Cummins QSK95 digs into mining market
16 September 2021
Cummins brings its largest 4400 hp QSK95 diesel to global mining markets, making it the most powerful engine ever to be developed for ultra class trucks. Mike Brezonick reports.
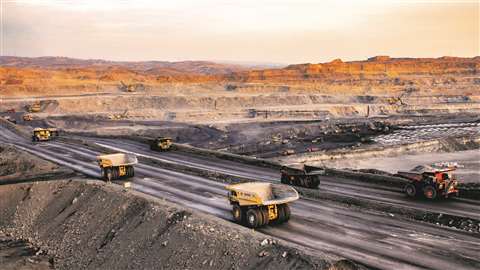
Cummins unveiled the QSK95 in late 2011, the largest home-grown high speed diesel engine in the company’s history. Now, after seeing it thrive in applications such as power generation, rail traction and marine, Cummins has decided it is time for its biggest engine to finally get down and dirty as the company is launching a version for surface mining applications.
With a top rating of 4400 hp with 13,020lb ft. of torque at 1800 rpm, the 16-cylinder, vee configuration diesel targets equipment such as 400 ton haul trucks and large mining shovels. A 3800 hp rating is also offered for mining equipment applications requiring increased fuel economy and longer life to overhaul.
“At Cummins we have developed a deep understanding of the key profitability metrics for our customers,” said Gary Johansen, vice president Power Systems Engineering at Cummins, “In the mining industry that metric is the cost of production. Mining companies are now more than ever looking for ways to achieve the lowest cost of production, and to do so in the most sustainable way possible.
“At Cummins we have made it our goal to enable miners to achieve that by applying cutting-edge technology to improve product performance, reliability and durability. We keep pushing to deliver more from our products and we have applied this mindset to bring our most powerful engine ever to the mining industry.”

Cummins QSK95 designed to thrive
Johansen said the QSK95 “is designed specifically to thrive against key mining requirements, reliability, faster cycle time, increased power at altitude, fuel economy, service repair time, life to overhaul and ability to remanufacture the engine system.”
The QSK95 was one of the largest engine developments in the history of Cummins, both in terms of engine size – it has a bore and stroke of 190 x 210 mm and a total displacement of 95.3 L – and financially, as the company spent upwards of US$300 million on its clean sheet design.
Its availability for mining is also somewhat appropriate in that its code name prior to launch was “hedgehog,” a critter known for feeling at home in the dirt.
Like all Cummins engines, the QSK95 incorporates a host of the company’s engine and component technologies.
Among the most significant is a Modular Common Rail Fuel System (MCRS) that eliminates the long fuel rail used in most common rail systems, instead maintaining a pressurized fuel volume within the injector body itself. The system can deliver multiple injection events at pressures up to 31,000 psi.
The engine also incorporates a quad-turbocharger layout that utilizes Cummins Turbo Technologies’ HE 900 frame single-stage turbochargers engineered to deliver strong performance and responsiveness at high altitudes. Accordingly to the company the use of lighter, single-stage turbochargers contributes to improved exhaust manifold life.
Four Cummins Electronic Control Modules (ECMs) – one for each bank of four cylinders – are grouped together for easy access at the front of the engine under a protected cover, with an interface providing diagnostic access.
Cummins said that the ductile iron engine block incorporates a deep skirt and internal bedplate, both of which help reduce vibration and noise, while also enabling the engine to be rebuilt multiple times.
A single piece forged steel piston is engineered for better durability and reuse capability at rebuild. The hardened power cylinders have midstop cylinder liners and dual piston cooling nozzles, designed to reduce piston ring temperatures and increase wear resistance. The company claimed that service life is also enhanced through the use of more robust engine bearings.
Filtration components from Cummins Filtration include a triple element 5 micron primary lube oil filter/water separator, a secondary filter incorporating a 3 micron/2 micron, filter-in-filter design, an air cleaner with dry replaceable filter elements and a Cummins Impactor crankcase breather. The filters and oil coolers are mounted on the outside of the engine to improve service access.

