Autonomy, batteries driving farm equipment design renaissance
28 May 2021
Farm equipment: From horseshoes to artificial intelligence.
“Turning from the broader side of the tractor situation to the matter of detail design, one finds an amazing variety of types and constructions. There are, at the present time on the market, something over 150 tractors, no two of them alike. The designs are so widely dissimilar that it is even difficult to classify them except in a most general way. Each design represents an evolution based on the condition as analyzed separately by the different engineers and no two have achieved exactly the same result.”
-C.M. Eason, manager, Hyatt Roller Bearing Co.
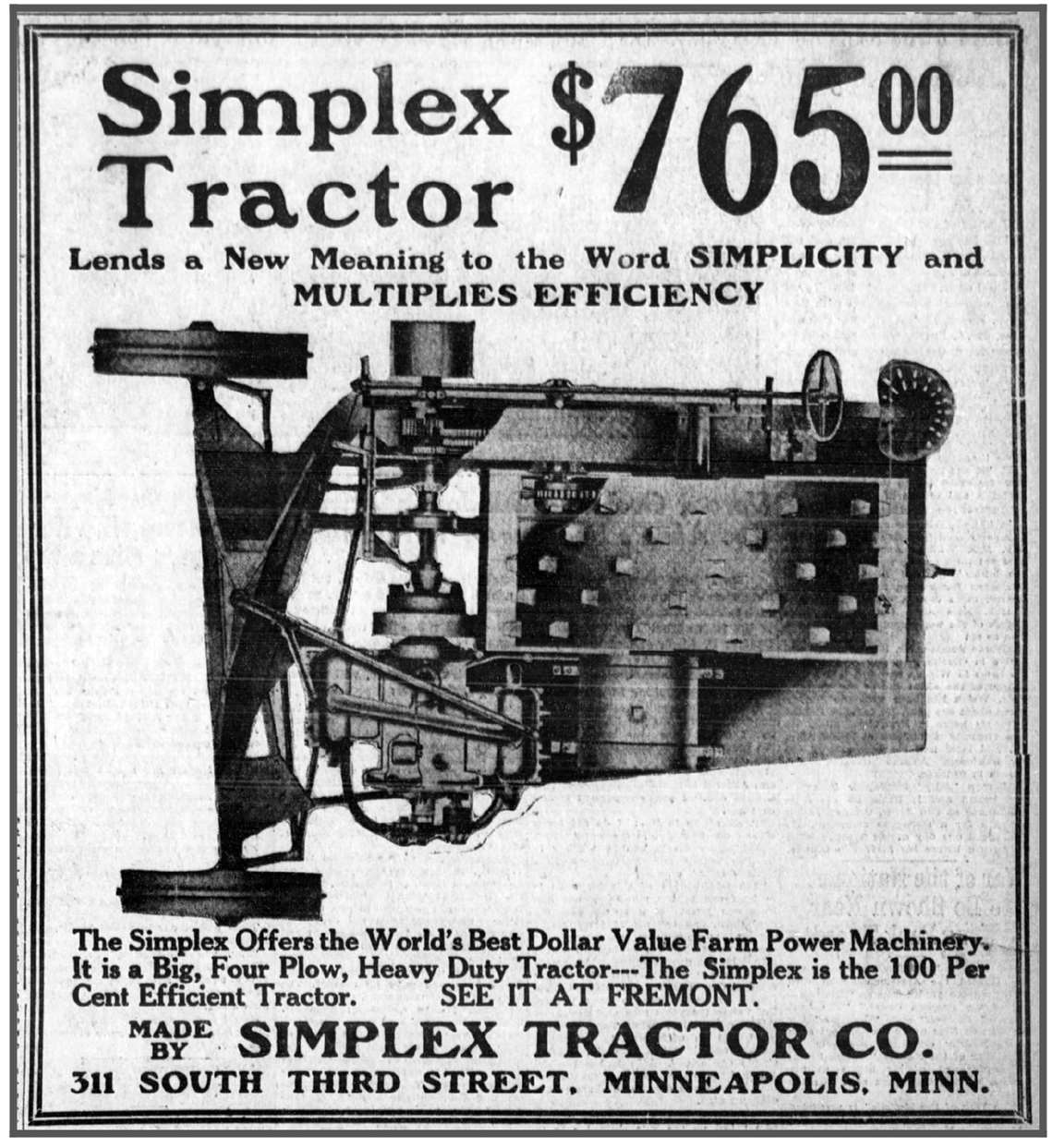
Mr. Eason spoke those words during the ninth annual meeting of the American Society of Agricultural Engineers – today’s American Society of Agricultural and Biological Engineers (ASABE). He could have been talking about farm equipment design in May 2021, but it was December 1915.
When ASABE was founded in 1907, farmers depended on horses and implements that were perfected through decades of trial and error. That changed rapidly during the association’s early years. The 1910s were a crazy time for tractor development. Everyone was focused on their vision of what the perfect tractor would be – with varying degrees of commercial success. Drawbar work was an engineering challenge.
There were two-, three- or four-wheeled tractors and drive wheels could be positioned anywhere. Some designs used the horse-drawn plows a farm already owned. If a steering wheel was intimidating, tractors were available that could be controlled via reins like a horse team. Farmers knew what would work only after field demonstrations or when a new machine was delivered.
By 1915 many agreed the tractor did have a future – working alongside horses. As Eason said, “It was at one time the firm belief of many of the pioneers in the tractor business that a new era in agriculture was opening up wherein animal power would be replaced exclusively by mechanical power…. That these expectations will not, however, be entirely fulfilled, has lately come to be the opinion of the better-informed tractor builders. While it cannot be expected that they will replace horses entirely it has been proven conclusively that tractors can be used, in connection with horses, to better advantage than either the tractor alone or the horses alone.”
That prediction became obsolete soon after it was proffered. When the United States was involved in World War I (1917 to 1918), there was a severe food shortage. Bad weather hurt yields and field help was hard to find. Kerosene and gasoline-fueled tractors had more endurance than horses, saved time and labor expenses, and meant farmers could convert hay fields to crops for human consumption.
