Macrotrends influencing the future of fluid power
15 April 2025
Part 1 of this two-part series examines major trends impacting machine design and fluid power demands.
“The times they are a-changing,” as Bob Dylan first sang back in 1964. It was true then and it is certainly true now as technology in various forms produces major shifts in virtually every aspect of industry. Motive power is no exception, as it shifts further and further afield from the systems and technologies that have been used throughout much of its history.
While often overlooked in discussions of major industry trends, what’s transpiring in mobile fluid power has broad implications on where motive power might head next. That’s what led Power Progress to seek input from the following industry experts:
- Daniel Winter, president, Danfoss Power Solutions
- Corey Quinnell, vice president of Engineering, Husco
- Russ Schneidewind, director of Business Development, HydraForce
In part one of this two-part series, we look at the trends these experts are seeing within the markets they serve, what’s behind them and the impact these trends are having on the mobile fluid power sector and its customers. In part two, we’ll look more closely at the hurdles the sector is facing and how these and other suppliers are evolving to address these challenges now and into the foreseeable future.
Productivity and Reliability
The mobile fluid power industry closely follows what the mobile OEM industry is demanding, Schneidewind noted.
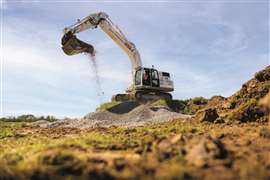
“If you look at off-highway mobile equipment, they’re trying to offer equipment that is more rugged and has longer uptime and availability so that you have machines that are readily available for a lot of applications,” he explained. “They’re also looking for increases in productivity. They want to be able to function faster with more accuracy, especially on, say, repetitive motion.
“This is driving a lot of different requirements from the mobile fluid power industry, and that includes a higher degree of integration with electronics and the hydraulics themselves.”
That demand for productivity and reliability plays a role regardless of machine size.
“As equipment becomes smaller, more powerful and more efficient, hydraulic components must deliver higher power density while minimizing energy losses,” said Quinnell. “This has led to innovations in hydraulic circuits, pumps and integrated electrohydraulic solutions – for example using sensors to eliminate\reduce mechanical part count\complexity – to maximize system efficiency.
“Many OEMs are looking to use larger displacement pumps with lower engine rpm to operate in a more fuel-efficient region of the diesel engine while keeping the same productivity,” he added.
Electronics and Software
Delivering on that productivity in the field has historically lay in the hands of the equipment operator. But a macrotrend affecting mobile machinery design, and in turn the subsystems on those machines, said Winter, is the skilled labor shortage.
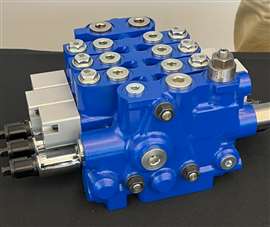
“It used to be the operator was mostly the ‘brains’ and the hydraulics were the ‘muscle.’ More and more so in the last, say, three to five years... it’s become the operator and the electronics are the brain and the hydraulics are the muscle,” Schneidewind commented. “So, in a move to address the uptime and availability aspect the OEMs are interested in, what we’re seeing is this need for more flexible systems.
“Electronics helps with that because you can have a similar hydraulic architecture and adjust the way the machine operates or feels based on the operator or the application by adjusting the electronics or the application software on the machine,” he said. “That allows for a machine to be more available in more applications, as well as more uptime in a lot of cases.”
Electronics and software are essential to enabling today’s modern control systems, Winter agreed. “We’re seeing more hydraulics with sophisticated electronic controls,” he stated. “In fact, today it’s rare to see new products designed with mechanical interfaces. Almost all our new product developments at Danfoss are designed solely for digital control.
“We, of course, still offer mechanical controls, but the advantage of digital only is you eliminate mechanical devices that add cost. We’re also starting to see more distributed architectures with component-level controls rather than centralized control.”
Move to More Automation
OEMs are being tasked to deliver solutions that fit the dynamics of a changing workforce, meaning an increasing level of automation is needed.
“You used to have a highly efficient operator who is a professional for that type of equipment. Now you find less and less of those skilled operators and you’re finding more generalists who may have to operate multiple types of machines,” Schneidewind pointed out. “Having that automation to assist is what the OEMs really desire for the increased productivity. The fluid power industry has to be able to respond to that.”
