Answers to common queries about fuel cells
20 July 2021
It is fair to assume that a lot of engineers at mobile and stationary original equipment manufacturers understand the technology of Proton Exchange Membrane (PEM) fuel cells. After all, fuel cells have been around since the mid-1800s (at least in concept) and over the years have been involved in some rather high-profile applications with the most notable arguably the US space program.
But as the push toward cleaner and hydrogen-based becomes more pronounced, how do fuel cells work has taken a backseat to a much more prosaic queries, such as ‘How will they fit in my vehicle or machine?’, ‘How many do I need to use in my equipment?’, ‘How long do they last?’ and ‘How are they serviced?’
As Diesel Progress editors have regularly heard these kind of questions, we have collated the most common queries and asked two leading professionals for their answers.
Philippe Gorse (director of fuel cell technologies at mtu solutions in Germany) and Ryan Sookhoo (business development director for Cummins’ fuel cell business in Canada) were posed the questions.
Question: What is the scalability of fuel cells? Can you make a single fuel cell that is the equivalent of a 400 hp engine or are a series of fuel cells required to reach that kind of output?
Philippe Gorse: We are talking about three system levels with fuel cells, namely a stack with the stacked cells, a module (including the balance-of-plant component), and; fuel cell systems (plant).
What this means for scalability is that at the cell level it is the cell manufacturers who determine how big they make them. That depends on how well they can get the hydrogen, water and air distributed throughout the cells.

Several hundred cells are then stacked on top of each other in a stack. In doing so, one is limited by the media supply (air and hydrogen) and by the electrical system, which must maintain certain voltage ceilings.
Around the stacks we integrate the balance-of-plant components of hydrogen supply, exhaust air, air supply with integrated compressor or turbocharger and a cooling system. This is then a module with a certain power output.
The market currently offers 50kW to 80kW passenger car systems, with significantly more powerful systems for heavy duty trucks expected in the near future. The trend will continue to go up in the future because more powerful systems are required.
In applications such as marine, power generation, construction and industrial, this is also the case. We will then produce megawatt systems from several modules at the system level. In the case of internal combustion engines, scalability is established by the different cylinder variants.
Ryan Sookhoo: What you have happening in the industry is that as new markets unfold, or get into a trial, we are basically taking fuel cells that are already commercial and putting multiples of them to fit that application.
When you compare horsepower to electric, it is not like a one-to-one. The fuel cell is an energy source. The motor is determining what that energy source needs to deliver, like 100kW or 200kW. It is the electric motor of the application that is going to determine the power of the fuel cell.
What you have happening is that heavy-duty applications are starting to come online. Because the technology was not initially designed for heavy duty, that is where you have the multiple fuel cells being configured to do it. But that the technology is maturing towards a commercial productization, we are currently testing and demonstrating heavy duty fuel cell stacks intended for hundreds of kilowatts to megawatts.
Question: Can fuel cells offer a variable output so that in a mobile application, they could directly drive an electric motor or must they always be used with a battery?
RS: Every fuel cell system is actually hybridized with a battery, it is not always shown. But every successful mobility hybridization, whether land or sea or air, has been a hybrid with a fuel cell and a battery technology. Then when you go into battery technology, there are different chemistries. You can have lithium, which is very popular, lead acid and you can even get into ultracapacitors. There are so many options for batteries or energy storage technology that are always hybridized with a fuel cell.
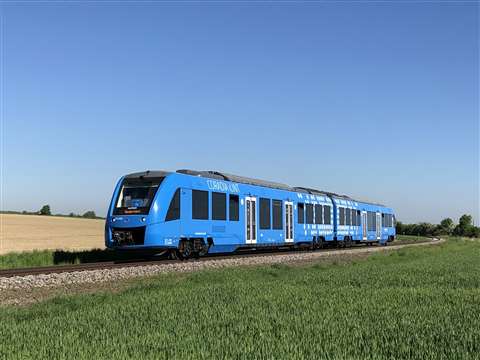
A fuel cell will cycle, it just cannot react in microseconds like a battery. With a fuel cell you can go from 10% of rated power to 100%, and it may just take one second. Whereas in a battery it is done in microseconds if you were to go from 10% to 100%. One of the main reasons you hybridize with a battery is literally to bridge that one-second gap.
A fuel cell works by combining hydrogen and oxygen, so that delay that we are talking about for ramping up is actually the ability of the fuel cell to suck oxygen from the air and create the reaction. So rather than putting some really exotic or complex air delivery system with pressurized air and added costs, use a battery. It is far cheaper and it is proven that the operator should see seamless power.
