New Technology For Faster Battery Charging?
22 February 2018
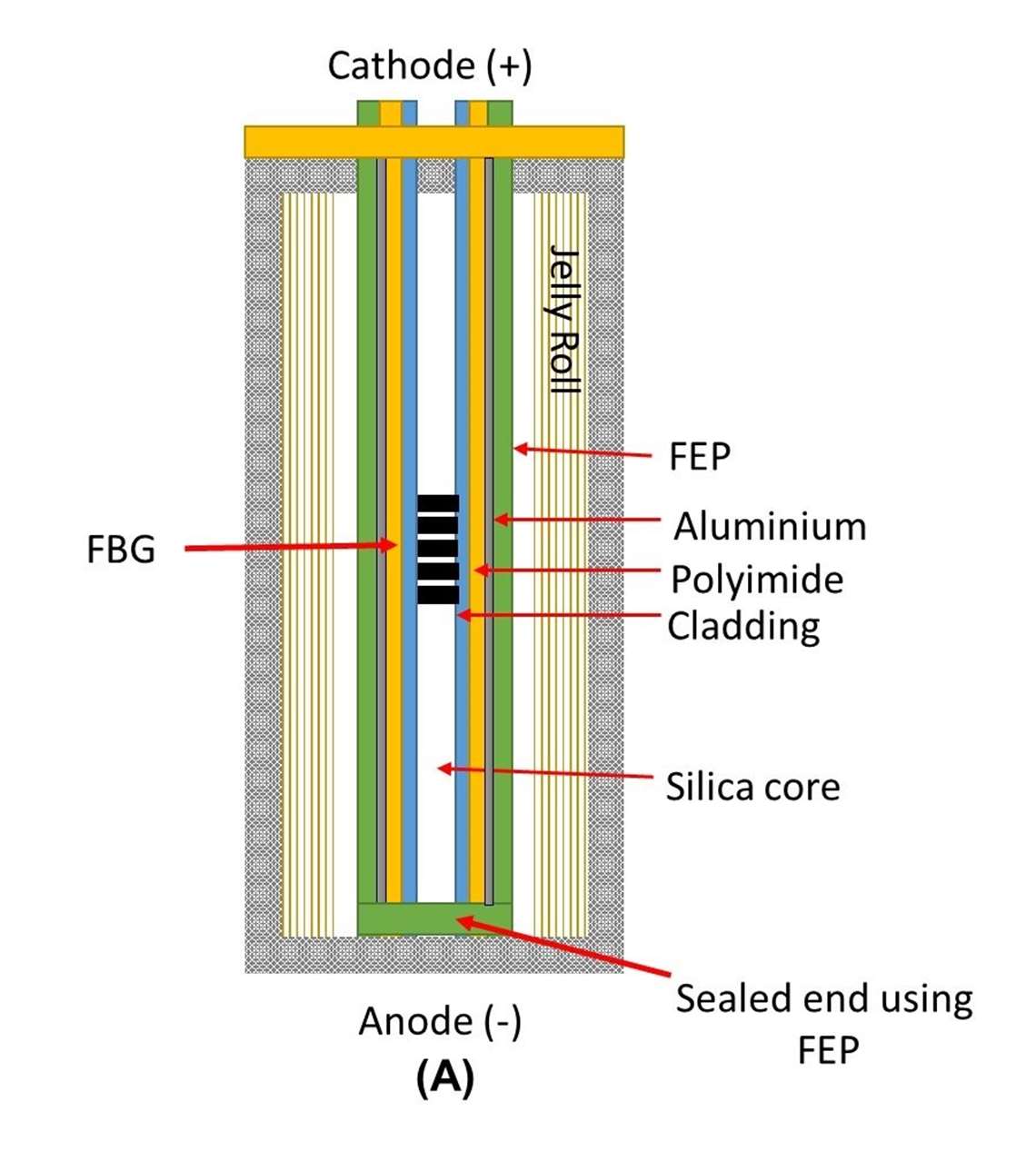
BY IAN CAMERON
As the commercial on-highway and off-highway sectors continue to take a closer and closer look at electric drivetrains the question of battery charging efficiency is frequently raised.
Indeed, one high profile UK transport policy and research organization, The RAC Foundation, has even suggested that potential purchasers of vehicles tempted by the benefits of quickly-improving battery capacity might still hesitate if the public charge point network doesn’t keep pace with changing technology.