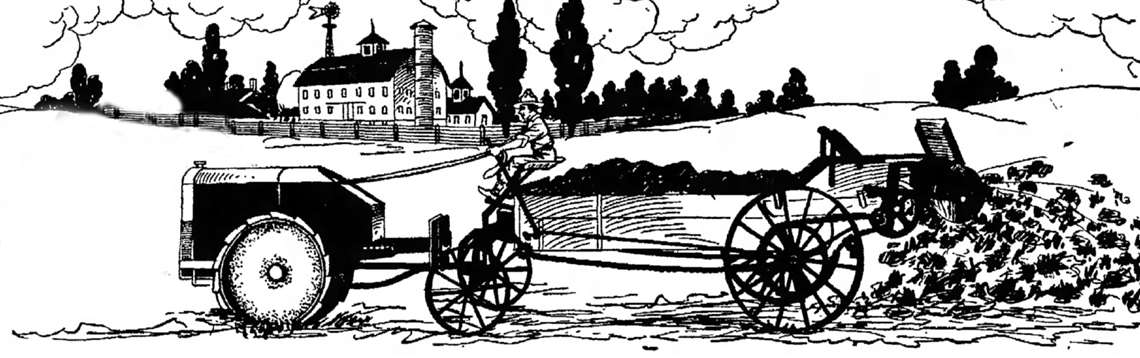
Several years of trial and error paid off, and by the early 1920s the industry did arrive at the ideal tractor, one that could plow as well as cultivate and perform most of the other tasks required on the farm.
Future farm machinery
One century later, the world of self-propelled farm equipment research and development is once again diverging.
Autonomous technologies and energy storage batteries have the power to change the look and function of agricultural equipment and alter the way a dairy barn, grain field, vineyard or orchard operates. Removing the operator from the cab – and the cab from the machine – offers machine forms not possible before. In the same way hydraulic systems made it possible to develop completely new high-clearance row-crop sprayers, the latest technology will enable equipment to be developed that will utilize the land, seed and chemical inputs and human labor in ways never thought possible.
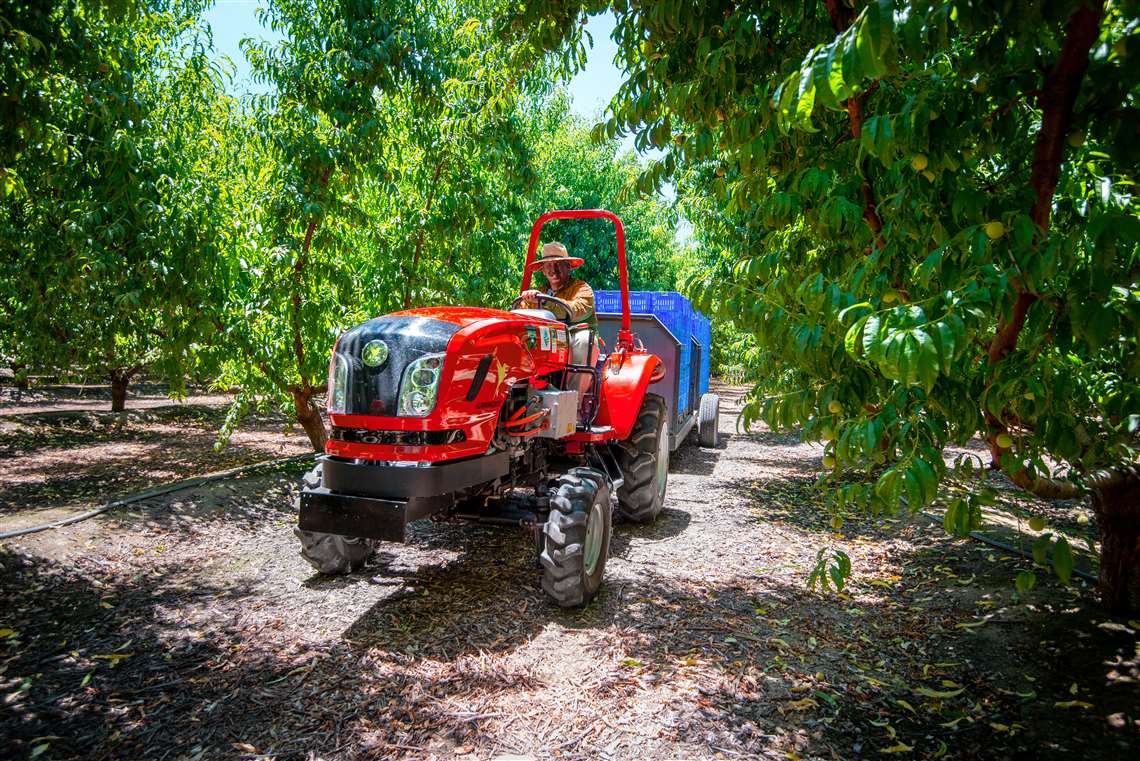
“Farmers are trying to maintain or increase their yields in a smaller space, especially in places such as California,” said Rakesh Koneru, COO of electric vehicle start-up HummingbirdEV in Livermore, Calif. “As ground is lost to development, farmers are looking for ways to plant more fruit trees so they can do more with less land. The existing equipment chassis are not going to be a fit with tighter row spacing. That’s why some farms are moving toward ATVs to pull bins and trailers instead of using bigger tractors.
“It’s becoming very clear to us that we should address those challenges, not only from an emissions and convenience standpoint, but from what orchards and other farms will look like in the future. The battery-electric technology we have developed would permit a very small tractor to be designed that’s closer to the ground, for example, to protect fruit trees and still be able to do all of the work that a tractor does. I think there’s a huge potential and we’re just in the starting phase.”

100-acre farms 100 years ago
Growers already have access to a greater variety of equipment than the 100-acre family farm did in 1915, even when considering the “amazing variety of types” of which Eason spoke.
