Powertrain Solutions For Electrified Trucks & Buses
21 September 2017

AVL paper looks at powertrain components and systems needed for zero-emissions urban transport
Editor’s Note: AVL List GmbH (AVL) developed two specific solutions for electric trucks and buses: a modular battery concept and an integrated electric axle.
The concept designs for both systems were described by Heimo Schreier, head of Product Line – Truck & Bus Electrification at AVL List GmbH, in a paper presented at the 2017 AVL International Commercial Powertrain Conference in Graz, Austria, with the title “Powertrain solutions for electrified trucks and buses”.
Co-authors are: Burak Aliefendioglu, senior system engineer – Battery; Roger Perthen, manager – Electric Drive Systems; and Jürgen Tochtermann, lead engineer design – Commercial Vehicle Transmission at AVL List GmbH.
A condensed version of the paper is presented here.
In the past, electrified trucks and buses were mainly built by the integration of existing components and sub-systems with the target of minimized modifications compared to the conventional vehicle. To reach the necessary energy content several existing battery systems were integrated in parallel and mounted on the outer side of the vehicle frame. On the inner side of the vehicle frame, existing electric motors, inverters, transmissions and propeller shafts replaced the conventional powertrain.
While such a concept is appropriate for low production volumes, the drawback is less than optimum efficiency, durability and weight as well as relatively high product cost. Furthermore, mounting battery packs on the outer side of the vehicle main-frame structure compromises crash safety.
The actual target of today’s specific developments is the reduction of the product cost as well as the improvement of system efficiency, weight and durability.
Depending on the specific application though, vehicle weight, driving cycle power and energy demands for trucks and buses vary strongly. Therefore, it is necessary to develop modular concepts which share components and conceptual features and can be scaled as well. Actually it is necessary to build a commercial vehicle family of varying sizes depending on the application and the gross vehicle weight (GVW).
A central part of the newly developed approach by AVL is a modular battery system, which is packaged inside the vehicle main-frame, between the front and the rear axle. Such an arrangement improves not only the crash safety of the vehicle, but also enables more freedom for vehicle packaging at the outer side of the vehicle frame.

The possibility of easily adjusting the battery capacity and power output depending on the application and customer requirements is essential to avoid recurring development costs.
The new battery concept for commercial vehicles by AVL introduces a scalable rack system so that the battery can be easily adapted to any vehicle variant from light duty to heavy duty. The racks integrate a flexible number of existing battery modules mechanically, thermally and electrically. They can be arranged in various different alignments.
The most suitable rack concept will depend on the actual topology of the selected modules as well as the actually available space in the vehicles to reach highest energy packaging density.
With such a modular arrangement, different rack sizes can be assembled; as an example, a rack could consist of two identical half racks which are connected via a two-sided liquid cooling plate. The large rack consists of 12 battery modules (six in each half rack) in three layers. The small rack consists of four battery modules (two in each half rack) in one layer.
With the two rack sizes (large and small) different battery pack configurations can be realized – depending on the actual vehicle packaging requirement.
The battery concept is also flexible to provide different voltage and energy levels within the battery family. Even a voltage level of 800V is possible, which provides also benefits during high-power charging for commercial vehicles.

One crucial requirement for commercial vehicles applications is fast charging to ensure high vehicle availability and productivity. To investigate the charging performance, AVL performed a simulation for a pack with 223 kWh energy content. The simulation considers pack, module and cell level voltage as well as current limitations. Results have shown that 65% charge is reached in less than 30 minutes, while 80% is reached after 40 minutes.
One of the main advantages of this battery pack design by AVL is the thermal management. Based on detailed thermal analysis, an advanced cooling concept has been developed which enables not only the highest battery performance during charging and discharging, but also ensures durability in all ambient conditions.
In addition to the battery hardware, AVL provides advanced battery management system functionalities.
Finally, the modular battery concept enables the integration of various existing and future battery modules from different suppliers and can be adjusted to individual customer requirements.
In order to provide maximum space for the battery packaging – and hence maximum battery energy for maximum electric range of the vehicle – a compact integrated electric axle is mandatory for the electric drive.
Electric Axles
The electric axle for heavy-duty urban trucks developed by AVL can be packaged in conventional vehicles without major vehicle modifications. Its 800-V design ensures that the power requirements are achieved with cost effective components.
By integrating all electric drive components in the axle, the protected space within the vehicle frame can be used for the battery packaging. Additionally the high degree of integration provides potential for the optimization of system weight and efficiency compared with an electric drive system with separate components.
The electric axle system integrates all electric drive components in the axle: inverter (including control of all transmission functions); electric machine; transmission (including shift actuation and lubrication system); and cooling system (including oil pump).
This configuration limits overall system complexity and supports system reliability as well as the vehicle assembly process, as the number of interfaces to the vehicle is limited. Just high voltage power connections, controller connections as well as cooling-oil connections need to be linked into the vehicle.
The integration of AVL’s unique permanent synchronous electric motor design, with direct cooling of the stator, ensures highest continuous power density, smallest packing, as well as a wide range of electric motor efficiencies – above 95%. With that, lowest energy consumption and longest electric range of the vehicle can be achieved. An electric motor speed level of up to 16 000 r/min ensures minimized product cost and size.
The highly integrated design of the AVL power electronics based on standard insulated-gate bipolar transistor (IGBT) technology – which also includes the transmission control – eliminates the need of AC cabling and therefore helps avoiding electromagnetic compatibility disturbances in the entire vehicle. Additionally, it leads to minimum system cost.
In order to ensure highest system efficiency and best vehicle performance, a two-speed transmission and a differential are integrated in the e-axle system. A layshaft-type arrangement allows smallest packaging as well as modularity for different applications. The design is optimized to handle the high input speeds of the e-motor.
The cooling system design ensures that each component of the electric axle is supplied with a coolant temperature meeting its individual requirements. This makes highest system efficiency and durability possible.
Both the battery concept and the integrated electric axle developed by AVL are prepared to be packaged in todays’ vehicle architectures. Hence, both concepts can be carried over into a mass production development program within short term.
The first start of production of such specific truck and bus solutions is expected to happen in the time frame 2019/2020.
For more information: avl.com
POWER SOURCING GUIDE
The trusted reference and buyer’s guide for 83 years
The original “desktop search engine,” guiding nearly 10,000 users in more than 90 countries it is the primary reference for specifications and details on all the components that go into engine systems.
Visit Now
STAY CONNECTED



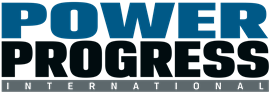
Receive the information you need when you need it through our world-leading magazines, newsletters and daily briefings.
CONNECT WITH THE TEAM
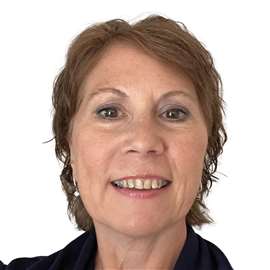
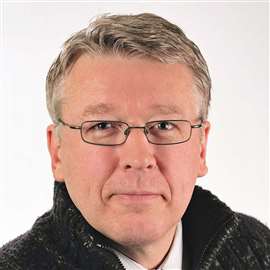
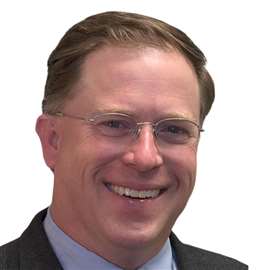
