Automatisch von KI übersetzt, Original lesen
Qualität und Service sind der Schlüssel zum Erfolg auf dem spanischen Energiemarkt
11 Juli 2024

Im Jahr 2022 veröffentlichte die damalige Diesel Progress International einen Bericht über eine Reise zu verschiedenen Maschinenbau- und Energieunternehmen in ganz Spanien. Damals begannen sich diese Branchen gerade erst von den Auswirkungen der COVID-Pandemie und den damit verbundenen Versorgungsengpässen aufgrund nationaler Lockdowns zu erholen. Zwei Jahre später ist Power Progress International nun wieder nach Spanien zurückgekehrt, um die Marktentwicklung zu erkunden und die Gelegenheit zu nutzen, einige der neuesten Technologien kennenzulernen, die sich derzeit in der Entwicklung befinden.
Roquet Hydraulics mit Hauptsitz in Tona bei Barcelona ist auf die Entwicklung und Produktion von Zahnradpumpen, Zylindern, Motoren und Ventilen für Hydrauliksysteme in mobilen Maschinen und landwirtschaftlichen Anwendungen spezialisiert. Das Unternehmen verfügt über Prüfeinrichtungen, um beispielsweise Ermüdungs- und Korrosionsbeständigkeit der Teile zu ermitteln und berät zu optimalen Fertigungsverfahren.
In der Nähe des Firmensitzes in Centelles produziert ein Werk eine breite Palette von Zylindern für Hydraulikanwendungen. Die unter der Marke Dinacil (Teil des Roquet-Portfolios) vertriebenen Teile kommen in Bau- und Landmaschinen sowie in einer Reihe weiterer Industrieanwendungen zum Einsatz.
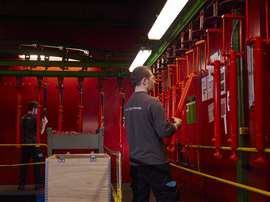
Alle Zylinderteile werden von Roquet in Europa produziert; Dinacil verfügt über ein Schwesterwerk in Rumänien, das ebenfalls Zylinder produziert. Vor diesem Hintergrund ist es überraschend, dass Roquet weder aktuell noch zukünftig plant, in China zu produzieren.
„Auf Messen hören wir ständig die Frage: ‚Produzieren Sie die Teile in China?‘“, sagt Ruth Martinez aus der Vertriebs- und Marketingabteilung. „[In China] gibt es sehr große Produktionsstätten, die Maschinen und die Mitarbeiter. Aber alles, was wir produzieren, wird in Europa und, wenn möglich, von Roquet selbst hergestellt. Wettbewerber fertigen ihre Teile in China, und der Preisunterschied ist nicht unerheblich. Daher setzen wir auf die Qualität unserer Produkte.“
Der Fokus liegt so sehr auf Qualität, dass es bis zu zwei Jahre dauern kann, bis ein neues Zylinderdesign auf den Markt kommt. Nach der Produktion stellt ein 100%iger Testzyklus sicher, dass jeder fertige Zylinder für eine lange Lebensdauer im Feld bereit ist.
Roquet betreibt außerdem weltweit mehrere Ersatzteillager. Laut Martinez tragen diese dazu bei, die OEMs pünktlich mit Komponenten zu beliefern und den Kundenservice des Unternehmens zu unterstützen. „Unser Lager in Thailand beliefert viele lokale Kunden. Außerdem können wir bei Problemen mit einer Komponente vor Ort schnell Ersatz finden und beschaffen.“
Roquet hat kürzlich ein Büro in den USA eröffnet. Während der Standort nach neuen Möglichkeiten sucht, betont Arnau Bellapart, Direktor für Geschäftsentwicklung, dass das Hauptziel die Betreuung bestehender Kunden sei. Er erklärt, dass viele europäische Unternehmen mit lokalen Niederlassungen weiterhin Roquet-Teile verwenden und das neue Büro dazu beitragen werde, den gleichen Support wie in Europa zu bieten.
„Wir müssen in der Nähe sein, um alle Probleme lösen oder bei der Spezifikation beraten zu können. Mit diesem neuen Standort können wir den gleichen Lieferplan wie in Europa anbieten“, erklärt er. Künftig dürfte eine begrenzte Produktion, zumindest bei weniger kundenspezifischen Serienteilen, in den USA stattfinden.
Roquet war ursprünglich kein Komponentenlieferant. Die Ursprünge des Unternehmens gehen vielmehr auf eine Gießerei zurück, die Teile für andere Komponentenhersteller produzierte. Die Gießerei liefert heute rund 30 % ihrer Produktion an Roquet, während ein Großteil der verbleibenden Kapazitäten dem breiteren Markt, darunter auch anderen Hydraulikherstellern, angeboten wird.
