A Champion For Digitalization
01 August 2018
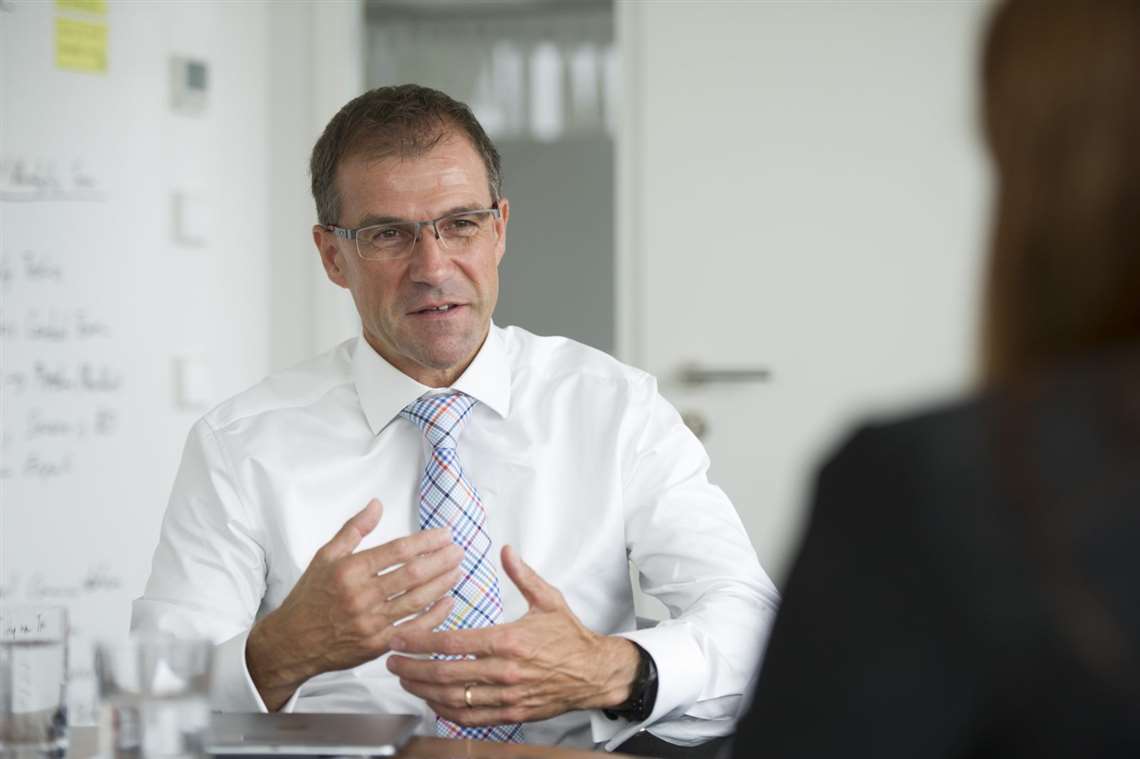
Andreas Schell has been CEO of Rolls-Royce Power Systems for about 18 months and if his influence on the company so far is demonstrated just by the brand-new Digital Solutions group that Diesel & Gas Turbine Worldwide was invited to visit, we can say that his arrival has already put a rather strong imprint on the company.
Schell’s background includes experiences with digital technology, hybrid and electric drive solutions, and fuel cells. He believes, though, that robust and efficient modern diesel engines complying with the latest emission standards will remain the prime source of energy in construction, marine, industrial applications, agriculture and underground mining for the mid- to long-term.
“What we do foresee, though, is that diesel engines will not be the sole source of energy, instead there will shortly be power systems combining diesel prime-movers with battery technology for boost or peak-shaving operations or to reduce emissions. This will then foster the demand for intelligent system automation along with advanced battery technology,” he said.
“Additionally, remote systems and digitalization will enable extended services to allow a more complete customer care, from spare parts supply over remote diagnostics, preventive maintenance and customer training up to guaranteed fuel consumption and uptime.”
A reorganization of the company’s engineering department, as well as the establishment of the new Digital Solutions group within a new, dedicated facility in Friedrichshafen, Germany, were among the first priorities of the new CEO. According to Daniel Eberle, Rolls-Royce Power Systems’ director of Digital Design and Technology, Schell is not just a champion for digitalization but likes to get his hands dirty, so to speak. In fact he seems to spend quite some of his time with the new group.
“Digital Solutions has a sort of life of its own within the company and reports directly to me,” pointed out Schell. “The group employs at the moment about 40 people but plans are to double this figure already within the end of 2018. It is a highly innovation-oriented team, with bold ideas and a daring attitude. At the same time, they are an integral part of Rolls-Royce Power Systems.”
Schell said that his first months with Rolls-Royce Power Systems have been very exciting; on the one end he found a great company to begin with: “This is a company with great products and great people. As far as our internal combustion engines are concerned, I believe we play Champions League, to use a European football metaphor.” On the other hand, though, the company needed some change.
“The markets we are active in require more and more system solutions, so there was a need to transform our company into a solutions provider.”
Rolls-Royce Power Systems had already a transformation program in place to improve the company’s efficiency, but one of the first thing that the new CEO noticed was the almost complete lack of digital solutions in the offering. “A year and a half later, it is very exciting for me to be able to show what we accomplished in such a short time. The launch of Digital Solutions in 2017 was a massive change in company’s culture, from a static organization with extremely well-defined processes, to an innovative, open environment, that is not just dedicated to developing digital products for our customers but represents a change in the way the company works.”
“The differentiator in our Digital Solutions is not technology—which nowadays is available to everyone—but lies in three different categories: the data, the people you have, and knowing customer needs. For data, one of the most important criteria is data protection and cybersecurity and here we can tap on 20 years of experience with our parent company Rolls-Royce in aerospace. It is also crucial to tap into data in real time for a reliable predictive maintenance.
“In terms of people, when we set up Digital Solutions we looked for new skills: data science but also people who have been educated to do research and use different research methods to apply to our customer base and really understand customers’ needs.”
According to Schell, engineering is still core to what Rolls-Royce Power Systems does: the company has a strong engine R&D organized in systems and in engine programs, and a branch for electrification and automation. “Rolls-Royce Power Systems nowadays has quite some unique qualities: technically sophisticated products; a very broad and exciting range of applications; a very experienced and committed engineering team and, not least, some very good customer relations.
“Our market and product complexity is based on a few key development pillars: having compliant diesel engines for the emissions regulations worldwide; working on alternative fuels, such as gas in marine applications, or fuel cells; developing hybrid systems for some applications, namely rail and marine; and offer digitalization in the way of connected devices.” As far as hybrid solutions are concerned, the MTU hybrid PowerPack for railway applications is now ready to be launched in series production, and in 2019 the company will offer a hybrid solution also for marine.
Digitalization and connected devices is a very important topic for the service side of the business. Jörn Lindstädt, director Global Customer Support, said that maximum availability is important across all applications despite their different characteristics: “Product performance is a must, but our customers also require global and seamless support. We have moving fleets and we need digitalization to support our service offering,” he said. “Our Service Of The Future, or Customer Care 4.0 programs are based on superior customer experience and a full stream of data collection and analytics.” He pointed out the company has more than 100 000 engines installed in the field worldwide.
The first digital products that Digital Solutions brought to the market are the MTU-Go! Act and MTU Go! Manage apps, that were designed specifically for individual applications of the MTU brand engines initially ranging from ships, to trains, or power generation.
Connecting up the customer’s system to a data logger enables MTU experts and the customer to remotely monitor the performance of engines; schedule maintenance work and spare parts needs; analyse operational data; and determine what actions to recommend.
While Go! Manage is a platform meant for fleet managers, Go! Act is a person-centric app tool to take action on product’s issues. Rolls-Royce Power Systems said that a further app called Go! Care will be soon released for MTU’s authorized service dealers.