If you are in a truck all you want to know is when I hit it am I’m getting the best performance I can out of it? And the best way to do that is hybridizing the fuel cell with a battery, because the battery will cover that instantaneous reaction and the operator will not even know when the fuel cell comes on because both the fuel cell and the battery are in parallel feeding the motor.
When the voltage starts to drop on the battery, that is where the fuel cell starts to take over, charging that battery. But to the operator the motor does not miss a beat.
PG: The fuel cell can be operated as dynamically as an internal combustion engine. This has also been demonstrated by the first vehicles. But it is always advisable to couple the fuel cell with a battery to achieve a long service life for the fuel cell. The battery is needed to start the fuel cell anyway. Then the battery can be dimensioned in such a way that it can take overload gradients and relieve the fuel cell.
The principle is the same as for the combustion engine. Here there are very dynamic engines as for yachts, and less dynamic ones as for workboats. The service life of a less dynamic workboat engine is longer.
The power of the battery and fuel cell is sized to the customer’s application. The better the customer’s requirements can be described, the way the vessel or power system will operate, the better the battery and fuel cell can be matched.
For example, a small battery system can be combined with a large fuel cell system or vice versa. This is also an important advantage of the fuel cell. By combining it with the battery, flexibility in the design of the propulsion or energy system can be enabled.
Question: How quickly can fuel cells be started? Is there a period of time they need to warm up or do they begin producing the rated amount of electricity immediately?
PG: The start-up time of a fuel cell system is absolutely comparable to that of an internal combustion engine. When operated in combination with a battery, the system initially supplies electrical power immediately via the battery.
The fuel cell itself needs electricity for a short time to drive the compressor to ensure the air supply to the stack. Then, in the fastest case, it can be brought to full load in 30 seconds. If it is operated more gently it will be at full load in about 60 seconds.
However, the fuel cell should not be frozen. The cooling water should always be liquid (5º to 10º C) to be ready for immediate operation, which is similar to a large diesel engine that is also preheated.
RS: You can expect the exact same as an engine, and that is the beauty of that hybridization with the battery. Toyota, Hyundai and General Motors, they have done a good job of showcasing that the experience on the vehicle is identical. You start it up and you go.
A fuel cell warms up pretty quickly once it has started. Take a 100kW fuel cell. If you are producing 100kW of electricity then you are also generating a minimum of 100kW of heat. Warming up and getting to temperature happens very rapidly. So the experience is seamless, you would hit start and then you would start to drive.
Question: Combustion engines use accessories – starters, motors, radiators and fans, air and fuel filter motors – to operate. What accessories are needed in a fuel cell system?
RS: At the end of the day a lot of the things you are going to do with a fuel cell in terms of optimizing it or operating it, you are already doing with engines.
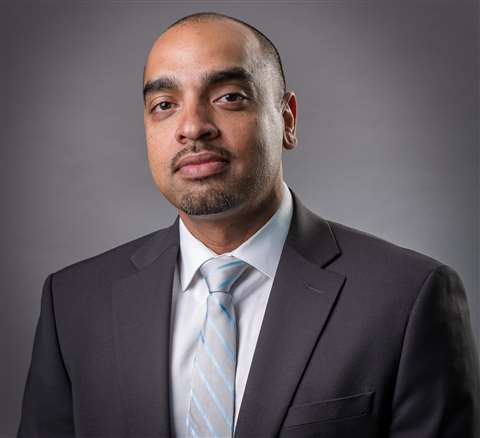
We already have a radiator fan system for heat rejection in engines, we already have cooling pumps where we pump liquid coolant through the engines, we already have an air intake with a filter. You have all of those things with a fuel cell, so what is new?
What is new is that it is generating electricity instead of horsepower. And instead of pumping diesel fuel into the engine, you are sending hydrogen into the fuel cell. So when you look at the fundamentals it really is not all that different, other than the reaction inside.
PG: In a fuel cell module the stack is extended to a fuel cell module by integrating an air supply, a hydrogen supply and a cooling supply. Usually this includes an air supply by a compressor or a turbocharger, an off-air system to bring the exhaust air outside, cooling pumps, a control unit and power electronics to bring the voltage in the stack to a desired level.
Added to the module for a fuel cell system are plant coolers, the hydrogen tank, the battery and power electronics that convert the direct current supplied by the fuel cell into alternating current for 50Hz or 60Hz grids.
