Flory Industries gets charged up for nut harvesting
20 February 2025
Field elevators play a vital role in the harvesting of tree nut crops such as almonds, pecans, hazelnuts, walnuts and pistachios. Used to transfer the nuts into hopper trucks or stockpiles, they help facilitate the processing of anywhere from 50,000 to 250,000 lbs. of product per day during the fall harvest season.
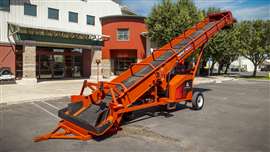
Diesel-powered field elevators can spend about 80% of their duty cycle at low idle in between loads, accounting for about 45% of total fuel consumption. Such long periods of non-productive operation interspersed with the need for instantaneous power make this equipment an ideal target for an electrified powertrain.
Flory Industries, a leading manufacturer of nut harvesting equipment, recognized the potential for electrification in this application and sought out prospective suppliers.
“In early 2023, we met with several of the big OEMs offering large lithium-ion batteries,” said Kyle Dreyer, P.E., engineer at Flory Industries. “We decided on Caterpillar because of the unrivaled support they’ve provided on diesel engine projects with us. We knew Cat and our Cat dealer, Holt of California, would be invaluable in taking this project from concept to completion.”
The resulting demonstration project has become the first presentation of a prototype machine by a third-party OEM using Caterpillar’s battery solution.
Components of electrification
The Flory 4840E electric field elevator prototype utilizes a portfolio of Rexroth eLion electric powertrain components – including a 130-hp electric motor – paired with a 600-volt, 64-kWh Cat lithium-ion battery.
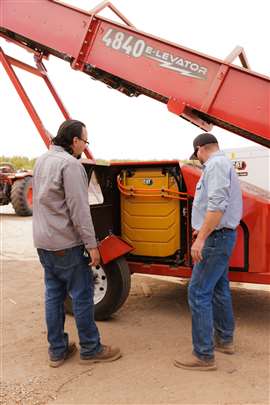
“We decided on the Rexroth eLION portfolio of components because they could supply everything we needed to power our elevator and charge it,” Dreyer said. “The support from Rexroth and our Rexroth integration partner, Hydraulic Controls Inc., was another deciding factor.”
The components operate from 275 to 825 VDC. “That motivated us to use the 600-volt Cat battery – and because 600 volts would be enough power for any future machines we electrify,” Dreyer pointed out. “The Caterpillar battery was designed in-house and has a flexible modular design. Those two factors gave us confidence it would be a reliable design and wouldn’t be at risk of supply chain issues.”
The battery and electric powertrain components require liquid cooling. “We went to AKG, which has been a trusted cooling package supplier for our engines. Their AKG Green product family had the solutions we needed,” said Dreyer. “We used the 5-kW Battery Thermal Management System for the battery circuit. And we used their heavy-duty Power Electronics Cooling system to keep the eLion components at the right temperature.”
Integrated solution
Holt of California, the local Cat dealer, has applied its specific knowledge of Flory’s equipment architecture and duty cycles to provide day-to-day engineering, integration and testing support for the demonstration project.
Engineers are optimizing the system with the goal of enabling a standard 10-hour day of operation in the field on a single charge, with full recharging overnight. The team is integrating the batteries with inverters, motors, electronic controls, digital services and other critical technologies in a power-dense solution that Caterpillar said addresses common user concerns while demonstrating the numerous benefits.
By replacing the traditional engine with an electrified powertrain, the new system is said to eliminate up to 126 lbs. of carbon emissions per machine in the field daily, while eliminating diesel fuel purchase, transport and storage costs. A diesel field elevator can use roughly $95 in fuel per 10-hour workday, said Dreyer, while the 4840E electric field elevator will use only $5 in electricity over the same period.
The 4840E also provides instant torque. “The machine never stalled from an overloaded belt. Diesel elevators occasionally stall and require the farmer to shovel nuts off of the belt,” Dreyer pointed out.
Low noise is another benefit. “The 4840E is nearly silent between unload events,” Dreyer said. “The noise reduction is great for nearby homes, and it was a surprisingly popular feature for the farm workers.”
In addition, Dreyer said the San Joaquin Valley Air Pollution Control District can cover up to 85% of the cost of the electric model if the farmer turns in an old diesel elevator.
