Automatisch von KI übersetzt, Original lesen
Meilenstein für autonomes Bohren erreicht
27 Juni 2024
Durch die Zusammenarbeit von Caterpillar, Thiess und WesTrac wurden mehr als 1 Million Meter autonom gebohrt
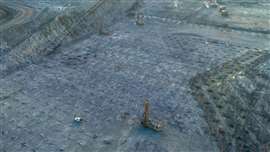
Im April trafen sich Vertreter von Caterpillar, Thiess und WesTrac im Kohlebergwerk Mt. Arthur South in New South Wales, Australien, um einen Meilenstein im autonomen Maschinenbetrieb zu feiern, der drei Jahre lang geplant war. Der globale Bergbaudienstleister Thiess überschritt die Marke von einer Million Bohrmetern autonom. Dabei wurden Cat MineStar-Technologien auf einem Cat MD6250 und zwei Cat MD6310-Bohrern installiert.
Thiess betreibt derzeit drei vollautonome Bohrgeräte in der Mt. Arthur South Mine in NSW. Die Steuerung der drei Bohrgeräte übernimmt ein einzelner Bediener von einer Remote Operating Station (ROS), die zum Bohren Cat MineStar Command verwendet.
Der Weg zum autonomen Bohren in der Mine geschah nicht über Nacht. Laut Caterpillar umfasste die mehrstufige Entwicklung hin zur Automatisierung einen Bausteinansatz, der mit dem Bohrgerät MD6250 begann. Dies erforderte eine enge Zusammenarbeit zwischen Thiess, WesTrac und Caterpillar, nicht nur bei der Implementierung der Technologie, sondern auch bei der Entwicklung spezieller Prozesse für den autonomen Betrieb, dem Change Management und der Entwicklung neuer Schulungsprogramme für das Baustellenpersonal. Diese Prozesse ermöglichten Thiess den Übergang von der personellen Steuerung zur autonomen Steuerung der Bohrgeräte, einschließlich sicherer Arbeitsabläufe.
„Das Engagement von Thiess für dieses Projekt und die Bereitschaft zu einer intensiven Zusammenarbeit waren eine treibende Kraft für den Erfolg“, sagte Sean McGinnis, Vizepräsident und General Manager für Technologie und globalen Vertriebssupport bei Cat MineStar Solutions. „Wir haben eng mit Thiess und WesTrac zusammengearbeitet, um sicherzustellen, dass unsere autonome Lösung ihre wichtigsten Leistungsindikatorenziele erfüllt.“
„Wir sind stolz darauf, ein führendes Unternehmen im Bereich Automatisierung und Autonomie für Bergbaudienstleistungen zu sein“, sagte Trent Smith, Leiter für Autonomie- und Betriebstechnologie bei Thiess. „WesTrac hat das Projekt hervorragend gemanagt und uns vor Ort unterstützt, um uns bei der Technologieimplementierung, Schulung und der Bewältigung der Hürden – einschließlich derer, die durch die globale Pandemie entstanden sind – zu unterstützen.“
Thiess berichtete unter anderem über folgende Ergebnisse der Zusammenarbeit der drei Unternehmen bei der Weiterentwicklung ihrer Betriebsabläufe hin zum autonomen Bohren:
- 20 % Verbesserung der Bohrleistung.
- Mehr als 23 Stunden Bohrauslastung pro Tag.
- Keine erneuten Bohrungen durch autonomen Betrieb.
- Verbesserte Sicherheit und geringere Ermüdung durch Entfernung des Bedieners vom Bohrer, Lärm, Vibrationen und Staub.
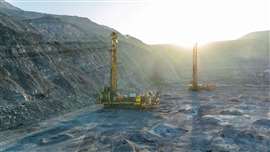
Baustein-Ansatz
Der Weg von Thiess zum Bohr-Meilenstein begann im Herbst 2021 mit der Assistenztechnologie MD6250 der Einstiegsklasse.
„Der schrittweise Ansatz umfasste drei Stufen der Bohrautomatisierung“, sagte Nakia Brewer, Technologie- und Lösungsmanagerin bei WesTrac, „Operator Machine Assist (OMA), halbautonomes Bohren und vollständig autonomes Bohren mit Kollisionsvermeidung.“
Caterpillar bietet verschiedene Autonomiestufen als Baustein für autonomes Bohren. Die Bohrgeräte mit integrierter und erweiterter Cat MineStar-Technologie bieten vielfältige Funktionen, mit denen Bohrsysteme entsprechend den Budget- und Standortanforderungen konfiguriert werden können.
