Hengst’s hydrogen filtration solutions
04 May 2023
Hengst is seeking to address the specific challenges of hydrogen fuel cell filtration by introducing new solutions, which it hopes to start supplying to customers later this year.
Fuel cells, particularly proton exchange membrane (PEM) fuel cells, require outside air entering through the air intake to be very effectively cleaned of particles, the company noted. Such pollutants can cause unwanted deposits in the fuel cell and potentially damage it. In addition, gaseous impurities such as nitrogen oxides (NOx), ammonia and sulfur oxide may interfere with the desired chemical processes in the fuel cell and reduce the effectiveness of the system or even cause damages to the membrane.
A specially developed cathode air filter system from Hengst is designed to protect fuel cell components from both particles and harmful gases.
“The fuel cell is a little more particular in terms of air [quality],” said Wolfgang Hilfenhaus, application engineering manager, Hengst Filtration. “This is why this is not only a particle filter.”
Rather, the system has a multilayer structure, with each layer optimized for a specific task. For example, one layer filters out particles while another layer of activated carbon filters out gases in the intake air that would harm fuel cell function, he explained.
The range of applications covered by Hengst cathode air filters extends from small fuel cells and mobile systems in the on- and off-highway segment to large-scale systems for stationary power generation and ships. The mid-range filters shown at ConExpo can be attached to the fuel cell system at various angles to accommodate the required configuration of inlet and outlet.
The cathode air filter system is also variable in size. By adding more units, it can attend to larger air intake volumes based on the existing tool set for housing and filter element.
“It’s a construction kit and you can adapt it to the application,” Hilfenhaus said. This includes the elements inside the filter. “For example, if the problem is not dust, we may reduce the depth of the pleats to reduce space needed for the particle filter to accommodate more activated carbon for gas absorption.”
Individual elements of the filters are designed to be easily removed and replaced for service.
Deionization of coolant
Fuel cells generate heat during operation, so cooling is required to ensure optimal performance. “To have the fuel cell working perfectly or at its optimum working point, you need to keep the temperature below a certain level,” Hilfenhaus said.
“The coolant shouldn’t be conductive because then you have undesired chemical reactions that you cannot control,” he continued. “You want to have a defined reaction with water, hydrogen and oxygen and nothing else if you want to have [the fuel cell] generating electrical energy that you can use. If you have other reactions in the fuel cell, you’re losing power.”
As such, a deionization filter is required. According to Hengst, its new Blue.iox ion exchanger ensures a rapid lowering of the initial ion concentration within the coolant circuit. It can be integrated in the main flow or in parallel connection with components of the coolant circuit.
“This deionization filter gets all kinds of ions out of that coolant that are brought in by leaching material used in components in the coolant circuit,” Hilfenhaus said. A proprietary mix of standard or customized resins are housed within the filter cartridge. “We have our own development for these resins and create our own mixtures, so we can adapt to the customer’s needs.”
Receptors within the resins capture and trap ions inside the cartridge. Once the cartridge begins to fill up, an optional conductivity sensor, built into the filter housing, can help.
“You want to have a low conductivity in the coolant. When the conductivity goes slightly up, you know it’s time to change that [cartridge]. You can monitor that function,” Hilfenhaus said.
A screw cap allows the filter cartridge to be easily changed using standard tools, while integrated shut-off valves avoid complete drainage of the housing and facilitate deaeration of the system after service.
“What makes us unique with a lot of our products is sustainability. Most of our products are cartridge-based filters,” said Marco Dell’Api, marketing specialist, Hengst Filtration. “Where possible we have a three-quarter turn; the system opens and you just replace the filter element, [which is] 100% combustible.”
This simplicity and ease of service means less downtime, Hilfenhaus said, which can make the filters an attractive option for fuel cell developers seeking to sell the advantages of their products over battery-electric solutions as well as competitors’ fuel cell products.
Proper water management is required to prevent liquid water deposits and ensure continuous effective operation of the fuel cell, Hengst noted. As such, the company also offers a new type of separator module for anode gas recirculation. It combines the function of droplet water separation and gas drainage with a unique configuration of the purge and drain valve.
POWER SOURCING GUIDE
The trusted reference and buyer’s guide for 83 years
The original “desktop search engine,” guiding nearly 10,000 users in more than 90 countries it is the primary reference for specifications and details on all the components that go into engine systems.
Visit Now
STAY CONNECTED



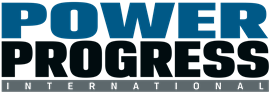
Receive the information you need when you need it through our world-leading magazines, newsletters and daily briefings.
CONNECT WITH THE TEAM
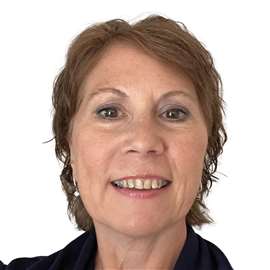
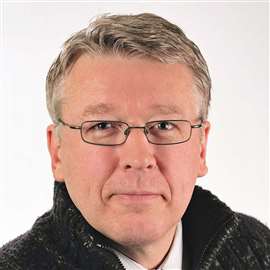
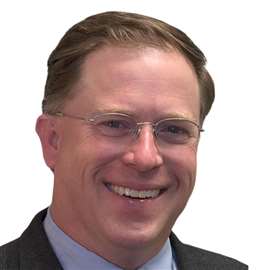
