Automatically translated by AI, read original
Stapleton : les giga-usines de batteries ne sont pas toujours le bon choix
15 juillet 2025
Pour la fabrication de batteries destinées aux véhicules et équipements électriques à batterie (VE), il existe des usines et des giga-usines. Ces dernières, comme leur nom l'indique, sont des installations gigantesques conçues pour produire plusieurs gigawattheures (GWh) de batteries par an, souvent de type lithium-ion.
Les giga-usines modernes peuvent dépasser les 100 GWh de production chaque année, une grande partie de cette capacité étant destinée à alimenter le secteur des véhicules électriques en pleine croissance.
Aux États-Unis, on peut citer la Gigafactory Nevada de Tesla et la BlueOval City de Ford dans le Tennessee. Northvolt Ett en Suède et la Gigafactory de CATL en Allemagne comptent parmi les plus grands sites de production d'Europe.
Pas toujours adapté
« Les gigafactories sont importantes », a déclaré Alex Stapleton, directeur commercial d'Alexander Battery Technologies, fabricant britannique de batteries sur mesure pour les équipementiers. « Elles sont un indicateur important de la destination des investissements, des flux de trésorerie et de la réalisation des projets. »
Cependant, Stapleton a déclaré que l'échelle qu'ils fournissent n'est pas nécessairement appropriée pour de nombreux équipementiers commerciaux et constructeurs automobiles.
« Si l'on parle d'automobile de premier plan ou autre, ces entreprises sont parfaitement préparées et c'est ce qu'elles cherchent à faire », a-t-il déclaré. « Mais ce sont des projets qui s'étendent sur plusieurs années. Ils se disent : « Démarrons la production vers 2030, environ », et ils planifient tout en conséquence. »
Cependant, pour les équipementiers qui produisent entre 1 000 et 5 000 véhicules par an, notamment compte tenu de leurs prix souvent à six chiffres, le modèle de gigafactory n'est souvent pas approprié.
« Cela implique de s'enfermer dans des formats de cellules spécifiques, de respecter des calendriers de production et des programmes à long terme », a déclaré Stapleton. « Cela accroît probablement le risque. »
La flexibilité et la personnalisation sont importantes
Les équipementiers commerciaux et les constructeurs automobiles ont également des besoins uniques qu’une gigafactory ne peut pas répondre efficacement.
« Souvent, ils ont besoin de plus de flexibilité, de plus de personnalisation, d'un délai d'exécution plus rapide », a déclaré Stapleton, « d'une piste d'accès plus facile, je dirais, à leurs projets que ce que permet ce type de modèle de gigafactory. »
Il a ajouté : « Je pense que le modèle des giga-usines soutient véritablement l'offre et ne s'attaque pas vraiment à la demande, là où un soutien est réellement utile. Ces entreprises ont besoin d'un soutien technique sérieux, sans les frais généraux ni les prévisions d'échelle qui accompagnent ces programmes automobiles. »
L'avantage du sur mesure
C'est ce qui, selon Stapleton, incite de nombreux équipementiers à envisager des batteries sur mesure pour leurs équipements. Pour les équipements et véhicules électrifiés, peu de composants sont aussi essentiels que la batterie.
« En prenant le temps et le soin de travailler sur cette batterie, vous apporterez presque certainement de la valeur à votre client final », a-t-il déclaré.
Stapleton a ajouté : « Avec des applications à plus petit volume, je pense qu'il y a une croissance parce que les gens veulent accéder à cette différenciation.
Processus clair
Pour les OEM souhaitant développer des batteries pour leurs produits, Alexander Battery Technologies a développé un processus robuste destiné à aider les clients à relever les défis.
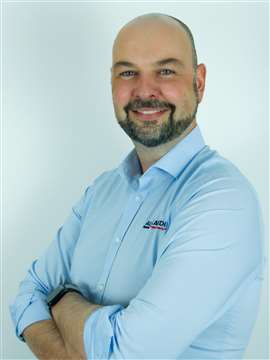
« L'écouteur sans fil est très différent du véhicule, mais les principes restent les mêmes », a déclaré Stapleton. « Notre processus d'ingénierie est très rigoureux et structuré en étapes. »
Il a expliqué que la première tâche à accomplir est d’élaborer de manière collaborative un champ d’action.
