Power Plants of the World
08 March 2022
Power Plants of the World
Each year, Diesel & Gas Turbine Worldwide asks prime-mover original equipment manufacturers to submit one specific power generation project they feel merits special attention because of advances in one or more of the following areas: efficiency increase, environmental aesthetics, operation characteristics, emissions improvements or construction principles. This originally appeared in the Spring issue of the magazine.
Balancing hydropower in Brazil
Porto de Sergipe plant helped keep lights on
Centrais Elétricas de Sergipe S.A. (CELSE), a Brazilian power producer, owns Porto de Sergipe I, Latin America’s largest combined-cycle, gas-fired power plant in operation, powered by three GE Gas Power’s 7HA.02 turbines. Occupying over 200 000 sq. m near the coastline in the state of Sergipe, the 1544 MW facility can meet on average up to 15% of the equivalent electricity needed to power the demand of Brazil’s Northeast. In 2021, it helped enable the grid to respond to changes in demand and adapt rapidly to weather changes due to a severe drought and lower-than-expected rainfall in a nation which depends heavily on hydroelectric power.
Hydropower is the largest source of energy in Brazil, providing approximately 63 percent in the country’s energy mix—according to grid operator ONS—but in 2021 the rainy season in the southern Brazil was worse than expected. In August 2021, Brazil’s Mines and Energy Minister Bento Albuquerque said the reservoirs of the country’s hydroelectric power plants in the southeast and midwest suffered a greater reduction than expected, and Brazil had lost hydropower output equal to the energy consumed by the city of Rio de Janeiro in five months.
The country had to import electricity from its neighbors and boost power generation at plants across the country to meet energy demand. Case in point, Porto de Sergipe I was requested to generate power non-stop since early July 2021 to compensate for the lack of hydro. generating uninterrupted operation (24x7) with efficiency and safety.
In September, Bento Albuquerqued tweeted: “The Porto de Sergipe I plant, located in the municipality of Barra dos Coqueiros, has an installed power of 1.5 GW with consumption of 6 million m³/day of natural gas. Thermal Plants such as Porto de Sergipe are extremely strategic to enable the growth of the renewable energy park.”
GE’s 7HA technology played an important role in enabling a quick response to fluctuations in grid demand and adapting quickly to weather changes. Glauco Maximiano de Campos, CEO of CELSE said: “Port of Sergipe I Complex project represents a milestone for Brazil, adding to the system a large-capacity plant that operates in a safer, more reliable, flexible, and efficient way, which brings stability to the country’s electricity matrix and helps to reduce the risk of rationing and/or blackouts”.
Building the entire plant with focus on safety
Porto de Sergipe incorporates three GE Gas Power-manufactured 7HA.02 turbines powering three H65 generators, and a STG -D650 steam turbine powering a W90 generator, three Heat Recovery Steam Generators (HRSG) which are triple pressure reheat drum and auxiliary installations, such as cooling towers. GE also built the infrastructure needed to transport the energy produced by CELSE to the Brazilian interconnected system: 33 km of overhead power lines and a 500 kv substation that steps up the power into high voltages for long-distance transmission.
GE provided full engineering, procurement, and construction (EPC) of the Porto de Sergipe I gas power plant and grid construction, as well as associated grid interconnection systems—in addition to controls software and analytics as well as providing service agreements.
“GE has delivered the highest standard of quality in building this entire power plant. They have supplied the advanced power generation and transmission equipment, as well as a comprehensive financial solution package, delivering 1.5 GW of capacity to
the Brazilian grid,” said Edio José Rodenheber, CIO of CELSE.
COVID challenges
The project addressed unprecedented challenges in the construction phase. As COVID-19 pandemic infection rates were climbing rapidly in the region, restrictions on travel reduced the availability and mobilization of construction resources. On-site teams quickly employed procedures such as social distancing and the use of personal protective equipment such as masks and gloves. Additionally, a COVID-19 task force was developed to help address the rapid evolving situation and comply with local and national regulations.
Although this posed a significant challenge in bringing the plant in operation, GE Gas Power and Fieldcore teams put safety first, including initiatives such as the “Stop Work Authority,” which gave power to employees to stop production if they identify a work hazard or a safety issue. In addition, rigorous quarterly audits and a permit-to-work process, activities such as daily site work coordination, toolbox talks, walkdowns, inspections and reward programs were implemented on a regular basis to ensure safety remained top of mind.
Quality was also at the forefront of the project: Sergipe used a modular-based construction process— where large parts of the plant were manufactured and shipped already assembled to the construction site. This included the gas turbine enclosure that houses the machinery, which consists of several pieces, each around the size of a shipping container. Several parts of the steam system, including the critical steam pipes and interconnections within the service platforms, air extraction modules and fuel control modules were connected at the site like massive puzzle pieces. GE Gas Power estimated that this ‘plug and play’ system saved around 400 000 manhours of work at Porto de Sergipe. This modular approach led to a consistent improved manufacturing quality and extended power life, and on-site installation was quicker, easier, and safer.
