How below the hook devices are improving safety on site
09 August 2024
New below the hook devices are improving the safety and efficiency of lifts, despite challenging project requirements. Niamh Marriott reports.
Used for a range of heavy lifting work, new below the hook products, both standard and bespoke, are being developed, tested and launched to market. These devices, often viewed as an extension of the hook, can be tailored to each specific lift, enhancing both the efficiency and safety of a project.
Safe tests
The safety precautions of a load test can dramatically affect the outcome. Spanish automation and lifting equipment manufacturer Elebia Autohooks launched its D10 drop test release hook, designed specifically for load testing. The company says it offers both improved safety and efficiency in load handling applications.
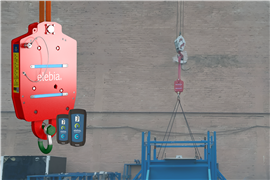
The 10 tonne load drop hook is controlled remotely which improves the safety of the work, as there is no need for manual intervention, climbing or the use of ropes or cables. The company adds that the automated quick drop systems also saves time by reducing workflows and comes equipped with high capacity battery for extended productivity.
Vertical position
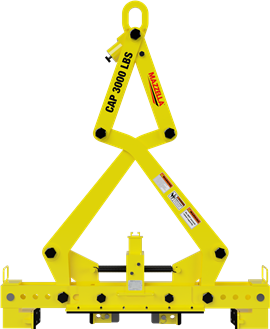
USA-based lifting equipment provider Mazzella has engineered and manufactured a below the hook device for lifting coils of steel in a vertical position.
As the vertical lifting tong extends, the outer pads come together to press against the outer diameter of the coil, while the inner pads spread apart to press against the inner diameter of the coil.
The outer pads are adjustable in 140 mm increments with the largest distance in the open state being 1,300 mm, compressing down to 1,120 mm in the closed state.
The inner pads are adjustable in 100 mm increments with the largest distance in the open state being 360 mm.
Loss reduction
Dropped objects are a safety hazard in industry and lead to numerous accidents.
The Green Pin Catch Shackle, made by Dutch manufacturer Van Beest, prevents the accidental dropping of shackle bolts, nuts, cotter pins and even complete shackles which, the company says, helps prevent injuries or deaths.
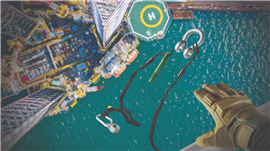
These shackles have an attachment point on each component to connect them to a lanyard. The product was developed in co-operation with DROPS, a non-profit organisation focused exclusively on dropped objects prevention schemes. It is suitable for both one-leg and multi-leg systems and is available in a range with a working load limit (WLL) from 1.8 up to 8.6 tonnes.
Load connection
USA-based manufacturer The Caldwell Group expanded its series of RUD ACP-Turnado lifting points, with Max and Supermax versions. A lifting point is a key below the hook product because it is the connection between the lifting gear and the load.
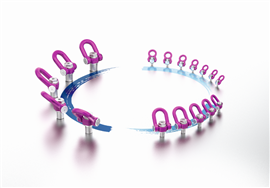
ACP stands for automatic centre point. The RUD ACP-Turnado’s lift shackle turns in the load direction automatically when it is lifted, so it cannot remain in an incorrect position. Dangerous transverse loads and a sudden drop of the load are excluded, due to a unique spring mechanism.
With the relaunch, RUD has gone one step further in terms of WLL, the company says. The ACP-Turnado lifting point is now available from 10 to 100 mm, meaning the product can be used for many applications, including extreme heavy duty use.
A practical feature of Max and Supermax versions is the deflector disc. It carries an angle marking and enables a quick, simple assessment of the current stop angle. It has a universal bolt head with internal and external hexagon, which enables optimum handling.
The bolt is captive, but still replaceable, which is useful in many applications, Caldwell adds.
