Ethium by EControls incubates a unique battery solution
29 March 2023
The field of lithium-ion batteries is getting more crowded by the minute as suppliers emerge seeking to capitalize on global momentum toward electrification. Standing out from the masses is becoming increasingly difficult.
Jinger McPeak, vice president of Ethium by EControls, believes it’s the advantages that aren’t readily apparent that can make all the difference. Her division is what she likes to refer to as an “incubated startup,” born out of parent company EControls, a leading provider of engine control solutions founded in 1994. EControls merged with FW Murphy in 2009 to form a large, private entity. FW Murphy is a global supplier of instrumentation for gas compression engines with a history dating to 1939.
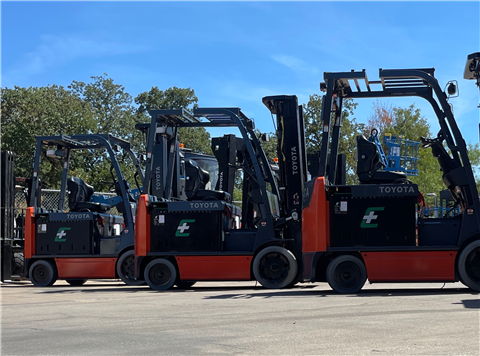
“The reason that’s important is the longevity of the company,” said McPeak. While FW Murphy may have the longest track record, EControls has been producing onboard controllers for industrial engines for forklifts – Ethium’s target market – for more than 20 years.
“There are all kinds of products on [an internal combustion] forklift that are manufactured by EControls and have been for many years. We sell them directly to the engine manufacturer or to the forklift manufacturer, and they are integrated into the vehicle, but people don’t really know that it’s an EControls product,” McPeak said.
The company, she noted, is really an engineering solutions firm that also manufactures. “Engineers from an OEM engage with engineers from EControls, and they design solutions and systems from the ground up.” This includes onboard engine controls for industrial engines ranging from 3 L to over 150 L. “We go out and solve complex problems with OEMs and that solution is then integrated into their product offering.
“I call [Ethium] an incubated startup because as EControls was continuing to produce hundreds of thousands of electronic controls and other combinations of electromechanical parts over the last five years, they’ve also been investing in the development of this lithium-ion battery from the ground up.”
Not many lithium-ion battery startups can say they have that kind of organizational strength behind them. “Once we get people to understand how big EControls is and how much intellectual property and intellectual prowess there is,” said McPeak, “it makes so much more sense for why Ethium is so different.”
Starting from scratch
Over the past 25 years, industrial forklifts have migrated away from combustion engines to electric power, with the majority adopting lead acid batteries. These batteries are now gradually being phased out by advanced technologies like lithium-ion as forklift OEMs and their customers recognize the advantages.
In order to continue to operate in this space, EControls saw a need to invest in building out the propulsion of forklifts. “They initially looked around to buy a company to start the seed of doing lithium-ion batteries but couldn’t find a company that they felt had the technology or the resources we could put our name on,” McPeak said. “So instead, they stepped back and said, ‘Okay, what can we do to change the game associated with lithium-ion?’”
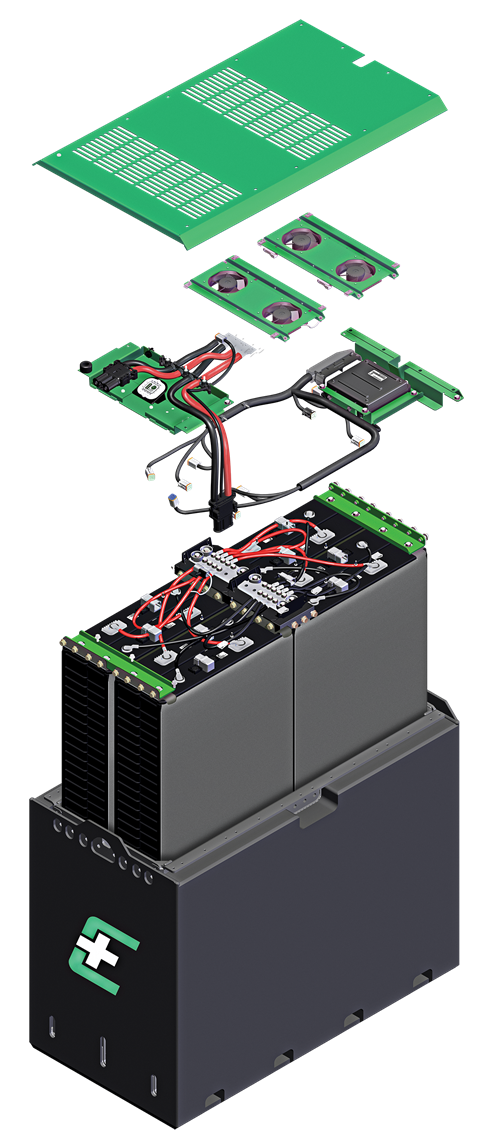
It turned out the answer was to develop a battery from scratch, capitalizing on EControls’ existing resources. “We make engine control modules. We have 200 engineers – 12 with PhDs – who write software and [develop] hardware for a living,” McPeak commented.
