The New Frontier: System Integration
16 May 2016
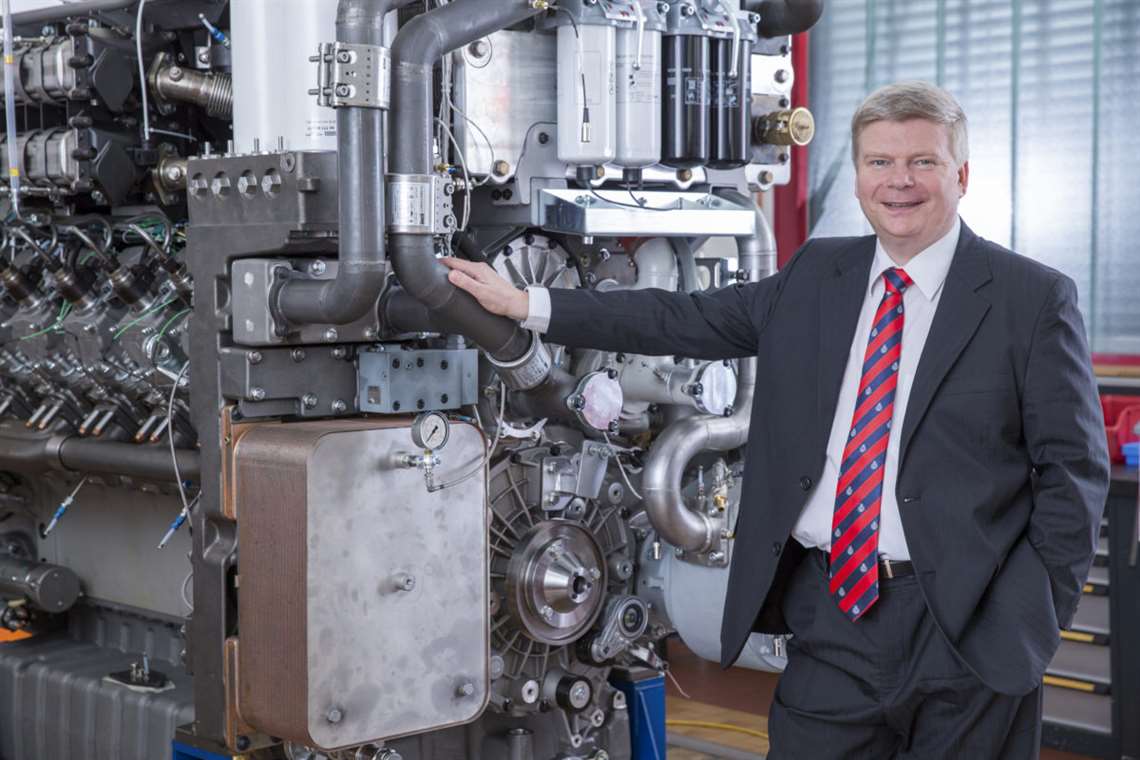
BY ROBERTA PRANDI
Editor’s Note: The concept of system integration has become more and more important for manufacturers of mobile vehicles, marine vessels and power stations. Diesel & Gas Turbine Worldwide spoke with Dr. Marko Dekena to better understand what this system integration means, what advantages it can bring and which prospects it has for success in the market.
Dekena, executive vice president at AVL List, was recently confirmed to the board of CIMAC (The International Council On Combustion Engines) as one of the vice presidents—Technical Programme.
WW: Dr. Dekena, could you expound on the concept of system integration. What does it mean in practice?
Dekena: Every power or transmission system, but also the respective auxiliary systems, contain a variety of components. In the past, these components were taken from the market as available and installed mainly based on criteria like function and acceptable output and costs. Such a system cannot be an optimum solution.
System Integration is a real paradigm change and needs a holistic approach. It starts with the system requirements followed by the system specifications and ends in the subordinated components definition. It has the task to optimize the whole system already during the planning phase towards optimum function at highest efficiency and lowest fuel consumption.
WW: Would you give some examples of what system integration can mean for the various applications (marine, power generation, oil & gas, railway, and other mobile applications)?
Dekena: The advantages of system integration can be very diverse for different applications. For marine applications these can, for example, start with the integration of both mechanical and electrical systems thereby enabling new degrees of flexibility in the arrangement of main and auxiliary engines. When combined with on-board batteries, such hybrid systems offer a huge potential for the optimization of overall system performance.
