New Configuration Software For Valve Drivers
02 June 2020
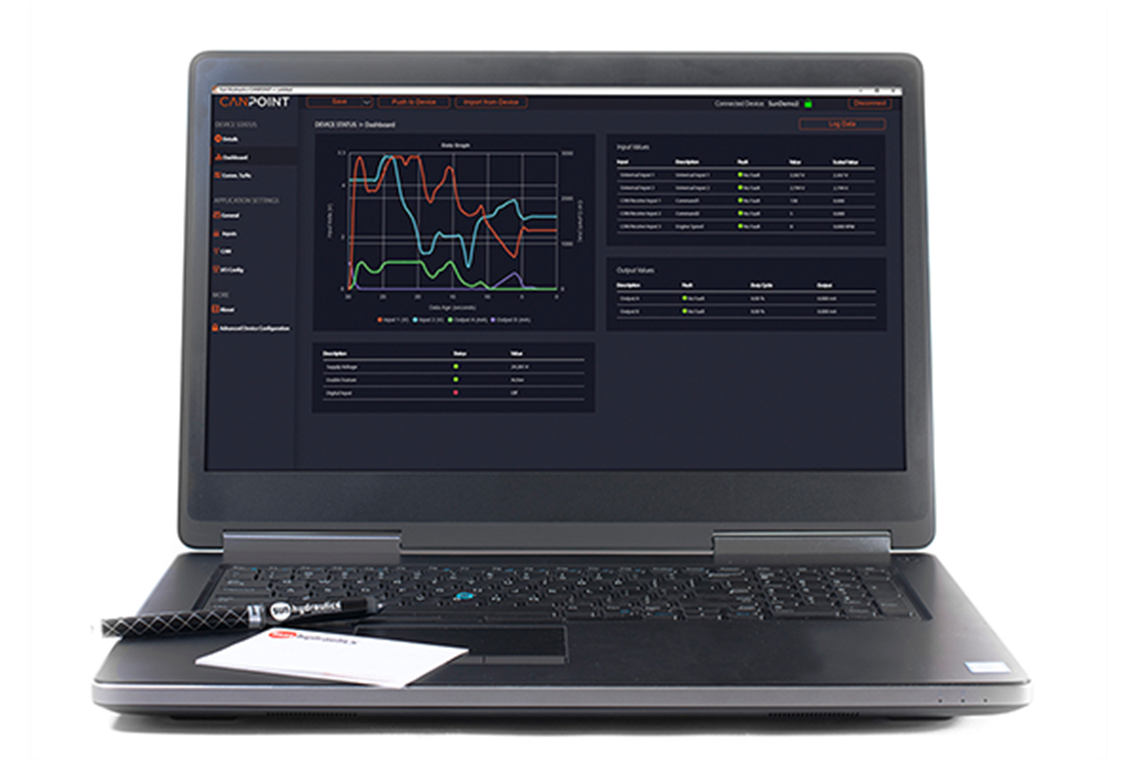
Sun Hydraulics, Sarasota, Fla., has released new software designed to expand the capabilities of the company’s line of XMD mobile valve drivers. The new CANpoint XMD configuration software, available as a free download from the Sun Hydraulics website (www.sunhydraulics.com) allows the compact XMD drivers to be configured quickly and easily over CAN bus using a computer and an CAN to USB hardware interface cable.
With the XMD dual-output drivers configured with CANpoint, users can implement open-loop, closed-loop (PID) and hydraulic fan drive control using pre-programmed modes. CANpoint provides a software interface that allows for simple point-and-click output shaping and requires no programming to go from connecting to configuring to completing the application setup. All the user needs is Sun’s XMD CAN-to-USB hardware interface cable to connect the driver to a computer.
In addition, CANpoint includes features critical for application setup including:
• Live graphing with data logging.
• Live CAN data traffic view.
• Multiple input types.
• Scalable input values.
• Multi-point calibration.
• Simplified output settings.
• Password-protected systems settings.
User Dashboard
In the CANpoint dashboard, users can view inputs and outputs in real time and store results for post-data analysis. At a glance, Sun said users can see everything needed to evaluate the application and optimize the results. This includes real-time plotting, data logging for post-analysis, real-time view of inputs and outputs, data in raw and scaled values and diagnostic indicators with descriptions.

The XMD driver accommodates multiple input types, such as voltage, current, pulse width modulation (PWM), frequency, resistive and digital. CANpoint provides a simple output menu for most common solutions and end-use cases with PWM frequency, output mode and ramp settings. Advanced options offer more control for experienced users, with output current regulation PID settings and robust fault detection that includes user-defined fault status modes.

Configuration Modes
Open-loop mode offers a range of I/O configuration modes, the company said, with input and output settings customizable. Input variables are user-defined, with custom output shaping and there is a thermostat on/off feature for high- and low-pressure and flow-control applications.
The closed-loop proportional–integral–derivative (PID) mode provides additional functionality using the two PID loops. PID loops enable the control of output A and output B independently. Each loop provides command and feedback and is applicable to position, pressure and flow control.
CANpoint can also control unidirectional or bidirectional hydraulic fan drives using up to five configurable inputs not limited to temperature. Inputs available include two universal and three CAN values. Features in hydraulic fan drive control mode include start-up delay, ignition switch, minimum engine speed, reverse toggle and auto reverse, minimum fan speed and minimum pressure protection.
POWER SOURCING GUIDE
The trusted reference and buyer’s guide for 83 years
The original “desktop search engine,” guiding nearly 10,000 users in more than 90 countries it is the primary reference for specifications and details on all the components that go into engine systems.
Visit Now
STAY CONNECTED



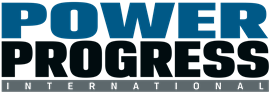
Receive the information you need when you need it through our world-leading magazines, newsletters and daily briefings.
CONNECT WITH THE TEAM
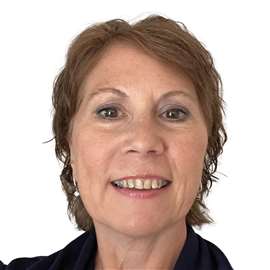
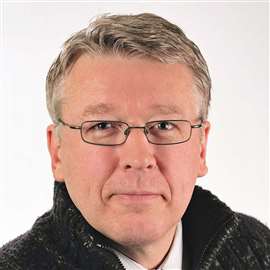
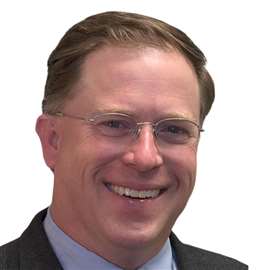
