Printed Blades From Siemens
06 February 2017

Siemens said it achieved a breakthrough by finishing its first full-load engine tests for gas turbine blades completely produced using Additive Manufacturing (AM) technology.
The company successfully validated multiple AM printed turbine blades with a conventional blade design at full engine conditions. This means the components were tested at 13 000 rpm and temperatures beyond 1250o C. Siemens also tested a new blade design with what it said was a completely revised and improved internal cooling geometry manufactured using the AM technology. The project team used blades manufactured at its 3D printing facility at Materials Solutions, the newly acquired company in Worcester, UK. Materials Solutions specializes in high-performance parts for high-temperature applications in turbomachinery where accuracy, surface finish and the materials quality is critical to ensure operational performance of the parts in service, the company said. The tests were conducted at the Siemens testing facility in the industrial gas turbine factory in Lincoln, UK.
“This is a breakthrough success for the use of Additive Manufacturing in the power generation field, which is one of the most challenging applications for this technology,” said Willi Meixner, CEO of the Siemens Power and Gas Division. “Additive Manufacturing is one of our main pillars in our digitalization strategy. The successful tests were the result of a dedicated international project team with contributions from Siemens engineers in Finspång, Lincoln and Berlin together with experts from Materials Solutions. In just 18 months they completed the entire chain from component design and AM material development to new methods for lifing simulations and quality controls. With our combined know-how in 3D printing, we will continue to drive the technological development and application in this field,” added Meixner.
The blades were installed in a Siemens SGT-400 industrial gas turbine with a capacity of 13 MW. The AM turbine blades are made out of a powder of high performing polycrystalline nickel superalloy, allowing them to endure high pressure, hot temperatures and the rotational forces of the turbine’s high-speed operation. At full load, each of these turbine blades is traveling at over 1600 km/h, carrying 11 tons or equivalent to a fully loaded London bus, is surrounded by gas at 1250° C and cooled by air at over 400° C. The advanced blade design tested in Lincoln provides improved cooling features that can increase overall efficiency of the Siemens gas turbines.
Additive Manufacturing is a process that builds parts layer-by-layer from sliced CAD models to form solid objects. Also known as ‘3D printing’ it especially provides benefits in rapid prototyping. “This exciting technology is changing the way we manufacture by reducing the lead time for prototype development up to 90%,” said Meixner. “Siemens is a pioneer in Additive Manufacturing. We can accelerate the development of new gas turbine designs with an increased efficiency and availability and can bring these advancements faster to our customers. This new flexibility in manufacturing also allows Siemens to develop closer to the customer’s requirements and also to provide spare parts on demand.”
Siemens said it has a broad knowledge in essential areas like materials sciences, automation, manufacturing and process know-how and is thus in a great position to shape the future in the 3D printing industry. The successful test of the advanced blade design is the next step in order to use the full potential of AM. Siemens is developing unique gas turbine designs which are only possible with AM and extends its serial production for printed turbine equipment. Siemens uses AM technology extensively for rapid prototyping and has already introduced serial production solutions for components in the gas turbines’ compressor and combustion system. In February 2016 Siemens opened a new production facility for 3D printed components in Finspång, Sweden. The first 3D printed component for a Siemens heavy-duty gas turbine is in commercial operation since July 2016.
POWER SOURCING GUIDE
The trusted reference and buyer’s guide for 83 years
The original “desktop search engine,” guiding nearly 10,000 users in more than 90 countries it is the primary reference for specifications and details on all the components that go into engine systems.
Visit Now
STAY CONNECTED



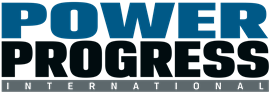
Receive the information you need when you need it through our world-leading magazines, newsletters and daily briefings.
CONNECT WITH THE TEAM
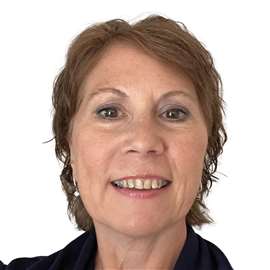
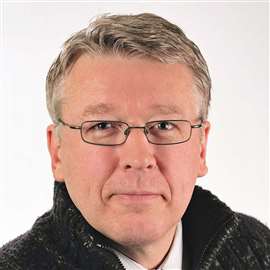
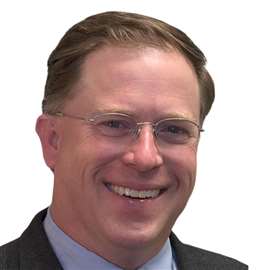
