Perkins demos drop-in electrification solution
05 May 2025
In addition to a selection of engines encompassing diesel and flexible fuel solutions, Perkins chose Bauma 2025 in Munich to showcase a project that Alan Davies, lead design engineer for Perkins called the “Disruptor”. It’s a commercial demonstrator consisting of a battery-electric power unit fitted in a McElroy TracStar 900i pipe fusion machine, and it is intended to highlight the potential for a “drop-in” solution to electrification.
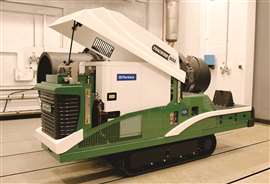
“From conversations that we’ve had at previous events, [suppliers] can showcase components, but what people are struggling with is how to get those components together in a package that they can put into a useful form factor that’s easy for them to install, service and work with,” said Davies. So, Perkins set out on a journey to develop just such a solution.
Perkins had already initiated its e-wheel loader project – the conversion of a diesel-powered wheel loader to battery-electric power.
“We saw the potential there for what a power system could look like... So that rolled into looking for a use application for one of our OEM customers that lent itself to battery systems,” Davies said. After speaking with some of its customers, U.S.-based McElroy expressed interest in exploring an electrification project with one of its pipe fusion machines.
“They were keen to support us with the machine and get some of their engineering team engaged with us so that we could talk to them on how to do the project,” Davies noted.
Before long, a TracStar 900i arrived at the Perkins facility in Peterborough, UK, where a team of engineers set about determining how to replace the existing 3.6 L Perkins 904 diesel engine system with a fully enclosed battery-electric power unit.
‘Plug-and-play’ electrification
According to Davies, the project entailed working with suppliers to identify the right components, as well as with its internal team to ensure the project aligned with the requirements of Perkins’ battery system. Then, the transformation began.
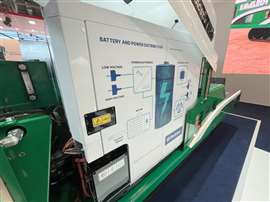
“Out comes the engine and then crudely back in goes the power unit. Now, there were some tweaks to componentry and a bit of change to the body work for the host, just to accommodate some of the air channels and vents,” he explained. “The software is from our side to make sure that it behaved like the engine system that [McElroy was] trying to go for. Really the McElroy team – you couldn’t fault them for their engagement.
“That was a nine-month sort of ‘sprint’ of work to get from the initial machine conversations [starting with] what machine from their family we wanted to use, right through to what we’re seeing here,” Davis said of the demonstrator on display.
The pre-packaged battery-electric power unit includes a Perkins battery, an inverter, electric motor, controller, power distribution unit and onboard charger – all housed in a “plug-and-play” solution.
“What we’ve done is bring all the components needed to deliver a battery-electric power system, and ultimately rotational power, we’re now able to [provide] in the same space claim as a diesel unit. So, tear-up to the machine was minimal,” Davies stated.
“The big thing from the customer standpoint is that all the high-voltage architecture is self-contained into one enclosure. Our customers just need to focus on connecting to the rotational power and everything else is dealt with.”
‘Disruptor’ delivers minimal disruption
The battery-electric power unit utilizes the same mechanical connection and electrical interface points as the diesel engine.
“The position and alignment match up with the 904 diesel engine from an interface standpoint... There’s no movement of hydraulic systems; you can line up with it and integrate onto it,” Davies said. “Same with the harness for the machine. The multi-pin plug is the same as with the diesel engine, so the customer doesn’t need to do harness changes.” The only addition the OEM needs to provide is a ground strap.
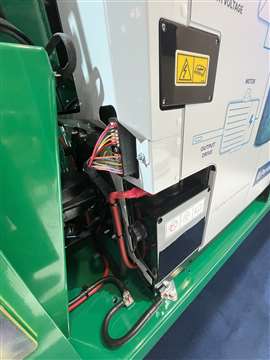
“For our dealer interfacing, once they open the panels, everything is the same inside there. So, our dealer technicians and our teams won’t have to have training on different layouts of high-voltage systems,” Davies pointed out. “It’s going to be a common interface, so they can slowly ramp up their training as they get more experience with high voltage.”
As for end users, the difference compared to a diesel machine should be minimal. “It acts like a diesel engine,” Davies stated. “For customers, they can turn the key as if they’re cranking the engine on a diesel platform and that power unit will respond in the same way, communicate in the same way. It’ll be the same performance as the diesel engine but with zero emissions at point of use.”
Seeing the possibilities
The unit displayed at Bauma was built to explore the possibilities of a drop-in solution and as a learning opportunity.
“Along the journey, [McElroy] started off saying, ‘It’s something that we want to understand what it looks like,’” Davies noted. “Now, there are more and more customers coming on saying, ‘Yeah, we get it; we can see how easy this is. We can see the application.’ And they’re starting to see what other benefits this power unit can give to their customers.”