Ob Serienfertigung oder Sonderanfertigung – Qualität ist nach wie vor der wichtigste Faktor. „Unsere Zylinder sind teurer, weil wir einige Hightech-Features integriert haben. Gleichzeitig müssen wir aber die Qualität beibehalten – das bedeutet Zuverlässigkeit und die Fähigkeit unserer Komponenten, mehr als eine halbe Million Zyklen auf der Baustelle zu absolvieren“, so Bellapart.
Kundenbetreuung
Qualität spielt auch in der Produktion von Dicsa , einem Spezialisten für Hydraulikschläuche und -armaturen, eine entscheidende Rolle. Das in einem Industriegebiet nahe Saragossa ansässige Unternehmen ist wie viele andere in der Branche tätig und verfügt über Lager voller Teile in allen erdenklichen Formen und Größen, die zum Versand bereitstehen.
Die Liste der Lieferanten, die Dicsa beliefern, ist ein „Who is Who“ der internationalen Hydraulikbranche. „In vielen Fällen fungieren wir als Lager für unsere Kunden“, sagt Pilar Marin, Medienmanagerin. „Wir verwalten ihren Bestand und liefern die benötigten Teilemengen, wann und wo sie benötigt werden.“ Neben dem Standort in Saragossa mit rund 20.000 Quadratmetern Lagerfläche betreibt Dicsa mittlerweile auch ähnliche Standorte in Italien, Deutschland und den USA.
Dicsa stellt auch einige seiner Edelstahlbeschläge selbst her. Marin: „Wir waren schon immer sehr kundenorientiert. Als wir in den 1990er Jahren Probleme hatten, einige Anfragen zu erfüllen, gründeten wir die Fabrik, um unseren Kunden die benötigten Teile liefern zu können.“
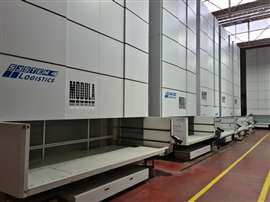
Der 3D-Druck dient der Herstellung von Prototypenteilen, wie Sergio Miguel, Produktmanager am Standort Saragossa, erklärt. „Bevor wir eine Maschine für die Produktion einrichten, können wir vom Kunden freigegebene Muster liefern. Das spart viel Zeit und Geld.“ Teile können so individuell angepasst werden, dass sogar die Spirale einer Verschraubung an die Anwendung angepasst werden kann.
Miguel erläutert, dass in den Produktionshallen in jedem Bereich Teile gleicher Art und Größe produziert werden, was zu kürzeren Umrüstzeiten beiträgt. „Je nach Teil und Komplexität können wir die Maschine in etwa drei Stunden einrichten“, erklärt er. „Eine einzelne Maschine umfasst eine Reihe von Stationen, die verschiedene Prozesse durchführen, bis hin zum fertigen Bauteil. Wir verfügen auch über Montagevorgänge, um verschiedene Teile zu kombinieren; einige sind manuell, andere vollautomatisch.“
Miguel erklärt die Prüfung der fertigen Teile genauer. „Wir verwenden grundsätzlich 316L-Stahl, dessen kohlenstoffarme Qualität entscheidend für die Langlebigkeit der Teile ist. Wir können die Qualität und die Zusammensetzung des Stahls mit einem Funkentest prüfen. Die Maschine erzeugt einen Funken auf das Material, und die entstehende Welle kann analysiert werden, um die Zusammensetzung, den Anteil an Kohlenstoff, Chrom und anderen Elementen zu bestimmen.“
Leistungsentwicklung
Eine kurze Fahrt durch die sonnenverwöhnte Landschaft rund um Saragossa bringt uns zu Carod , einem Unternehmen, das sich ursprünglich auf Motorpumpen für die Landwirtschaft und den Brandschutz konzentrierte, heute aber eine Reihe von Generatoren, Hochdruckreinigern und pneumatischen Kompressoren liefert.
