Traducido automáticamente por IA, leer el original
La calidad y el servicio son claves del éxito en el mercado eléctrico español
11 julio 2024

En 2022, la entonces Diesel Progress International publicó un informe basado en una visita a varias empresas de maquinaria y energía en España. En aquel momento, estas industrias apenas comenzaban a recuperarse de los efectos de la pandemia de COVID y los problemas de suministro de piezas derivados de los confinamientos nacionales. Ahora, dos años después, Power Progress International ha regresado a España para analizar el rendimiento del mercado, aprovechando la oportunidad para conocer algunas de las últimas tecnologías en desarrollo.
Roquet Hydraulics , con sede en Tona, cerca de Barcelona, se especializa en el diseño y la producción de bombas de engranajes, cilindros, motores y válvulas para sistemas hidráulicos utilizados en maquinaria móvil y aplicaciones agrícolas. Para ello, la empresa cuenta con instalaciones de prueba para determinar problemas como la fatiga de las piezas y la resistencia a la corrosión, además de ofrecer asesoramiento sobre las mejores prácticas de fabricación.
Cerca de la sede de la empresa, una planta en Centelles fabrica una amplia gama de cilindros para aplicaciones hidráulicas. Operados bajo la marca Dinacil (parte del portafolio de la empresa Roquet), los componentes se utilizan en maquinaria de construcción y agrícola, además de en otras aplicaciones industriales.
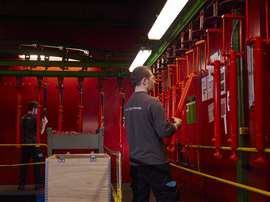
Todas las piezas de los cilindros son fabricadas en Europa por Roquet; Dinacil cuenta con una planta hermana en Rumanía que también produce cilindros. Por ello, resulta sorprendente saber que Roquet no tiene planes actuales ni futuros de iniciar la producción en China.
“En las ferias comerciales nos preguntan constantemente: '¿Fabrican las piezas en China?'”, dice Ruth Martínez, del departamento de Ventas y Marketing. “En China tienen instalaciones muy grandes, la maquinaria y el personal necesarios. Pero todo lo que producimos se fabrica en Europa y, siempre que es posible, Roquet lo fabrica internamente. La competencia fabrica sus piezas en China y la diferencia de precio es considerable, así que nos basamos en la calidad de nuestros productos”.
La atención a la calidad es tal que puede tardar hasta dos años en comercializar un nuevo diseño de cilindro. Una vez en producción, un ciclo de pruebas del 100 % garantiza que cada cilindro terminado esté listo para una larga vida útil en el campo.
Roquet también opera varios almacenes de piezas en todo el mundo. Según Martínez, estos ayudan a garantizar la entrega puntual de componentes a los fabricantes de equipos originales (OEM), además de contribuir al servicio al cliente de la empresa. "Si nos fijamos en nuestro almacén en Tailandia, vemos que realiza entregas a muchos clientes locales. Pero también nos ayuda a que, si un componente en el campo presenta un problema, podamos identificarlo y conseguir un reemplazo rápidamente".
Roquet ha abierto recientemente una oficina en Estados Unidos. Si bien la ubicación buscará nuevas oportunidades, Arnau Bellapart, director de Desarrollo de Negocio, afirma que el objetivo principal es dar soporte a los clientes existentes. Afirma que muchas empresas europeas con operaciones locales han seguido utilizando componentes Roquet y que la nueva oficina contribuirá a ofrecer el mismo nivel de soporte que en Europa.
“Necesitamos estar cerca para poder resolver cualquier problema o asesorar sobre las especificaciones. Con esta nueva ubicación, podremos ofrecer el mismo calendario de suministro que en Europa”, explica. De cara al futuro, es probable que se realice una producción limitada en EE. UU., al menos para piezas de volumen menos personalizadas.