Die Reise in die Welt des autonomen Bohrens beginnt mit der integrierten automatisierten Drill Assist-Funktionalität, die in drei Maschinenfunktionen unterteilt ist:
- Auto Level – ermöglicht die Nivellierung der Maschine und überwacht die Bedingungen, um sicherzustellen, dass sie bei einem Problem angepasst oder gesperrt werden kann.
- Auto Mast – der Bohrer hebt den Mast selbstständig auf den idealen Winkel für das Bohrmuster.
- Auto Drill – verhindert Über- oder Unterbohren durch die Möglichkeit zur Konfiguration standort- und bodenspezifischer Parameter wie Lochdurchmesser, Tiefe und Bohrmethode.
McGinnis sagte, dass Auto Drill einen höheren Grad an Komplexität voraussetzt und für Dreh- und Imlochbohrverfahren (DTH) sowie für Einzel- oder Mehrfachdurchgangsanwendungen verfügbar ist.
„Unter den meisten geologischen Bedingungen ermöglicht die Auto-Drill-Technologie das Bohren ohne Bedienereingriff. Sie überwacht und reagiert auf Komplikationen wie das Freilegen eines Lochs mit hohem Gefälle“, sagte er. „Aufgrund unterschiedlicher Schneidwerkzeuge und Bodenverhältnisse nutzen unsere Bohrgeräte integrierte Bohralgorithmen, um sich an komplizierte Bodenverhältnisse anzupassen und diese ohne Bedienereingriff zu bewältigen.“
Weitere Automatisierung
Cat MineStar Solutions setzt den Weg zur Autonomie fort. MineStar Terrain zum Bohren bietet präzise Führung, um Muster präzise und produktiv fertigzustellen.
Cat MineStar Command für Bohrarbeiten ist der letzte Baustein für autonomes Bohren. Zu Beginn des Programms stattete Thiess den Cat MD6250 mit der OMA-Technologie aus. Diese nutzt Terrain für Bohrarbeiten und dessen bestehendes Netzwerk-Backbone, um die Bediener zu überzeugen und ihnen die Vorteile des autonomen Bohrens näherzubringen, während die Bediener gleichzeitig an Bord bleiben. OMA ermöglicht dem Bediener die Auswahl einer Reihe, und die Maschine navigiert automatisch von Loch zu Loch und bohrt jedes Loch in der ausgewählten Reihe. Sie nutzt die Drill Assist-Automatikfunktion sowie das GPS- und Navigationspaket von Terrain für Bohrarbeiten.
„OMA steigert die Produktivität und Positionsgenauigkeit der Bohrarbeiten und stellt sicher, dass die Bohrer stets der Konstruktion entsprechen, was das Vertrauen in das System erheblich stärkt“, sagte McGinnis.
„Nach der Installation von OMA auf dem MD6250 haben wir sofort den Wert der Technologie erkannt und wie sie eine bessere Bohrleistung für unseren Betrieb ermöglichen könnte“, sagte Smith.
Der nächste Schritt für Thiess bestand darin, den Bediener aus der Kabine zu entfernen. Command for Drilling bietet zwei Stufen des autonomen Bohrens für mehrere Bohrgeräte – mit Sichtverbindung (LOS) und ohne Sichtverbindung (NLOS). Thiess entschied sich für das autonome Bohrsystem NLOS, das den Bediener mithilfe des ROS von der Bohrstelle entfernt positioniert.
Vom ROS aus betreibt das Unternehmen drei völlig autonome Cat-Bohrgeräte und hat es erstmals geschafft, die drei autonomen Cat-Bohrgeräte – ein MD6250 mit Multi-Pass-Funktion und zwei MD6310 mit Auto Multi Pass-Funktion – gleichzeitig mit einem einzigen Bediener zu betreiben.
Neben den betrieblichen Vorteilen durch verbesserte und konsistente Bohrleistung, höhere Auslastung und geringere Nacharbeitskosten nannte Trent Smith auch die erheblichen Vorteile für die Mitarbeiter, die das autonome Bohrprogramm mit sich bringt. „Es verbessert die Sicherheit unserer Bediener, trägt zur Verringerung der Ermüdung bei, da sie kurze Pausen einlegen können, ohne den Bohrbetrieb zu unterbrechen, und bietet attraktivere Möglichkeiten zur Weiterbildung im Umgang mit den neuesten Technologien.“
Thiess hat bisher über 30 Mitarbeiter in Mt. Arthur South von der traditionellen Bohrsteuerung zu autonomen Bedienern und einer Reihe weiterer unterstützender Funktionen befördert. Darüber hinaus hat das Unternehmen in die Schulung von über 500 Mitarbeitern im Umgang mit autonomen Bergbausystemen investiert.