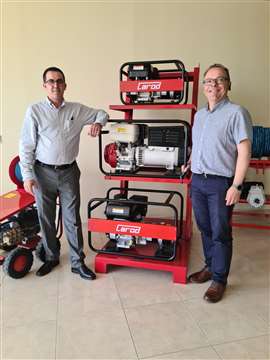
„Das ursprüngliche Werk lag etwa elf Kilometer von hier entfernt, aber 2011 haben wir dieses Grundstück gekauft und unseren neuen Hauptsitz errichtet“, erklärt Exportmanager Mohamed Mohinah. Er fügt hinzu, dass Teile wie die Stahl-Generator-Verschlüsse derzeit zwar von Zulieferern geliefert werden, es aber Pläne gibt, die Anlage zu erweitern und diese selbst zu produzieren. „COVID hat unsere Zulieferer hart getroffen, und die Lieferzeiten stiegen auf fast ein Jahr. Deshalb werden wir unsere eigene Produktion aufbauen, um eine Wiederholung zu vermeiden.“
Seit der Fertigstellung des neuen Werks hat Carod die Leistung seiner Generatoren kontinuierlich gesteigert. „Wir haben die Leistung von etwa 250 kVA auf 800 kVA gesteigert“, so Mohinah. „Wir haben Projekte in Planung, darunter auch unser erstes 1-MW-Generatoraggregat.“ Er fügt hinzu, dass die Produktion bei Carod zu etwa 60 % aus Generatoraggregaten besteht, die restlichen 40 % entfallen auf alle anderen Produkte.
Der Strom für die Generatoren stammt von verschiedenen Lieferanten, darunter Deutz, Volvo Penta, FPT, Honda und Kohler. Neben diesen üblichen Verdächtigen ist auch MWM International, Teil der Navistar-Gruppe mit Hauptsitz im brasilianischen São Paulo, beteiligt. „MWM-Motoren sind rein mechanisch, ohne Computer. Das macht sie sehr zuverlässig und robust.“
In der Montagehalle lagern in Regalen Hunderte von Motoren. Mohinah sagt, dass sie einen Motorenbestand von über 6 Millionen Dollar haben. „Das ist eine weitere Folge von COVID. Wir halten Motoren vorrätig, um Kundenaufträge schnell erfüllen zu können. Wenn der Motor auf Lager ist, kann ich eine Generatorbestellung in etwa vier bis sechs Wochen erfüllen.“ Der Bestand umfasst Motoren der Stufen 2, 3 und 5 mit Leistungen bis zu 500 kVA.
Auf der anderen Seite der Halle zeigt Mohinah auf eine kürzlich fertiggestellte Hochdruckwasserpumpe. Es handelt sich um eine eigenständige Einheit mit Deutz-Motor, Pumpe, Kraftstofftank usw., alles ordentlich in einem Anhänger untergebracht. „Die ist für einen Kunden hier in Spanien. Sie wird zur Brandbekämpfung, aber auch zur Graffitientfernung eingesetzt. Das ist hier sehr verbreitet.“
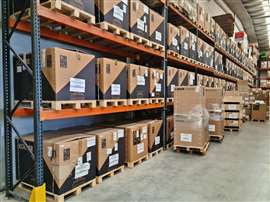
Technische Entwicklung
Spanien blickt auf eine lange Tradition in der Herstellung von Maschinen für Bauwesen, Landwirtschaft, Bergbau, Transport und Energieerzeugung zurück. Darüber hinaus beherbergt das Land zahlreiche technische Institute und Universitäten, die gemeinsam mit Behörden und verwandten Gruppen neue Technologien entwickeln, um die Betriebseffizienz in diesen und anderen Branchen zu steigern.
Das 1984 gegründete ITA (Instituto Tecnológico de Aragón) ist ein Technologiezentrum mit Sitz in Saragossa. In Zusammenarbeit mit dem Ministerium für Wirtschaft, Beschäftigung und Industrie der aragónischen Regierung arbeiten die Teams dort an Projekten zu sauberer Energieerzeugung, digitaler Agrarwirtschaft und nachhaltiger Mobilität.
Ein Team des ITA arbeitet beispielsweise am Ephyra-Projekt (Europäische Produktion von Wasserstoff aus erneuerbaren Energien). Dabei wird eine 30-MW-Anlage zur Produktion von erneuerbarem Wasserstoff in eine Raffinerie in Korinth integriert, die von Motor Oil of Hellas betrieben wird. Diese Anlage wird grünen Wasserstoff an die Raffinerie und andere externe Nutzer liefern und so als Testfall für die Wasserstoff-Kreislaufwirtschaft dienen.
