Read this article in French German Italian Portuguese Spanish
Dintec: PDUs often underestimated mobile equipment components
03 December 2024
Systems integrator Dintec explains why it’s better to consider specifying the power distribution unit early in the design phase of a high-voltage system.
Let’s start with the basics, shall we?
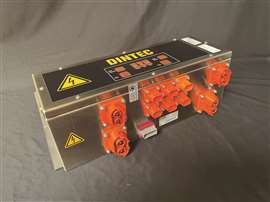
A power distribution unit (PDU) is the core of an electrified machine, distributing power between each of the components which make up the electrical system. In high-voltage (HV) systems, the role of the PDU is especially critical as these must be designed to safely and efficiently interconnect the components receiving the high-power direct current needed to bring the systems to life.
According to Michael Schmitt, managing director of Dintec, a German company which specialises in the development of electrical vehicle systems, there are some across the power industry which regard the PDU as just a box, without recognizing the complex and critical operations it represents.
“In designing a high-voltage system, you need to think about the system architecture,” he said. “Of course, when designing a machine you start with dimensioning the drives, calculating how much energy you need and consequently battery dimension, and so on. But at the same time – meaning at a very early stage – you need to consider building a safe and reliable architecture. And here is where PDUs play such a key role.”
Power Control
The PDU is the brain that manages, actuates and monitors power flow across the system. Primary tasks involve management of the HV current and ensuring there are no faults across the wider power unit.
-Michael Schmitt, Dintec.
Power distribution is the most fundamental job. This is carried out by inputs, connectors, cables, poles, etc. Within these, though, there are precise normative requirements and this is the first design hurdle. “In a medium-size electric mobile machine, the currents are 15 to 20 times higher than those we have in our homes. To handle such high currents there are a lot of parameters and safety requirements to consider,” explained Schmitt. “For example, temperature and even operating altitude can affect the design of a PDU.”
Another underestimated design aspect is space availability. In a working machine the space assigned for placement of the PDU is usually tight, meaning there will be a relatively small box handling high current and high voltage.
“Practically speaking, when you design the system you need to evaluate how the machine will be operated. But some aspects are not finalized by the OEM until later in the design process, which means the PDU cannot be fully specified until the final vehicle architecture is defined,” Schmitt said.
He continued: “Until the machine is structurally designed, you won’t be able to determine, for example, the layout of the cables. We have to remember here that we are talking about thick cables that cannot simply be bent in any direction at will.”
According to Schmitt, sensors are another hurdle: “Until the control strategy of the machine is defined, based on the operational modes, you won’t be able to determine which sensors will be needed and where they will be positioned.”
Trusted Partner
It’s important for OEMs to have an experienced partner when it comes to PDU design; the partner will effectively act as a guide which can direct the client through the full design phase, managing the process based on final agreed performance levels.
“After the initial evaluations and studies, the first step involves the relatively quick delivery of a PDU pilot prototype. In our experience, 100% of projects will need major changes as you get feedback after the installation of the prototype. From there you move along in the machine design.”
Dintec is currently involved with a manufacturer project covering design of a lightweight commercial vehicle for special transport services; the first PDU prototype has already been delivered. After some evaluation, it was determined that the box itself needed to be smaller, yet wider overall. While the project is still in the initial stages, Dintec has already had 10 major change requests – the capability to react quickly to these changes is critical.
Of course, cost is another major consideration and Schmitt explained that Dintec typically offers different technologies at various stages of the machine development process. “In the first phase we would use standard copper busbars; they are flexible in design and relatively easy to change but their installation is labour-intensive. Therefore, they are not a component you will use in serial production for high quantities, but they are great to get started with a prototype.”
Collaboration Lead
In addition to OEMs, Dintec can also be called on to collaborate with Tier 1 suppliers. One example could be where battery manufacturers expect their customer to need help with integration of the various electrical components and systems.
“This is a typical situation when more than one battery is used in the machine. With batteries working in parallel, you need a battery management system (BMS) and the PDU will work as the brain, integrating the BMS within the full electric system.”
Whether it’s an OEM or Tier supplier, the sharing of end goals and the choice of routes on how to achieve those targets is fundamental to making every step of the process timely and cost effective. That trust will invariably result in a final PDU design that meets the reliability and safety criteria required by the specific HV architecture.
Editor’s note: This article originally appeared in the Q4 2024 issue of Power Progress International.
POWER SOURCING GUIDE
The trusted reference and buyer’s guide for 83 years
The original “desktop search engine,” guiding nearly 10,000 users in more than 90 countries it is the primary reference for specifications and details on all the components that go into engine systems.
Visit Now
STAY CONNECTED



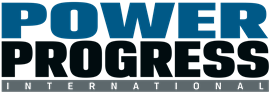
Receive the information you need when you need it through our world-leading magazines, newsletters and daily briefings.
CONNECT WITH THE TEAM
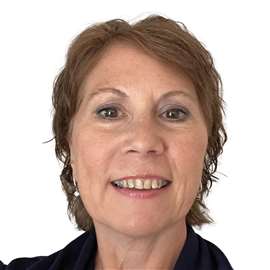
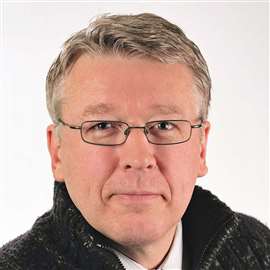
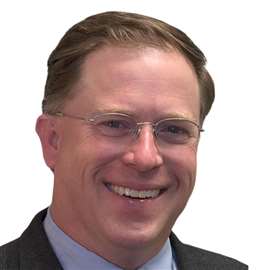