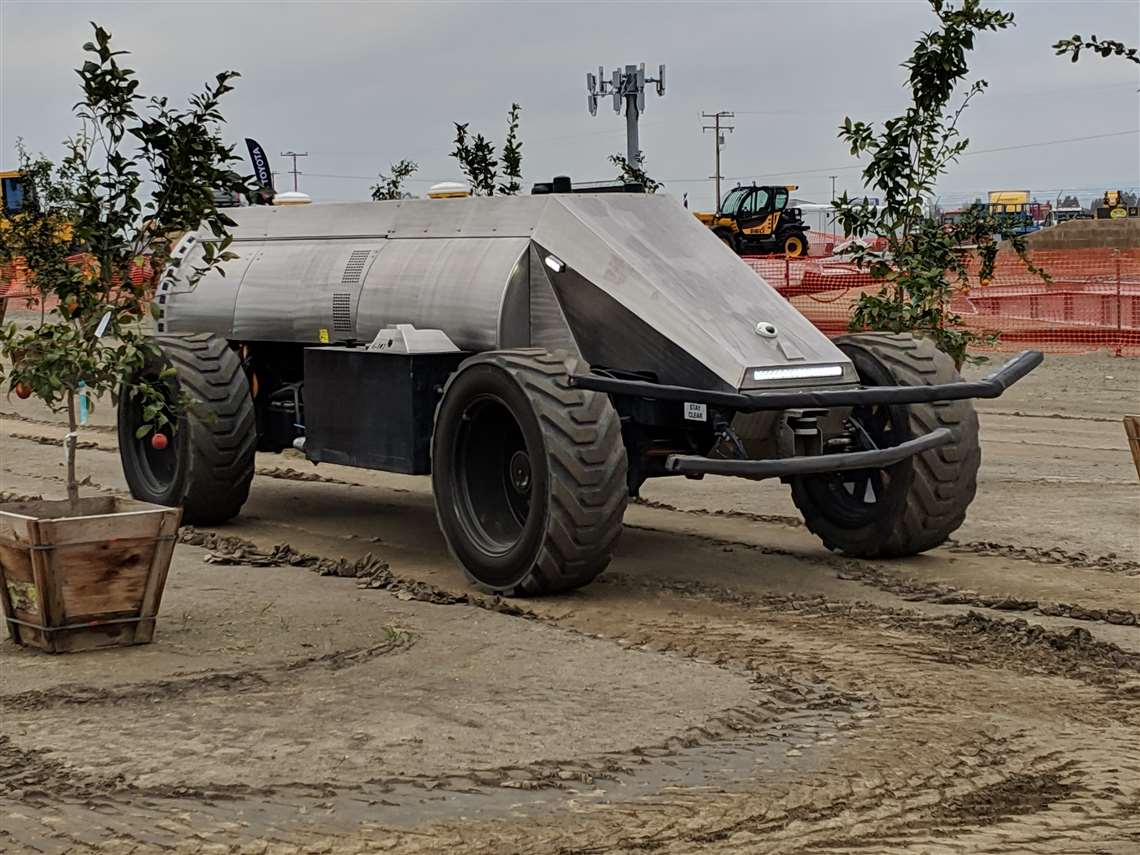
Today, it’s not only the horse that stays home while work is being done, it’s the human equipment operator and hired help. It’s not kerosene and gasoline replacing oats and grass as the fuel of choice. It’s electricity, diesel, gasoline, methane or hydrogen working together. Growers can select a power source that what works best for their operation.
“If somebody from 100 years ago was transported to 2021, I think they’d be shocked,” said Darrin Drollinger, executive director, ASABE, St. Joseph, Mich. “They would have no trouble identifying a tractor. That’s just how it has been, but autonomy and electrification are game-changing.”
While the tractor is the most recognizable piece of farm machinery to the average urban consumer, the fleet of equipment necessary to grow food, fiber and fuel is diverse, of course. So too are the opportunities for technology.
“It’s not only what people think of as regular field equipment,” said Scott Cedarquist, director of standards and technical activities, ASABE. “There are a whole lot of opportunities for new technology to make a difference. I’ve attended EuroTier, and the number of automated pieces of equipment for the farmer was eye-opening.” Held in Germany, EuroTier is organized by DLG and focuses on animal husbandry.
“There are a lot of other areas on the farm where electrification would be a good idea, especially on equipment that runs indoors,” Cedarquist said. “Part of why there is so much automated equipment at EuroTier is attendees come from European and Scandinavian countries where labor is very expensive. We have members that are working on assisted devices as well as full automation for fruit and vegetable growing because those crops take a lot of labor.”
Emerging countries also stand to benefit from new ag equipment designs.
“I visited Nigeria during the fall of 2019,” said Drollinger, “and several people there said they wanted U.S. technology but knew the tractor industry wouldn’t be interested in building machines in the size they needed. I can understand that – for years, the reality of agriculture and the need for efficiency in countries like the United States drove bigger, bigger, bigger. But now the farm of the future can include a whole hive of little autonomous bee-like machines that work 24/7.”
Swarm system
As the size and weight of farm machinery increased, soil compaction and its effect on crop yield has become a significant concern. When the current battery-electric journey began years ago, naysayers warned the weight of a battery pack that could match the power density and run-time of an internal combustion engine would be impractical in a tractor. One solution is the swarm system: Rather than make one tractor bigger, a team of much smaller robot tractors crawl over the field.
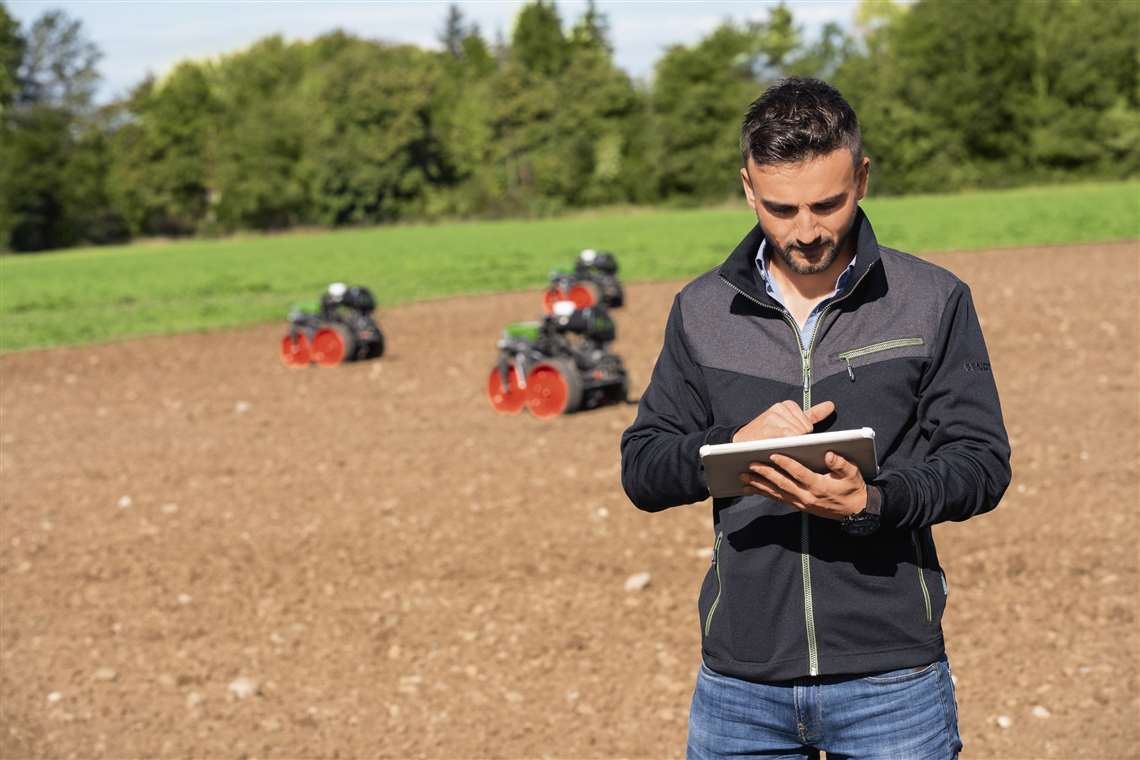
AGCO Corp. presented the Fendt Xaver concept during the 2017 Agritechnica trade show in Hanover, Germany. Following extensive testing, the little machine has been redesigned and its robotics system enhanced.