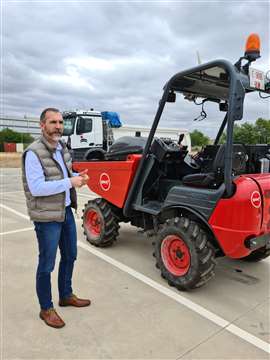
Während die Entwicklung dieses Megaprojekts weitergeht, entwickelt das ITA weiterhin Mechatroniksysteme für Straßen- und Geländefahrzeuge, wie Carlos Bernad, F&E-Projektmanager am ITA, erklärt: „Wir beschäftigen uns mit der Integration von Mechanik, Elektronik und Robotik in Maschinen, um die Funktionalität in allen Bereichen zu verbessern. Wir suchen nach Synergien zwischen diesen Bereichen und konzentrieren uns darauf, wie Mechatronik die Robotik unterstützen kann und umgekehrt. Das unterscheidet sich etwas von der üblichen Perspektive.“
Während sich die Arbeit ursprünglich auf die Verbesserung bestehender Komponenten und Maschinen konzentrierte, erklärt Bernad, dass man von Anfang an in ein Projekt eingebunden sei, das den größtmöglichen Nutzen in Bezug auf Funktionalität und Leistung bringen werde. So führte beispielsweise ein ursprünglich auf Robotik ausgerichtetes Projekt zur Entwicklung neuer Sensoren und zugehöriger Software, die das ITA nun zur Entwicklung von Systemen für verschiedene Zwecke nutzt.
Auf einem Testgelände im Freien präsentiert Bernad eine Reihe von Testmaschinen, darunter einen Muldenkipper und einen mittelschweren Lkw. Jede Maschine verfügt über ein anderes autonomes Fahrsystem, das speziell für die Einsatzumgebungen der Fahrzeuge entwickelt wurde.
Da es für solche Fahrzeuge bereits autonome Fahrsysteme gibt, wird Bernad gefragt, was sich von den vom ITA entwickelten unterscheidet. „Diese Systeme wurden an raue Umgebungen und spezifische Aufgaben angepasst“, sagt er begeistert. „Dank neuester Sensoren und Rechenleistung können sie deutlich mehr Daten verarbeiten und sind dadurch effizienter. Die Datenkapazität macht die Fahrzeuge zudem sicherer, da sie auf Gefahrensituationen besser reagieren und bessere Entscheidungen treffen können. Die neuen Sensoren erfassen die Daten, und unsere Algorithmen nutzen diese Informationen, um die beste Wahl zu treffen.“
Neue Marktchancen
Nach einer Übernachtung in der Nähe von Pamplona reisen wir weiter zu unserem letzten Stopp dieser Tour nach Ibarra, einer kleinen Stadt etwa 30 km südlich von San Sebastian. Hier erreichen wirObeki , einen Hersteller von Elektromotoren, die bisher hauptsächlich in verschiedenen Hebeanwendungen im Baugewerbe, in der Schifffahrt und in anderen Bereichen eingesetzt wurden.
„80 bis 90 % der weltweiten Elektromotorenproduktion finden in Niedriglohnländern statt“, sagt Javier Múgica, kaufmännischer Leiter. „Das bedeutet, dass das Geschäft in Europa weitgehend auf Logistik, Lagerhaltung und Vertrieb basiert. Obeki ist daran nicht beteiligt; wir bieten stattdessen Speziallösungen mit nicht standardmäßigen Funktionen wie Bremssystemen und höherem Drehmoment.“
In diesem Zusammenhang strebt Obeki eine Ausweitung seiner Forschungs- und Entwicklungskapazitäten an, um mit intelligenten Produktdesigns neue Geschäftsmöglichkeiten zu schaffen. „Wir möchten Produkte für anspruchsvolle Kunden entwickeln, die höhere Anforderungen stellen als Kunden mit Standardelektromotoren“, erklärt er.
Laut Múgica produziert Obeki jährlich rund 4.200 Einheiten. „Das ist für ein chinesisches Unternehmen nichts Besonderes“, erklärt er. Für diese Motoren entwickelt das Unternehmen jährlich rund 700 einzigartige Designs. „Eine Produktionsserie von zehn Motoren ist für uns keine Seltenheit, obwohl manche Kunden vielleicht nur ein einziges Exemplar wünschen.“
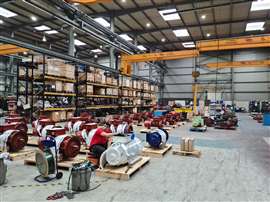
Diese individuelle Anpassung bietet zwei Vorteile. Erstens ist der Motor spezifisch auf seinen Einsatzzweck zugeschnitten, d. h. er ist optimal für die Anwendung geeignet – und dies ist garantiert. Sollte es dennoch zu Problemen kommen, steht Obeki hinter jedem produzierten Motor. „Große Unternehmen versuchen im Problemfall nur, Ihnen einen anderen Motor zu verkaufen. Wir sparen, wenn möglich, Geld und Zeit, indem wir den vorhandenen Motor reparieren.“
Aufbauend auf diesem Know-how, so Múgica, besteht der nächste Schritt darin, die Zahl der Märkte, in denen Obeki-Motoren eingesetzt werden, zu erweitern. „Wir arbeiten derzeit an Projekten, die erneuerbare Energie aus den Ozeanen gewinnen. Unsere Motoren sind Teil von Systemen, die Energie aus Wellen gewinnen.“ Dies erfordert nicht nur eine maximale Motoreffizienz (basierend auf Materialauswahl und Design), um Energieverluste zu minimieren, sondern auch robuste Konstruktionen, die den rauen Bedingungen standhalten.