A gen-set system with an internal combustion engine also has similar components – a radiator, a fuel tank, a starter battery, a generator that produces alternating current and in addition today, usually an exhaust gas aftertreatment system and a silencer.
A generator, exhaust gas aftertreatment and silencer are not required for fuel cell systems. Nevertheless, the required installation space is about the same because the cooling system for a fuel cell is much larger. Since a fuel cell system requires fewer components overall, it is less complex than a system with an internal combustion engine.
A short excursion: with fuel cell systems a major advantage is that emissions compliance is not an issue. Only grid compliance must be ensured for feeding into the grid.
Question: Would an OEM buy a fuel cell and package it or does the fuel cell supplier typically provide the fuel cell system as a kind of plug-and-play module?
PG: OEMs are advised not to assemble a fuel cell system themselves. Solution providers like Rolls-Royce Power Systems are more experienced in system integration, know the individual components and their properties better.
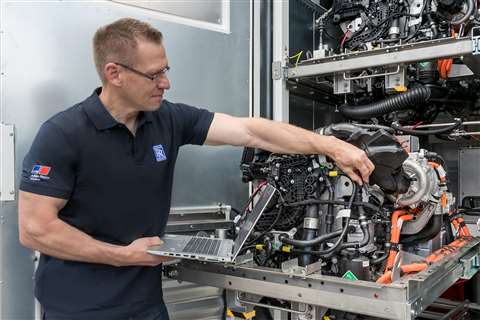
We have customers who have tried, but who are now grateful that we do the work for them and offer them a fuel cell system with battery, the power electronics and cooler etc, all coordinated with each other.
RS: That is typical. Not typical of fuel cell companies, but typical of companies who make engines. You buy an engine from Cummins you get an engine “block” if you will, with everything. The fuel cell will come with your pumps, your air system, your regulator, so essentially you will put hydrogen in here, put coolant in here and take electricity out there.
There are some fuel cell companies who only sell you the stack or just a fuel cell, and then you have got to go find your pumps, your regulators, your air filter etc. From a Cummins perspective, we tend to be more on the complete solution side.
We announced last year a joint venture with a tank company called NPROXX. Cummins makes power electronics and owns battery technology. So we are really trying to deliver on a power solution, rather than a fuel cell.
And it is not just the technology and the system packaging, we are really after truly trying to also bring down the cost. Because at the end of the day these vehicles have to make sense economically, and we cannot just bring down our piece and leave the hydrogen supply tank out there, because the OEM is going to feel it.
Question: How durable are fuel cells? Can they accept the shock loads routinely seen in applications like mobile vehicles and equipment and marine vessels?
RS: I would say the durability has been steadily improving. They were designed to be better. When the automotive market launched fuel cells, they were supposed to exceed the performance of the combustion engine. The fuel cell gives you the strengths of a combustion engine, like range, and all of the strengths of a battery, which was zero emissions.
On the durability side, the unit will run as long or longer than a diesel truck engine. That is the goal, to give you the same performance expectation.
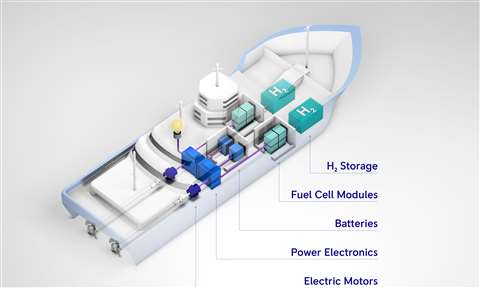
The runtime of the Cummins fuel cell right now is somewhere around, I’m going to say 12,000 to 15,000 practical hours, but this is very duty cycle dependent. Like with cars, it is not the age but the mileage that impacts longevity.
In controlled conditions and under light duty cycles they can run much longer, so its lifespan is largely dependent on how it is used. Cummins is quite confident that over the next few years we are actually going to get to where we need to be, comparable with the diesel runtime.
PG: Who knows? We have a very long experience with diesel engines. With fuel cells no one has that experience yet, because they have not been operated for a very long time. We still have to find that out. That is why we are also taking the route of pilot plants, which we want to bring into the field at an early stage of development and observe them under real conditions. Theoretically, they have long-term requirements. After all, they also have to meet the high demands of the heavy duty truck sector. It is important that the fuel cell system is designed for a long service life.
Question: Are fuel cells limited in any way in terms of operating temperatures? What sort of thermal management is needed on fuel cells (radiators or heaters)?
