Intermat Goes Electric
09 February 2018

The Intermat show in Paris in April typically features the introduction of the latest engine-powered machines for the global construction equipment markets. This year’s Intermat however, will have a decidedly more electric feel to it.
In fact, among the winners of the Intermat 2018 Innovation Awards were two fully electric compact excavators: the model EX2 from Volvo CE (pictured) and the Mecalac model e12. Both will be exhibited at Intermat, April 23-28, 2018, at the Paris Nord Villepinte exhibition center.
Volvo EX2
The Volvo EX2 is a fully electric prototype where the engine has been replaced with two lithium-ion batteries for a total of 38 kWh power output which, according to Volvo, is enough to operate the machine for eight hours in intense applications such as digging compacted ground.
Volvo CE said the excavator has 10 times higher efficiency than a conventional machine and its average power consumption of 3.5 kW is comparable to that of a large iron.
Also, Volvo CE said the EX2 does not need any power when in idle mode – which for a compact excavator is calculated to be 40% of the time spent on a job site, an obvious reduction in operating costs. Then there is the currently lower price for electricity compared to diesel, which makes fueling the machine from the electricity grid cheaper than tanking diesel fuel, Volvo said.
In the EX2, the hydraulic architecture is replaced by an electrical system that incorporates electromechanical actuators to optimize the transmission chain. Volvo said eliminating the hydraulic circuits, as well as the engine and its cooling system, reduces maintenance and total cost of ownership, and significantly lowers noise levels. This makes the excavator applicable for use in urban areas, even at night.
Volvo CE said the EX2 delivers the same power and force as its engine-powered counterpart while also delivering faster movements. The machine has been designed to work with four different configurations:
- with two, 600 V, 19 kWh lithium-ion batteries;
- with one 600 V, 19 kWh lithium-ion battery and one diesel range extender;
- with one battery and a fuel cell system;
- or directly plugged into the grid for power and for recharging the batteries.
In addition to these, the excavator recovers energy from movements such as lowering the boom and rotation of the cabin.
The EX2 can also be controlled remotely from a mobile phone or tablet for use in hazardous environments. Since the excavator is a prototype, Volvo specified that it does not fully comply to European standards yet. Overall risk assessment has been done for the electronically-controlled functions according to EN60204 and ISO12100 regulations, Volvo said. Full compliance to EU standards and regulations is part of phase two of the project.
Mecalac e12
Mecalac’s fully electric model e12 wheeled excavator is an 11-ton machine with a 146 kWh battery and two separated electric circuits, each with its own motor, to power the travel function and the front end attachment.
Mecalac explained that the architecture of the excavator – with an articulated chassis frame – is key to machine performance and battery life. In fact, the vehicle is capable of carrying a battery pack of about one cubic meter volume and 1650 kg weight in the rear lower frame, which also stabilizes the machine.
The battery pack is a 650 V lithium-iron-phosphate – a type of lithium-ion battery – with 146 kWh capacity, chosen for its performance but also for safety and environmental reasons. The battery is dry and inert, does not catch fire, does not explode and does not leak poisonous fluids, Mecalac claimed.
The capacity of the battery allows for eight hours of operation and the re-charging time is six to seven hours on a 22 kW plug. Based on one load and unload cycle per day, the battery has a life of 3000 cycles which should last the whole life of the machine, the company said.
The battery supplies the two main electric motors, one moving the driveshaft through a fully electric gearbox. The other motor, completely independent from the other, drives the main hydraulic pump to operate the front end attachments, turret slewing, and chassis articulation. The two power circuits are managed by an electronic control to optimize of the energy efficiency for each function.
The fully automatic electric gearbox provides a strong drawbar force, said Mecalac, including at low speed, and allows energy recovery when the machine decelerates.
Mecalac said the project for the e12 has been developed in partnership with the University of Grenoble. Parker Hannifin provided the electric motors and inverters; and South-Africa-based Powertech supplied the battery.
STAY CONNECTED



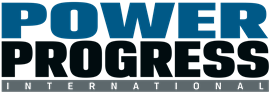
Receive the information you need when you need it through our world-leading magazines, newsletters and daily briefings.
POWER SOURCING GUIDE
The trusted reference and buyer’s guide for 83 years
The original “desktop search engine,” guiding nearly 10,000 users in more than 90 countries it is the primary reference for specifications and details on all the components that go into engine systems.
Visit Now
CONNECT WITH THE TEAM
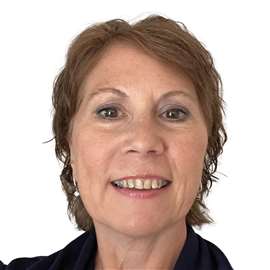
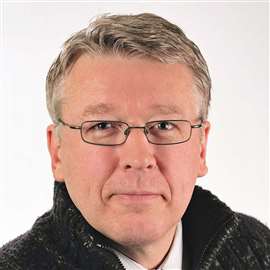
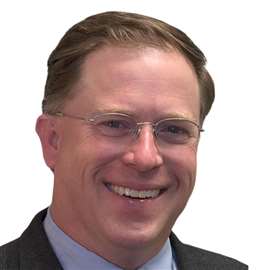
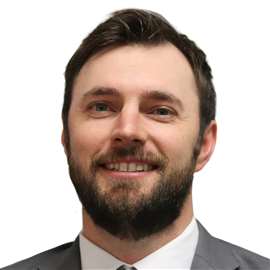
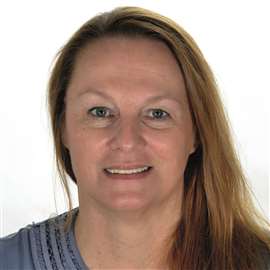
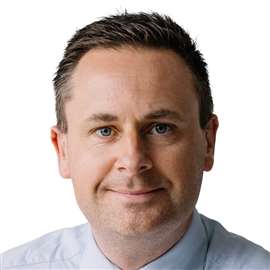