Cummins drives towards mining sector
Johansen elaborated, “The QSK95 is really for ultra class trucks demanding the highest productivity and speed in the mines. We have sold over 1,200 QSK95s in more than 20 countries in a wide range of applications, and now we are bringing it to our mining customers.
“We believe the QSK95 will run faster and longer than other products out there, and will thereby significantly lower the total cost of production for mining companies.”
The QSK95 is also available with PrevenTech, Cummins Cloud-based software designed for engine health monitoring and remote diagnostics.
PrevenTech can map equipment locations via GPS, listing problematic assets according to severity, which Cummins claimed helps focus service and troubleshooting.
It can also provide alerts when machinery is being operated improperly, such as if a cold engine is being run at rated speed, if idle times are being stretched or if there’s excessive cranking.
Johansen added, “We are continuously evaluating ways to improve productivity and performance of our engine portfolio. Along with the QSK95, we have redesigned QSK78 MRCS engine to offer better performance, reliability and durability.
“Field trials and initial results from units in Chile show a marked improvement in fluid consumption, noise and vibration, harshness profile and transient response.
“We have also taken our MCRS technology and made it available as an upgrade kit for existing fleets of QSK78 HPI engines, which can be outfitted during the scheduled engine rebuild process for Tier 2 equivalent and unregulated markets.
“Cummins will also be launching the EPA Tier 4 final and EU Stage 5 version of our QSK38 in early 2022, targeting excavator, wheel loader, and haul truck mining applications.
“The engine will meet the latest emission regulations while offering the same reliability and durability that customers have come to expect from Cummins. This engine is very compact and fits the space claim within OEM chassis designs.”

Heavy investment in Cummins’ Engine Plant
The QSK95 is built at the Cummins High Horsepower Engine Plant at Seymour in Indiana, USA.
“We have invested US$110m to build the QSK95 manufacturing and testing capability in the plant,” Johansen said, “including a new cylinder block machining line, new assembly line production test cells and a new engineering office with 500 engineers onsite.”
The launch of the QSK95 and the upgrades and redesigns of the other High Horsepower products demonstrate that for all its recent activity in fuel cells, electrification and other New Power technologies, Cummins’ commitment to diesel engines has not wavered.
“There is still a lot of work to be done with the existing technology, which we are investing in and advancing all the time,” said Norbert Nusterer, vice president of Cummins Inc. and president of the Power Systems segment. “We are striking a balance, I think in a really healthy way, by advancing diesel technology and investing in the technologies of the future.”
Click here to learn more about Cummins Inc.
This story first appeared in the September issue of Diesel Progress. For a free print or digital subscription, click here.
POWER SOURCING GUIDE
The trusted reference and buyer’s guide for 83 years
The original “desktop search engine,” guiding nearly 10,000 users in more than 90 countries it is the primary reference for specifications and details on all the components that go into engine systems.
Visit Now
STAY CONNECTED



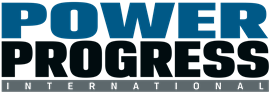
Receive the information you need when you need it through our world-leading magazines, newsletters and daily briefings.
CONNECT WITH THE TEAM
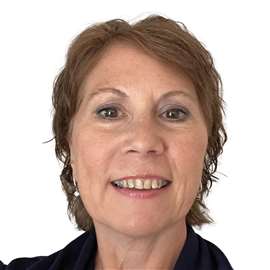
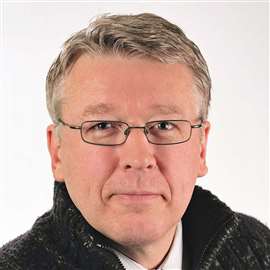
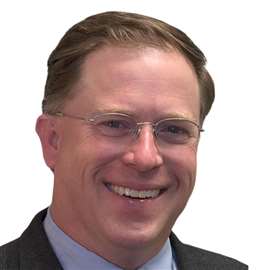