“The cornerstones of our swarm system are scalability in terms of investment costs and impact, minimizing failure risks from robot redundancy and integrating autonomy and precision farming,” said Dr. Benno Pichlmaier, director, Global Technology & Innovation, AGCO Corp. “When sowing with the Xaver, it maps the field and we can use this for all of our follow-up work, such as plant protection, mechanical weed control and fertilization.”
Just over 6 ft. (2 m) long, the ballasted robot has a maximum total weight of 550 lb. (250 kg) and tips the scales at less than 330 lb. (150 kg) empty. Ground pressure is up to 80% lower than with conventional machines, said the company.
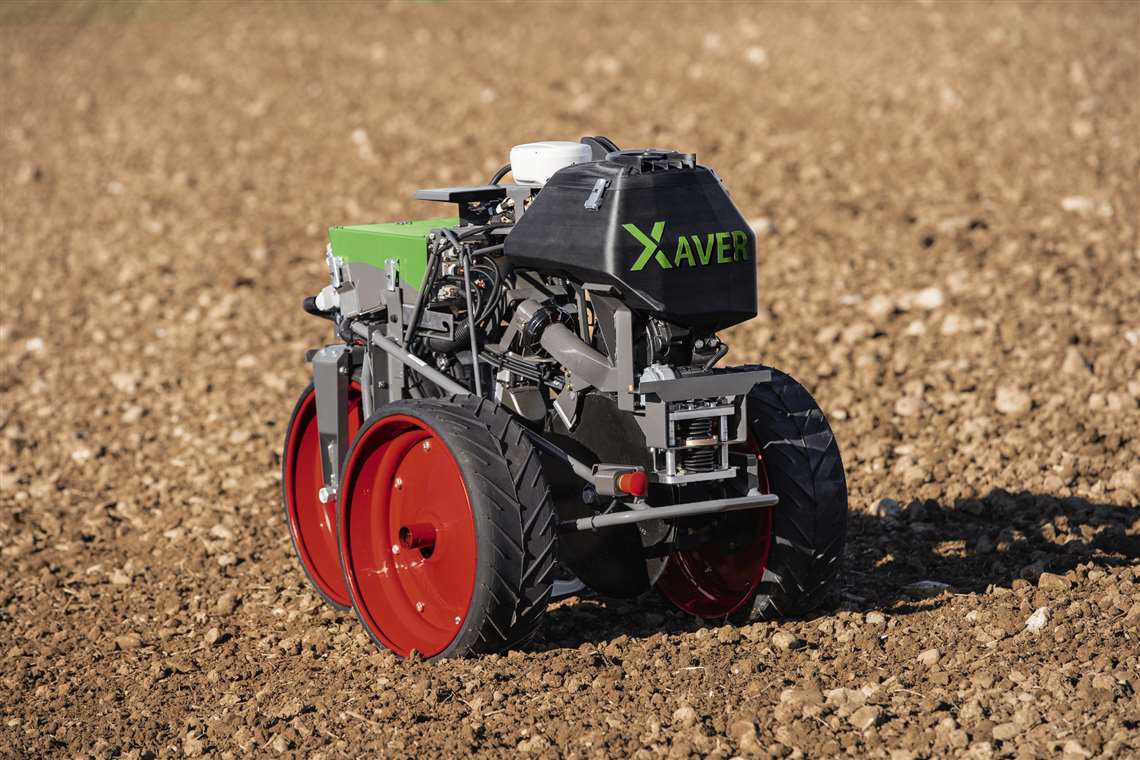
The latest Xaver has a three-wheel, all-wheel-drive design. The rear wheel steers and propels the robot and compacts the soil around the seed to initiate germination. The company said the larger wheels offer increased ground contact, greater ground clearance and more precise depth guidance. The seed tank capacity has been enlarged to carry enough for about an acre (0.5 ha) at 90,000 grains and acre.
The robot’s 2.6 kWh lithium-ion battery runs an electric direct-drive system, which the company said it good for 1.5 hours before returns to a base station for charging. A swarm of six robots could achieve coverage of around 7.5 acres an hour (3 ha/h).
The field robot has Fendt’s VarioGuide lane guidance system and is integrated into the FendtOne control platform. The farmer can access the fleet or individual robots ion a tablet or PC.
“The prerequisite for swarm technology is a reliable network coverage for communication,” said Pichlmaier. “Going forward, we will use the imminent implementation of the digital strategy with a 5G network expansion in Germany and worldwide.”
People scale
“We’re building something that I describe as being ‘people scale,’” said Charlie Andersen, CEO of Burro, a Philadelphia, Pa.-based developer of collaborative agricultural robots. “When you get down to people scale and can replicate some of the work a person does in the field, you can really save money on labor. Labor is oftentimes about a quarter of a grower’s revenue, and in the case of table grapes, which is the dominant crop we’re in right now, labor is about half of revenue, with more than half of that around harvest.”