PG: With PEM fuel cells, as we use them, the stack has its comfort zone between 60º and 80º C. Above that it becomes difficult to cool the fuel cell down. Excessively high temperatures significantly reduce its service life.
At lower temperatures it is important to ensure that the fuel cell does not freeze. That is why a minimum temperature should be maintained with preheaters.
RS: Fuel cells generate a lot of heat so one we are running, significant subzero temperature really isn’t a challenge. Subzero temperature is a challenge for us when we are not running. As part of the equation, we generate electricity by making water. So where that water drips out, we have to make sure it does not freeze. It is just basically stuff like that.
Operating temperature for fuel cells are going up, meaning we are trying to run them hotter and the reason we are trying to do that is we are trying to maintain an operating temperature all of the time.
We are basically asking our cooling system to hold that temperature. What that means is if you are in an area where it is really hot outside then the radiator system is much larger to hold that temperature. It is not rocket science, it is good engineering.
Question: How easily will fuel cells fit in vehicles and equipment? Using a truck example, can you package a 400hp fuel cell system in the same space as an engine?
RS: I think it will change by application, but not by industry. If you look at a vehicle for a commercial fleet, the duty cycle, how it runs, will dictate the sizing and how big the fuel cell is
versus the battery. If you do a long haul truck, that’s going to have a different configuration.
What is great about it is system package, the power solution, is targeted by duty cycle. That is not a standard ‘this one fits all’, because what ends up happening is you overpay. If you are on the wrong side of that equation then you are going to overpay for performance you do not need.
What you see happening in the industry is, through trials and evolution, as things are commercialized they are kind of segmenting into a certain size fuel cell and a certain size battery. That same sizing may not fit a heavy duty truck. So by application, yes, you are going to get a little bit more standardizing in package. But it is not one fits all.
PG: The complete drive system with tanks and batteries should be considered. The fuel cell system is heavier than the drive system with combustion engines, mainly due to the tank. The volume is also larger because the hydrogen in tanks requires more space than diesel tanks.
For example, a 40 ft. diesel gen-set container today provides about 3 MW. A 40 ft. fuel cell container will provide 2 MW to 3 MW. Over time we expect fuel cells to get a similar power density as a gen-set, but the tank will always be larger. This poses a challenge, especially for marine applications. Therefore, some future fuels are currently being discussed – liquid hydrogen, methanol and ammonia – some of which can then be used reformed as fuel for the fuel cell.
There are customers who do not have this challenge because they already have a hydrogen infrastructure, eg access to the hydrogen grid.
Question: Are fuel cells sealed or can they be opened up for repair or maintenance? Is there any routine maintenance required?
PG: There are very few moving parts in a fuel cell. Wear and tear is therefore significantly reduced compared to an internal combustion engine. We assume that fuel cells will be much easier to maintain, especially in terms of predictive maintenance. Regular maintenance is required for the air filter and deionizer, which reduces the conductivity of the coolant.
The fuel cell operates at a pressure of only 3 bar, which puts less stress on the components than an internal combustion engine that operates at up to 250 bar. The relatively low temperature of the PEM fuel cell of 80º C (combustion engines are 1,000º C) also means that the material is not particularly stressed. This means that the fuel cell is generally easier to maintain than an internal combustion engine.
It is quite possible to replace the balance-of-plant components, eg the cooling water system, the air filters, the piping and the control units. This can be done in a workshop. However, clean room conditions are required to open the stack. After a major overhaul of a stack, it must be conditioned again so that it is sufficiently humidified.
We plan to allow individual modules of a system to be removed and replaced during operation, so that the propulsion or energy system can continue to operate at high power without failure. This is a clear bonus in terms of availability.
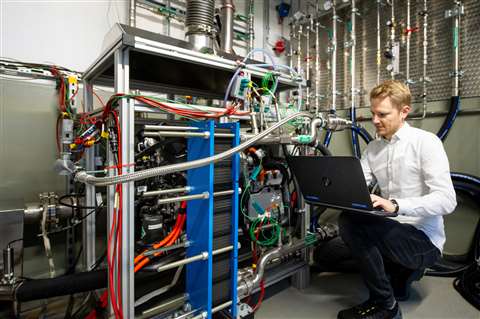
As a general rule the fuel cell system is designed for a lifetime of the respective application, the module for a certain number of operating hours. This means that the module is replaced every few years. When the module is replaced the stack must also be replaced, because the fuel cell module is usually designed for the lifetime of the stacks. However, it is also possible to replace only the stack.
