises fournissant des technologies pour les secteurs de la construction et des mines.

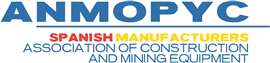
POWER SOURCING GUIDE
The trusted reference and buyer’s guide for 83 years
The original “desktop search engine,” guiding nearly 10,000 users in more than 90 countries it is the primary reference for specifications and details on all the components that go into engine systems.
Visit Now
STAY CONNECTED



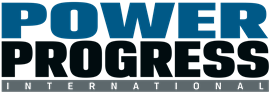
Receive the information you need when you need it through our world-leading magazines, newsletters and daily briefings.
CONTACTEZ L'ÉQUIPE
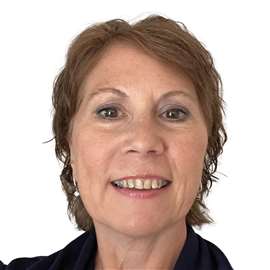
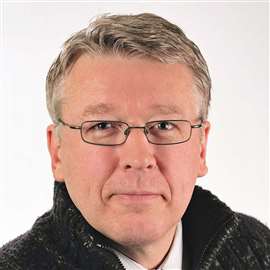
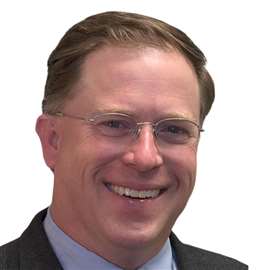