On locomotives and mining trucks, where the powertrain is mostly already electrified, system integration will, at a future stage, encompass the aftertreatment system integration through to hybridization.
For stationary power generation, system integration can mean the integration of alternative energy sources, such as solar and wind power, while maintaining grid performance and grid stability. It can also mean the power management of multiple engine installations for maximum efficiency of both engine and aftertreatment systems.
All these applications have something in common, namely the need for accurate system simulations in order to optimize system performance, rather than focusing only on components.
WW: What does system integration entail for the vehicle manufacturer, the plant operator? What type of work needs to be done ahead of the final project, with the various suppliers?
Dekena: First of all suppliers as well as OEMs and plant operators have to be open for new approaches in planning and development of complete power systems. They have to accept that the bigger effort in planning and optimization of power systems will finally be rewarded by a stronger position on the market, higher efficiency and availability of the plant and lower total cost of ownership respectively.
WW: How much more complicated is system integration in the developing phase, compared to less integrated and more conventional development work?
Dekena: Of course the effort during the development phase is higher and called “Front Loading Approach,” but it finally pays off. With this approach a solution can be created which lowers total cost of ownership, which means saving operational costs, increasing the quality and reliability of the system. In addition time to market will be reduced.
WW: How much of the development phase can profit of virtual tools? Can you explain which kind of tools can be used to make system integration easier or more successful?
Dekena: Virtual System Integration is a valuable methodology in the entire development process. Extended system simulations of ships, mining trucks, locomotives or power plants support concept and investment decisions at the beginning of the development phase. Furthermore, model-based approaches help to develop an optimum application according to the given requirements, even merging the simulation and testing world.
A good example is the model-based development of the control system during which the hardware control system is running together with models of engines and other components of large engine applications as hardware in the loop. Due to the reduced testing effort the model-based approaches are very beneficial in view of cost and reduction of development time. Besides, virtual system integration is a criterion for quality assurance as in a very early stage of the development phase the system behavior can be investigated and possible weak points can be detected. Development loops are much faster and cheaper. Virtual system integration can be used seamlessly during the entire development process supporting numerous tasks.
WW: What are in your opinion the benefits of system integration? Which key aspect would you say makes this approach interesting for the manufacturers?
Dekena: System Integration provides benefits for both the manufacturers and the users. The manufacturers strengthen their position compared to their competitors based on the above mentioned advantages. The users save operational costs. In case of hybridization, where it makes sense from the operational point of view, a reduction of fuel consumption up to 30% can be realized. So a short-term return of investment can be achieved despite the higher initial development effort.
WW: What is the future of this approach in the various markets? Do you see some applications or markets that are already more advanced with this approach? Some that are particularly promising for future developments?
Dekena: For sure the automotive industry is leading in system integration today. But in the marine and rail industries, which are supported by the CIMAC organization, we can already experience growing development efforts towards system integration. For this purpose CIMAC has introduced a new working group “System Integration”. The main driver is fuel cost reduction. This means not only lower operational costs, but also an essential decrease in CO2 emissions and thus a valuable contribution to protect our environment.”
A discussion of System Integration will be part of the Technical Programme of the CIMAC World Congress, which will be held from June 6 – 10, 2016, in Helsinki, Finland.
POWER SOURCING GUIDE
The trusted reference and buyer’s guide for 83 years
The original “desktop search engine,” guiding nearly 10,000 users in more than 90 countries it is the primary reference for specifications and details on all the components that go into engine systems.
Visit Now
STAY CONNECTED



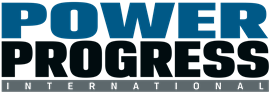
Receive the information you need when you need it through our world-leading magazines, newsletters and daily briefings.
CONNECT WITH THE TEAM
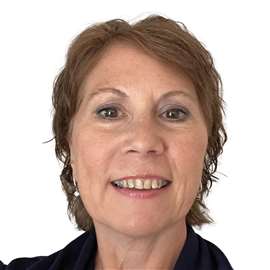
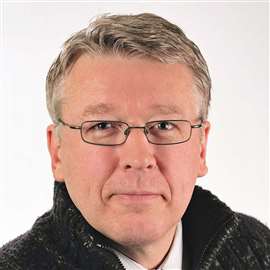
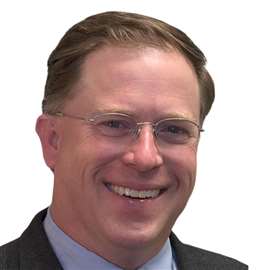