It must be noted that the stack is still a cost driver for maintenance today. With the expected rise of fuel cells in the mobility and power generation sectors, the price of stacks will drop dramatically and maintenance costs will decrease. We have already seen this effect with similar new technologies such as solar or batteries.
RS: The strength of a fuel cell is that it has a very low service requirement because of the technology. There are not a lot of moving parts in there, it is a chemical reaction. It really comes down to the stack life that really dictates servicing of the stack. The other parts are like regulators and solenoids, which almost never fail.
I would say for the majority of it, the annual maintenance is really visual. Maybe the air filter, but that will be depending on application. You are not swapping out coolant pumps.
That is the beauty of why DOE [the US Department of Energy] really advocates that the OpEx or the operating costs on a fuel cell is so low that when combined with the higher CapEx [capital expense] of the fuel cell, your TCO [total cost of ownership] is ultimately still less.
And all of these systems are fairly intelligent. After each run, the Cummins fuel cell sends you a health update. All that that data, whether it is used by the operator or not, is kind of helpful for predictive maintenance.
Question: Notwithstanding the fuel infrastructure issues, are fuel cells production ready?
RS: The fuel cells themselves are production ready. Our facilities are geared to produce thousands a year. We have the major facility for fuel cell production, here in Mississauga, Canada, and we also have a large facility at Herten in Germany. The stack builds are there. If we get engaged with a wonderful contract, I wouldn’t say we can do 10,000s a year, we are in thousands a year right now. But we could scale up easily and are actively doing so.
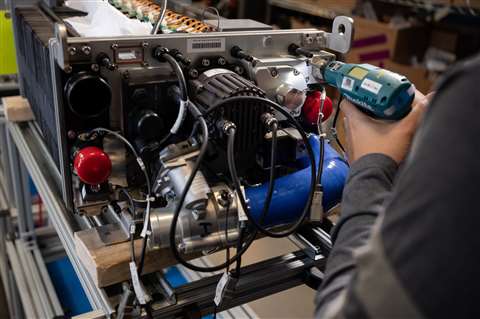
Cummins is going to be in a very good position as the volumes come, because we are pretty good at scaling up in manufacturing.
PG: The technology is mature. We see fuel cells everywhere on the road. Daimler has a thousand vehicles in the field, Hyundai and Toyota have vehicles in the field, Switzerland is starting a a thousand truck program. There are a few manufacturing plants that are already capable of producing in large numbers.
Plans are to enter mass production of fuel cells in 2025. The investments will be made to be able to manufacture in large quantities in a highly automated way. What does not yet have a secure perspective is the hydrogen infrastructure. But I believe that with the availability of fuel cells, this chicken-and-egg problem will be reduced.
The investment plans of many countries for the expansion of the hydrogen infrastructure show that it will come, also driven, for example, by the truck emissions legislation that calls for hydrogen vehicles.
Question: While most of the interest and activity involves PEM fuel cells, what about solid oxide fuel cells?
PG: PEM technology is the most mature fuel cell technology. It is becoming cost competitive. The SOFC [solid oxide fuel cell] is a high temperature fuel cell that operates at 600º to 700º C. It does not tolerate load changes, but must be operated at the same operating point. This makes it excellent for CHP plants, ie when the customer has a heat demand.
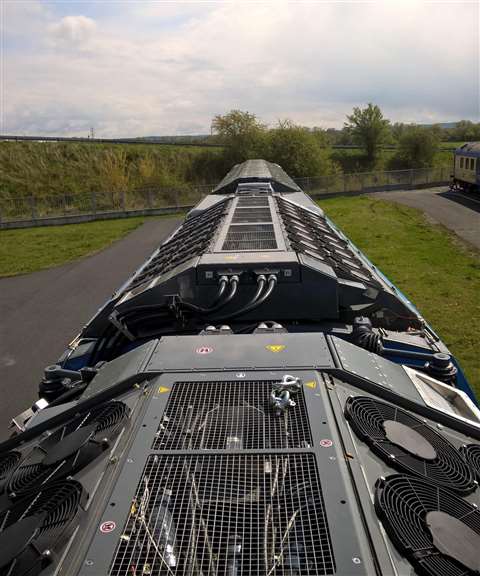
It can also be operated with natural gas. This is an obvious choice since natural gas networks are available today. The main challenge is market penetration. Prices today are still significantly higher than for the PEM fuel cell. Electrical efficiencies are slightly higher than PEM. If it opens up the markets it will have its raison d’être.