“The scope and nature of this project were extraordinary,” said Eric Gray, president of GE Gas Power in the Americas region. “GE built not just the power plant but also the infrastructure to enable lower dispatch costs and reliable connection from the power plant to the interconnected power grid, making the electricity generated by Sergipe plant available not only in the northeaster region, but also almost anywhere in the country. Our Operations and Maintenance services and digital solutions proved to be crucial to plant’s performance and availability. We are proud to have completed this exciting turnkey project with high standard of safety and quality which required engagement with a wide range of stakeholders: thousands of local workers, community leaders, local businesses and government and helped CELSE compensate the lack of hydro power while Brazil was going through one of its worst energy crises.”
Fuel efficient, low carbon emissions
Mitsubishi Power said it is constructing one of the world’s most fuel-efficient power plants with among the lowest carbon emissions of any combined cycle power plant in the world at J-Power USA’s Jackson Generation Energy Center in Elwood, Illinois, USA.
While manufacturing and plant construction took place amid the challenges posed by a global pandemic, the project remained on schedule. Both units achieved first fire by the end of 2021.
The project is expected to enter commercial operation in April 2022.
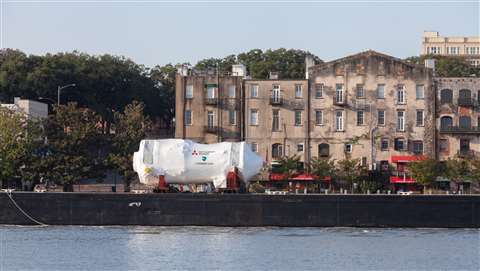
To help modernize, diversify, and decarbonize Illinois’ power grid, J-Power USA ordered two Mitsubishi Power 1-on-1 M501JAC power trains for the Jackson Generation project in July 2019. The project supports the state’s commitment to renewable energy by providing efficient, flexible generation that complements additional wind and solar energy and reduces Illinois’ dependence on coal-fired generation. It will enable Illinois to take advantage of increasingly affordable natural gas and keep electricity rates lower for consumers. The new plant will generate 1000 to 1200 MW of energy — enough to power 1.2 million homes.
Mitsubishi Power’s M501JAC gas turbine solution provides J-Power with the following advantages:
- A combination of greater than 64% efficiency and 99.5% reliability
- Up to 50% more efficiency than peaking plants
- Flexibility to meet fluctuating energy demands
- Low levels of NOx, CO2, UHC, and VOC emissions
Optimized constructability for smooth installation
“We chose the MHPS M501JAC gas turbines for the Jackson Generation Project because MHPS has the best track record of any OEM for delivering fast, flexible, reliable and efficient power,” said Mark Condon, president and CEO of J-Power. “Additionally, the fuel flexibility of the J-Series combustion system allows our plant to use locally available, higher ethane content fuel, and significantly improve the project economics.”
Manufactured at Mitsubishi Power’s Savannah Machinery Works in Savannah, Georgia, USA, the J-Power units are the first M501JAC gas turbines to be manufactured in North America and the first to be installed in North America.
Reducing CO2
Flexible CHP project replacing coal with natural gas
MAN Energy Solutions is setting up two gas engine powered combined heat and power (CHP) plants in the city of Chemnitz, Germany, for local energy service provider eins energie in Sachsen.
The two plants, MHKW Nord and Altchemnitz, will respectively operate with seven and five MAN 20V35/44G TS gas engines, each with an electrical output of 12.6 MW. The new CHP plants will supply the city with 150 MW of electricity and up to 140 MW of thermal output – with an overall fuel efficiency of more than 90%.
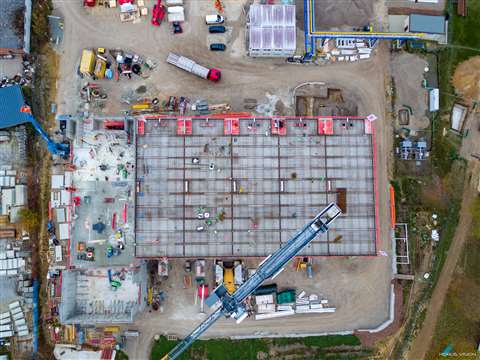
Replacing coal
The power plants are replacing an existing, lignite-powered plant, currently responsible for 95% of Chemnitz’ heat supply, as part of eins’ future concept: ‘New heat for Chemnitz’. Thanks to its low-emission gas engines, the two new plants will reduce CO2 output to around 60% of those emitted by the older plant, corresponding to the emissions of around 260,000 passenger cars.