“There is a growing demand for autonomous and semi-autonomous machinery in agriculture, construction and material handling,” Quinnell said. “Ag and material handling are further ahead in this segment due to a more defined operation than the varied environments and tasks that construction equipment experience.”
Thus far in construction equipment, advances have largely consisted of what Schneidewind described as automation assistance for repetitive functions, such as return to dig or return to height for wheel loaders used in truck loading applications.
“It can be done faster and more accurately through an automated function where you just click a button after you set the limit, and then that bucket comes down fast to the position it’s needed while the operator is driving towards the pile,” he explained.
Enabling this type of semi-autonomous and even fully autonomous operation on a machine requires “high-power electronics, advanced software and the know-how to put it all together,” Winter stated.
“It’s no longer enough to be a component supplier,” he said. “You need to thoroughly understand the applications, and you need systems and software expertise.”
Sustainability Focus
A second macrotrend affecting mobile fluid power, said Winter, is sustainability. “Environmental stewardship and rising fuel costs are driving the demand for more efficient hydraulic systems,” he noted, “and accelerating the pace of electrification.”
OEMs are under pressure to reduce fuel consumption and emissions, said Quinnell, which requires hydraulic systems to become more efficient and integrated with alternative power sources.
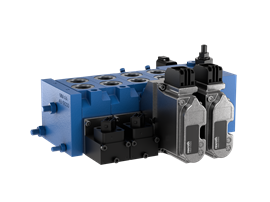
“The challenge lies in the fact that each OEM – and even different machine classes within the same OEM – adopts a unique strategy for improving machine efficiency and selecting alternative power sources,” he continued. “To remain competitive and support these diverse needs, Husco has developed flexible, modular valve platforms that can be tailored to align with each OEM’s specific strategy.”
Specific to electrification, Quinnell cited the growth in adoption of electrohydraulic and fully electric systems. “OEMs are integrating smart hydraulic controls, electrified actuators (on small and micro machines) and battery or hybrid powertrains to enhance fuel efficiency and reduce environmental impact.”
But even given this shift, he believes hydraulics will have a place. “While fully electric actuators are gaining traction in certain applications (mainly in small\micro machines) or specific functions on larger machines, hydraulics remain essential where high power density and force output are required,” said Quinnell.
“Hydraulic optimization is important for conventional machines, but also – maybe more so – for electric machines,” Winter asserted. “Take an excavator, for example. The hydraulic system wastes 70% of the useful power it receives. By slashing this figure, we improve machine runtime, perhaps we reduce the batteries needed in the machine, thereby reducing the cost and accelerating adoption of EVs.
“At Danfoss, we continue to develop more efficient hydraulic components and optimize existing components, but today the biggest efficiency lever is at the systems level. There are more variables in play, and we can optimize machine operation, and therefore power consumption, through software.”
Not Mutually Exclusive
Winter went on to state: “There’s a common misconception that hydraulics and electrics are mutually exclusive. In fact, they complement each other in many cases.
“For instance, while an electric propel system could replace a hydrostatic propel system, high-powered off-highway machines still rely on hydraulics for their robust, efficient power conversion. Electrics have replaced hydraulics in some lower power and rotary applications, but it’s difficult to replace linear hydraulic power with cost-effective, robust and compact electrified solutions.”
Driving Efficiency
The greatest impact Winter believes electrification is having is in the need for vast improvements in hydraulic system efficiency.
“In first-generation electric machines, OEMs tend to replace the internal combustion engine with an electric motor and batteries while leaving the hydraulic system largely the same. In many applications, this produces a machine with inadequate runtime. In other words, it cannot perform an entire day’s worth of work on a single charge,” Winter pointed out.

“For their second-generation machines, OEMs are focusing on optimizing hydraulics by considering alternative architectures and technologies such as gravity lowering, independent metering, zonal systems and energy recovery,” he continued. “At Danfoss, we’ve done several of our own machine conversions, including a wheel loader and a backhoe loader. We’re also working on an excavator. This has equipped us with the real-world experience to guide OEMs on their own journeys, not only how to electrify, but how to optimize the hydraulics.”
