Bloom Energy supplies fuel cell power system for Ferrari HQ
29 August 2022
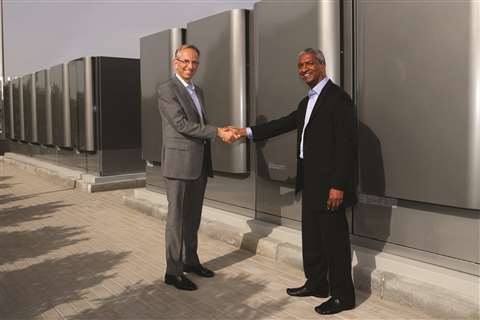
A great many companies and organizations around the world are looking to decarbonize. Some, however, are doing it faster than others.
Italian automotive icon Ferrari is driving toward carbon neutrality in manufacturing at its Maranello, Italy, headquarters by 2030. That effort is being accelerated by a 1 MW solid oxide fuel cell (SOFC) system supplied by California’s Bloom Energy.
The project with Ferrari – a signature brand in the luxury and automotive sectors for 75 years – marks Bloom’s entry into the European Union and Italian markets and is the first step toward potentially larger projects between the two companies, Bloom Energy said.
“Ferrari is a legendary trailblazer in the luxury automotive industry, and Bloom Energy commends their commitment to leading in both operational excellence and carbon neutrality across their entire value chain by 2030,” said KR Sridhar, founder, chairman and CEO, Bloom Energy. “By collaborating, we’re showcasing how energy-intensive industries such as manufacturing can be decarbonized through clean, reliable energy.
“Ferrari, like Bloom Energy, has a commitment to uniqueness, innovation, technology leadership and continuous learning that makes them the ideal partner for Bloom’s entry into the European manufacturing landscape, where energy resilience is more crucial than ever. Bloom Energy’s fuel cell platform is a best-in-class solution for a best-in-class luxury automaker.”
Conserving energy
The Bloom Energy Servers were installed at Ferrari in May and are expected to be commissioned and go fully online shortly. When operating at peak efficiencies, they will initially provide 5% of the energy needed at Ferrari’s Maranello headquarters and manufacturing center.
The Bloom Energy Servers are expected to cut gas requirements by around 20% from the combined heat and power (CHP) system now in use at Ferrari, while also reducing emissions. This will enable Ferrari to bolster energy conservation amid record-high energy prices, while simultaneously reducing greenhouse gas emissions and improving local air quality, with virtually zero harmful air pollutant emissions, such as sulfur oxides, nitrogen oxides and particulate matter.
Bloom Energy’s fuel-flexible platform also equips Ferrari to lead the race in Italy’s emerging hydrogen economy. According to Italy’s Ministry of Economic Development, the country plans to cover one-fifth of its overall energy demand from hydrogen by 2050.
Beyond fuel cells
Along with its fuel cell products, Bloom Energy is also using its solid oxide technology to develop electrolyzers for producing hydrogen from low- and zero-carbon sources. Earlier this summer, the company and LSB Industries, a North American producer of industrial and agricultural chemicals, announced a plan to install a 10 MW solid oxide electrolyzer at LSB’s Pryor, Okla., facility. The project is expected to generate green hydrogen that will contribute to the synthesis of approximately 13000 metric tons of zero-carbon ammonia per year.
The 10 MW solid oxide electrolyzer installation will contribute to making LSB’s Pryor facility the largest green ammonia production site in North America, Bloom Energy said. ThyssenKrupp will co-develop the multi-phase project, developing an initial engineering design to convert a small portion of existing conventional gray ammonia capacity at LSB’s Pryor facility into green ammonia. Bloom Energy will then install, operate and maintain the 10 MW electrolyzer at LSB’s Pryor facility, targeting hydrogen production to begin in 2023.
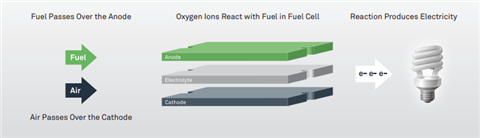
All types of fuel cells share a common design and process: a negative electrode (the anode) and a positive electrode (the cathode) positioned around an electrolyte undergo an electrochemical reaction to produce an electric current. Electrolytes vary among fuel cell types and, depending on the electrolyte deployed, the fuel cells undergo slightly different electrochemical reactions, use different catalysts, run on different fuels and achieve varying efficiencies.
