How Schroeder Industries developed its new filter line
09 November 2021
Schroeder Industries explains why it is moving forward with its new particulate, coalescing fuel filter line.
U.S. Environmental Protection Agency (EPA) Tier 4 and European Union Stage 5 engines were introduced to the off-road equipment market in early 2011. Since 2018, many of the diesel engines manufactured and sold within the European Union and North America under 750 hp are now Tier 4 emissions level or higher.
As the technology of Tier 4 and Euro 5 engines has progressed, so too has their requirement for clean, dry fuel to achieve consistent performance. In response, engine manufacturers have upgraded their fuel filtration systems and tightened their specifications to better meet today’s higher operating standards while still meeting the demands of equipment operators.
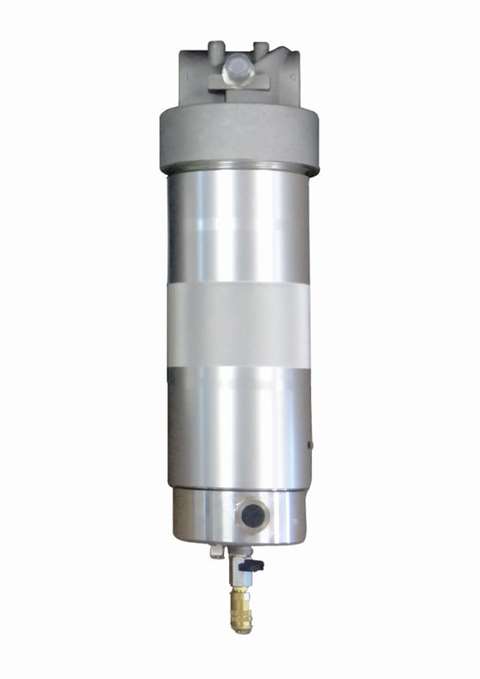
These engine requirements have driven advances in filtration technology, as well. Such enhancements include:
- Multiple stages of filtration prior to and after the low-pressure lift pumps
- Stricter cleanliness requirements approaching the high-pressure fuel system components
- Lower acceptable water levels in the fuel itself.
Tier 4 engines
When Tier 4 engines arrived on the market, many operators were faced with frequent, high maintenance and repair costs for fuel injection system components, such as injectors and pumps. These problems were primarily caused by excessive amounts of water and particulate contamination that had passed through the filtration system. The fuel system components had a much shorter life cycle than was originally designed.
“Today, better filtration design and media technology has allowed for improved particulate filtration and water separation capabilities,” said Rob Sabo, Group Product Manager, Fuel Filtration, Schroeder Industries. “Modern filtration performance exceeds the technology available during EPA Tier 1 through 3, and even when Tier 4 was first introduced.
“This is very similar to the evolution of hydraulic systems over the last several decades, which have also experienced many of the same challenges as they became more compact while operating at much higher pressures. There can be experience and knowledge gained from the entire fluid power industry during this rapid advancement in technology. It can provide insight into where the future of machine architecture, and ultimately fuel system design, is headed in the years to come.”
Deep understanding of OEM objectives
The National Fluid Power Association (NFPA) Roadmap Committee recently surveyed 113 respondents across the fluid power supply chain to rank the importance of eight key customer drivers, which it defined as “the business or technology objectives of fluid power customers.”
Based on that survey, NFPA reported that the following are of highest importance to those surveyed. In order of priority:
- Increased availability and uptime.
- Increased productivity and performance.
- Compliance with safety regulations and machine directives.
- Lower capital and operating costs.
- Easier and more predictable maintenance.
- Greater integration of technologies, including data acquisition, utilization, and ownership.
- Weight reductions and increased power density.
- Autonomous operation.
“We have already begun to see reflections of these objectives applied to fuel systems in recent years,” said Sabo. “Engine manufacturers have been striving to obtain longer service intervals on their maintenance schedules for both oil and fuel filters. Where previously fuel filters were recommended or required to be changed every 250 hours of operation, we are now seeing the industry moving towards 500, 750, and, in some cases, 1000 hours or more of service between scheduled maintenance on equipment.
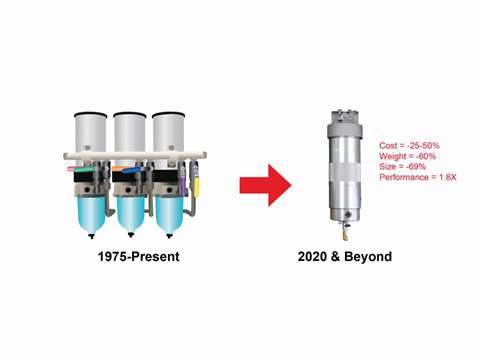
“These longer service intervals require less frequent maintenance, reducing both downtime and labor expenses while using fewer filter elements and other consumables. These cumulative savings can help offset the costs associated with other new expenses like the additional consumable of DEF and the routine DPF cleaning. Managing these expenses can directly improve customer satisfaction with ownership of today’s diesel-powered equipment.”