So, while Winter acknowledged electrics will take more share from hydraulics in the long term, he also believes hydraulics will in turn take share from mechanical solutions in some applications. “The demand for hydraulics will not fall off a cliff anytime soon,” he assured, “so those in the industry today should not worry.”
Efficiency is at the heart of Schneidewind’s argument, as well, when it comes to alternative power. “Regardless if electrification [is] the power system or diesel or hybrid or even hydrogen or others – methane as an example in the ag markets potentially – it really comes down to efficiency,” he stated. “There’s only so much power that you can have on the vehicle, as far as the space to carry that energy. So, the hydraulics have to become more efficient in how it utilizes the energy that’s available on that machine.”
New Architecture Needed
Schneidewind foresees this increased efficiency being achieved through new hydraulic architectures and systems. “It’s going to require lower pressure drop, advanced control techniques, the integration of more electronics and sensors,” he predicted. “That’s going to be the biggest challenge, I would say, for the industry – what do these systems look like, how do they get promoted and how does the customer integrate that new type of architecture into their machines?
“That’s going to be some of the biggest challenges, but it’s also an opportunity for those companies who can [provide] that sort of support for those customers, and can make those changes and demonstrate 25%, 30%, 40%, 45% efficiency gains,” Schneidewind continued. “There’s a lot of room in mobile fluid power and hydraulics to become more efficient.”
Companies Represented
Danfoss Power Solutions designs and manufactures a range of engineered components and systems that optimize the performance of mobile and industrial equipment. It offers full system solutions capabilities in hydraulics and electrification, as well as fluid conveyance, electronic controls and software. A comprehensive portfolio is available for industrial applications. Editron, its electrification division, focuses on off-highway applications such as construction equipment, harbor and airport equipment, mining and marine, plus has product offerings for on-highway applications such as buses and trucks.
Husco is a global developer and manufacturer of highly engineered hydraulic and electro-mechanical control solutions serving the automotive and off-highway industries. In the automotive sector, it specializes in electrohydraulic and mechatronic technologies that improve vehicle efficiency, including active valve control systems for internal combustion, hybrid and electric powertrains. For the off-highway market, the company provides advanced hydraulic control systems for construction, agriculture and material handling equipment.
HydraForce is a global designer and manufacturer of motion control systems, encompassing hydraulic cartridge valves, manifolds and electronic controls for a variety of off-highway industries, including farming, construction, marine, material handling, mining and forestry. The company was acquired by Bosch Rexroth, becoming a significant part of the Compact Hydraulics Business Unit. Bosch Rexroth and HydraForce combine their presence in complementary regions to provide comprehensive coverage in Europe and North America, while enabling growth in Asia.
Editor’s note: this story first appeared in the April 2025 issue of Power Progress. Watch for Part 2 of this series in a future issue of Power Progress.
POWER SOURCING GUIDE
The trusted reference and buyer’s guide for 83 years
The original “desktop search engine,” guiding nearly 10,000 users in more than 90 countries it is the primary reference for specifications and details on all the components that go into engine systems.
Visit Now
STAY CONNECTED



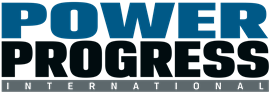
Receive the information you need when you need it through our world-leading magazines, newsletters and daily briefings.
CONNECT WITH THE TEAM
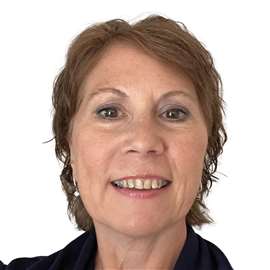
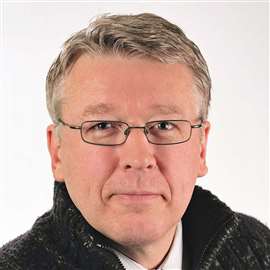
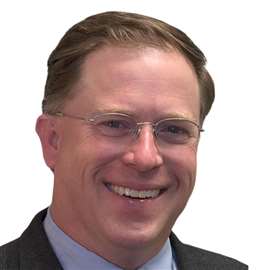
