Cummins talks remanufacturing at ETF webinar
01 May 2025
While electrification is undoubtedly a trend in mobility, internal combustion (IC) engines continue their broad use across a variety of applications.
In his opening remarks at the recent Engine Technology Forum (ETF) webinar about the role engine and component remanufacturing can play in the circular economy, Allen Schaeffer, ETF executive director, described IC engines as part of the energy future.
“We know that they have increasing efficiency,” Schaeffer said. “They achieve near-zero emissions. They’re able to use renewable and low-carbon fuel capabilities.”
One additional advantage they offer is their ability to be remanufactured, and thus reused, extending their useful life.
“These engines last a long time, and that’s a high value,” Schaeffer said.
Three-Phase Process
One engine maker that has been taking advantage of remanufacturing for decades is Cummins.
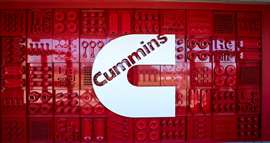
“Cummins’ involvement in remanufacturing actually began in the late ‘50s, and it was in response to technical fuel and service problems with fuel systems and air compressor components,” said Patricia Covington, executive director for Cummins’ ReCon manufacturing business.
On the Cummins ReCon website, the company said that as much as 85 percent of an engine can be remanufactured — not just once, but multiple times.
According to Covington, Cummins focuses on providing remanufactured components and engines that deliver like-new performance. The company also seeks to address sustainability, both for the customer and itself.
You would think Cummins’ ReCon process would begin with an engine or component that has come to the end of its useful life. However, it’s a process that occurs in three phases, which collectively often span decades.
For instance, there is the phase immediately after the launch of a new product — the “growth” phase — during which Cummins will begin collecting cores.
“One of the most critical elements is what we call the core,” Covington said, referring to the component itself. “It is essentially the ‘dirty product.’ So once that repair cycle starts and that product has reached the end of its useful life, we want that dirty core back. That dirty core is the most important element.”
Collecting cores at this stage is critical, Covington said, so that the company can begin “banking” them.
“When we actually start the remanufacturing process, we [need] enough to make sure that we [have] at least 50 percent usage for whatever that component or engine may be, so that we can offer the customers that price point that they prefer,” Covington said.
Remanufacturing actually begins after the company has collected a sufficient number of cores. According to Covington, this can be as soon as 12 months, but the actual timing depends upon core availability.
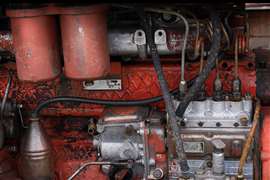
“That reman process often starts before the end of the new production,” she said. “In the example of an engine, new engines and reman engines can be manufactured at the same time.”
In the second “mature” phase, Cummins will see cores being returned at a normal rate.
“The new engine platform may cease to exist and go on to a better engine or newer engine, and we will still have the ability to offer those customers the repair parts and the whole reman engine for a period of time,” Covington said. This phase could last as long as 20 or more years, depending upon the product and how often it can be remanufactured.
Finally, there is the “declining” phase of the product in which remanufacturing is no longer possible.
“That is when we will start to see the core return from the field at higher rates than expected, and that is when we start to think about getting that product out of the remanufacturing cycle, thus ending the lifecycle for that specific product,” Covington said.
Like-New Product
When it comes to collecting cores, Cummins uses reverse logistics — a process designed to make it easy for the customer to return the product. Once acquired, the core is disassembled, cleaned and entered into the salvaging process.
“Our engineers are always happy to work in the remanufacturing space, because for many of them, it is a playground to think about the different salvage technologies that are required depending on what the component is,” Covington said.
After reassembly, Cummins performs the same kind of inspection and testing that it would apply to a new product before it is sold to customers.
“It is like new,” Covington said. “So, same quality standards, same expectation as new.”
Supply Chain Mitigation
For Cummins, the remanufacturing process has helped the company address supply chain risks. As an example, Covington hearkened back to the COVID-19 pandemic, which had a dramatic impact on supply chains globally.
“A lot of our suppliers were significantly constrained,” she said. “So, it gave us an opportunity to then think about even some products that we were not remanufacturing or did not have plans to remanufacture as soon as expected, but we were able to quickly get the product into the remanufacturing process and offset.”
Covington added that remanufacturing provides Cummins the ability to offset any supply chain disruption, “whether that is external supplier capacity for new components or our own internal manufacturing capacity.”
Remanufacturing offers other benefits, as well. Covington noted that ReCon products have a shorter lead time than their new counterparts. They tend to be more cost-effective. Additionally, they require less raw materials.
Again, back to the environment,” Covington said. “We want to make sure that we’re always doing the right thing. So, as much as we can remanufacture, the better [it is] for the environment, because we are not relying as much on the raw material.”
There are also benefits to Cummins in terms of providing options to customers navigating their own supply chain uncertainties.
“It gives us an opportunity to offer to our customers an alternative option to new, and through that opportunity, we’ve built really strong relationships with customers and helping them understand how to provide options for their end user customers and have sustainable supply chains,” Covington said.
POWER SOURCING GUIDE
The trusted reference and buyer’s guide for 83 years
The original “desktop search engine,” guiding nearly 10,000 users in more than 90 countries it is the primary reference for specifications and details on all the components that go into engine systems.
Visit Now
STAY CONNECTED



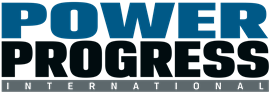
Receive the information you need when you need it through our world-leading magazines, newsletters and daily briefings.
CONNECT WITH THE TEAM
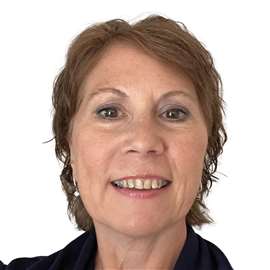
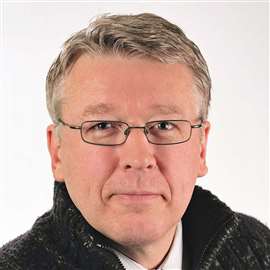
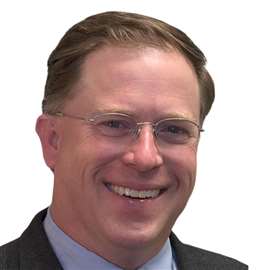
