Assessing Filter Performance
26 September 2017
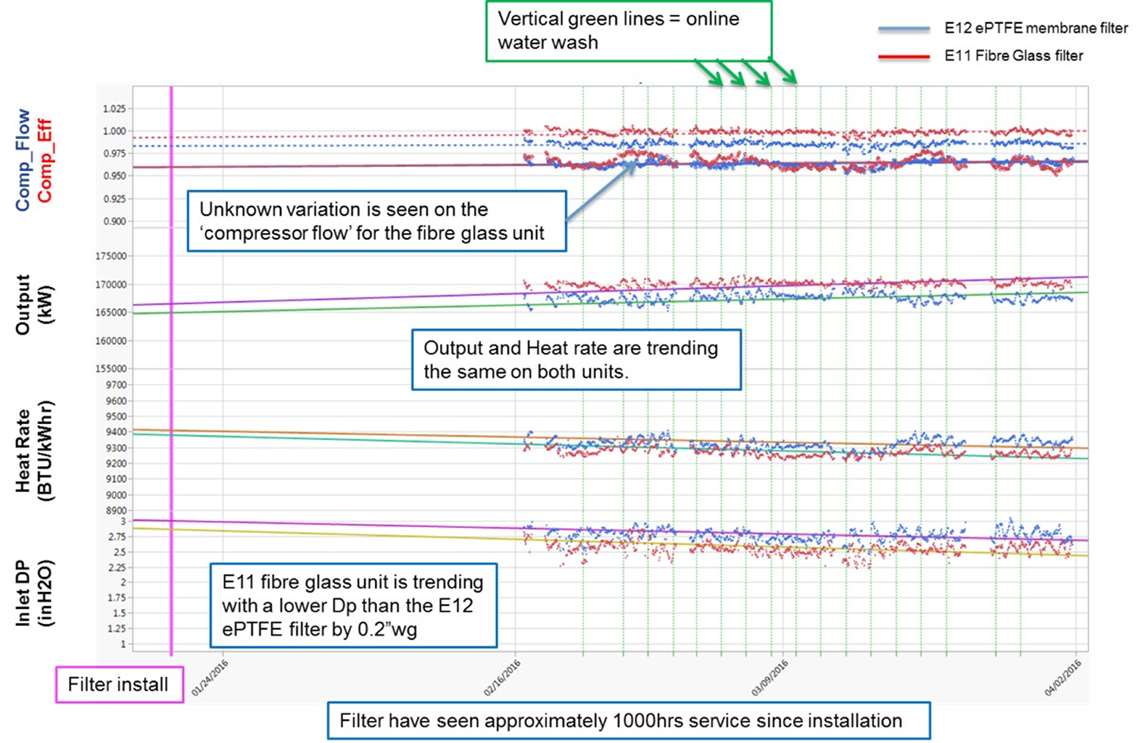
A true evaluation of how well an inlet filtration system is performing is the resulting performance of the gas turbine. Considering the amount of air a turbine consumes, the quality of this air has an impact on its operation.
The performance of the filtration system depends on filtration media and overall system configuration. Depending on operational goals, how the system performs may be measured by turbine availability, frequency of offline washes, lifetime of the filter and/or cost. The filter efficiency rating is one measure of performance but different media types handle varying environmental conditions with different levels of effectiveness – so what factors need to be considered when selecting a filtration solution?
According to Tim Nicholas, Gas Turbine technical services leader at Clarcor Gas Turbine Filtration division, it is a natural perception that a filtration grade of 12 is better than 11 – but using a higher rated filter does not necessarily mean you are getting value for your money. Clarcor Industrial Air, part of Parker Hannifin Corp., supplies a range of inlet systems and filters.
“One of the biggest threats to many installations is an unplanned outage,” Nicholas said. “To reduce this risk, a lower rated, more stable media technology may offer more benefits to the operator.
“High-efficiency particulate air (HEPA) filters capture finer particles of dust, sand and other contaminants and so, in theory, should help to better protect the turbine and its performance. However, if the filter chosen is not designed to handle all local environmental conditions, operators may experience unnecessarily high maintenance overheads, reduced turbine reliability, degradation in performance and unexpected shutdowns.
“By its very nature, the finer media in a higher efficiency filter can be more prone to blockages. If this blocking happens rapidly, it can cause immense operational challenges.
Nicholas said sudden pressure spikes can lead to turbine outage and unplanned maintenance which, depending upon the type of application, can lead to millions of dollars’ worth of lost production capacity.
“The challenge with many installations is that it is not just dry dust that the filter is handling; there are usually many more local environmental factors to consider,” Nicholas said. “A standard filter rating is based on laboratory conditions.”
Nicholas said the performance of a filter may be very different in the ‘real world’, especially as many gas turbine installations are in locations with very harsh environments including extreme temperatures, moisture in the form of mist or fog, high levels of sand or dust, and salt if the site is within 12 miles of the sea.