Diese Energiesammelsysteme befinden sich noch in der Prototypenphase. Angesichts der laufenden Untersuchungen der Technologie in Spanien, Großbritannien und Australien (unter anderem) besteht das Ziel darin, ein Netzwerk von Unternehmen aufzubauen, die eine regelmäßige Versorgung mit entsprechenden Komponenten gewährleisten können.
Vor diesem Hintergrund erklärt Múgica, dass Obeki plant, Motoren für Anwendungen unter noch härteren Bedingungen zu entwickeln. „In Kernkraftwerken werden Motoren für verschiedene Funktionen eingesetzt, wie Lüfter und Pumpen für Kühlsysteme usw. In der Nähe des Reaktors müssen sie zertifiziert sein, um verschiedenen Bedingungen, wie beispielsweise einem Erdbeben, standzuhalten, und aus Materialien bestehen, die durch Radioaktivität nicht zerfallen. Wir möchten uns an der Entwicklung hochentwickelter Motoren für diese Art von Anwendung beteiligen.“
Herausforderungen bleiben bestehen
Während China sich zum weltweit führenden Standort für die Massenproduktion von Maschinen und Komponenten entwickelt hat, sind europäische Unternehmen in denselben Branchen gezwungen, über die niedrigen Kosten hinausgehende Alleinstellungsmerkmale zu entwickeln, um Kunden zu gewinnen und zu binden.
Diese Besuche zeigen, dass die Herausforderungen durch COVID und die daraus resultierenden Lieferkettenprobleme nun vorüber sind – zumindest in einem Fall dient ein größerer Lagerbestand nun als Produktionspuffer. Doch während die Auswirkungen der Pandemie nachlassen, erfordern neue Herausforderungen eine ständige Überwachung und die Umsetzung agiler Lösungen.
In jedem der in diesem Artikel beschriebenen Fälle, von Roquet bis Obeki, ist es den Unternehmen gelungen, ihren Marktanteil zu halten (oder auszubauen), indem sie das erforderliche Fachwissen in einem bestimmten Geschäftsbereich nutzten, sei es Qualität, Anpassung oder Kundendienst.
Es ist eine Selbstverständlichkeit, dass es immer einen Markt für günstige Lösungen geben wird. Doch wenn ein Teil schnellstmöglich benötigt wird, Qualität (und garantierte Verfügbarkeit) ein Muss ist oder eine neue Lösung für eine bestimmte Anwendung entwickelt werden muss, ist ein reaktionsschnelleres Unternehmen wahrscheinlich die beste Wahl.
Dieser Artikel wurde mit Unterstützung von ICEX , dem spanischen Institut für Außenhandel, und ANMOPYC , der Vertretungsorganisation in Spanien für Unternehmen, die Technologien für die Bau- und Bergbauindustrie liefern, erstellt.

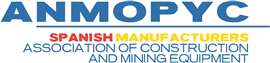
POWER SOURCING GUIDE
The trusted reference and buyer’s guide for 83 years
The original “desktop search engine,” guiding nearly 10,000 users in more than 90 countries it is the primary reference for specifications and details on all the components that go into engine systems.
Visit Now
STAY CONNECTED



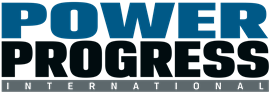
Receive the information you need when you need it through our world-leading magazines, newsletters and daily briefings.
KONTAKT ZUM TEAM
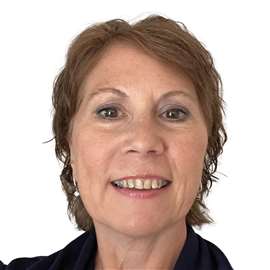
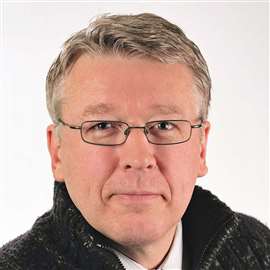
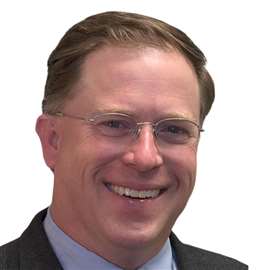