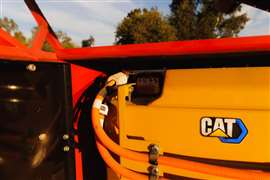
Development is ongoing
Flory engineers are coordinating the demonstration project from the company’s headquarters and development center in Salida, Calif., with support from Caterpillar and Holt of California’s teams located in the Sacramento area. The initial prototype successfully completed a full 2024 harvest testing (see below).
According to Dreyer, Flory Industries hopes to use the project to gain expertise in battery-electric powertrains so it can be ready when regulations or technology advancements make electrification the preferred solution.
“We also wanted to build relationships with suppliers in the battery-electric space,” he said. “In agriculture, there’s a lot of machines with low duty cycle diesel engines. Like our field elevator, they will be a great case to switch to battery power.”
The 4840E project is already proving to be a conversation starter with farmers about their views on electric equipment and the challenges of recharging in remote areas.
“The farmers are really receptive to battery-electric,” Dreyer said, “especially when it can lower their cost of ownership.”
Pilot units of the 4840E electric elevator are scheduled to be available for customers in 2025, with full production expected in 2026.
Editor’s Note: The Caterpillar and Flory Industries prototype demonstration project was a finalist for the 2024 Power Progress Summit Awards’ Off-Highway Product Application of the Year.
Field testing results
Completed during the fall harvest season in the Central Valley region of California, the field test of the Flory 4840E electric field elevator successfully showed how a 600-volt battery-powered powertrain can deliver the performance, reliability and durability currently provided by a conventional 74-hp diesel engine while reducing maintenance and operating with zero tailpipe emissions, Caterpillar stated.
Supported by Holt of California, the prototype was tested over seven weeks in almond and walnut orchards in California, with one site being Heinrich Farms, a 1,200-acre crop farm based in Modesto. Here, the unit operated an entire 10-hour workday on a single charge, loading 422,000 lb. of nuts into trailers throughout the test.
To overcome the constraints of being off-grid, Heinrich Farms fully recharged the electrified field elevator overnight during non-working hours using the Cat XES60 Compact ESS mobile battery energy storage system, which provides up to 56.8 kWh of capacity.
“The electrified field elevator from Flory was reliable and unloaded our harvest as fast as conventional equipment powered by diesel engines while generating far less noise,” said Jerad Heinrich, orchard manager for Heinrich Farms. “It lasted an entire day of work without stopping for a recharge, and we’re eager to use it again for our next harvest as the technology continues to progress.”
The battery-powered elevator is designed to be configured with Cat Connect, enabling equipment owners and Cat dealers to remotely monitor performance during operation and charging cycles.
“We’ve gained valuable insights from working with Flory to apply our knowledge of electrification and high-voltage systems to the challenging environments of working California farms,” said Steve Ferguson, senior vice president of Caterpillar Industrial Power Systems. “This project demonstrated how Caterpillar is successfully aligning with fellow innovators to develop technologies that maximize the performance and reliability of electrified machines at real-world worksites. Caterpillar can provide customers with access to the full ecosystem of components to insights and the charging infrastructure.”
POWER SOURCING GUIDE
The trusted reference and buyer’s guide for 83 years
The original “desktop search engine,” guiding nearly 10,000 users in more than 90 countries it is the primary reference for specifications and details on all the components that go into engine systems.
Visit Now
STAY CONNECTED



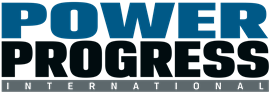
Receive the information you need when you need it through our world-leading magazines, newsletters and daily briefings.
CONNECT WITH THE TEAM
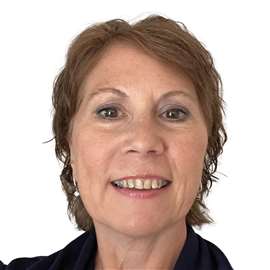
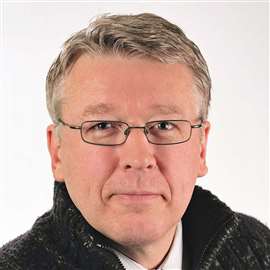
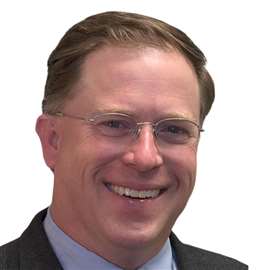
