Read this article in French German Italian Portuguese Spanish
State of on-highway electrification: More barriers to growth
12 August 2024
Charging infrastructure, supplier base needed to encourage Class 8 EV use
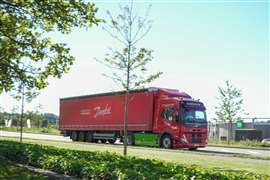
(Editor’s Note: In this final part of a series on the State of On-highway Electrification, we look at charging capability and cost, the supply chain for batteries and components and the prospect for efficiency gains in battery technology.)
The hesitation to invest in electric-powered, heavy-duty, on-highway vehicles stems from a number of factors, not the least of which is the ability to keep the vehicles charged and running over long distances. Charging infrastructure is currently nowhere near the level it needs to be for adoption to become practical for most long-haul applications.
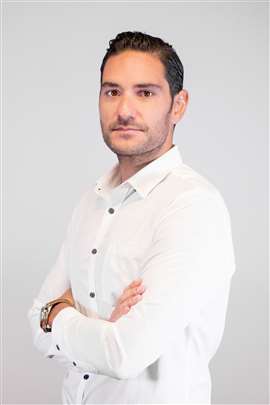
“Roland Berger came out with a report not too long ago saying that to fully electrify the U.S. trucking industry would cost about a trillion dollars. And that’s just charging infrastructure and utility infrastructure upgrades,” said Shaun Twomey, ZF’s Commercial Vehicle Solutions division. “That’s a huge number and, of course, the trucking industry doesn’t have a trillion dollars sitting around just to throw at it.”
“It’s really the limiting factor today, even in passenger cars,” said Eric Azeroual, vice president of On Highway for Danfoss Editron. “This is a new market. We need more charging infrastructure in place. It almost has to happen before [customers] buy the trucks just to know where they’re going to charge them.”
Charging capability and costs
Advances in battery technology will gradually make battery-powered heavy vehicles more affordable. However, as Azeroual noted, “it won’t necessarily move the needle until we can demonstrate to [owner-operators] and fleet operators where they’re going to be able to charge trucks and how much it’s going to cost to charge them.”
Electric school buses – which tend to return to a station or depot at the end of each shift – are currently leading the transition to commercial battery-electric vehicles (BEVs). But charging systems for these vehicles tend to be relatively simple – typically consisting of an onboard AC charger rated up to 19 kW and capable of charging a 200-kWh battery overnight at a relatively low cost.
The batteries required in a Class 8 on-highway vehicle are obviously larger, heavier and have a higher power draw in a much shorter time frame. “If you charge a truck and ask for 300 kW of power, there’s a surcharge for that peak power because you’re stressing the grid in a very short time,” Azeroual said. “We need to work on the electricity rates to make sure they are modulated so that it’s not more expensive to charge the truck than it is to fuel it.”
DC fast charging stations are necessary to get such large vehicles fully charged and back on the road as quickly as possible. Installation of such systems – which may require extensive modification to the electrical system in a plant, facility or depot, depending on the application – is where much of the added infrastructure cost comes in.
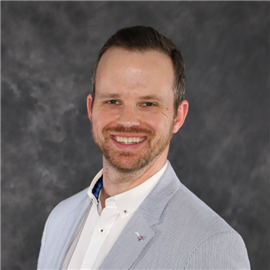
A study from the International Council on Clean Transportation estimated the cost of DC fast chargers at anywhere from about $28,000 to $140,000 installed, compared to a roughly $6,000 estimated installed cost for an AC charger.
Subsidies built into government legislation can help offset a portion of the cost of charging infrastructure. “The Bipartisan Infrastructure Law and other programs… are all at least in some part designed not necessarily just offset the cost of the truck to the fleet, but more holistically to build up the infrastructure,” Twomey noted.
While more subsidies need to be available and scaled to the application, it’s a starting point.
“Today, it’s really challenging to take a Class 8 BEV and drive from Dallas to Los Angeles the way that you can with an ICE (internal combustion engine),” said Twomey. “But as the infrastructure builds up, as it should with all the money that’s being thrown at it… these are all good signs that point in the right direction for improved future infrastructure capabilities.”
Localized supply
Another challenge to commercial EV adoption is the lack of a local or regional supply chain for batteries and the critical materials that go into their production. This adds cost and creates uncertainty for both fleets and the OEMs that supply them.