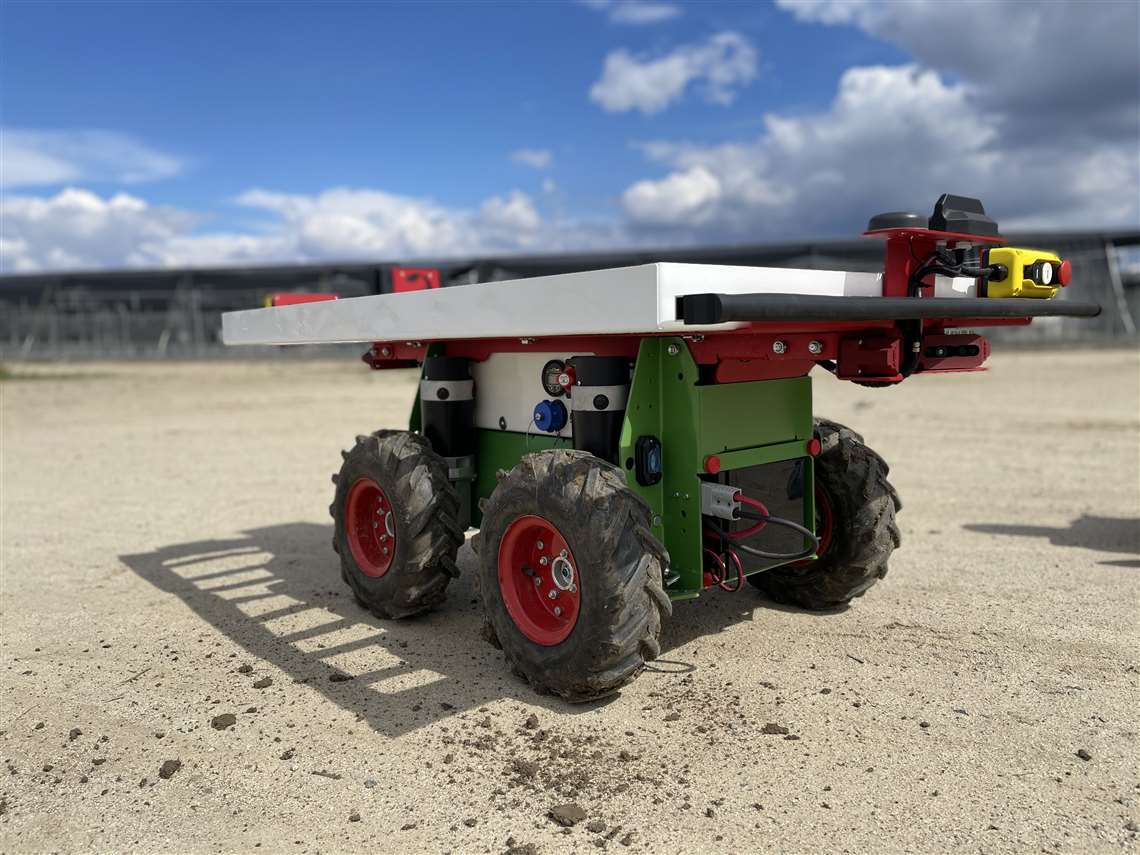
Burro is an autonomous, self-propelled cargo-toting platform that helps field crews pick fresh fruit safely and efficiently. Andersen said the machines are learning to do much more, as well.
“The approach to artificial intelligence (AI) we’re taking is to begin with a collaborative robot that works alongside people,” said Andersen. “Operators can get a productivity boost from the Burro that helps it pay for itself in a season or less. It’s a mobile autonomous platform that’s built around computer vision and is basically learning as it works. We think that’s the right way to start – mastering on-farm mobility today where most people work, while paving the way toward a whole host of further autonomous functions around crop data and dexterity, such as pruning, picking and de-leafing.”
Burro has a length of 54.7 in. (138.9 cm) long, height of 27.3 in. (69.3 cm) tall and width options of 27 in. (68.5 cm) or 36.25 in. (92.07 cm), the latter for table grape growers. It weighs 420 lb. (190 kg) and rides on four 14.5 x 5.00-6 tires and has a maximum payload of 500 lb. (226 kg).
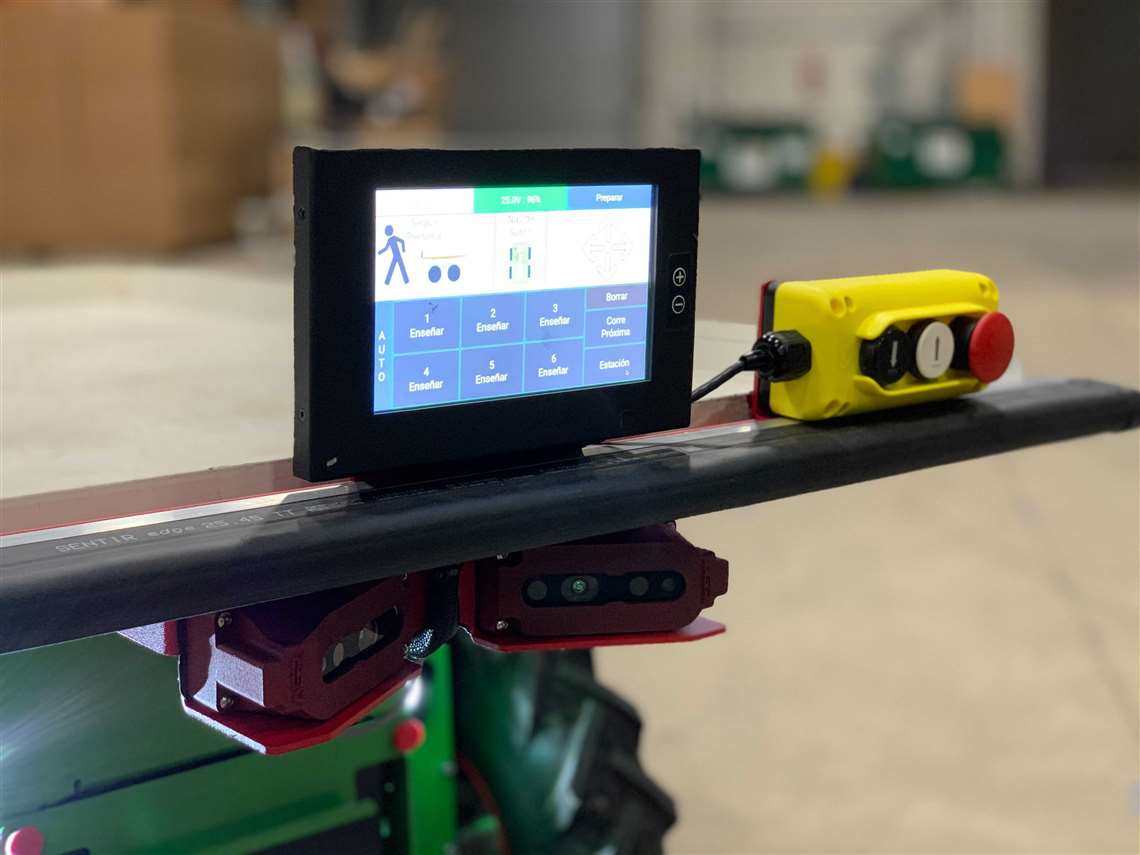
It is powered by 5 hp wheel motors and two 135 ah sealed lead acid batteries with extended range options available. The standard battery pack is good for a range of 8 miles and requires a battery charge time of 12 hours. Batteries can be swapped in the field. A sealed, forced air cooling system keeps it from overheating on 120 F days. The overall design was developed to be robust, said the company, with a goal of an 8000-hour lifespan before it needs to be rebuilt.
