Deere Power’s Electrification Program
09 April 2019

With an eye on a range of off-highway applications, John Deere Power Systems (JDPS) is using the Bauma show in Germany to roll out its new electrification strategy; an electric and integrated drivetrain system portfolio comprised of both power generation and traction drive components.
“In this emerging market for electrification technology, we are working closely with our OEM customers to understand their application needs,” said Darren Almond, drivetrain product planning manager for John Deere Power Systems. “While the off-highway industry continues to grow and adapt to changing market needs and value propositions, its demands for reliability, durability, and performance remain the same. A rugged market requires a product that can meet expectations in a variety of applications — whether diesel, hybrid or electric.”
JDPS and John Deere Electronic Systems (JDES) are developing integrated, series electric drive components designed in a modular fashion to provide power generation with a diesel engine or electric traction drive solutions that installs to a vehicle’s existing axle.

Brand new at bauma, JDPS will show a single-speed transmission and generator pump drive (above) as prototype opportunities scheduled to begin production by the end of this year. New three-speed transmission prototypes for select applications will be available next year.
The full electric drivetrain system will include compact, high-speed electric motors, controlled by power electronics from JDES. These eMachine components are integrated with various John Deere pump drive and transmission solutions resulting in a flexible and integrated drivetrain portfolio for ease of OEM implementation, Almond said.
For OEM applications ranging from variable speed power generation to fully electric vehicle transmissions, the modular and scalable electric drivetrain component designs offer power generation and traction drive solutions up to 200 kW per unit.
Application Flexibility
One of the keys to this approach is application flexibility. “Frequently you’re dealing with situations where a manufacturer wants to electrify a traction drive, but still requires power for the hydraulic systems. With this dual-purpose solution, we can have both a hydraulic pump stack and a high power electric generator on the same gear box,” Almond said

“Another interesting aspect is we can take that motor and put it on the front side of one of our pump drives. Then that pairing can serve as an electrically-driven hydraulic drive which can be used in a hybrid or full battery electric vehicle application,” he said.
“That’s a real advantage when you’re talking about ease of an electric vehicle conversion. An OEM might say, ‘I want to go into full electrification, but I don’t know if I have the traction drive for it. I have a hydrostatic transmission.’ In this situation, we can electrically drive the hydraulic pump stacks, enabling a zero-emission vehicle conversion with minimal vehicle disruption,” Almond said.
“We’re offering OEMs a solution on the power generation side and a solution on the traction drive side independently. If they need both for a hybrid electric application, we can support that as well.”
The key to making this work, Almond said, is managing the energy through the JDES PD400 inverter between a 700-volt DC bus (that can connect to a vehicles battery management system) and 3-phase cables to drive the motor or interface with the generator. The John Deere inverter and John Deere electric drivetrain components work together with standard interfaces to adjacent vehicle systems like engines, axles and batteries.
Early Adopters
JDPS said it is targeting early adopters of off-highway electrification technology. Specific applications include underground mining equipment (especially machines in hard rock mining), specialty railroad applications (such as yard spotters and railway maintenance machines), and material handling applications (especially those used in port operations).
Hybrid power generation is a fourth potential market. “There are entrepreneurial efforts in hybrid power generation systems with connected battery systems,” Almond said. “We’re seeing an emerging opportunity for high power variable speed gen-sets in the power generation market and believe we have a piece of the solution for gen-set manufacturers,” Almond said.
The other key driver for JDPS electrification development is integration into existing machines and production systems. “We have manufacturers telling us they want to consider electrification, but they also want to run those machines on the same manufacturing line as their other products,” Almond said.
“In our development of these solutions, we are looking closely at how we can drop these electric transmissions into the space of an existing transmission, minimizing the disruption of incorporating an electric or hybrid vehicle variant on a vehicle manufacturing line,” Almond said.
First Deere Electrification
Electrification isn’t new to John Deere. In 2013, John Deere introduced the 644K hybrid wheel loader, followed by the 944K hybrid wheel loader in 2015. In February 2019, Deere announced those two models had collectively logged more than one million operating hours.
Following the launch of the two hybrid loaders, JDPS and JDES successfully designed and demonstrated its first fully integrated OEM electric drivetrain system — a concept first introduced at bauma in 2016.
“JDES plays a major role with experience in a wide variety of OEM power electronics implementations,” Almond said. “Additionally, the robust performance of the series electric systems within the 644K and 944K hybrid loaders in the field has demonstrated our deep understanding of high speed electric motors and associated mechanical system interfaces in areas such as bearing life, component cooling and shift development.”
“There is also a system integration and controls aspect that shouldn’t be understated when we’re discussing a series electric system and the optimization of the engine performance,” he said. “The fact that we’re also an engine manufacturer and are experienced with communication between the engine, the power electronics, and the transmission provides for system level solution optimization for things like engine calibrations and transmission gear shifting.”
“The integration between all of the John Deere components offers a significant value to OEMs exploring electric drive or hybrid solutions, Almond said.”
By Mike Osenga
POWER SOURCING GUIDE
The trusted reference and buyer’s guide for 83 years
The original “desktop search engine,” guiding nearly 10,000 users in more than 90 countries it is the primary reference for specifications and details on all the components that go into engine systems.
Visit Now
STAY CONNECTED



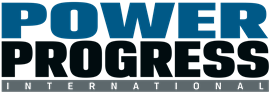
Receive the information you need when you need it through our world-leading magazines, newsletters and daily briefings.
CONNECT WITH THE TEAM
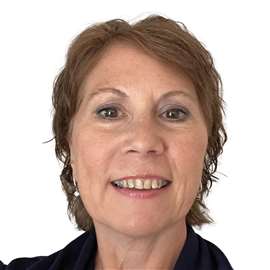
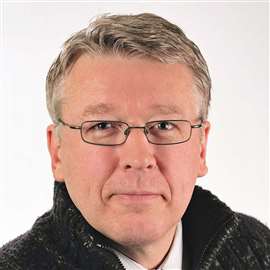
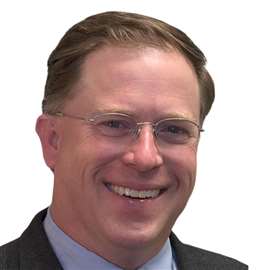
