Read this article in French German Italian Portuguese Spanish
Engine refinements mean fuel efficiency, power gains for Volvo Trucks
15 July 2024
Reduction in fuel consumption decreases volume of greenhouse gases emitted
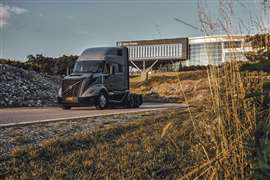
As emission requirements increase, reducing fuel consumption stands as a pivotal strategy to meet those standards. A direct correlation exists between fuel consumption and the volume of emissions released into the atmosphere.
By employing more fuel-efficient technologies or optimizing engine performance, the amount of fuel burned per unit of work decreases. Consequently, this reduction in fuel consumption directly decreases the volume of greenhouse gases emitted, notably carbon dioxide (CO2), during the combustion process. Every gallon of diesel fuel burned generates approximately 22.45 lb. of CO2 emissions, highlighting the impact that decreased fuel consumption can have on minimizing overall emissions output.
One of the big changes Volvo Trucks has brought through engineering recently is a smaller needle control valve in fuel injectors, which serve a crucial role in regulating the flow of fuel into the engine’s combustion chamber. This valve, often precision-engineered and controlled electronically, governs the amount of fuel that enters the injector nozzle. When the valve opens, it permits pressurized fuel to pass through, and when closed, it stops or restricts the flow. The reduction in size allows for more precise and rapid control over the fuel flow rate, leading to improved fuel atomization, better combustion efficiency, and enhanced engine performance. The smaller size often contributes to decreased weight and inertia within the injector, enabling quicker response times and more accurate fuel delivery, thereby optimizing the engine’s fuel consumption and emissions.
The engineering team at Volvo Trucks has also found success with shorter piston height and elongated connecting rods. By strategically altering the piston height and extending the length of connecting rods, we’ve mitigated piston side loading within the engine’s combustion chamber. This reduction in side-loading significantly reduces frictional forces and minimizes internal parasitic losses. The alteration in these components ensures smooth movement, thereby enhancing the engine’s overall efficiency and longevity.
We have also seen exciting progress with turbo compounding units. The latest thinking is to completely insulate the turbocharger and turbo compound unit to minimize heat-loss and increase efficiency. Engineers like this approach because it allows a smaller compressor and turbine wheel, enabling it to recover additional excess energy.
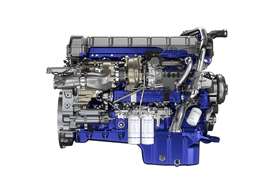
Oil pump drag
Many Power Progress readers will know that oil pumps can be a big drag on the engine, and the latest advances Volvo Trucks has implemented include the integration of a variable vane oil pump. We believe that is a pivotal advancement in optimizing oil pressure regulation while minimizing parasitic losses. This pump employs adjustable vanes that dynamically adapt to the engine’s oil pressure demands, ensuring a consistent and precise delivery of oil throughout various operating conditions. By dynamically altering the vane angles, the pump can tailor its output to match the engine’s requirements, thereby preventing excess oil flow when not needed and maintaining optimal pressure when demanded. This adaptability not only enhances engine efficiency by reducing the energy required to drive the pump but also minimizes unnecessary strain on the engine components, resulting in improved fuel economy and reduced wear and tear over time.
Vehicle efficiency transcends mere engine performance; it encompasses the synergy between various components, where the transmission plays a pivotal role. The transmission’s ability to optimize gear shifts, reduce energy loss, and harmonize power delivery significantly influences overall vehicle efficiency, showcasing that a holistic approach beyond the engine is vital in achieving optimal performance and fuel economy.
Software algorithms
Volvo Trucks introduced an automated manual transmission to the North American market in 2007, becoming standard in 2013, and recent advancements in the I-Shift transmission have accelerated shift speeds by up to 30% through a comprehensive overhaul of software, electronics, clutch mechanisms as well as precision engineering.
This is all possible because today’s diesel engines rely on refined software algorithms, which permit seamless power delivery while fuel consumption is meticulously managed. When this is paired with a reduced clutch throw and an enhanced clutch brake system that has revolutionized gear shifts, it significantly reducing transition times. This improvement not only amplifies acceleration but also minimizes energy loss during gear changes, resulting in heightened overall efficiency.
Another significant change is decoupling of the HVAC system from the engine, and Volvo Trucks’ introduction of the integrated parking cooler in the new VNL truck significantly slashed idle time by offering an independent climate control system that operates without the need for the engine to run, curbing emissions long associated with idling, and giving drivers a comfortable cabin while minimizing engine usage, reducing wear and tear while conserving fuel.
This advancement lessens the strain on the truck’s engine, aftertreatment system and batteries, effectively lowering maintenance needs and prolonging their lifecycle.
Volvo Trucks’ commitment to integrating the parking cooler prioritizes driver comfort and aligns with this company’s ethos of advancing technology that not only enhances trucking experiences but also significantly contributes to a cleaner, more sustainable transportation ecosystem.
About the Author: Duane Tegels is Volvo Truck North America’s product marketing manager for Powertrain, based at the company’s headquarters in Greensboro, N.C.
POWER SOURCING GUIDE
The trusted reference and buyer’s guide for 83 years
The original “desktop search engine,” guiding nearly 10,000 users in more than 90 countries it is the primary reference for specifications and details on all the components that go into engine systems.
Visit Now
STAY CONNECTED



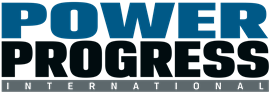
Receive the information you need when you need it through our world-leading magazines, newsletters and daily briefings.
CONNECT WITH THE TEAM
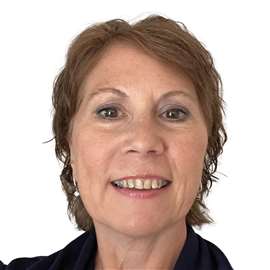
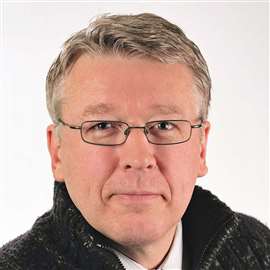
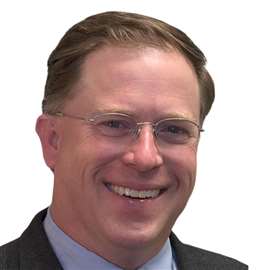