Burro might look like a table with wheels, but it is more capable than that. Twelve cameras keep an eye on its surroundings, as does RTK GPS and a 4G LTE modem, along with a CPU and GPU. These cameras can also help Burro pay attention to crop health, such as pests or diseases.
“Those cameras tell it how to navigate through the world,” said Andersen. “Now we are adding cameras that face the crop, as well. They’re higher fidelity and permit us to gain a lot of insight about the crop itself. About half the machines we will ship this year will have a permanently installed crop data camera kit on them, and every single robot is online.”
Burro was designed so a crew could be up and running with the Burro after less than ten minutes of training. It follows the crew to learn the routes and as they better understand the world around them, those routes can be easily extended.
In picking operations, the Burro can replace wheelbarrows or trailer solutions for moving fresh fruit off the field. Typically, six to eight people will work with one robot.
One of the challenges with developing autonomous farm machinery versus self-driving automobiles, said Andersen, is that data sets are readily available for engineers and software developers to test algorithms for specific tasks, such as parallel parking. For most specialty crops, however, no data exists.
“We’re planning to create a data repository that other ag companies can access,” said Andersen. “We have a ton of data that other companies can use to create more value for our customer base.”
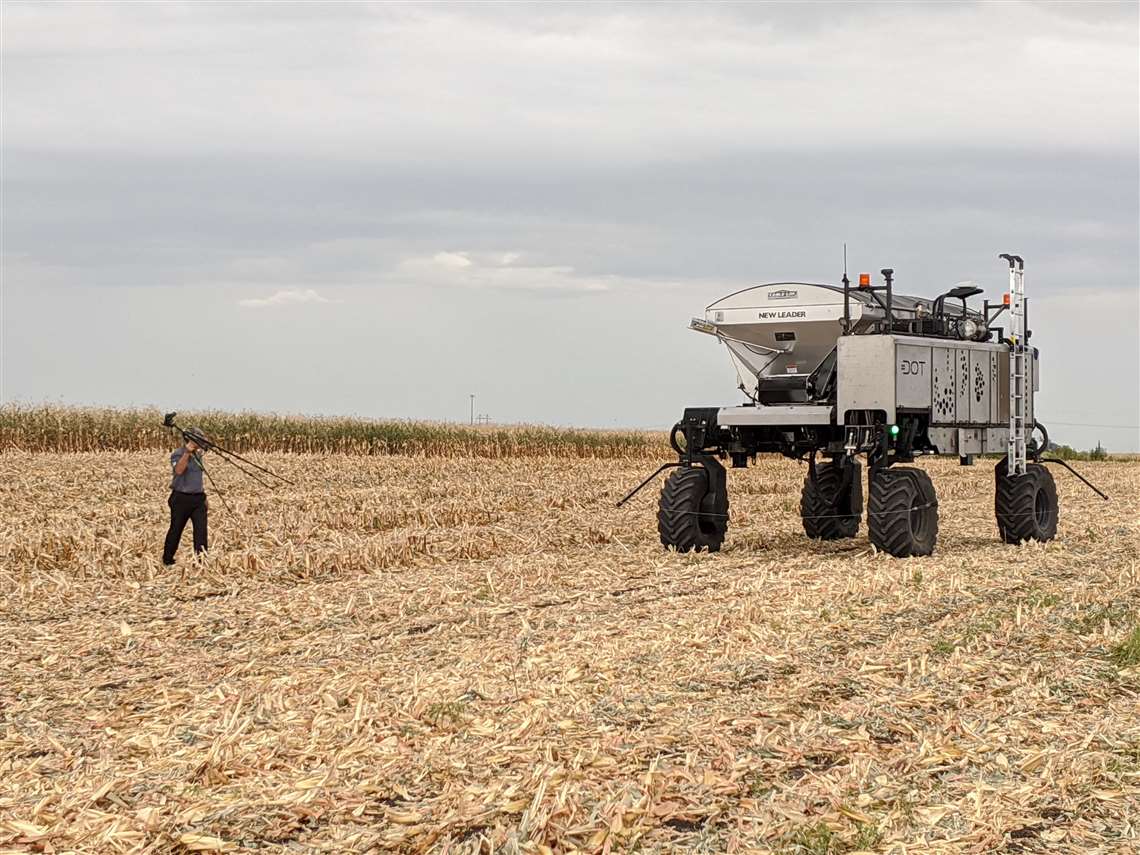
Life imitating art
“I think autonomy will create a new class or new shape of machinery that will be smaller than people-operated equipment,” said Andersen. “It’s akin to something like Disney’s Wall-E,” the animated character from the 2008 science fiction comedy. If you imagine what the Wall-E character’s evolution may have been, it probably didn’t start as an “emotive being that’s got dexterity and can go and do everything. It probably started as autonomous cart, working alongside people. Overtime, it evolved, and it could eventually perform more functions on its own.
“That’s why we are focused on specific use cases, so the technology can build on its capabilities over time. As we fill out the data set, then logically the final step will be to add dexterity to do whatever work people don’t want to do.”