The team of engineers chose to approach the project from an electronics standpoint, said McPeak, asking such key questions as “how do we want this battery to behave” and “how do we want to control it – what do we want its ‘brain’ to be able to do?”
“We always come at a problem from an engineering perspective – like, how can we create a product that is engineered in a way that is the most robust, the [highest] quality, etc.”
Management at the cell level
In terms of “form factor,” the team chose a cylindrical design for the cells, which are more adaptable to changing chemistries/technologies, rather than the more common prismatic, or square-shape, configuration. It also chose to use lithium iron phosphate (LFP) as its core.
“We settled on lithium iron phosphate because it’s the safest. It has the highest thermal runaway tolerance,” McPeak said. “Thermal runaway is where the cell begins to self-heat in an uncontrollable manner, which can often lead to gassing, fire and smoke.”
In addition, LFP doesn’t contain precious metals like cobalt and nickel, which have become difficult to obtain, and it has the highest durability and highest depth of discharge, said McPeak. “It’s a little bit more expensive but even that gap is closing, and it’s superior in all these other categories.”
Each battery box consists of up to eight modules that are fully enclosed and self-contained with their own battery management system (BMS). The modules are also replaceable. “You can actually pull a module out and put another module back in, if necessary,” said McPeak.
A single module holds close to 400 cells that have been individually characterized and grouped according to impedance and capacity for optimized performance. Each cell is equipped with sensors to monitor voltage, temperature, current and more. Advanced software within the BMS activates heating/cooling to the cells automatically as needed. It is also designed to continually measure and control cell voltage.
“We shift the energy around inside the battery so that we’re keeping all the modules inside the battery at [peak level],” McPeak said. “So, if this cell is going way down, we will transfer from a cell over here and put it into that cell.” Conversely, excess energy can be shifted to cells with a lower charge, ensuring even energy distribution. “What that does is make this battery run a lot longer and a lot more efficiently than most any other lithium-ion batteries. We call that active balancing.”
Safety is built at the cell level, as well. For example, a passive safety system activates if a cell begins to overheat, taking that cell offline, McPeak noted. “So, out of the 400 cells per module, if one of them gets ‘angry,’ instead of us allowing it to get hot and have an issue, it will just pop its fuse and it is no longer attached to the energy source.”
Another unique feature is each battery goes out with a connected device onboard. “[There is] an app and a web interface where we can see everything about that battery, and so can the customer,” said McPeak. “In fact, we can remotely access the battery and upload software, extract information and troubleshoot the battery from our desk.”
Such connectivity is not just about managing battery health. It’s also about overseeing specific aspects of operation, such as opportunity charging and production capabilities. For example, consider a large warehouse operation running three shifts of forklifts, 24/7, for which the manager needs to calculate how much additional throughput the operation can accommodate.
“As a manager of that team, you would want real-time and historical visibility to see battery state of charge, idle time and charger plug-in behavior. We have reports that show a wide range of data – like idle time that the truck was not running or plugged in, and the battery state of charge throughout the shift,” said McPeak. “These reports take the guesswork out of managing a fleet of lift trucks and empower users to make educated decisions around their operation, which equates to additional throughput capability for the facility without having to add additional equipment.”
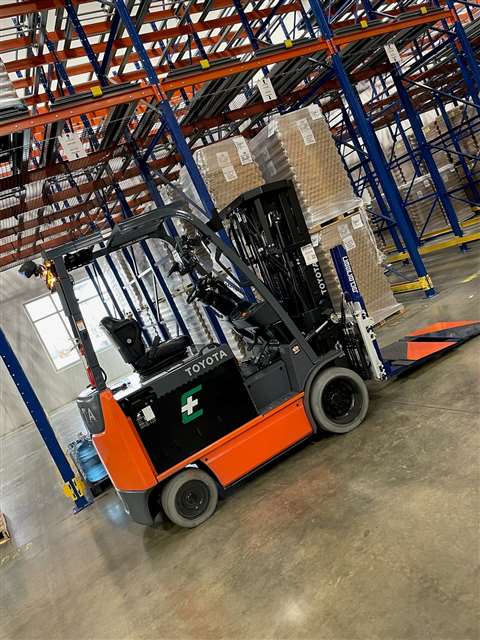
Application targets
Virtually all aspects of battery development and manufacturing now take place in-house at a new facility purpose-built for Ethium’s operations. Combined with the support of its multi-million-dollar parent organization, the division is well-positioned to expand its battery technology’s reach in the material-handling market.