Diesel engine operators solutions
To achieve the long-term goals set by diesel engine operators, fuel filtration on modern equipment has evolved rapidly. Changes in fuel injection technology and the fuels themselves have been addressed through innovative filtration technologies and modern manufacturing methods.
The basic hardware within today’s fuel filtration system is usually a combination of both particulate and coalescing filters – the latter designed to remove water from the fuel.
However, as the systems have become more sophisticated in performance, so too has the design and integration of other components into these products. Those components can include lift pumps, water-in-fuel sensors, temperature sensors, pressure sensors, vacuum gauges, automatic drains, and contamination sensors for real-time condition monitoring. Several of these options can be incorporated into pressure side and/or vacuum side applications, both on and off-engine.
“It is very important to protect all aspects of the fuel delivery process from bulk storage through to the consumption stage,” said Kelly Coyne, application engineer, Fuel Filtration, Schroeder Industries. “Two years ago, Schroeder Industries introduced the GeoSeal high-flow particulate (GHPF) and coalescing (GHCF) fuel filtration product line. This product was designed specifically to address the three key challenges plaguing diesel fuel filtration today.”
According to Coyne, those challenges are higher pressure common rail systems and increased cleanliness requirements; lower interfacial tension fuels and the variability of biodiesel blends globally, and ultra-low sulfur diesel (ULSD), because sulfur content of 15 ppm is more susceptible to microbial growth in the fuel tanks, creating acidic environments that contribute to storage tank corrosion.
Ultra-low sulfur diesel
“The end result of Schroeder’s new products really revolved around the innovative new proprietary media design incorporated into the GHCF filter housing,” said Sabo. “The design consists of a multistage particulate, coalescing and water separation filter-in-one, with a unique inside-to-outside flow to perform with the highest water removal rates in the industry today. This design also provides a much lower overall pressure differential across the media allowing it to be used in both pressure and vacuum applications. This new design results in increased filtration performance as well as longer filter life and service intervals due to the high dirt holding capacity of the filter elements.”
Schroeder Industries said it worked with a wide range of OEMs as it designed and developed the new fuel system platforms.
“The GHCF is a radical departure from what has been the industry standard for large diesel engines,” said Aaron Keck, product manager, Fuel Filtration, Schroeder Industries. “From the mid-1970s to present-day, the industry standard has been to combine, in parallel, multiple filters to achieve the desired flow rate and service interval needed for the high-flow fuel systems of large diesel engines.
“With these new products, Schroeder Industries is working a novel solution — a better mousetrap — to meet the needs and goals of the customer. Designed, tested, and made in America, these filters support the advancements in filtration technology and the future of fuel systems.”
These improvements align with the key objectives seen in the NFPA survey, said Schroeder Industries.
“This process of integrating radical changes like this has just begun,” said Sabo. “There is an alternative to what OEMs have become accustomed to, and the new alternative is a better fit in many ways.”
POWER SOURCING GUIDE
The trusted reference and buyer’s guide for 83 years
The original “desktop search engine,” guiding nearly 10,000 users in more than 90 countries it is the primary reference for specifications and details on all the components that go into engine systems.
Visit Now
STAY CONNECTED



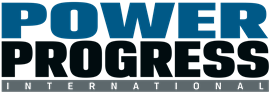
Receive the information you need when you need it through our world-leading magazines, newsletters and daily briefings.
CONNECT WITH THE TEAM
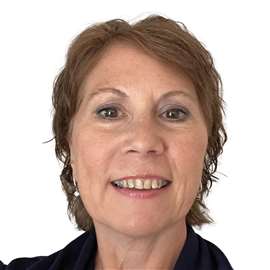
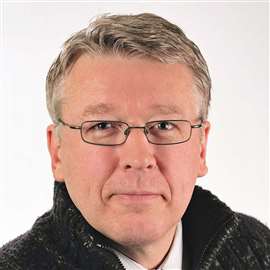
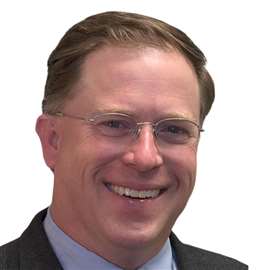