These new digital tools are integrated into new service agreements for the customers which are managed by Customer Care Centers – one of which is located in Friedrichshafen, Germany, in the same location as the Digital Solutions group. Other Customer Care Centers are located in Singapore for the Asia-Pacific region, China and Australia; and in Novi, MI, USA, for the Americas.
In the Customer Care Center in Friedrichshafen experts work side-by-side with the digital team. Preventative maintenance work is scheduled to ensure that everything runs smoothly. Maintenance intervals are coordinated and an optimized, transparent cost structure is in place, guaranteeing the reliability and availability of engines and systems.
Rolls-Royce Power Systems is currently delivering 360 MTU PowerPacks for 122 Hitachi trainsets for the UK‘s Intercity Express Program. Under the Value Care Agreement, MTU guarantees the availability of these drive systems for the next 27.5 years. The PowerPacks are equipped with data loggers and personnel from MTU UK will carry out the maintenance of the PowerPacks, supported by up-to-date sensor data, in Hitachi depots to ensure reliability.

Schell concluded the discussion with a brief overview of the markets, saying presently they are mostly doing all right, even though the majority of the markets Rolls-Royce Power Systems is involved with are cyclical. “Rolls-Royce Power Systems is not a mass-volume company which luckily makes us less vulnerable to these cycles. I expect however that we will probably see a good market for the off-highway industry for a few years to come,” he said. “For what regards the future, I see our company 10 years from now still doing business with our core technology but in a much broader sense. I can assume that there will be additional businesses we will play in, as for example battery storage systems, and microgrids.”
By Roberta Prandi
POWER SOURCING GUIDE
The trusted reference and buyer’s guide for 83 years
The original “desktop search engine,” guiding nearly 10,000 users in more than 90 countries it is the primary reference for specifications and details on all the components that go into engine systems.
Visit Now
STAY CONNECTED



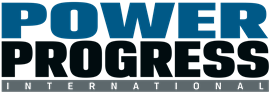
Receive the information you need when you need it through our world-leading magazines, newsletters and daily briefings.
CONNECT WITH THE TEAM
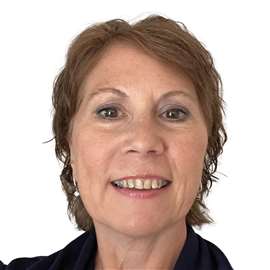
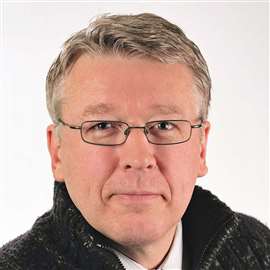
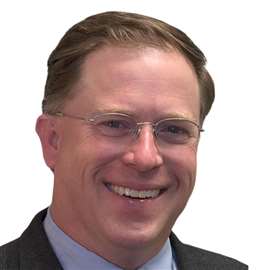
