Moog advances autonomous robotic solutions
02 May 2023
Robotics in construction was one of the most prominent themes at ConExpo-Con/Agg 2023 in Las Vegas in March. It’s not hard to see the benefits the technology can bring to the jobsite – robotic machines filling the labor void, increased safety and greater productivity, too – but it can be difficult to picture how it’s realistically going to work in construction’s varied and unpredictable settings.
Many of the major equipment manufacturers – Bobcat, Komatsu, Case, Develon, to name just a few – are promoting concept machines that suggest the time for robots on construction sites is coming sooner than we think. Interestingly, the technology behind more than one of those concepts can be traced back to the same place: Moog Construction, a worldwide developer of electric motion control solutions and systems for industries ranging from aerospace and defense to construction.
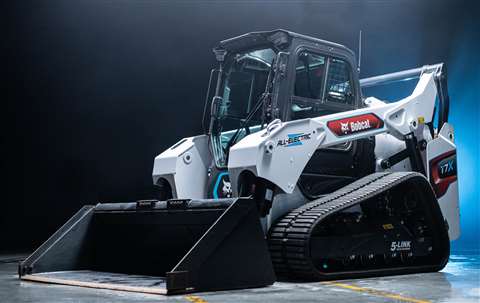
Moog Construction has been involved in some significant and innovative equipment launches over the past year or two, including the Bobcat T7X all-electric compact track loader, debuted at CES in 2022, and the Komatsu all-electric wheel loader introduced at Bauma 2022.
The company has continued its involvement with Bobcat, which just unveiled its all-electric S7X skid steer and autonomous RogueX concept at ConExpo-Con/Agg. With no cab or operator station of any kind, the RogueX explores the idea of operating where humans cannot safely go.
To find out more about Moog’s role in the advancement of technology in construction, we spoke to Aditya Sharma, manager of business development and strategic opportunities at Moog Construction.
Q: What is the story behind Moog?
A: The company was founded in July of 1951 by Bill Moog, Art Moog and Lou Geyer. They pulled together $3,000 and opened a company called Moog Valve to make proportional valves used in many applications.
Today, we design and manufacture integrated precision motion control products and systems that you see in military and commercial aircraft. Innovation is the main pillar of this company.
A couple of years ago, we launched Moog Construction, a dedicated business unit with the goal of becoming a leading provider of electrified digitally connected and automated solutions for the construction industry, enabling the transition to a more productive, safe and sustainable future.
We’re targeting a system-level approach, where we work with major equipment manufacturers, such as Bobcat, Komatsu and Case Construction. We’re looking forward to more collaborations.
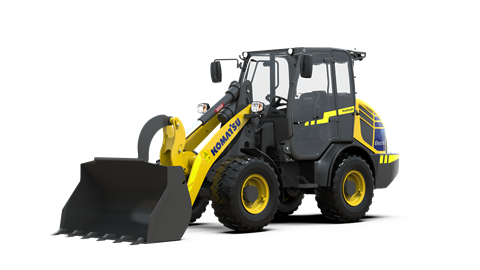
Q: How do you manage working with competing companies?
A: We respect that they are competitors, but each has a different approach and different products they’re working on. But it is all based around technology we have developed and advanced over the last several decades.
We are a technology provider, so mechatronics, software and digital insights are our main competencies. Our system, which is the electrified solution, contains electromechanical actuation and power electronics, motion control software, digital tools, energy management system… and the whole system is automation enabled. This is all inside the machine and we supply it as a system.
Q: Tell us about Moog’s own autonomous machine that was shown at ConExpo-Con/Agg.
A: Moog Construction demonstrated an autonomous compact track loader designed to help construction companies boost productivity on work sites. The collaborative autonomous robot (based on a Bobcat loader) carried out commands to navigate and perform tasks in an outdoor arena.
A vehicle like the one on display at ConExpo-Con/Agg helped deliver solar panels at a U.S. utility-scale solar energy site. These large sites are typically built in remote areas, and installation crews require the delivery of thousands of pallets.