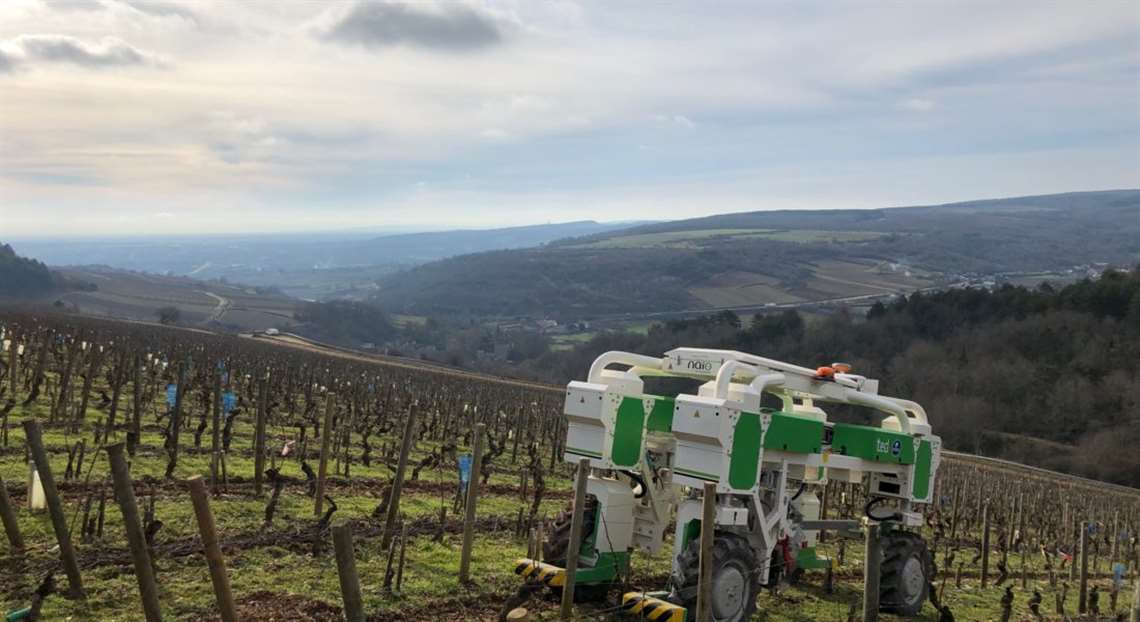
Sidebar:
Supporting future farm equipment engineering
“You men are designers and builders of tractors, but I doubt if many of you have had much experience operating tractors. Otherwise you would change the seats on them.”
-Leon W. Chase, professor, University of Nebraska
“Something else that will further add to the diversity in agriculture equipment is that at no other time have the major farm equipment companies had as many people involved in key engineering and design decisions that have no other connection to agriculture,” said Darrin Drollinger, executive director, American Society of Agricultural and Biological Engineers (ASABE), St. Joseph, Mich. “If you didn’t grow up working on the tractor or another traditional ag machine, you won’t have any preconceived hang-ups that those machines must keep a certain configuration.”
The other side of that situation is perhaps best illustrated by the quote at the right from Professor Chase, who was instrumental in starting the Nebraska Tractor Test Laboratory to prevent hapless buyers from becoming unpaid test engineers. He spoke those words to a room of engineers in July 1919, during a dinner that followed tractor field demonstrations in Wichita, Kan.
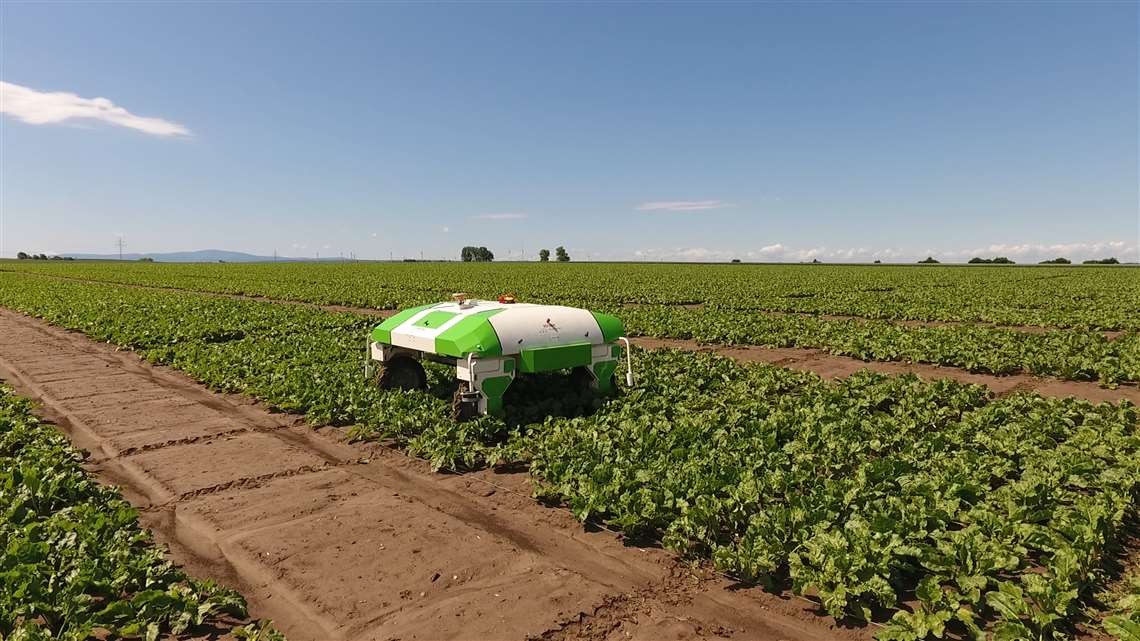
The more things change, the more they stay the same. In 1919, farm tractors were relatively new – young ag engineers could not be expected to have grown up around them. Many of today’s software engineers and roboticists are similarly far removed from agriculture.
“That can be an issue,” said Scott Cedarquist, director of standards and technical activities, ASABE. “When companies and government entities hire people with no ag background, they at least need some basic training. We’ve helped new hires for the USDA, and we’ve discussed doing something similar for some of the major OEMs. They recognize that not everyone knows why there are tracks on some tractors. They’ve never heard about soil compaction. Running through some of the reasons we do things has a lot of merit for some of these smart, young, technical people.”
ASABE is an educational and scientific organization dedicated to the advancement of engineering applicable to agricultural, food and biological systems. It has members in more than 100 countries. Educating engineers and non-engineers about the value of agriculture and the ways engineering can improve upon it is one of its missions. It also leads the development and maintenance of technical standards.
“We will often talk with companies that have developed and tested a product, and as it moves into production, they want to make it safe,” said Cedarquist. “They’ll learn that in their state or country there are lighting and marking requirements for traveling on the road. Then they’ll come to us.”