“China owns the supply chain. They have the highest capacity of battery manufacturing in the world; they have a huge supply of raw material,” Azeroual said. “So, the policies involved in the U.S., and the discussions between the U.S. and China are very important to the EV space.”
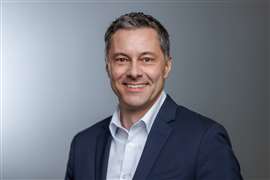
Thomas Heck, key account manager for heavy-duty customers in the Regions Americas at Schaeffler, said the U.S. is currently dependent on other countries to source batteries and other elements essential for electrification, but companies like Schaeffler are seeking to change that.
“System suppliers like us, we’re looking at our regional footprint and saying, ‘How can we expand here to make sure that we have a local supply chain for the critical components, for the critical raw materials that we would need’ – whether that’s for batteries or E-motors, magnets inside of E-motors, specialty steel for E motors and so on,” said Heck. “Building up that local or regional supply chain to reduce our dependencies on other countries is, I think, a very important factor to give the OEMs a certain confidence that… this is the right way to go.”
Azeroual believes the push toward BEVs in the passenger car industry will help to regionalize battery production more quickly. He noted that large companies like Ford and GM have already announced the start of battery production in North America.
“That’s definitely going to help because the trucking industry will piggyback on that,” he stated. “They’ll buy whatever is readily available, so that’s going to help in terms of driving down costs and accessibility to batteries.”
Efficiency gains
Advancements in battery technology are also expected to lower costs and improve operating efficiency for BEV fleets. Take solid-state batteries, as an example.
Currently, increasing power and range in an electric truck means adding more and heavier battery packs, with corresponding space constraints on the vehicle, reduced load capacity and higher TCO for the end user.
“Solid-state batteries provide higher power density, they are much lighter, they are safer when it comes to fire risks and things like that,” Heck pointed out. “We think that a lot of battery manufacturers will continue to develop in that direction, which of course will be a big benefit to the commercial trucking industry.”
ZF is encouraged by what it’s seeing not only in solid-state development but in battery technology as a whole. “For example, we know that solid-state batteries – and even subsequent technologies that will probably come online in the second half of this decade in big numbers – will help mitigate a certain amount of the range anxiety problem,” said Twomey, “because you can get more watt-hours out of that same size battery pack, and you can charge it faster when you do have to charge. These are critical improvements.
“In parallel, we certainly expect the infrastructure to get better because of the various incentives and programs that the government is setting up for the industry,” he continued. “All these things will align in such a way that make even heavy-duty electrified applications much more competitive in the future.”
Admittedly, there’s still a lot of work to be done – and still plenty of potential within existing technology before broader BEV adoption occurs.
“We’re not at the end with internal combustion technologies; there’s further optimization potential in there to reduce greenhouse gas emissions,” said Heck. “The transition to battery-electric cannot happen overnight. It will be a transition that happens over many years. I think the optimization of the current technology is just as important as being able to provide new technology for battery-electric vehicles.”
POWER SOURCING GUIDE
The trusted reference and buyer’s guide for 83 years
The original “desktop search engine,” guiding nearly 10,000 users in more than 90 countries it is the primary reference for specifications and details on all the components that go into engine systems.
Visit Now
STAY CONNECTED



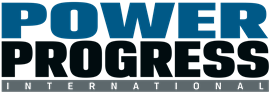
Receive the information you need when you need it through our world-leading magazines, newsletters and daily briefings.
CONNECT WITH THE TEAM
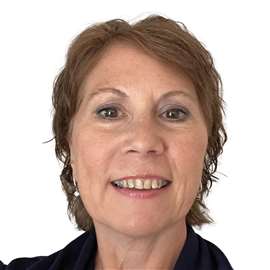
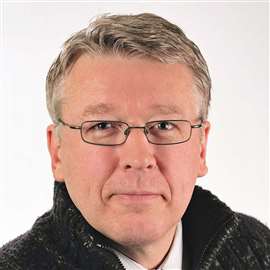
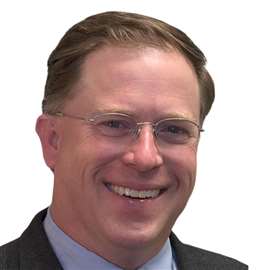
