Read this article in French German Italian Portuguese Spanish
An electric equipment battery primer, part 3: choosing the right battery
23 July 2024
Editor’s Note: the following was contributed as an exclusive to Power Progress by battery manufacturer EnerSys, Reading, Pa., and edited for length and style. It is part of a three-part series from EnerSys on understanding battery technology for electric equipment and vehicles.
As internal combustion engine (ICE)-powered equipment comes under increasing scrutiny due to emissions concerns, fluctuating fuel prices and maintenance concerns, companies are switching to electric power for industrial vehicles, such as forklifts and floor care equipment. There are several battery options today that serve different application needs, from traditional lead acid to the more advanced thin plate lead acid (TPPL) and lithium-ion batteries.
A well-matched battery technology and charging system will optimize a fleet’s potential by maximizing productivity, reducing maintenance and eliminating unplanned downtime. Choosing the right one requires careful measurement of data and consideration of several operational factors.
Matching Energy Capabilities
While there are several attributes to examine when choosing the optimal battery, energy capabilities — including capacity and recharge efficiency — are core to the overall evaluation. This becomes increasingly important as applications migrate toward 24/7/365 operation, which reduces available charging time to a point at which the only option is charging during brief worker breaks. Such opportunity charging makes the overall efficiency and speed of the charging activity even more critical.
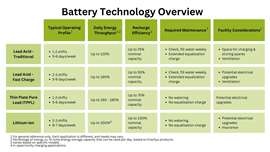
Most traditional lead acid batteries are designed to require an extended period for them to charge and cool — one that can take several hours. This makes them impractical for most opportunity charging applications. In the past, users addressed this shortcoming by maintaining multiple batteries for each piece of equipment, changing them out as they became depleted during shifts.
However, such an approach has become impractical with the advent of TPPL and lithium-ion technologies, which are designed specifically for opportunity charging. Both can be plugged in whenever the equipment is not in use, such as during breaks, between shifts and at other periods of downtime.
Aligning Life Expectancies
Just as different kinds of equipment have different life expectancies, so do different battery technologies, which is further complicated by how the equipment is used and, particularly in the case of flooded lead acid batteries, how well the battery is maintained. The longevity of the selected battery should align as closely as possible with that of the equipment.
For instance, a traditional flooded lead acid battery has a typical useful life of 3 - 6 years. The fast-charge varieties have an average useful life of 2 - 4 years. The typical life expectancy of a TPPL battery is 4-5 years, depending on how intensely it is used, and lithium-ion batteries can last 5-7 years depending upon usage.
While many approach battery life in terms of the frequency of battery replacement, there’s also little sense in overpaying for a battery that will outlast an equipment lease or the expected lifetime of the equipment.
Tolerance for Maintenance
Battery maintenance can also be a significant concern for applications having little or no scheduled downtime or those with either high worker turnover or inexperienced operators.
Lead acid batteries typically require a high level of maintenance. Water must be added weekly to the appropriate level, for instance, and they must be regularly equalized to remove sulfate crystals that can build up over time. If they are not properly maintained, they will likely have a shorter life and need to be replaced more frequently.
By contrast, TPPL and most lithium-ion batteries require no maintenance at all.
Facility Implications
There are a few considerations in battery selection when it comes to facilities. The first is space, mostly if the operation is choosing traditional flooded lead acid batteries and the application’s power demands require multiple batteries for each piece of equipment. Flooded lead acid batteries require large, dedicated spaces for charging, storage and maintenance, meaning less space for other items or operations.
Another factor is electrical infrastructure. More advanced, faster opportunity charging technologies may require investment in facility electrical upgrades to deliver the volume of charging power required if opportunity charging is the only option.
Regarding lithium-ion batteries, insurance can also be a consideration. Many facility insurance companies require additional riders, premiums or inspections prior to providing coverage for operations using lithium-ion batteries. This is due to some safety concerns, particularly with poorly designed lithium-ion batteries or those with questionable battery management systems (BMS). Be sure to check with your insurance company prior to committing to lithium-ion batteries.
Leveraging Power Data
While several factors affect the choice of an optimal battery technology and charger system, it’s crucial to determine your power needs. With the advancement of battery technology, this has become a complex exercise due to the many variables and options. Traditional hand calculations and spreadsheets no longer suffice for a thorough evaluation.
The best approach is to capture actual power usage and other data from fleet equipment instead of using anecdotal or estimated numbers. Battery monitoring devices can collect information such as energy usage, charging intervals and other critical measures to provide a full picture of an application’s energy demands.
But this is just the start. Entering equipment energy data into an advanced simulation modeling system allows comparisons of various battery and charger technologies. This can provide a full evaluation — facilitating true optimization of your equipment energy solution based on actual fleet data, not estimates or assumptions. Certain simulation programs can also model future changes in facility throughput, cost factors and other information crucial to making the right decision for your operations.
POWER SOURCING GUIDE
The trusted reference and buyer’s guide for 83 years
The original “desktop search engine,” guiding nearly 10,000 users in more than 90 countries it is the primary reference for specifications and details on all the components that go into engine systems.
Visit Now
STAY CONNECTED



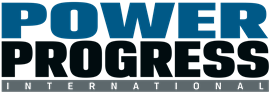
Receive the information you need when you need it through our world-leading magazines, newsletters and daily briefings.
CONNECT WITH THE TEAM
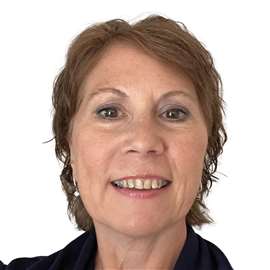
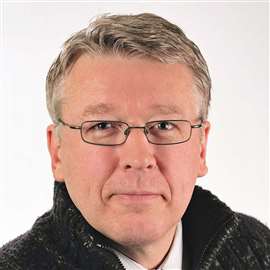
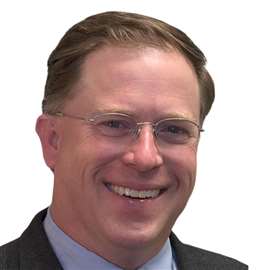