« Cela permet d'établir une documentation complète dès le début du projet, comprenant toutes les contributions du client, ses spécifications et ses objectifs », explique Stapleton. « Nous étudions ensuite les aspects réglementaires, la conformité et tout ce qui doit être pris en compte dans ce processus. »
Selon Stapleton, la phase de documentation des batteries de véhicules et d’équipements peut prendre du temps.
« Si le projet est entièrement nouveau, un délai de 18 mois à deux ans n'est pas irréaliste en termes de documentation », a-t-il déclaré. « Car les sujets sont vastes – la sécurité fonctionnelle, par exemple, est un enjeu crucial pour ce type de batteries – et les exigences en matière de documentation sont extrêmement élevées. »
Bien que Stapleton ait déclaré que la documentation est la partie la plus difficile du processus, le résultat est une liste de livrables qui répondent aux étapes et aux indicateurs clés.
« Ils bénéficient d'un lancement très transparent, auquel toute notre équipe est présente », a déclaré Stapleton. « Ils rencontrent tous les acteurs du projet en amont, et leurs échanges sont documentés pour savoir qui sont les personnes impliquées. »
Répétabilité vs. Nouveauté
Compte tenu du travail d'Alexander Battery Technologies dans le domaine des batteries sur mesure pour véhicules, Stapleton a déclaré que parfois le processus de documentation peut être rationalisé grâce à leur expérience antérieure.
« Ces batteries ont un principe directeur : elles seront probablement modulaires, nécessiteront un bus CAN et une gestion thermique », a-t-il déclaré. « Il y aura certainement des éléments reproductibles. »
Cependant, certains aspects nouveaux des batteries ne peuvent être prédits.
« Nous avons découvert de nouvelles technologies avec de nouvelles chimies, comme des batteries contenant des composants comme l'oxyde de titanate de lithium », a déclaré Stapleton. « Nous avons récemment réalisé un eVTOL (décollage et atterrissage verticaux) – une innovation incontestable. Le processus doit donc être conçu pour répondre à la question suivante : "Comment concevoir un appareil parfait à chaque fois ?" La réponse n'est pas simple. »
Soutien politique nécessaire
Stapleton a déclaré qu'il espérait que les politiques du monde entier accorderaient davantage d'attention aux fournisseurs de batteries qui ne font pas partie du modèle des gigafactory.
« Il existe une sorte de classe moyenne du design, des batteries, des équipementiers et de tout le reste, qui pèse des milliards – ce n'est pas une petite industrie – et qui nécessite également une politique ciblée », a-t-il déclaré. « Et pas seulement au niveau des giga-usines. »
Stapleton a réitéré la valeur que les petits fournisseurs de batteries peuvent offrir.
« Il faut également un soutien à l’innovation sur le terrain », a-t-il déclaré, « et je pense que cela rend les deux parties plus viables. »
POWER SOURCING GUIDE
The trusted reference and buyer’s guide for 83 years
The original “desktop search engine,” guiding nearly 10,000 users in more than 90 countries it is the primary reference for specifications and details on all the components that go into engine systems.
Visit Now
STAY CONNECTED



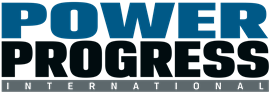
Receive the information you need when you need it through our world-leading magazines, newsletters and daily briefings.
CONTACTEZ L'ÉQUIPE
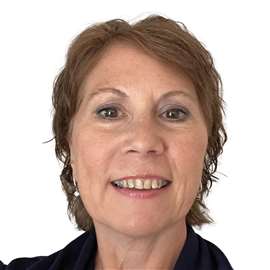
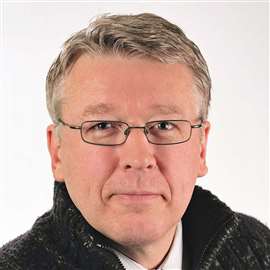
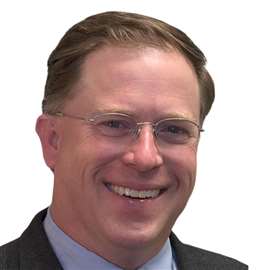