However, researchers at WMG, (formerly Warwick Manufacturing Group) an academic department of the University of Warwick, England and employing more than 600 staff including industrial secondees, have developed a new direct, precise test of Lithium-ion batteries’ internal temperatures and their electrodes potentials and found that the batteries can be safely charged up to five times faster than the current recommended charging limits.
According to researchers, the new technology works in-situ during a battery’s normal operation without impeding its performance and has been tested on standard commercially available batteries. Such new technology will enable advances in battery materials science, flexible battery charging rates, thermal and electrical engineering of new battery materials/technology and it has the potential to help the design of energy storage systems for high performance applications, WMG claimed.
It added that if a battery becomes overheated it risks severe damage particularly to its electrolyte and can even lead to dangerous situations where the electrolyte breaks down to form gases than are both flammable and cause significant pressure build up.
Overcharging of the anode can lead to so much Lithium electroplating that it forms metallic dendrites and eventually pierce the separator causing an internal short circuit with the cathode and subsequent catastrophic failure, WMG said.
To avoid this, manufacturers stipulate a maximum charging rate or intensity for batteries based on what they think are the crucial temperature and potential levels to avoid.
However, until now internal temperature testing (and gaining data on each electrode’s potential) in a battery has proved either impossible or impractical without significantly affecting the batteries performance, according to the department.
WMG added that manufacturers have had to rely on a limited, external instrumentation. This, it added, is unable to provide precise readings which has led manufacturers to assign very conservative limits on maximum charging speed or intensity to ensure the battery isn’t damaged or worst case suffers catastrophic failure.
Researchers in WMG at the University of Warwick have been developing a new range of methods that allows direct, precise internal temperature and “per-electrode” status monitoring of Lithium-ion batteries of various formats and destination. These methods can be used during a battery’s normal operation without impeding its performance and it has been tested on commercially available automotive-class batteries, said WMG
It added that the data acquired by such methods is much more precise than external sensing and the WMG have been able to ascertain that commercially available lithium batteries available today could be charged at least five times faster than the current recommended maximum rates of charge.
Dr. Tazdin Amietszajew, the WMG researcher who led the project, said the work could bring huge benefits to areas which would gain obvious benefits from being able to push the performance limits, but it also creates opportunities for consumers and energy storage providers.
“Faster charging as always comes at the expense of overall battery life, but many consumers would welcome the ability to charge a vehicle battery quickly when short journey times are required and then to switch to standard charge periods at other times. Having that flexibility in charging strategies might even/further down the line help consumers benefit from financial incentives from power companies seeking to balance grid supplies using vehicles connected to the grid,” Amietszajew said.
“This technology is ready to apply now to commercial batteries, but we would need to ensure that battery management systems on vehicles, and that the infrastructure being put in for electric vehicles, are able to accommodate variable charging rates that would include these new more precisely tuned profiles/limits”
The technology the WMG researchers have developed for this new direct in-situ battery sensing employs miniature reference electrodes and Fibre Bragg Gratings (FBG) threaded through bespoke strain protection layer. An outer skin of fluorinated ethylene propylene (FEP) was applied over the fibre, adding chemical protection from the corrosive electrolyte.
The result is a device that can have direct contact with all the key parts of the battery and withstand electrical, chemical and mechanical stress inflicted during the batteries operation while still enabling precise temperature and potential readings.
POWER SOURCING GUIDE
The trusted reference and buyer’s guide for 83 years
The original “desktop search engine,” guiding nearly 10,000 users in more than 90 countries it is the primary reference for specifications and details on all the components that go into engine systems.
Visit Now
STAY CONNECTED



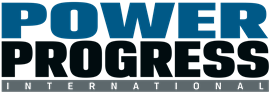
Receive the information you need when you need it through our world-leading magazines, newsletters and daily briefings.
CONNECT WITH THE TEAM
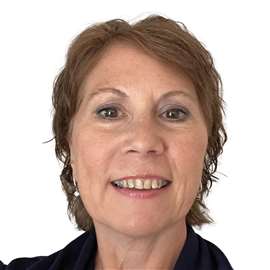
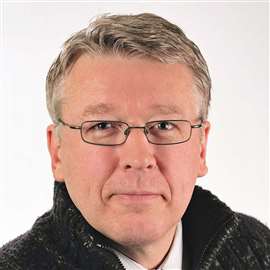
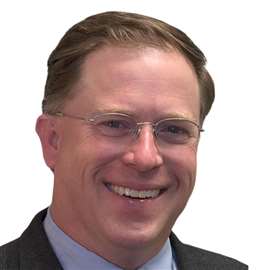
