Read this article in French German Italian Portuguese Spanish
Tula Tech tackles inefficiencies in diesel and electric vehicles and equipment
29 April 2025
The duty cycles for commercial vehicles and equipment vary widely depending upon the application. As such, machines can suffer efficiency losses in certain operational situations regardless of their motive power source — whether engine, electric or hybrid.
“When e-machines as well as combustion engines operate at low loads, which they very often do, those low-load operating points are relatively inefficient,” said John Fuerst, president and CEO of Tula Technology.
Addressing those challenges is Tula’s mission. The company provides controls for optimizing propulsion efficiency and emissions in mobility. Fuerst said that Tula was established in 2008 to advance its dynamic skip fire (DSF) concept: cylinder deactivation (CDA) on an individual cylinder basis. More recently, the company has implemented a related solution for electric vehicles: dynamic motor drive (DMD).
DSF for Diesel
CDA is hardly a new technology. While modern iterations can trace their history back to the mid-1970s and the oil crisis, a February 2018 article in Ohio’s Dayton Daily News identified the 1905 Sturtevant automobile as the first to use CDA. The driver could manually turn off three of the engine’s six cylinders.
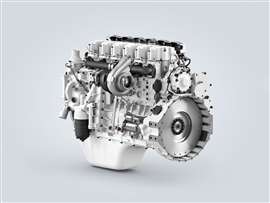
Many CDA approaches tend to group cylinders for deactivation. However, Tula’s DSF takes a different approach: deactivating cylinders individually.
“Dynamic skip fire says OK, I make all the cylinders deactivateable individually on demand and will only use the number of cylinder events that are required to deliver the requested torque by driver demand,” Fuerst said. It’s a patented approach that requires a combination of hardware and software.
While CDA in passenger vehicles tends to focus on fuel economy, when it comes to diesel engines for commercial vehicles, the benefit is in terms of emissions.
“In diesel applications, dynamic skip fire provides essentially a NOx (nitrogen oxides) reduction strategy with a minor fuel economy benefit, as well,” Fuerst said.
In 2021, Power Progress reported on research conducted by Tula and Cummins that showed a 74 percent drop in NOx emissions in the Cummins X15 diesel engine in low-load conditions. It was the first time Tula’s technology was applied to a diesel engine. There was a corresponding reduction in carbon dioxide (CO2) emissions, and fuel economy improved by 5 percent.
At the time, Fuerst said that maintaining exhaust temperature for NOx aftertreatment is often a challenge. Deactivating cylinders reduces excess air, meaning there is less to cool the exhaust. The result is warmer exhaust air for more efficient selective catalytic reduction (SCR), resulting in significant NOx reductions.
Tula also joined forces with Liebherr in 2022 to investigate the impact DSF could have on heavy-duty off-highway equipment. Using Liebherr’s 13.6L D966 engine, the study revealed a NOx reduction of 41 percent and a CO2 drop of 9.5 percent.
Addressing Electrification
According to Fuerst, industry changes that are somewhat moving away from internal combustion and toward electrification necessitated a new approach to the company’s technology.
“By 2018, we realized that there was an opportunity in electrification and in electric vehicles in general — an opportunity to use a strategy similar to DSF in electric machine drive systems,” he said. The result was DMD, which he described as a method to “tease out a little bit more efficiency” in electric vehicles, on the order of 0.5 to 2 percent.
Fuerst explained that DMD technology works best when a vehicle is operating between no-load and its point of peak efficiency.
“What our strategy does is, instead of operating in a steady state at that low efficiency point, we pulse up closer to the peak efficiency,” he said. “We deliver that lower efficiency on average, but with pulses of high efficiency.”
Fuerst continued, “It’s essentially shifting the [peak] efficiency point downward and putting higher efficiency at lower torque demands.”
DMD also applies to regenerative braking, something Fuerst said “can save electricity coming and going, as some people might say.”
Unlike the split fire technology, DMD does not require any hardware.
“The strategy is purely software,” Fuerst said. “The benefit granted is smaller, but in terms of benefit per dollar spent, it’s very competitive with DSF.”
That’s not to say that hardware adjustments cannot enhance the benefits of DMD.
“There are some hardware changes that make DMD more effective,” Fuerst said. “Right now, we think the best approach to the market is to say here are the benefits if you don’t make any hardware changes, and if you make some hardware changes, you might get a little more.”
One unique benefit of DMD as a software-only solution is its flexibility in deployment.
“It’s pure software, which means you can implement it on a vehicle that’s in production,” Fuerst said. “It can be a running change. We’ve talked to a couple companies already about implementing DMD as a running change in a current design, which means what they’re going to do is change what they flash into their controller.”
Commercial Applications
Fuerst said that commercial trucking can experience benefits from Tula’s technology, but not necessarily the long-haul variety.

“Trucking, there is an opportunity there, as well, but it’s probably more medium-duty type delivery where you’ve got a significant amount of operating empty,” he said.
Fuerst added that outside of delivery vehicles, applications such as cement trucks that run empty when returning to the plant are also possibilities.
“Buses that do need to push away briskly from the bus stop, but then, in the middle, they’re just easing along, there’s opportunity there,” he added. “It’s as we love to say very application-specific.”
According to Fuerst, there’s “no doubt” DMD can be applied to heavier-duty commercial applications, but it’s going to take a bit more time.
“We have had some commercial vehicle discussions and we’ve done some simulations that have caused [OEMs] to say yes, it could be DMD in our future,” Fuerst said. “Commercial trucks are engineered further in advance than passenger cars. There’s a little bit longer lead time for technology change.”
POWER SOURCING GUIDE
The trusted reference and buyer’s guide for 83 years
The original “desktop search engine,” guiding nearly 10,000 users in more than 90 countries it is the primary reference for specifications and details on all the components that go into engine systems.
Visit Now
STAY CONNECTED



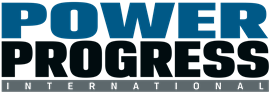
Receive the information you need when you need it through our world-leading magazines, newsletters and daily briefings.
CONNECT WITH THE TEAM
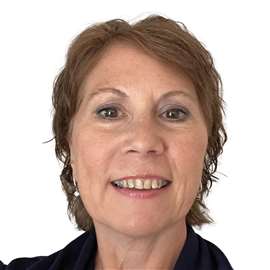
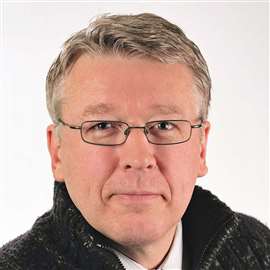
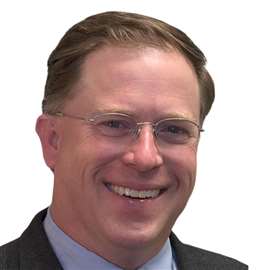