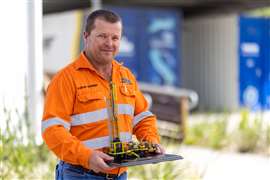
Vollständige Integration der Familie
Die Bohrgeräte MD6250 und MD6310 nutzen gemeinsame Plattformen, Teile, Komponenten und Technologien. Alle Bohrkomponenten und Subsysteme sind so aufeinander abgestimmt, dass sie als System zusammenarbeiten und so die Betriebszeit erhöhen, die Effizienz steigern und die Kosten pro Bohrmeter senken, so Caterpillar.
Der MD6310 bohrt Bohrlöcher mit Durchmessern von 203 bis 311 mm (8 bis 12,25 Zoll) und erreicht bei einem Durchgang eine Bohrlast von 42.149 kg (92.922 lb). Mit dem 13,7-m- bzw. 17,5-m-Mast werden Bohrtiefen von 13,7 m (44,9 ft) bzw. 17,5 m (57,4 ft) erreicht. Mit dem 13,7-m-Mast und dem 17,5-m-Mast erreichen mehrere Durchgänge Bohrtiefen von 74,6 m (244,9 ft), während der 17,5-m-Mast bis zu 48,0 m (157,4 ft) tief bohrt.
Mit einer Bohrlast von 32.655 kg (71.993 lb) bohrt der MD6250 Bohrlöcher mit Durchmessern von 165 bis 200 mm (6,5 bis 9,88 Zoll). Er kann mit einem 11,2 m (36,7 ft) oder 13,6 m (44,5 ft) langen Mast ausgestattet werden. Die Mehrdurchgangsbohrtiefe beträgt mit dem 11,2 m (11,2 m) Mast 53,9 m (176,7 ft), während der 13,6 m (13,6 m) Mast bis zu 37,9 m (124,6 ft) Mehrdurchgangsbohrtiefe ermöglicht.
Als Motor ist die Bohrmaschine MD2650 mit einem Cat C27-Dieselmotor mit 872 PS in der finalen Version der US-Umweltschutzbehörde EPA Tier 4 und mit 826 PS in der Tier-2-Version ausgestattet. Das größere Bohrgerät MD6310 nutzt einen Cat C32B-Dieselmotor mit 1.007 PS in der finalen Version der Tier-4-Norm bzw. 1.031 PS im gleichen Motor, der zur Erfüllung der Emissionsvorschriften der Tier 2-Norm gebaut wurde.
Um die Sicherheit zu erhöhen und potenziellen Ausfällen oder Missbrauch vorzubeugen, sind beide Modelle mit bewährter Cat-Elektronik und Verriegelungen ausgestattet. Die elektronische Kompressorregelung steigert die Produktivität und reduziert gleichzeitig den Kraftstoffverbrauch. Der Cat-Elektroniktechniker überwacht den Zustand von Thiess an Bord, um eine schnelle Fehlerbehebung zu ermöglichen und die Bohrverfügbarkeit zu erhöhen.
„Die beeindruckenden Ergebnisse, die mit Thiess erzielt wurden, lassen sich auch bei anderen Bergbauunternehmen reproduzieren, um deren Betrieb durch Bohrautonomie zu verbessern“, so McGinnis. „Wir freuen uns auf die weitere Zusammenarbeit mit Thiess und WesTrac und auf die Millionen Meter, die noch kommen werden.“
POWER SOURCING GUIDE
The trusted reference and buyer’s guide for 83 years
The original “desktop search engine,” guiding nearly 10,000 users in more than 90 countries it is the primary reference for specifications and details on all the components that go into engine systems.
Visit Now
STAY CONNECTED



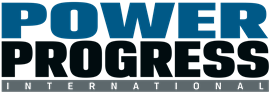
Receive the information you need when you need it through our world-leading magazines, newsletters and daily briefings.
KONTAKT ZUM TEAM
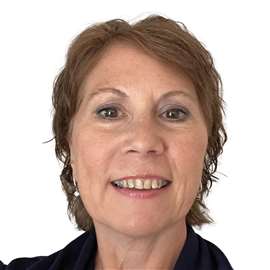
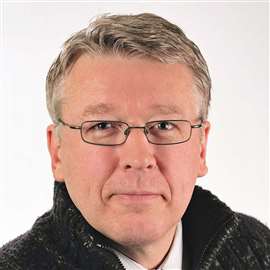
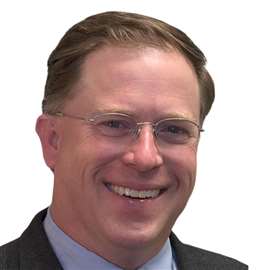
