Read this article in French German Italian Portuguese Spanish
Ketchel Axle Systems seeks to drive EV adoption with electrified axles
12 May 2024
The company has introduced commercial vehicle axles for a range of electric truck sizes.
Ketchel Axle Systems said its new eRhino electrified axle will help simplify repower and new production projects in Class 3 through Class 8 trucks. The system integrates an electric motor, inverter and thermal management system into a compact axle design the company said will minimize engineering changes for equipment manufacturers and ensure optimal performance.
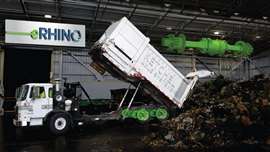
Founder and CEO Brad Ketchel’s engineering career has spanned the automotive industry, including electric vehicle (EV) drivetrain development at Magna Powertrain. He saw a gap in the commercial vehicle space for a new axle.
“The commercial market is filled with multiple fleet owners and multiple vehicle manufacturers, many of which are non-traditional OEMs,” said Ketchel. “The pressure to electrify these fleets is an increasing challenge. The current product offerings are expensive and inefficient and are not being addressed in the context of an overarching system solution. This is increasing vehicle costs and reducing the sales of commercial EVs. The eRhino is the system to break through these initial cost and performance barriers to recognize increased productivity and profitability.”
And that, he said, will help accelerate the acceptance of commercial vehicle electrification.
Coaxial Gears
The eRhino axle uses a coaxial gearbox and is designed around a modular concept that permits it to be used in a wide range of commercial vehicles with minimal modification, which Brad Ketchel said will help accelerate component verification testing.
Continuous power is 220 kW, peak power is rated 350 kW and the axle produces 12,700 Nm of peak torque – all from a system the company said has an efficiency better than 94%. In a Class 3 application, the complete axle weighs 244 kg (538 lb.). Installed on a conventional Class 5 truck, the company said the total weight savings achieved by the eRhino axle can be more than 500 kg (1,102 lb.) when the entire system – including the driveshaft – is considered.
“If we look at the efficiency of the unit, 94% can mean many things for the application,” said Ketchel. “That efficiency will allow us to reduce the number of batteries, which lets us consolidate battery packs to a certain location on the vehicle, which can mean weight savings. We can get rid of any cantilever structures that hang batteries off the frame and eliminate much of the wire harness and high-voltage connectors. Also, when you have batteries situated all over the vehicle, you get a much larger variation in temperature on the batteries — which means more inefficiency.”
The company said the heart of the eRhino sits between the axle tubes and is where the motors, electronics and thermal systems reside inside an aluminum enclosure. The axle arms can be switched out to form a drop-in solution for any vehicle up to Class 8, said Ketchel. The center structure has a 23,000-lb. gross axle weight rate. The company said the 12,700 Nm of torque created by the system is enough to meet gradeability requirements in a single-axle Class 6 application, while anything larger could get multiple eRhino axles.
“This is a highly engineered product that can be used across a whole gamut of vehicles, and there are several ways where we can see this axle going to market,” said Ketchel. “If you were to electrify a Ford E-450, using this system will allow you to reduce upfit labor by hundreds of hours because you can essentially put the system on a sled and bring it right up underneath the frame. We can basically distribute this as a kit. These fleets already have service centers, so they could be doing the retrofits in-house with some guidance.”
Repowering Fleets
Ketchel said the company is currently road testing the axle ahead of start of production in 2025. The axles will be assembled in Huntington Beach, Calif., in the company’s headquarters facility that has a capacity of 3,000 axles annually.
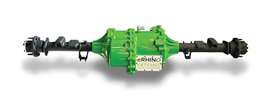
Ketchel said he’s been in conversation with several fleets that are looking for a solution. “Here in California, one fleet has thousands of garbage trucks, and there’s no way they are going to replace their entire fleet with new electric vehicles. They have to repower. So, we’re starting with the axle, and eventually the repowering of vehicles will become much more palatable.
“There are certain suppliers out there that we’ve worked with that have developed a modular software system – it’s almost like Windows, you just plug and play hardware – and then you can quickly get the axle and the rest of the truck to work together. I believe that’s where the future of this is going.”
Ketchel Axle Systems already has a second model in the works. The eBadger axle is designed for Class 1 trucks, such as the Toyota Tacoma. The company is also investigating opportunities for the eRhino axle in off-highway applications, such as utility vehicles used in underground mining.
“We’ve got the known quantities in airport shuttles, box trucks and last-mile delivery vehicles. Other axle suppliers are focused on the high-volume applications, and we’re happy to scoop up the crumbs, because we think 1,000 a year is massive volume. And it’s in the small- to medium-size fleets and OEMs where electrification has to happen, as well. That’s really what we’re excited about.”
POWER SOURCING GUIDE
The trusted reference and buyer’s guide for 83 years
The original “desktop search engine,” guiding nearly 10,000 users in more than 90 countries it is the primary reference for specifications and details on all the components that go into engine systems.
Visit Now
STAY CONNECTED



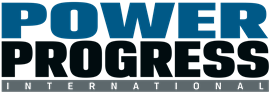
Receive the information you need when you need it through our world-leading magazines, newsletters and daily briefings.
CONNECT WITH THE TEAM
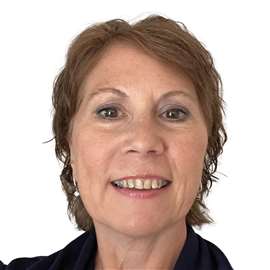
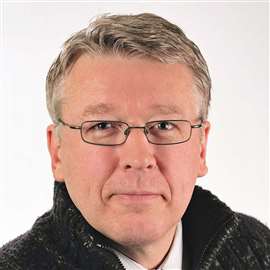
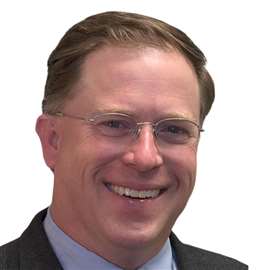