RS: Cummins also own solid oxide fuel cell through our acquisition of GE solid oxide program. It is about fuel, it is not the technology. Can you imagine being a data center running 10 MW with a fuel cell? Yes, the technology exists. But how do you get that much hydrogen to them? What’s been the limitation in the stationary market really is not the capability is the infrastructure for the fuel. There is not a hydrogen pipeline coming into that data center, but there is a natural gas pipeline.
At Cummins we believe that the natural gas solid oxide fuel cell would likely dominate this market space, as it grows because the natural gas pipeline is there.
Then you start getting to questions about which regions would allow a solid oxide fuel cell to operate. We look at California and their emission requirements, would solid oxide fuel cell comply? Who knows? If you go to Europe, it is the same question.
So it is not so much technology as both technologies can do the job. It is going to come down to whether you have enough hydrogen or is a solid oxide fuel cell emitting low enough emissions that they will comply with that regional emission criteria.
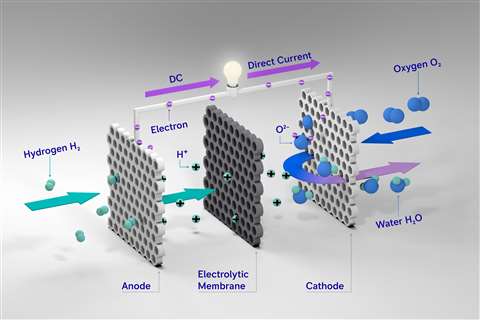
A proton exchange membrane (PEM) fuel cell consists of two electrodes, a negative electrode (the anode) and a positive electrode (the cathode) with an electrolyte in between.
Hydrogen is fed to the anode and air is directed to the cathode. A catalyst at the anode separates the hydrogen molecules into protons and electrons, which take different paths to the cathode.
The electrons are sent to an external circuit, creating electricity. The protons pass through the electrolyte to the cathode, where they join with oxygen and the electrons to produce water and heat.
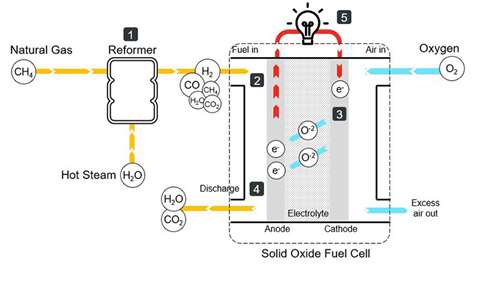
Solid oxide fuel cells (SOFCs) use a solid oxide material as the electrolyte between the negative electrode (anode) and positive electrode (cathode).
In many cases, SOFCs use steam-reformed natural gas, which produces hydrogen (H2), carbon monoxide (CO), carbon dioxide (CO2) and steam (H2O). These enter the fuel cell on the anode side and air enters on the cathode side. Oxygen in the air combines with free electrons to form oxide ions at the cathode and these travel from the cathode to the anode through the electrolyte.
At the anode the oxide ions react with hydrogen, forming water and with carbon monoxide (CO) forming carbon dioxide (CO2) and releasing free electrons, which travel to the cathode through an external electrical circuit, producing electricity.
POWER SOURCING GUIDE
The trusted reference and buyer’s guide for 83 years
The original “desktop search engine,” guiding nearly 10,000 users in more than 90 countries it is the primary reference for specifications and details on all the components that go into engine systems.
Visit Now
STAY CONNECTED



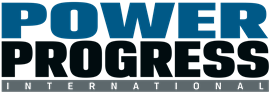
Receive the information you need when you need it through our world-leading magazines, newsletters and daily briefings.
CONNECT WITH THE TEAM
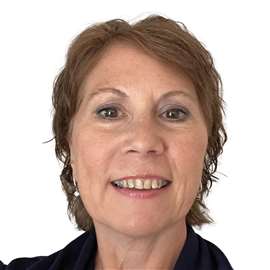
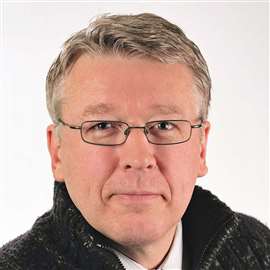
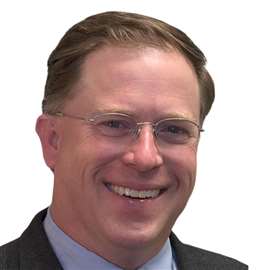