Continuous advancements in below the hook devices are significantly enhancing the safety and efficiency of lifting operations, meeting the demands of complex projects and ensuring better performance and protection on site.
Offshore operations
UK-based specialist lifting equipment manufacturer, Modulift, is facilitating the construction of a complex offshore energy project in the North Sea. Claimed as the world’s first artificial energy island, Princess Elisabeth marks a significant milestone in renewable energy infrastructure development.
The island is being constructed by TM Edison, a joint venture between European marine companies Jan De Nul and DEME Group.
Assembling the infrastructure of the energy island requires lifting and manoeuvring large structural elements and equipment. The outer perimeter of the island will be made up of a series of concrete caisson structures. These are built onshore before being transported to their offshore location.
Ruben Verschueren, site superintendent of civil works at TM Edison says, “Modulift’s spreader beams have been integral to the construction of the concrete sections, with one formwork section weighing around 17 tonnes and 10 metres in length. We are using a 1-over-1 configuration, utilising a MOD 34 spreader beam at the top and a MOD 24 on the bottom. Modulift spreader beams have been instrumental in safely hoisting the formwork into position.”
Sarah Spivey, Modulift managing director, adds, “We are very proud to be part of this groundbreaking project.”
Construction of the Princess Elisabeth Island is expected to last until the end of 2026.
Bespoke beam
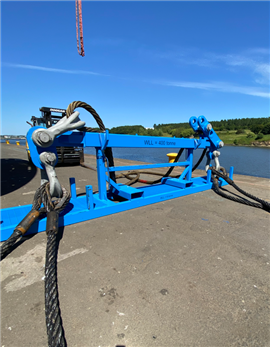
UK-based lifting equipment provider Tusk Lifting required a 400 tonne lifting beam to ensure safe lifting of giant sub-sea cable reels. Tusk turned to beam UK specialists Britlift to design and manufacture the product.
“Our client needed a beam that could lift cable reels of up to 400 tonnes, with offset centres of gravity,” says Julie Montgomery, sales and systems support lead for Tusk Lifting. “We brought Britlift the challenge and they came up with the solution.”
Working closely with Tusk Lifting and its client, Britlift supplied custom box spreader beam with a cradle and stand and heavy-duty sling adjuster. Its technical team specified a more hardwearing paint finish to better withstand offshore conditions.
Britlift also supplied proof of load testing and magnetic particle inspection, with an enhanced quality pack which included an inspection and test plan as well as welding maps with related procedures and qualifications, plus reports covering structural calculations and the paint specification.
“We have worked with Britlift many times before and have full confidence in their abilities,” adds Montgomery. “The quality pack and documentation they provide is always spot on and their communications at every stage of the job are excellent.”
POWER SOURCING GUIDE
The trusted reference and buyer’s guide for 83 years
The original “desktop search engine,” guiding nearly 10,000 users in more than 90 countries it is the primary reference for specifications and details on all the components that go into engine systems.
Visit Now
STAY CONNECTED



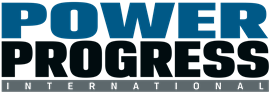
Receive the information you need when you need it through our world-leading magazines, newsletters and daily briefings.
CONNECT WITH THE TEAM
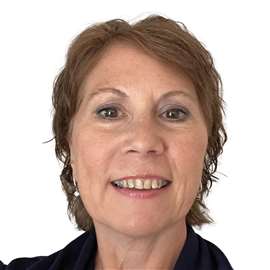
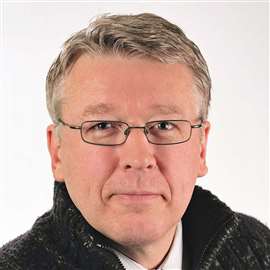
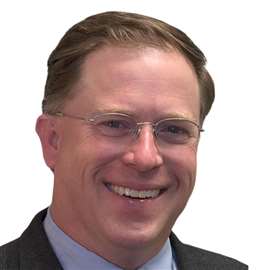
