Read this article in French German Italian Portuguese Spanish
Safety and performance in high-voltage batteries
13 January 2025
Flash Battery offers insight into high-voltage batteries, what they are, suitable applications and the components that help protect operators and maintenance personnel.
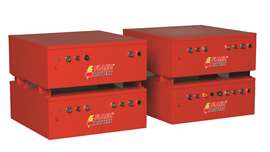
The growing share of electrified models in the industrial vehicle market now extends to larger machines with higher power. Delivering the increased power demand of models in this segment has been supported by a series of technology advances in lithium batteries and in particular high-voltage lithium batteries.
The What and the Why
Looking at industrial and off-highway applications, low-voltage batteries are commonly defined as units up to 102.4 V nominal. This, despite regulations defining low-voltage batteries as 60 V. High-voltage batteries start from 300 V and can deliver in excess of 800 V.
Flash Battery explained that the cost of a low-voltage battery is less than a high-voltage solution because the components in the low-voltage models are easy to source and do not need the uprated components required to handle higher currents, such as dedicated connectors or safety devices.
A low-voltage solution, though, simply cannot be adapted for use in a high-power system. This is due in large part to the output power of the electric motor, which has a direct influence on the choice of voltage; in industrial and off-highway applications, motors above 20 or 30 kW need a higher voltage to be compact and operate efficiently.
Flash Battery said that some OEMs are still skeptical when it comes to high-voltage solutions, often because they are concerned of the safety aspects. But it is important to underline how high-voltage batteries require stringent safety measures and protocols to ensure both operator safety and system reliability.
The How
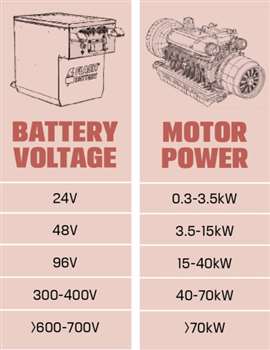
Flash Battery recently developed a 396.8 V 420 Ah battery (166.6 kWh) for a hybrid tracked crane. Given the high power demand, the solution required four battery packs in a series configuration, but separated into two different areas of the frame. The system included an integrated control system using an insulated high-voltage interlock system (HVIL) to meet the safety standards required by high-voltage applications. The project required a mechanical study for the positioning of the batteries within the vehicle frame.
The project was based on three key pillars: chemistry, smart assembly and advanced proprietary control electronics.
Battery Packs
According to Flash Battery, lithium ferrophosphate (LFP) cell chemistry is now considered the best choice for industrial applications, both for its efficiency and safety. Additionally, LFP has a long life – over 4,000 charge cycles – while also being the most stable chemistry currently available.
Battery cell assembly is another important safety aspect. Of particular concern is the cell capacity and consequently the number of cells connected in parallel within a battery pack.
Using smaller battery cells inevitably requires more parallel connections within the pack to reach the requested capacity, but increasing the number of connections raises the risk of a short circuit. Packs produced by Flash Battery use no more than four cells in parallel: tests have shown that the design delivers the safest solution.
Component Roll Call
There are other components which play a fundamental safety role in a high-voltage battery pack. These include fuses to interrupt the current if overcharging or a short circuit is detected, together with contactors which can break the circuit and limit damage to the system components.
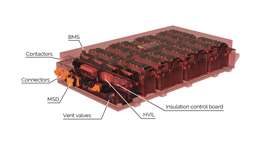
In addition, the high-voltage interlock system utilizes a continuous low-voltage circuit to monitor the correct connection of all high-voltage components across the vehicle. If the HVIL signal is interrupted, the high-voltage current is immediately interrupted.
Where all these are automated systems, the mechanical safety disconnect (MSD) is a manual device activated during maintenance operations to physically disconnect the circuit. It also acts as an additional layer of security in an emergency.
On top of all these elements, a package of intelligent control electronics is essential to provide complete and continuous control of the battery pack. This helps to ensure stable performance as the pack goes through its lifetime of charge/discharge cycles.
A key part of this is the BMS, which continuously monitors the temperature and voltage of each battery cell and initiates the required protocol should there be a safety issue. Such is the importance of the BMS that Flash Battery developed its proprietary BMS, the Flash Balancing System.
Flash Battery also operates its Flash Data Center, a remote system that utilizes the processing power of the cloud, machine learning and AI technology to collect and analyze real-time data from Flash Battery products operating around the world. Analysis of this data supports predictive maintenance for better longevity.
The Flash Data Center was one of the finalists in Control System/Monitoring Solution of the Year category at the Power Progress Summit 2024.
Editor’s note: this story first appeared in the October - December 2024 issue of Power Progress International.
POWER SOURCING GUIDE
The trusted reference and buyer’s guide for 83 years
The original “desktop search engine,” guiding nearly 10,000 users in more than 90 countries it is the primary reference for specifications and details on all the components that go into engine systems.
Visit Now
STAY CONNECTED



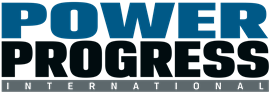
Receive the information you need when you need it through our world-leading magazines, newsletters and daily briefings.
CONNECT WITH THE TEAM
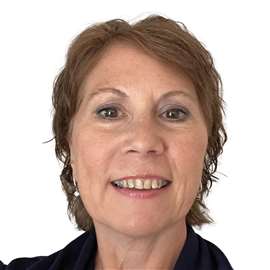
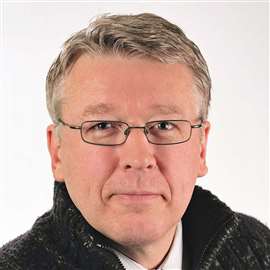
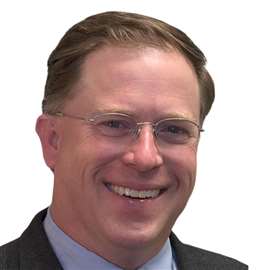