Roquet no era originalmente un proveedor de componentes. Los orígenes de la empresa se remontan a una fundición que producía piezas para otros fabricantes. Actualmente, la fundición suministra aproximadamente el 30 % de su producción a Roquet, mientras que gran parte de la capacidad restante se ofrece al mercado en general, incluyendo a otros fabricantes de sistemas hidráulicos.
Ya sea por volumen o por encargo, la calidad sigue siendo el factor clave. «Nuestros cilindros son más caros porque hemos integrado características de alta tecnología. Pero, a pesar de ello, debemos mantener la calidad, lo que se traduce en fiabilidad, la capacidad de nuestros componentes para completar más de medio millón de ciclos en la obra», afirma Bellapart.
Atención al cliente
La calidad también es fundamental en la producción de Dicsa , proveedor especializado en mangueras y accesorios hidráulicos. Ubicada en un polígono industrial cerca de Zaragoza, la empresa es similar a muchas del mismo sector, con almacenes repletos de piezas de todas las formas y tamaños imaginables, listas para su envío.
La lista de proveedores que abastecen a Dicsa es un completo catálogo de productos hidráulicos internacionales. "En muchos casos, actuamos como almacén para nuestro cliente", afirma Pilar Marín, directora de medios. "Podemos gestionar su stock y entregar los volúmenes de piezas cuando los necesiten". Además de la planta de Zaragoza, que cuenta con aproximadamente 20.000 metros cuadrados de espacio de almacenamiento, Dicsa también opera en ubicaciones similares en Italia, Alemania y Estados Unidos.
Dicsa también fabrica algunos de sus propios accesorios de acero inoxidable. Marin: «Siempre hemos estado muy orientados al cliente. Así que en la década de 1990, cuando tuvimos problemas para satisfacer algunos pedidos, abrimos la fábrica para poder entregar las piezas que nuestros clientes necesitaban».
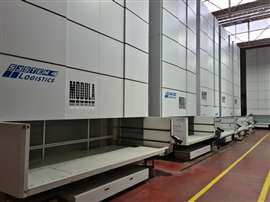
La impresión 3D se utiliza para producir prototipos, como explica Sergio Miguel, responsable de producto en la planta de Zaragoza. «Antes de preparar una máquina para la producción, podemos entregar muestras aprobadas por el cliente. Esto ahorra mucho tiempo y dinero». Las piezas se pueden personalizar hasta tal punto que incluso la hélice de un racor puede modificarse para adaptarla mejor a la aplicación.
Al pasar a las naves de producción, Miguel comenta que cada área produce piezas del mismo tipo y tamaño, lo que ayuda a reducir los tiempos de cambio. «Dependiendo de la pieza y su complejidad, podemos configurar la máquina en unas tres horas», explica. «Una sola máquina incorpora una serie de estaciones para completar diferentes procesos, dando como resultado el componente final. También contamos con operaciones de ensamblaje para combinar diferentes piezas; algunas son manuales, otras están 100 % automatizadas».
Miguel explica más sobre las pruebas de las piezas finales. «Generalmente utilizamos acero 316L, ya que este grado bajo en carbono es fundamental para la longevidad de la pieza. Podemos probar el grado y la composición del acero mediante una prueba de chispa. La máquina dispara una chispa al material y la onda resultante se puede analizar para determinar la composición, el porcentaje de carbono, cromo y otros elementos».
Evolución del poder
Un breve viaje a través de los soleados campos que rodean Zaragoza nos lleva a Carod , una empresa que originalmente se centró en bombas eléctricas para agricultura y protección contra incendios, pero que ahora ofrece una gama de grupos electrógenos, hidrolimpiadoras y compresores neumáticos.