“It was launched into production in 2021 in small doses. And now we’re in serial production,” McPeak said. “We have our customer footprint plan in place and are putting the name out there.”
Though capable of developing customized solutions for OEM customers, Ethium has recognized its greatest potential, at least for the near term, is with drop-in battery box replacements, which are currently available in 24, 36 and 48 V, with an anticipated release of 80 V in early Q2 2023.
“There’s hundreds of thousands of electric forklifts in the market space that are already using lead acid that can be switched over to lithium,” McPeak said. This includes both in-use and new electric vehicles. “Literally, they can pull the lead acid battery out and this slides in its place and plugs in. And that’s it.”
The company does work with select forklift OEMs seeking integrated solutions. “There are projects within those companies in which they’re wanting a battery that is integrated into the vehicle in a [unique] shape or position that takes the place of where an engine would go today,” McPeak said. “We definitely want to be a part of that.”
But while Ethium is “highly engaged with many of the OEMs to provide that integrated solution,” others aren’t yet at a point where they’re ready to make that shift. “Those companies are still finding their way on how to do that,” McPeak acknowledged.
Growth ahead
McPeak is highly optimistic about Ethium’s position and its prospects. “We think we now know how we want to go to market and we’re ready to go and do that,” McPeak said. “This year, we’ll be completely focused on a massive ramp-up.
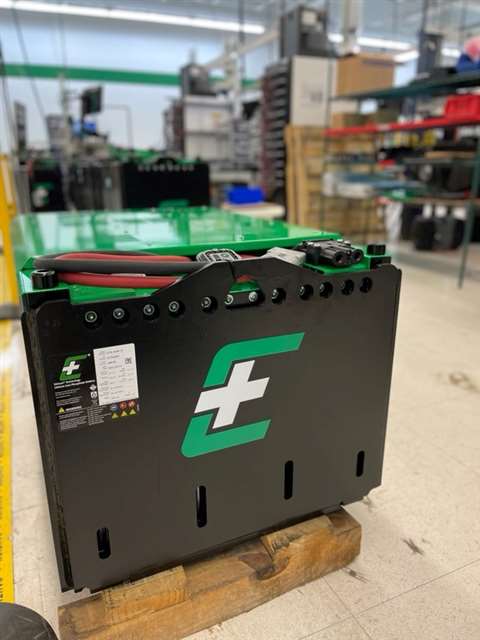
“2021-2022 was investigating all of the things that we didn’t really know about this marketplace,” McPeak said. It was also about identifying who to sell to and sell through, then fostering relationships via on-site visits to ensure the right industry partners were in place.
Those partners include large conglomerate dealers identified as having the necessary infrastructure. Ethium then strove to enable them to “sell and service the product and be really successful in enabling their customers to move from lead acid to lithium because they understand it, they understand the reasons why you would do it, they understand the product.”
Ethium also had to ensure its products would continue to be available in a timely manner. Currently, lead times for standard battery box replacements are around three weeks, with customized box sizes averaging roughly 12 weeks. To maintain this level of turnaround, Ethium installed multiple robotic assembly devices, with another scheduled to be in place by the end of March and two more by the end of 2024.
“That’s the level of investment and the level of ramp-up and growth that is happening,” McPeak said, adding, “We will sell exponentially more product this year than in 2022.”
POWER SOURCING GUIDE
The trusted reference and buyer’s guide for 83 years
The original “desktop search engine,” guiding nearly 10,000 users in more than 90 countries it is the primary reference for specifications and details on all the components that go into engine systems.
Visit Now
STAY CONNECTED



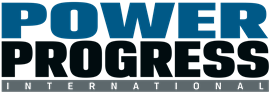
Receive the information you need when you need it through our world-leading magazines, newsletters and daily briefings.
CONNECT WITH THE TEAM
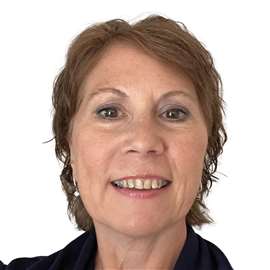
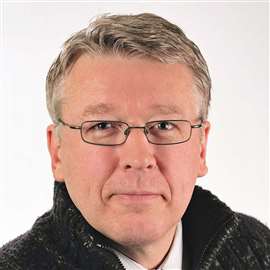
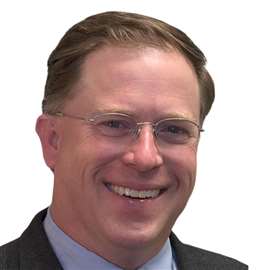