The delivery process is a repetitive, critical task that can cause delays and non-productive time on site. Autonomously delivering material provides a more consistent process and ensures crews have what they need, where and when they need it, to keep projects on track.
Moog’s Collaborative Construction Robots are unique in the market because they leverage Moog’s expertise with motion control and safety-critical systems to work with people in challenging construction environments. This approach expands the potential uses for robotics in construction and helps construction companies reduce project delays and budget overruns in the field.
Our experience in the aircraft and military sectors, reliability and focus on safety are in our DNA and we want to bring that to construction, because it can be a dangerous industry.
We are also focusing on the labor challenges construction is struggling with. Our technology can enhance and augment the existing labor force so workers can do their jobs on time and more productively. We aren’t taking away any jobs by introducing these solutions; we are making labor more enabled.
Q: How does Moog’s autonomous construction robotic solutions work?
A: We take the CAD design of the overall operations and collaboratively we work with the end user on defining what they need to do. With the help of our software, our machines are fully automated, but they don’t make their own decisions. They don’t carry that AI function at this point. The idea with this autonomous solution is to make people safer and more comfortable.
Q: How would a typical purchase of the technology look? Would a contractor buy a fleet of Moog’s machines and have them programmed for a specific job? Can existing machines in fleet be retrofitted?
A: Our autonomous solutions are not off the shelf – we customize them for each end user. Typically, we work in a collaborative approach with the customer to identify their current challenges and overall operations. Once we discover the metrics of success for that customer, we propose the solution for their application that includes overall costs.
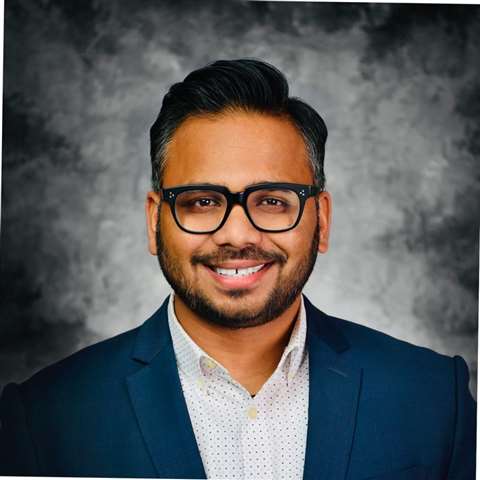
We believe robots have a unique place in the construction industry and as we progress, we will notice more of them doing different jobs. At this moment, repetitive jobs are our primary focus with the goal of enhancing the existing workforce. We want to introduce these solutions to help construction workers be more productive and cost effective by adding more reliability.
Q: Are there specific construction market segments you’re currently targeting?
A: In construction, each application requires a little bit of tweaking to the specific needs of the jobsite, and we see the implementation of this technology in many areas. At this point, we are focusing on dull, dirty and dangerous jobs… there could be infinite applications there.
POWER SOURCING GUIDE
The trusted reference and buyer’s guide for 83 years
The original “desktop search engine,” guiding nearly 10,000 users in more than 90 countries it is the primary reference for specifications and details on all the components that go into engine systems.
Visit Now
STAY CONNECTED



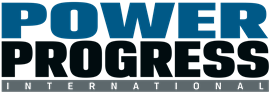
Receive the information you need when you need it through our world-leading magazines, newsletters and daily briefings.
CONNECT WITH THE TEAM
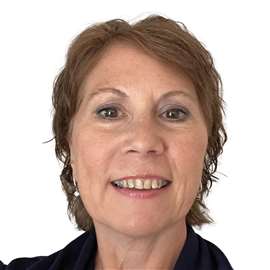
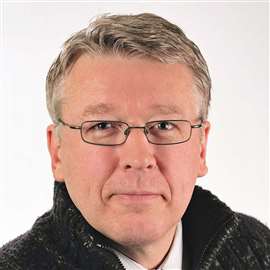
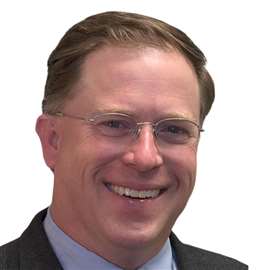