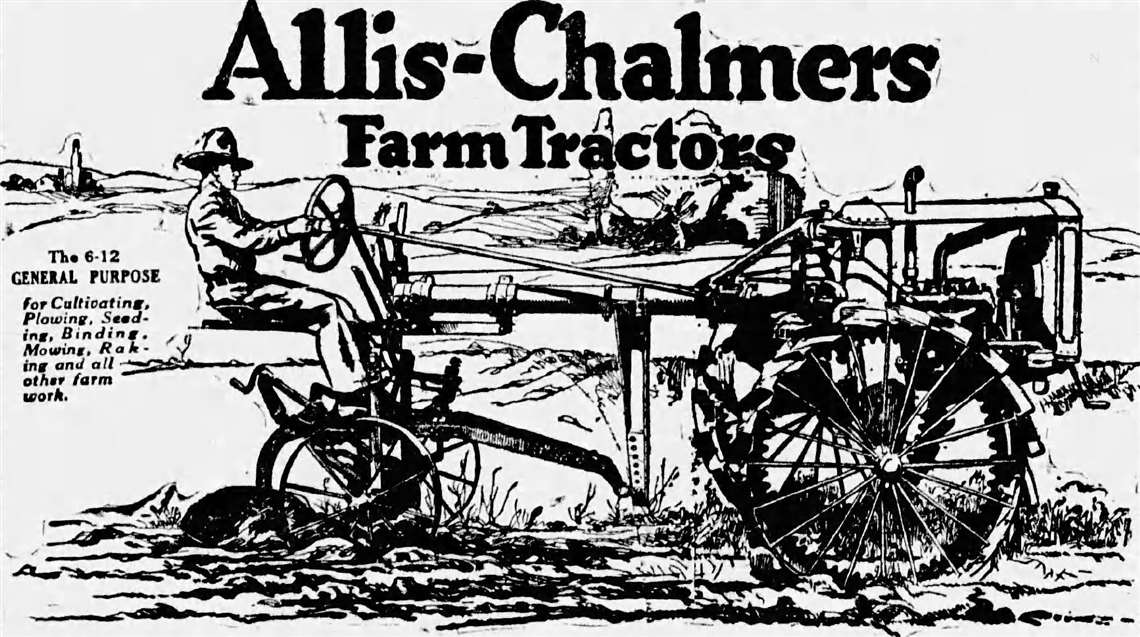
Written by Chad Elmore, this article originally appeared in the May 2021 issue of Diesel Progress magazine.
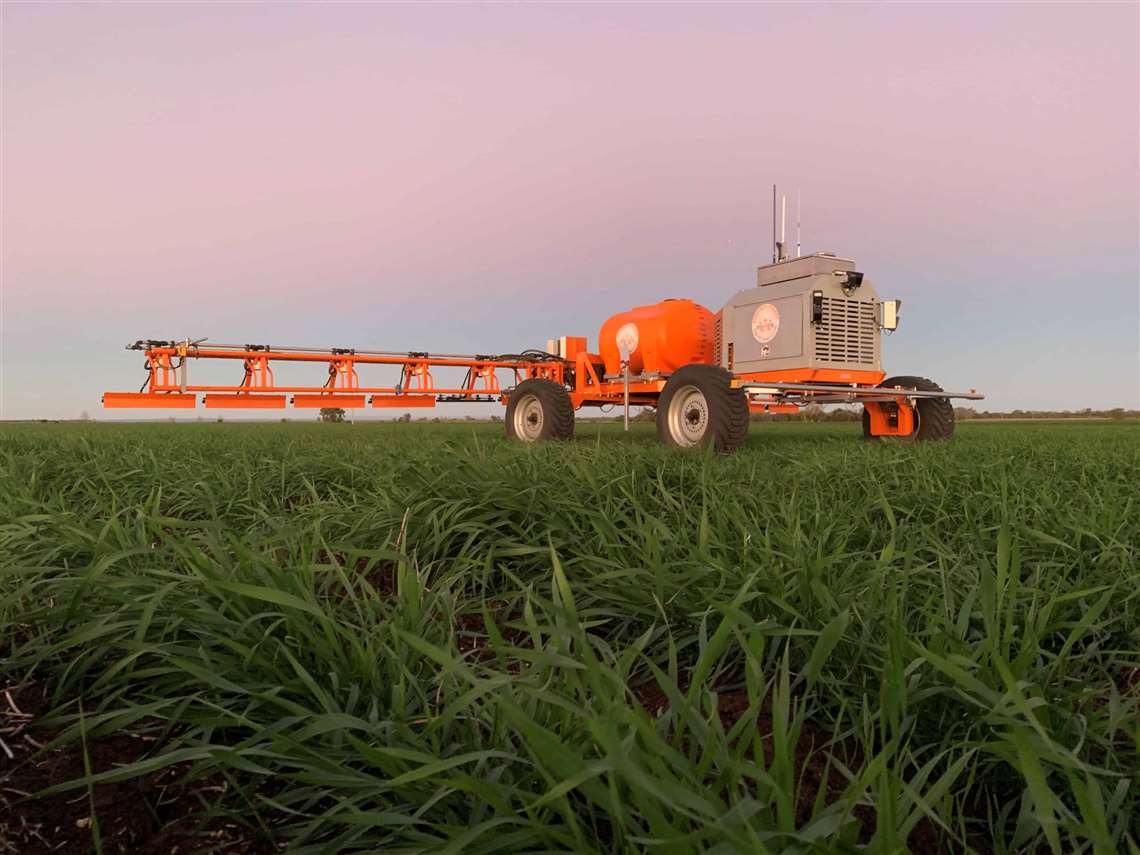
POWER SOURCING GUIDE
The trusted reference and buyer’s guide for 83 years
The original “desktop search engine,” guiding nearly 10,000 users in more than 90 countries it is the primary reference for specifications and details on all the components that go into engine systems.
Visit Now
STAY CONNECTED



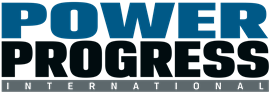
Receive the information you need when you need it through our world-leading magazines, newsletters and daily briefings.
CONNECT WITH THE TEAM
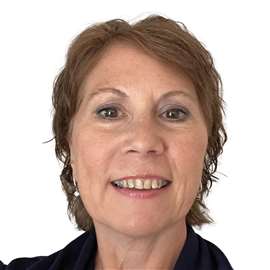
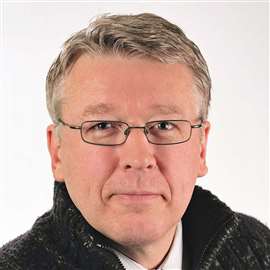
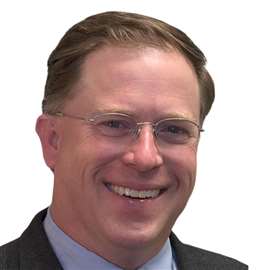
