No-Cost Peak Shaving?
20 April 2020
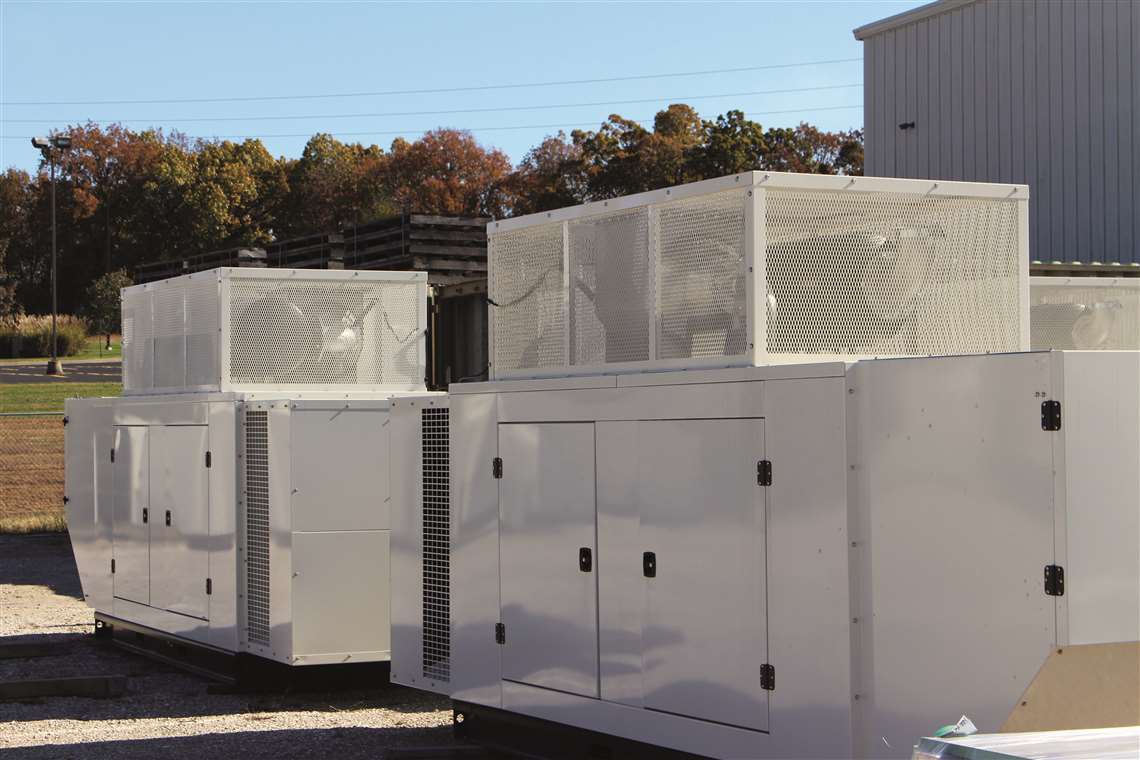
New gas gen-set introduced primarily for peak shaving applications with users only paying for the power provided
By Mike Osenga
Representing a new wrinkle in the onsite distributed power generation markets, specifically peak shaving applications, Leading Edge Power Solutions (LEPS), Laguna Beach, Calif., is introducing a new natural gas-fueled generator set system, the LE 240.
The wrinkle? There is no upfront capital investment required by the user for the LE 240 generator set, including installation and maintenance.
While the concept is not completely unique to Leading Edge, the business model is simple. Leading Edge and the user sign a contract, the pricing of the electricity to be supplied is locked in, and the installed gen-set(s) delivers electrical power to the end user at a lower price point than the utility.
It is not a system or a concept that works everywhere and for every application said David Walters, executive chairman and founder of Leading Edge. “Right now, we’re looking at states with higher electrical utility costs and when you evaluate those markets, a number of states jump out as possibilities.” He listed California, Massachusetts, Connecticut, New Jersey, New York, Rhode Island and Ohio as states where the LEPS concept would be competitive.
“From there you’re looking at specific types of applications,” Walters said. “You start with the amount of demand charges a user pays where we would be able to come in and provide kilowatt hours at a lower price for certain periods, such as the higher time-of-use hours during the day.”
Walters added that for an operation that has around 4000 or more demand charge hours a year, the Leading Edge solution starts to make economic sense. As a result, the initial intertest in the LE 240 is coming from applications such as plastics manufacturers, machine shops, foundries and other metalworking operations.
“Any application that has a lot of equipment that is being turned on and off, creating these up-and-down spikes, is what we’re looking at,” he said. He contrasted those type of applications to uses like data centers that run at about the same load levels 24 hours a day. “There isn’t a lot of opportunity to peak shave with data centers and other steady load operations,” he said.
