Parflex’s Case For Preformed Hydraulic Hose
14 March 2019

Designers can face challenges designing hydraulic hoses into the supply and steering lines of many types of mobile equipment. Decisions must be made whether to use metal or plastic tubes, hose and tube combination assemblies, conventional hose connectors or pre-formed thermoplastic connections.
Editor’s Note: This article is based on a white paper by Cedrick Barber, applications engineer, Parker Hannifin Corp., Parflex Division, Ravenna, Ohio
With cost concerns always at the forefront, designers are tasked with a technical challenge coupled with a cost reduction challenge.
For more than a decade, Parflex has offered solutions with pre-formed thermoplastic hose assemblies. Each design is tailored to the application’s specific needs, said Cedrick Barber, applications engineer, Parker Hannifin Corp., Parflex Division. “This technology for hydraulic systems and industrial applications has proven itself in a variety of different low and high-pressure applications such as fuel transfer, hydraulic fluid, and compressed-air lines.”
With demands continuing to push the limits, Barber said Parflex has met the challenge with pre-formed assemblies operating up to 5000 psi (345 bar) and with a new ToughJacket abrasion resistant cover that he said offers 650x the abrasion resistance of standard rubber hose, adding these enhancements open a new range of applications while increasing product life.
Applications range from low-pressure air and fluid transfer to high-pressure hydraulics. The pressure reinforcement is made of either synthetic fibers, steel wire, or a layer of each, which enables assemblies to handle up to 5000 psi (345 bar) working pressure with a min 4x burst pressure.
Temperature deformation of the product does not affect the assembly’s chemical compatibility, technical performance, or functionality. In addition, Parflex hose covers are insensitive to UV or ozone exposure and thus, resistant to environmental stress, Barber said.
While conventional assemblies can be less expensive in initial material and engineering cost, Barber said Parflex preformed assemblies add cost savings through a combination of reduced installation time/labor cost, alignment errors, maintenance repairs, and increased throughput yields. Cost can also be recovered in shipping and receiving costs, he said.
“Because the initial purchase of a pre-formed thermoplastic hose assembly is more expensive than a standard hose or tube, designers don’t realize they can actually save money on the overall build with a custom-built hose. It isn’t until they compare the costs from start to finish, considering all the inventory components, labor costs for actual assembly, labor costs for any rework, inventory, shipping and receiving and freight, that they see the true cost. Once they do the math, it’s typical to realize thousands of dollars in cost savings,” Barber said.
Another advantage, he said, of Parflex pre-formed thermoplastic hose assemblies is the savings in installation time. Since the pre-formed assemblies are shaped to fit, that brings an ease of install, even in difficult to reach areas. And thanks to the flexibility, it can compensate for manufacturing tolerances between different components during installation.
Pre-formed assemblies can be combined with push-to-connect fittings, which can also decrease install and labor cost per unit. Barber said these rapid assembly connections can typically reduce total connection requirements by 30%, decreasing total weight and part numbers of a single unit. This is another savings factor, where the cost savings increase proportionally to the number of units produced.
POWER SOURCING GUIDE
The trusted reference and buyer’s guide for 83 years
The original “desktop search engine,” guiding nearly 10,000 users in more than 90 countries it is the primary reference for specifications and details on all the components that go into engine systems.
Visit Now
STAY CONNECTED



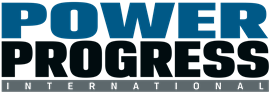
Receive the information you need when you need it through our world-leading magazines, newsletters and daily briefings.
CONNECT WITH THE TEAM
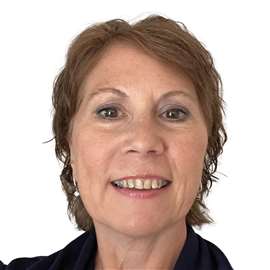
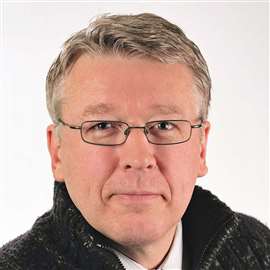
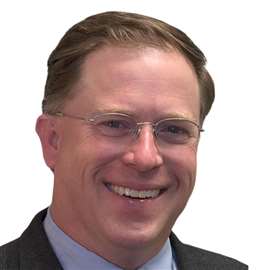