Hydrocarbon mists or moisture from mist or fog events are problematic because of the size of droplets involved. The droplets are small enough to enter the filter media but large enough to become stuck within it.
When combined with dust and other contaminants to form sticky or muddy residues, blockage can be very fast indeed. If salt is present, the moisture will also change the form of this highly hygroscopic contaminant from solid to liquid. Allowing salt into the turbine internals is particularly perilous as it combines with sulfur in the fuel to cause hot end corrosion, Nicholas said.
“Use of hydrophobic and advanced fiber coated filters is one way of stopping sticky contaminants such as salt in liquid phase and hydrocarbons reaching the turbine blades,” he said. “Care needs to be taken, however, so that these continue to offer protection throughout the lifetime of the filter.”
He said fluorocarbon coatings, for example, offer excellent performance at first but as dust covers the filter the coating becomes concealed and it no longer does the job for which it was intended.
What then are the pros and cons of moving from a HEPAE11 to E12 filter?
Nicholas added: “On paper, one of the main reasons for moving to a higher rated E12 filter is to reduce the number of offline washes required and so increase productivity. The problem is that this may well not change operational procedures in any case.
If a turbine OEM recommends periodic water washing to help prevent corrosion, it is likely that the operator will continue to follow the advice given to protect their asset. Indeed, the amount of additional dust an E12 filter removes compared with an E11 over 8000 turbine operating hours (one year’s production) typically equates to around 0.5kg for a 7FA GT, that is only 1 g per filter.”
The figure above compares performance of a HEPA E11 glass fiber hydrophobic filter with a HEPA E12 ePTFE membrane filter. Glass fiber media is around ten times thicker than an ePTFE membrane; which uses a thin, two-dimensional layer of high-efficiency media. The problem often seen with E12 ePTFE filters is the fine, thin media is very prone to sudden blockages when moisture or hydrocarbon mists are present. The risk of sudden outages means many sites prefer the more stable glass fiber solution.
As well as being less sensitive to moisture, there are other advantages in selecting an E11 glass fiber filter. As shown in the chart, the E11 solution shows about 0.2” wg better differential pressure compared with the E12. As a rule of thumb, 1” wg of pressure drop equates to around 0.4% of turbine output. Saving 0.2” wg, therefore, improves output by around 0.1%. If a MWh cost $40, the saving over 8000 hours of operation of a 170 MW rated turbine would equate to:
170MW x 0.1% x 8000 hours = 1360 MWh
1360 MWh x US$40 =US$54400 per year
“At the end of the day, plant operators are interested in the outcomes of installing a particular type of filter rather than the rating or detail of the filtration solution itself,” Nicholas said. “Often considered as just a commodity item, trying to save a few dollars on a filter may cost a lot of money over a relatively short space of time.
“Not considering all of the factors that may affect a filter’s performance when selecting which one to use may further put the whole operation at risk.
“While there is some reward with a higher rated filter as it will capture finer particles of dust, the level of this reward, however, may only be very small; especially when choosing between closely rated E11 and E12 options. More important factors include how the filter reacts to sudden mist or fog events, how it handles harsh conditions in terms of robust construction and making sure it is installed correctly. Maintenance schedules and strategies need to be set to ensure such filters are changed out at an optimum time.
“This will ensure filter efficiency is safeguarded and the turbine continues to have the correct level of protection, but change out is not so frequent as to make operational costs unacceptably high.”
POWER SOURCING GUIDE
The trusted reference and buyer’s guide for 83 years
The original “desktop search engine,” guiding nearly 10,000 users in more than 90 countries it is the primary reference for specifications and details on all the components that go into engine systems.
Visit Now
STAY CONNECTED



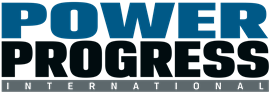
Receive the information you need when you need it through our world-leading magazines, newsletters and daily briefings.
CONNECT WITH THE TEAM
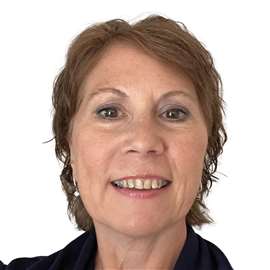
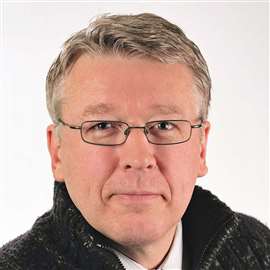
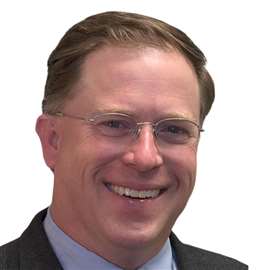