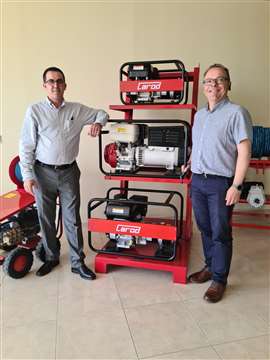
“La planta original estaba a unos 11 kilómetros de aquí, pero en 2011 compramos este terreno y construimos esta nueva sede”, explica Mohamed Mohinah, gerente de exportaciones. Añade que, si bien piezas como los cierres de acero de los grupos electrógenos son suministradas actualmente por proveedores, hay planes para ampliar las instalaciones y producirlas internamente. “La COVID-19 afectó gravemente a nuestros proveedores y los plazos de entrega se incrementaron a casi un año. Por lo tanto, estableceremos nuestra propia producción para evitar que se repita la situación”.
Desde la finalización de la nueva fábrica, Carod ha aumentado progresivamente la potencia de sus generadores. "Hemos pasado de unos 250 kVA a 800 kVA", afirma Mohinah. "Tenemos proyectos en marcha, entre ellos nuestro primer grupo electrógeno de 1 MW". Añade que la producción en Carod se divide en un 60 % de grupos electrógenos, y el 40 % restante corresponde a los demás productos.
La energía para los generadores proviene de diversos proveedores, como Deutz, Volvo Penta, FPT, Honda y Kohler. Además de estos proveedores habituales, se encuentra MWM International, parte del Grupo Navistar, con sede en São Paulo, Brasil. «Los motores MWM son completamente mecánicos, sin computadoras. Eso los hace muy fiables y robustos».
Alrededor de la sala de ensamblaje, las estanterías albergan cientos de motores en caja. Mohinah afirma tener un inventario de motores de más de 6 millones de dólares. "Es otra consecuencia de la COVID-19. Mantenemos los motores para poder atender rápidamente los pedidos de los clientes. Si el motor está en stock, puedo atender un pedido de grupo electrógeno en unas cuatro a seis semanas". El inventario incluye motores de las etapas 2, 3 y 5 con potencias de hasta 500 kVA.
Al otro lado del pasillo, Mohinah señala una bomba de agua de alta presión recién terminada; es una unidad autónoma que utiliza un motor Deutz, una bomba, un depósito de combustible, etc., todo perfectamente alojado en un remolque. "Esto es para un cliente aquí en España. Se usan para controlar incendios, pero también para borrar grafitis. Es muy común aquí".
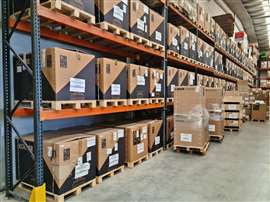
Desarrollo tecnológico
España cuenta con una larga trayectoria en la fabricación de maquinaria para la construcción, la agricultura, la minería, el transporte y la generación de energía. Sin embargo, el país también alberga una serie de institutos técnicos y universidades que, en colaboración con organismos gubernamentales y grupos afines, buscan desarrollar nuevas tecnologías destinadas a mejorar la eficiencia operativa en estas y otras industrias.
Fundado en 1984, el ITA (Instituto Tecnológico de Aragón) es un centro tecnológico con sede en Zaragoza. En colaboración con el Departamento de Economía, Empleo e Industria del Gobierno de Aragón, sus equipos trabajan en proyectos relacionados con la producción de energía limpia, la agroindustria digital y la movilidad sostenible.
En uno de estos casos, un equipo del ITA trabaja en el proyecto Ephyra, o Producción Europea de Hidrógeno a partir de Energías Renovables. Este proyecto consistirá en una planta de producción de hidrógeno renovable de 30 MW integrada en una refinería en Corinto, operada por Motor Oil of Hellas. Esto suministrará hidrógeno verde a la refinería y a otros usuarios externos como prueba de la economía circular del hidrógeno.
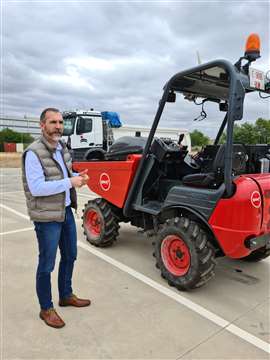
Mientras continúa el desarrollo de este megaproyecto, ITA continúa desarrollando sistemas mecatrónicos para vehículos de carretera y todoterreno, como explica Carlos Bernad, director de proyectos de I+D de ITA: «Estamos estudiando la integración de la mecánica, la electrónica y la robótica en las máquinas con la intención de mejorar la funcionalidad en todas las áreas. Buscamos sinergias entre estos campos, centrándonos en cómo la mecatrónica puede apoyar a la robótica y viceversa. Es un enfoque ligeramente diferente a la perspectiva estándar».