“We decided to use gas engines for power generation and are accordingly investing in − from our perspective – the most progressive and flexible, thermal power-plant technology as this is also the most environmentally-friendly solution,” said Roland Warner, chairman of the board at eins. “In addition to conventional natural gas, the engines will also be capable of running on such climate-friendly fuels as biogas or synthetic gas. Looking ahead, it will therefore be possible to reduce emissions even further.”
MAN Energy Solutions additionally reports that the MAN 35/44G TS engines are ‘H2-ready’ and operable with a hydrogen content of up to 25% by volume in a gas-fuel mix with specific conditions.
A technology push from Rolls
Company commissions new Fuel Cell Demonstrator
Another new technology – the hydrogen fuel cell – has been installed at the Friedrichshafen plant of Rolls-Royce’s Power Systems division with a 250 kW demonstrator to test future zero-carbon energy systems and present findings to customers.
“We firmly believe that fuel cell technology is set to make a huge contribution to a successful energy turnaround. That’s why Rolls-Royce sees it as its mission to assume a pioneering role in fuel cell applications,” said Andreas Schell, CEO of Rolls-Royce Power Systems. “Fuel cells shall form an elementary part of our product portfolio for sustainable solutions.”
High efficiency
Why fuel cells? Fuel cells have very high efficiency levels when generating electricity from hydrogen and oxygen. When run on pure hydrogen, they give off zero emissions – only water vapor – as well as being low-noise, low-maintenance, and vibration-free. “The greatest benefit is when they are run on regeneratively produced hydrogen because this enables polluting and climate-damaging gas emissions to be fully eliminated,” said Dr. Peter Riegger, vice president Rolls-Royce PowerLab. “This gives fuel cells a huge potential to become a major technology for decarbonizing propulsion and electrical power supply systems.”
Much has happened at Rolls-Royce Power Systems’ Friedrichshafen plant 1 in 2021, with the complex hydrogen infrastructure – which requires a lot of investment – installed and the container all set up complete with its four low-temperature PEM fuel cell modules. Indeed, this took quite a lot of work by engineers across a variety of sites.
Safety key
Designed at the company’s plants in Ruhstorf (Bavaria) and Friedrichshafen, safety reasons dictate the container has two separate compartments for fuel cells and batteries, plus a host of power electronics. The control system has now been fully refined, cooling and air conditioning are on the roof, and a rack system enables simple maintenance, allowing individual system modules to be replaced as required.
The energy systems using fuel cell modules from the automotive sector have been put through their paces on the test stand, and Rolls-Royce engineers are more than happy with the results: “Power flexing characteristics and performance are excellent, and as expected there are no vibrations or no loud noises,” said Riegger.
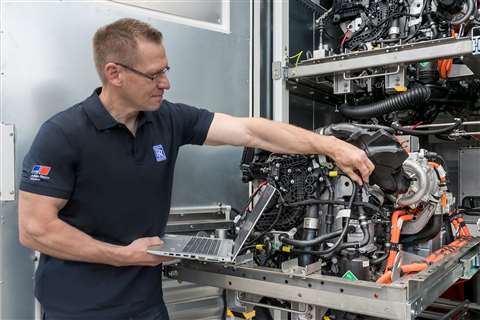
The next step was to connect all four demo modules together in the container and hook up the batteries and power circuit. The plant was successfully commissioned in the second half of 2021.
The demonstrator will be used for test purposes, and to show interested parties which applications the system is suitable for. These include standby power, prime power, uninterruptible power supplies (UPS) and black start capability, allowing the system to be started from scratch without a mains connection. The system consists of fuel cell modules, batteries, fire protection, air conditioning and safety systems, cooling, gas supply and automation.
POWER SOURCING GUIDE
The trusted reference and buyer’s guide for 83 years
The original “desktop search engine,” guiding nearly 10,000 users in more than 90 countries it is the primary reference for specifications and details on all the components that go into engine systems.
Visit Now
STAY CONNECTED



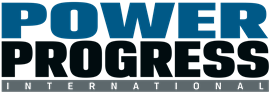
Receive the information you need when you need it through our world-leading magazines, newsletters and daily briefings.
CONNECT WITH THE TEAM
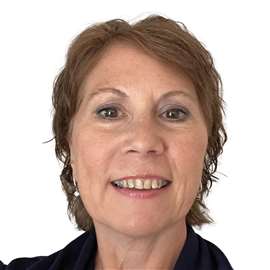
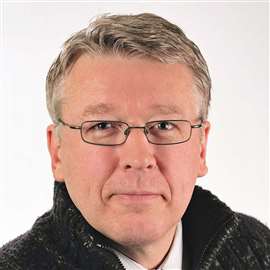
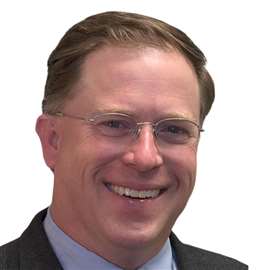