In addition to zero emissions and lower noise levels, Davies said there are other features that the power unit could provide – for example, an ePTO-like capability to power functions such as the heating element for fusing pipe, or low-voltage output to support cab lights and instrumentation.
Other options, such as hot or cold weather packages, range extenders, DC charging or battery cooling could be possibilities, as well.
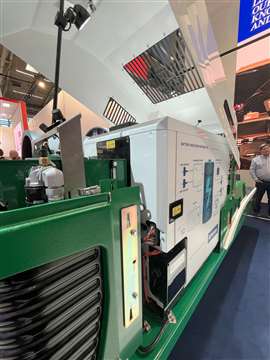
“All of these are things that we can start to talk about more with [McElroy] going forward – how we can tailor that solution to really deliver what they want for their customers,” Davies said. “What they’re really, really excited to see is how simple the install has been and how little tear-up is needed from their side. Although we’ve been engaged with them, we haven’t needed to lean on them heavily at all, because we wanted to make it as clean as possible.”
A new conversation
When the battery-electric power unit might be commercially available remains to be seen. There are still plenty of considerations to address.
“There are price points for some of these solutions that we need to be sensitive to and make sure that the TCO (total cost of ownership) is right. Some of the components we’re going to have to go for a purchased solution. But even then, there’s challenges,” Davies acknowledged. “How do you make that work in the application that you have to make sure that the data and service tool communications are robust?
“We partner with certain suppliers; we’re also manufacturing some of the components ourselves. What we’re looking at doing is collecting those pieces and solving how to make them all work together,” he continued. “So, there’s a bit of a mixture going on. It really just depends on at what price point the parts are coming in.”
Perkins will pilot additional models over the coming months to iron out some of these details and to not only start conversations about electrification but change those conversations altogether.
“The conversations that I’ve been having with our customers are more about how they can exploit as much benefit from that power unit as possible, rather than conversations that we were having maybe two years ago, ‘Well, how do I even start? Where do I go for an inverter?’ Now it’s ‘That’s the solution. Okay, how do I get the most out of that?’ So, it’s pivoted, which is a really good thing because it means that what we’re showing has got a market for it,” Davies stated.
“Part of the journey now is to work with our customers, the same as when we’re looking at engine installs, really digging down into what the machine is doing,” he continued. “When we’re talking to customers, we can look at the load cycles, the duty factors on the platform and work with them to see what size battery they need, what their charging schedule might look like. All of that is just to give confidence that the power system will do the shift that they need.”
The beauty in all this, said Davies, is that with the motor sizes and capabilities available in the industry, the battery technology that Perkins owns and the fact that Perkins can control so much of the system, “we’re in a great place to offer a scaled platform.”
While the system in its present form mimics the 904 engine platform, Davies said there’s no reason it couldn’t be scaled up or down to be used in place of other engine series.
“It’s about understanding who our lead customers are, what their pulls are and then tailoring the hardware sets for that,” he stated. “Although the package that we see there is in one form inside the box, what we’re trying to do is avoid the conversations of what’s in the box. What [customers] need is power. Let us sort out that, and we’ll deliver the power with everything inside the box.
“So, if there are other engines in other machines that we want to look at replacing with electric power, we can configure the footprint of that to match those engine platforms,” Davies concluded. “That opens us up to different markets and different opportunities that maybe we didn’t have before with the diesel only.”
POWER SOURCING GUIDE
The trusted reference and buyer’s guide for 83 years
The original “desktop search engine,” guiding nearly 10,000 users in more than 90 countries it is the primary reference for specifications and details on all the components that go into engine systems.
Visit Now
STAY CONNECTED



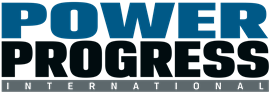
Receive the information you need when you need it through our world-leading magazines, newsletters and daily briefings.
CONNECT WITH THE TEAM
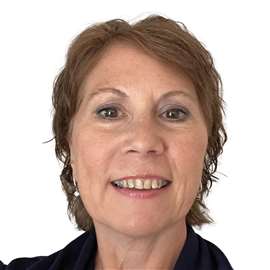
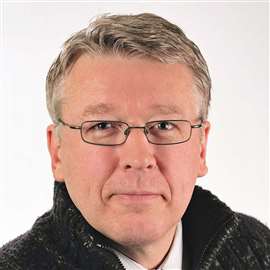
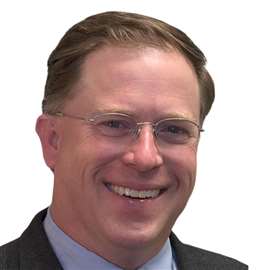