Si bien el trabajo se centró inicialmente en mejorar los componentes y máquinas existentes, Bernad afirma que desde el principio se ha involucrado en un proyecto que contribuirá a maximizar las ventajas en términos de funcionalidad y rendimiento. Por ejemplo, un proyecto inicialmente centrado en la robótica dio lugar al desarrollo de nuevos sensores y software relacionado, que ITA ha utilizado para desarrollar sistemas con diferentes propósitos.
En un área de pruebas exterior, Bernad presenta una serie de máquinas de prueba, incluyendo un volquete y un camión de carga media. Cada una cuenta con un sistema de conducción autónoma diferente, desarrollado específicamente para los entornos donde podrían operar los vehículos.
Con sistemas de conducción autónoma ya disponibles para estos vehículos, se le pregunta a Bernad qué diferencia hay con los desarrollados por ITA. «Estos sistemas se han adaptado a entornos hostiles y tareas específicas», afirma con evidente entusiasmo. «Con los nuevos avances en sensores y potencia computacional, pueden procesar muchos más datos, lo que los hace más eficientes. La capacidad de datos también hace que los vehículos sean más seguros, ya que pueden reaccionar ante situaciones peligrosas con una mejor toma de decisiones. Los nuevos sensores recopilan los datos y nuestros algoritmos utilizan esa información para tomar la mejor decisión».
Nuevas oportunidades de mercado
Tras una parada nocturna cerca de Pamplona, nos dirigimos a nuestra última parada del tour en Ibarra, un pequeño pueblo a unos 30 km al sur de San Sebastián. Aquí llegamos aObeki , fabricante de motores eléctricos que, hasta ahora, se han utilizado principalmente en diversas aplicaciones de elevación en los sectores de la construcción, la marina y otros.
“Entre el 80 % y el 90 % de la producción mundial de motores eléctricos se realiza en países de bajo coste”, afirma Javier Múgica, director comercial. “Eso significa que, en Europa, el negocio se basa principalmente en la logística, el almacenamiento y la distribución. Obeki no participa en eso; en cambio, ofrecemos soluciones especializadas con características no estándar, como sistemas de frenos y mayor par motor”.
Como parte de esto, Obeki busca aumentar su capacidad de I+D, con diseños de productos inteligentes que impulsen nuevas oportunidades de negocio. «Buscamos desarrollar productos para clientes exigentes con requisitos más exigentes que los que utilizan motores eléctricos estándar», afirma.
Según Múgica, Obeki produce unas 4200 unidades al año. «Esto no es nada para una empresa china», explica. Pero para esos motores, la empresa desarrolla unos 700 diseños únicos cada año. «Producir 10 motores no es inusual para nosotros, aunque algunos clientes podrían incluso querer solo una unidad».
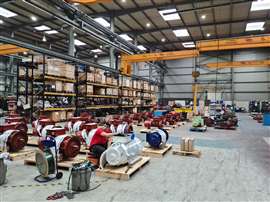
Esta personalización tiene dos ventajas. Primero, el motor es específico para su propósito previsto, lo que significa que es ideal para la aplicación y está garantizado como tal. Además, si surge algún problema, Obeki respalda cada motor que produce. «Si surge un problema, las grandes empresas solo intentarán venderte otro motor. Ahorraremos dinero y tiempo, siempre que sea posible, reparando el motor ya instalado».
