Read this article in French German Italian Portuguese Spanish
Future-proofing test facilities
21 July 2025
Building with a modular approach helps create a more agile test environment.
The off-highway equipment industry is in constant flux, impacted by evolving regulations, consumer demands and technology. To stay competitive, original equipment manufacturers (OEMs) need to rethink their testing investments, focusing on flexibility and future proofing, rather than committing to a single solution.
In the latter part of the 20th century, test labs for on- and off-highway machinery centered around the combustion engine, with the expectation that their investments would last for decades. Today, that confidence no longer holds. Electrification, hybrid powertrains, alternative fuels and hybrid solutions mean OEMs need to address a range of propulsion technologies, often simultaneously, calling for more adaptable, modular testing facilities.
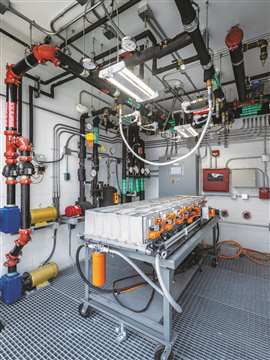
Navigating Change
The shift toward electrification has a significant impact on testing infrastructure requirements across the equipment sector. The transition encompasses multiple propulsion technologies simultaneously, creating complexity in testing needs. Engineers are required to focus on aspects such as battery chemistry, inverter logic and motor rotor positioning rather than traditional methods of measuring fuel consumption and emissions.
This change requires new testing methodologies and equipment. Similarly, alternative fuels and hybrid solutions present unique challenges incompatible with traditional internal combustion engine (ICE) approaches, demanding diverse testing requirements, no matter what solution OEMs choose to invest in.
Environmental and thermal testing is increasingly critical, as manufacturers must simulate extreme weather conditions for high-voltage battery or alternative fuel systems, where temperature and moisture sensitivity are crucial safety factors. Take, for instance, modern battery management systems (BMS), which are sophisticated electronic systems tasked with monitoring hundreds of cells and protecting batteries from damage. Validating BMS performance requires rigorous simulation across diverse operating conditions, demonstrating the scale of infrastructure needed to support electrification efforts.
Beyond Propulsion Tech
Propulsion technology is central to the development of off-highway equipment. Still, a wave of technological transformation is shaping future expectations of on- and off-highway vehicles. Artificial intelligence (AI) and automation can improve operational efficiency, while sites also integrate the Internet of Things (IoT) to track equipment and make it more efficient. Cloud computing is increasingly critical in testing environments to ensure the data acquisition process enables widespread measurement or control of all necessary testing and product data. This widespread digital transformation impacts every aspect of a testing facility.
The emergence of autonomous and software-defined vehicles invites new opportunities for manufacturers to advance their equipment to meet market demands. These advancements, however, introduce fundamental challenges to traditional testing approaches, including unpredictable software behavior and the need for systems that can keep working even after a failure. These challenges require testing methodologies to address probabilistic system behaviors, where passing a test once does not guarantee consistent performance.
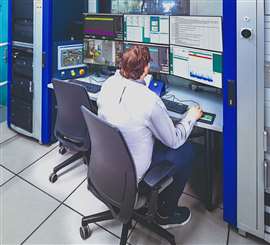
As the industry evolves, regulatory shifts and fluctuating consumer demands increase volatility and complicate testing facility planning. The industry faces increasingly stringent and fragmented regulatory demands, including tighter emissions standards for engines, such as those set by the U.S. EPA and the EU’s evolving battery and carbon footprint regulations. Compliance requires manufacturers to navigate lengthy permitting processes, adapt to region-specific laws and invest in advanced testing and documentation to meet requirements subject to frequent updates and regional variation. As a result, testing timeframes are more aggressive, putting pressure on OEMs to complete testing more quickly. This necessitates efficient and flexible testing.
To stay ahead, OEMs must prioritize flexibility and efficiency in test spaces. A modular approach accommodates higher channel counts, types of measurements and a wider variety of technologies.
Overcommitting testing infrastructure to a single propulsion solution, whether a traditional ICE or an upcoming battery system, poses significant risks in today’s rapidly evolving regulatory and technological landscape. Because of the uncertainty around which propulsion technologies will dominate, facilities designed for one technology can quickly become obsolete or require costly retrofits. Legacy engine test labs have had to invest millions to accommodate hydrogen or battery-electric testing. This inflexibility can leave manufacturers with stranded assets and the inability to respond quickly to changing customer demands or regulatory requirements.
Future-proofing test spaces with a modular approach helps establish a more agile environment that accounts for continued growth and evolution. A modular approach means designing testing facilities or systems using self-contained modules that can be combined, expanded or reconfigured to meet evolving requirements. Each module is structurally robust and environmentally controlled, capable of functioning independently or as part of a larger, integrated testing environment.
About the Author
As managing director at ACS Michigan, Chris Arnold spearheads business development and project execution for ACS initiatives in the Michigan area. Collaborating with engine and vehicle OEMs, tier suppliers and independent test labs, he specializes in tailored solutions. For information, visit www.acscm.com.
This approach is essential for modern vehicles that require comprehensive systems-level validation. Modular testing infrastructure can accommodate these integration requirements while maintaining flexibility to adapt as system architectures evolve. Designing facility space for growth, for example, allows the quick addition of new equipment with minimum rework of existing infrastructure. When further backed by a modular approach to software controls and data acquisition, adaptability for future needs is built into the design, engineering and manufacturing of vital construction equipment.
The more flexible OEMs are in their testing, the quicker they can adapt to direction changes in the industry. It’s imperative for the product development team, test engineers and facility designers to communicate frequently about the current facility requirements and future needs. This allows designers and builders to envision a facility that accounts for maximum flexibility.
Uncertainty an Opportunity
Investing in a testing facility is a 20-year-plus commitment. As such, it’s vital to design with adaptability in mind from the outset. OEMs that plan for regulatory unpredictability, market fragmentation and rapid technological change can reduce lifecycle costs and stay competitive. This approach requires robust infrastructure and a company culture that embraces uncertainty rather than resists it. Organizations ensure long-term success by making adaptability a strategic imperative in all stages.
Editor’s Note: this article originally appeared in the July 2025 issue of Power Progress.
POWER SOURCING GUIDE
The trusted reference and buyer’s guide for 83 years
The original “desktop search engine,” guiding nearly 10,000 users in more than 90 countries it is the primary reference for specifications and details on all the components that go into engine systems.
Visit Now
STAY CONNECTED



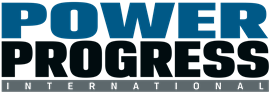
Receive the information you need when you need it through our world-leading magazines, newsletters and daily briefings.
CONNECT WITH THE TEAM
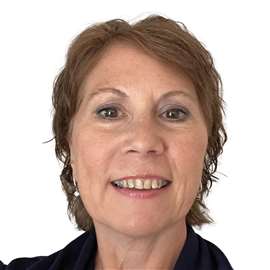
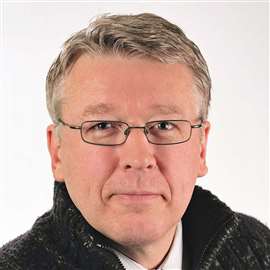
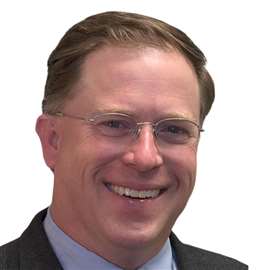