The electrolyte in a SOFC is a solid, ceramic material. The anode and cathode electrodes in Bloom’s fuel cells incorporate special proprietary inks that coat the electrolyte.
In operation, high-temperature air enters the cathode side of the fuel cell, while steam is mixed with fuel entering the anode side to produce reformed fuel. As the reformed fuel crosses the anode, it attracts oxygen ions from the cathode. The oxygen ions combine with the reformed fuel to produce electricity, water and small amounts of CO2.
The water gets recycled to produce the steam used in the fuel reforming process, and the electrochemical process also generates the heat required to keep the fuel cell warm and drive the reforming reaction process. As long as fuel and air are available, the fuel cells continue converting chemical energy into electrical energy, providing an electric current directly at the fuel cell site.
The SOFCs are then combined to form a fuel cell stack and multiple stacks are used to create an Energy Server module. Four to six modules combine to form one 200 to 300 kW Energy Server that produces power in a footprint roughly equivalent to that of half a standard 30 ft. shipping container.
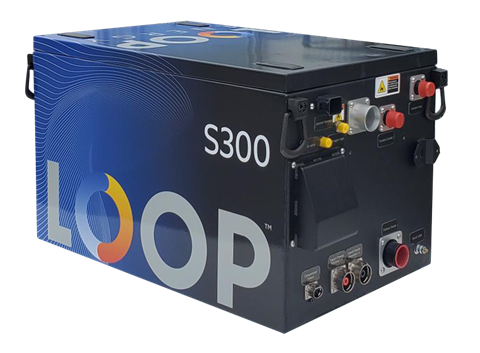
This spring, British Columbia-based Loop Energy sold a 30 kW proton exchange membrane (PEM) fuel cell system to Hylife Innovations, a Dutch developer of sustainable power solutions. Loop’s S300 fuel cell system will be integrated into Hylife’s Innovahub, which powers residential districts by utilizing green hydrogen to power residential buildings in the Netherlands.
The sale was facilitated by Loop Energy channel partner Aliant Battery, an Italian developer of lithium batteries. Hylife’s solution aims to combine battery technology and a hydrogen fuel cell system to generate electricity for “Green Residential Hub” applications within neighborhoods. Aliant Battery and Loop Energy will lead the engineering of the two technologies to provide a high-efficiency hydrogen electric generator. Aliant Battery was added as a qualified ecosystem partner in Loop Energy’s Total Customer Care program in May 2021.
Loop Energy’s partnership with Aliant Battery previously resulted in the sale of an S300 fuel cell system to emfeld Gmbh to develop generators for film sets in December 2021.
POWER SOURCING GUIDE
The trusted reference and buyer’s guide for 83 years
The original “desktop search engine,” guiding nearly 10,000 users in more than 90 countries it is the primary reference for specifications and details on all the components that go into engine systems.
Visit Now
STAY CONNECTED



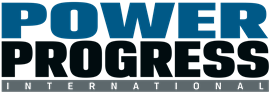
Receive the information you need when you need it through our world-leading magazines, newsletters and daily briefings.
CONNECT WITH THE TEAM
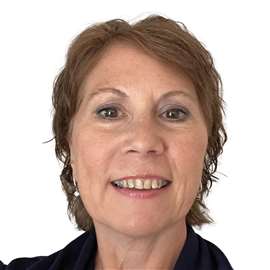
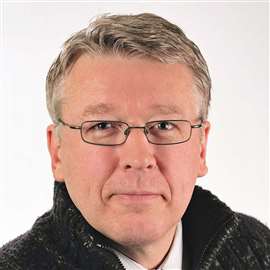
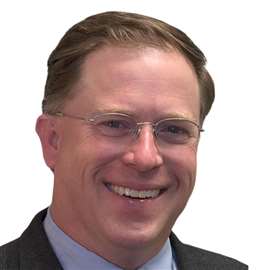