Basándose en esta experiencia, Múgica afirma que el siguiente paso es ampliar el número de mercados que utilizan los motores Obeki. «Actualmente trabajamos en proyectos que capturan energía renovable de los océanos. Nuestros motores forman parte de sistemas que recogen la energía de las olas». Esto requiere no solo la máxima eficiencia del motor (basada en la elección de materiales y el diseño) para minimizar la pérdida de energía, sino también diseños robustos que puedan soportar las duras condiciones.
Estos sistemas de captación de energía aún se encuentran en fase de prototipo. Sin embargo, con las investigaciones sobre esta tecnología en curso en España, el Reino Unido y Australia (entre otros países), el objetivo es crear una red de empresas capaces de suministrar regularmente componentes relacionados.
Basándose en esto, Múgica afirma que Obeki tiene planes para proporcionar motores para aplicaciones en condiciones aún más extremas. «Las centrales nucleares tienen motores que impulsan diversas funciones, ventiladores y bombas para los sistemas de refrigeración, etc. Si están cerca del reactor, deben estar certificados para resistir diversas circunstancias, como un terremoto, y utilizar materiales que no se descompongan debido a la radiactividad. Nos gustaría participar en el desarrollo de motores sofisticados para este tipo de aplicación».
Aún quedan desafíos
A medida que China ha ido creciendo como el principal lugar mundial para la producción en volumen de máquinas y componentes, las empresas europeas en los mismos sectores comerciales se han visto obligadas a encontrar propuestas de venta únicas más allá de los bajos costos básicos para atraer y retener a los clientes.
En estas visitas, se hace evidente que los desafíos que presentó la COVID-19 y los consiguientes problemas en la cadena de suministro están llegando a su fin; al menos en un caso, un mayor inventario sirve ahora como colchón de producción. Sin embargo, mientras los efectos de la pandemia se disipan, los nuevos desafíos requerirán un seguimiento constante y la implementación de soluciones ágiles.
En cada uno de los casos descritos en este artículo, desde Roquet hasta Obeki, las empresas han logrado mantener (o aumentar) su participación en el mercado aprovechando la experiencia necesaria en un área comercial específica, ya sea calidad, personalización o servicio al cliente.
Es obvio que siempre habrá mercado para soluciones económicas. Pero cuando se necesita una pieza lo antes posible, la calidad (y la garantía de disponibilidad) son imprescindibles, o se necesita desarrollar una nueva solución para una aplicación específica, una empresa con mayor capacidad de respuesta probablemente sea la mejor opción.
Este artículo ha sido elaborado con el apoyo de ICEX , el Instituto Español de Comercio Exterior, y ANMOPYC , la organización representativa en España de las empresas proveedoras de tecnologías para las industrias de la construcción y la minería.

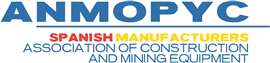
POWER SOURCING GUIDE
The trusted reference and buyer’s guide for 83 years
The original “desktop search engine,” guiding nearly 10,000 users in more than 90 countries it is the primary reference for specifications and details on all the components that go into engine systems.
Visit Now
STAY CONNECTED



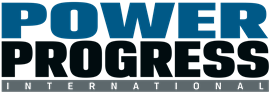
Receive the information you need when you need it through our world-leading magazines, newsletters and daily briefings.
CONECTE CON EL EQUIPO
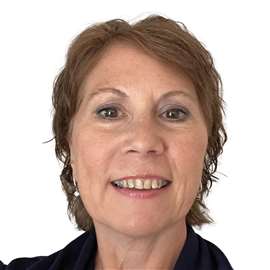
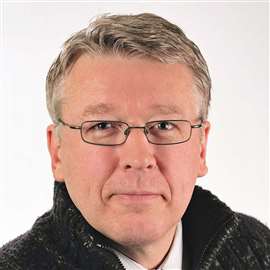
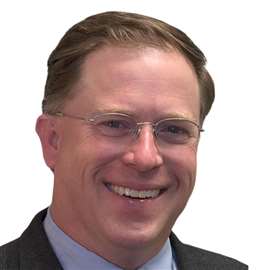