The initial applications of the Leading Edge system are expected to be installed in the first half of this year, depending on permitting, at an injection molding company and a metal recycling operation.
Built in Springfield
The LE 240 is a 120 to 240 kW natural gas generator set packaged by Springfield Remanufacturing Corp. (SRC), Springfield, Mo. The engine can load follow up to 240 kW. It is the first of what is expected to be a range of similar gen-sets, with a 400 kW package likely to be the second model introduced and a 600 kW unit after that.

In operation, the system can operate as a single gen-set or more typically in multiple unit configurations, depending on the application requirements.
The LE240 is powered by a 12.5 L, six-cylinder Weichai model WP13GTA turbocharged and air-to-air aftercooled natural gas engine. The WP13GTA drives a Stamford HCI434D alternator. The system controller is a Deep Sea Electronics model DSE8610. The engine and natural gas fuel system is controlled by an EControls system and an EControls 4G engine control module.
The set is packaged in a heavy-duty steel, fully welded base skid with cross members, fluid containment, forklift pockets, battery tray, sound attenuation and thermal protection. The engine is cooled by a skid-mounted engine-driven radiator with a pusher fan. The total package with custom enclosure has been UL certified.
Walters said the system has tested out to pass the most stringent air quality regulations and has been designed into an environmentally controlled enclosure for local site permitting and is also designed to pass utility interconnection requirements. Multiple units are connected and controlled via ASCO switchgear
As emissions permitting is always a major consideration (along with noise), the set uses a proprietary GESI-built SCAQMD compliant rare earth element catalytic converter, with pre- and post O2 sensors and silencer.
Walters said the highest sound pressure level tested for the 240 kW set was 72.2 dB(A) at 7.0 m.
The NOC
In operation, the gen-set is connected to a network operation center (NOC) that collects and stores all the operating data and runs financial audits to detail how the LE 240 has performed financially. The NOC also watches real time engine operation with an eye on preventative maintenance. In addition, the NOC is used to download updates like tariff rate changes.
Walters said where the “magic” of the system comes into play is in the LEPS (PLC) control system. He said the supervisory system is designed to meet the needs of a range of LEPS architecture. The system monitors and optimizes operation proving high power quality and reliability, maximizing renewable energy utilization, minimizing fossil fuel consumption and lowering a user’s overall energy spend.
The system uses three proprietary tools, Walters said. First are financial justification and dispatch algorithms developed using historical hourly load data, hourly utility time of use tariff rate changes and LEPS performance characteristics.
Second is the PLC-based a real time dispatch controller and data collector that dispatches the generator set using predetermined set points from the algorithms, combined with the user’s real time metered load data, to maximize energy and demand charge savings. It also collects generator performance data and customer usage data to upload to the NOC for auditing and preventative maintenance.
From there, the NOC-based process uses the collected real time data to monitor the system’s performance and operation and maintenance analysis. It also audits the financial performance from the actual metered hours of gen-set operation to confirm the utility savings and predicted financial returns.
This data is also used to program the LEPS system to work with the demand curves for maximum efficiency.
Other Possibilities
Finally, since the development of the LEPS concept, other application possibilities have emerged. Walters said that in California especially, given “sparking” fire concerns that have threatened continuous utility power supply, Leading Edge is now getting inquiries for standby use of their sets, in addition to the peak shaving possibilities.
Beyond that, Walters said LEPS could also be a component of a microgrid solution. “Our software, the same software that throttles our engine up and down, is software that could run an entire microgrid, which could include solar and battery and potentially other types of power like fuel cells.”
POWER SOURCING GUIDE
The trusted reference and buyer’s guide for 83 years
The original “desktop search engine,” guiding nearly 10,000 users in more than 90 countries it is the primary reference for specifications and details on all the components that go into engine systems.
Visit Now
STAY CONNECTED



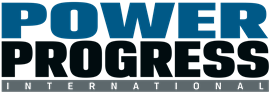
Receive the information you need when you need it through our world-leading magazines, newsletters and daily briefings.
CONNECT WITH THE TEAM
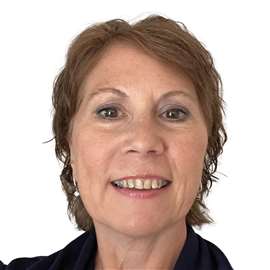
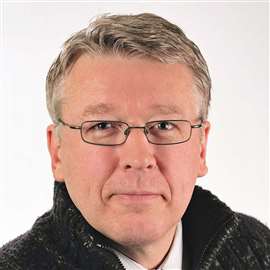
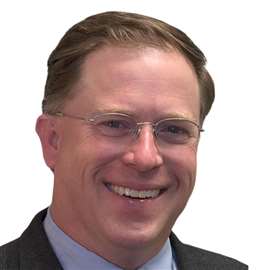
