Two decades in, Danfoss’ Plus+1 still eyes innovation, OEM empowerment
09 April 2025
In celebrating the 20th anniversary of its Plus+1 platform, Danfoss Power Solutions noted the tool preceded certain key technologies that we take for granted today. These include the launches of YouTube (2005) and the iPhone (2007).
Announced when the company was known as Sauer-Danfoss, Plus+1 was intended to allow small- and medium-sized OEMs — typically with fewer resources than their larger counterparts — to customize electronic machine control with the precise functions required for a specific piece of equipment.
At the time, it was apparently buzzworthy throughout the industry. Joseph Maher, sales director for Danfoss Power Solutions’ Connect & Control Solutions business unit, recalled his time working for a Danfoss competitor when Plus+1 was launched.
“It was introduced at a trade show, and I can remember that was the talk of the trade show,” he said. “It was really revolutionary. Everyone you talked to was like, you have to go to the Sauer-Danfoss booth and check out what this was all about. And it was a revolution — no one was doing that in our industry.”
A Comprehensive Suite
But Danfoss had bigger plans for the platform.

“We were at that time, 20 years ago, a component supplier,” said Paola Lugo, vice president of Software for Danfoss Power Solutions. “And we had this big vision of becoming a system supplier. So, one of the main challenges was to transition what at the beginning was a tool into a full ecosystem — a comprehensive and holistic ecosystem that offers different possibilities.”
Today, Danfoss has achieved that, calling Plus+1 a comprehensive platform of software, hardware and engineering services that speeds up development and allow OEMs to bring machines to market more quickly — a key to its success, Danfoss said.
“Plus+1 empowers equipment manufacturers by extending their in-house software development capabilities, enabling them to customize electronic machine control with unprecedented precision,” Lugo said. “It has helped OEMs achieve higher levels of efficiency, safety and productivity, and it has helped them reach these goals faster, simpler and with greater flexibility.”
The platform’s software includes Plus+1 Guide, which allows software engineers to quickly build and customize complete electrohydraulic subsystems and vehicle control solutions. The software simplifies programming via preprogrammed function blocks and application libraries.
“One of the key aspects of it is that with the ecosystem, we enable our customers to do their own development, and with the graphical programming, it’s very easy for a customer that might not have extensive experience in software development to still develop functions and systems together with us,” Lugo said.
Additionally, the Plus+1 software seamlessly integrates with users’ preferred coding languages, Danfoss said — such as Qt, C, MATLAB Simulink and PLCopen — allowing them to import and leverage existing code for additional customization and efficiency.
Know-How Built In
Maher added that Danfoss’ extensive experience working with customers is how the Plus+1 software has become so robust.
“Danfoss has always been a company that invests heavily in our application engineering services to our customers to make sure that we are helping them integrate products and solutions into their machines,” he said. “So, what ends up in the library of software function blocks that we have is essentially hundreds of years of different individuals’ know-how and expertise that gets translated into actual code in the software that is part of helping our customers get to market faster.”
Danfoss said the Plus+1 hardware complements the software so that all Danfoss electronic and electrohydraulic products can integrate seamlessly in the control system.
Engineering Expertise Available
Finally, the Danfoss engineering services team can supplement any OEM engineering team or take on entire projects as an OEM’s in-house software development team.
“We always strive to have local support where our customers are,” Lugo said. “That’s the way we operate. We have application engineers very close to our customers, talking their language, understanding their needs and translating that into software requirements.”
Maher added, “We empower you to do it on your own. We can work with you, or we can work for you. And we want to make sure that wherever the customer is on their on their journey on control systems, what capabilities they have, we can fill whatever niche that they want.”
The Evolution Continues
Danfoss said the Plus+1 platform will continue evolving to meet the needs of the off-highway machinery market. For example, the company plans to enhance system flexibility by enabling users to program directly in text-based languages while still leveraging the benefits of the platform. Additionally, Danfoss has introduced innovative connectivity and autonomy solutions that it continues to improve and expand.
Further investments in AI and machine learning are also planned to improve developer efficiency and empower end users with more data and predictive maintenance insights about their machines.
“Leveraging things like AI is just one example of many of how software is going to continue to evolve in making us more productive, making our machines more productive going into the future,” Maher said.
Finally, Danfoss will continue to focus on cybersecurity and functional safety, particularly as machine connectivity advances.
“Our customers can have peace of mind that the functions and the libraries in the Plus+1 are following state-of-the-art regulations and standards in terms of safety,” Lugo said.
Maher said it’s an exciting time to be in the industry and using the Plus+1 platform.
“The pace of innovation is accelerating, and to be in an industry that is at the forefront of that is what makes my job a lot more fun,” he said. “I can see it in the discussions that we have with our customers and our distribution partners and the excitement they have in employing solutions involving this ecosystem.”
Lugo added that the global adoption of the platform is a source of pride.
“When we started in 2004, we had at Danfoss internally around 50 developers using the Plus+1 ecosystem,” Lugo said. “Today, around the world, we have more than 3,500 developers — obviously the majority not being Danfoss developers. These are really our customers using the tool.”
John Quisenberry, general manager of Berendsen Drive and Control Systems — a Danfoss Power Solutions distribution partner — has been using the Plus+1 platform since its inception. He likened the tool to the printing press.
“Before it was invented, it was only the elite folks who had books,” he said. “But within years of its invention, the common people had reading materials that they could learn from. It was the same thing with Plus+1. We took what was reserved for large companies with deep pockets and made that available to thousands of manufacturers. This was the first time that small and medium-sized OEMs could get the same type of control system that was being used by the large OEMs.”
POWER SOURCING GUIDE
The trusted reference and buyer’s guide for 83 years
The original “desktop search engine,” guiding nearly 10,000 users in more than 90 countries it is the primary reference for specifications and details on all the components that go into engine systems.
Visit Now
STAY CONNECTED



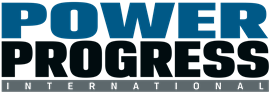
Receive the information you need when you need it through our world-leading magazines, newsletters and daily briefings.
CONNECT WITH THE TEAM
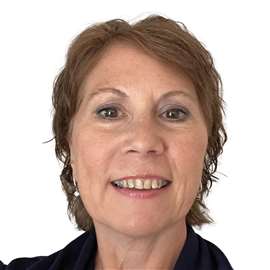
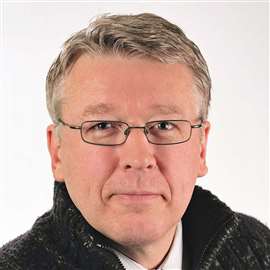
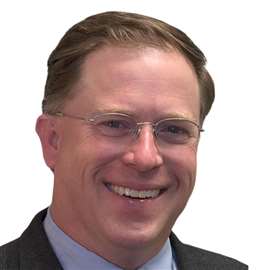
