Fortescue strives to drive real zero for all in mining
25 February 2025
The company is working to achieve ambitious goals and help partners in the process.
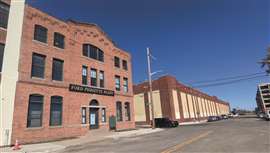
Fortescue, a diversified metals, energy, and green technology company, has placed a laser focus on achieving Real Zero across all of its Australian iron ore operations by 2030 – a full 20 years before the industry norm. To get there, the fourth largest iron ore miner in the world has brought much of the required technology and expertise in-house in such a manner that it’s poised to help partners in a number of markets also reach their zero-carbon targets – not only in mining nor only in Australia.
“In 2030, we believe Fortescue will be the go-to company for green metals, technology, energy and energy storage globally,” said Fortescue Metals CEO Dino Otranto during the MinExpo International event in 2024. “When the world needs the ‘how’ to be answered, it will turn to Fortescue.”
Fortescue in Las Vegas
To that effect, the Perth, Australia-based company has made several key moves that it announced during the mining equipment show at the Las Vegas Convention Center.
In what was perhaps the biggest news, at least in terms of dollars and tonnage, Liebherr and Fortescue expanded their partnership and showed a jointly developed autonomous battery-electric T 264 haul truck. The two companies will develop and validate a range of zero-emission solutions that is expected to result in the supply of 475 new Liebherr machines to Fortescue’s mining operations in Western Australia; the number was said to represent about two-thirds of the current mining fleet at Fortescue’s operations. The total value of the partnership, comprised of the supply of machines by Liebherr and the battery power systems by Fortescue Zero, is around $2.8 billion.
Fortescue also developed a stationary fast charging solution to provide 6 MW of power to reportedly charge the current battery-electric T 264 in 30 minutes.
Of the 475 machines that make up the deal, about 360 will be autonomous battery-electric Liebherr T 264 trucks and will use battery-electric power from Fortescue Zero.
The long-term goal is for each truck in the fleet to ultimately be equipped with the same system as well as the Autonomous Haulage Solution (AHS) that it jointly developed with Liebherr. Both can be retrofitted onto existing Liebherr haul trucks.
Such partnerships are critical, said Dr. Andrew Forrest, executive chairman of Fortescue and the driving force behind the mining giant’s targets and the tools it is putting in place to meet them.
“This is an important next step in our 2030 Real Zero target – to eliminate emissions from our Australian iron ore operations by the end of the decade. The world needs Real Zero now – it simply cannot afford to wait,” said Forrest. “The green solutions we need are here today, and Fortescue Zero is supplying them and rolling them out across our massive mining operations. Fortescue Zero developed this battery technology and jointly developed the Automated Haulage Solution, leading the way to provide green innovative solutions to eliminate emissions from heavy industry. We invite all companies in the mining, heavy industry and haulage sectors to join us. We can together be the trailblazers who forge the world’s move away from fossil fuels.”
The company has said the fully integrated AHS will be a “game changer” for reducing carbon emissions, and that it is based on the experience it has gleaned from more than 200 autonomous trucks.
Also at the mining event, MacLean Engineering said it will deliver 30 GR8 EV graders to Fortescue’s mining operations, each powered by a Fortescue Zero battery system. The first grader is expected to be delivered in 2026, with the full fleet expected to be operational in 2029. Above-ground mining machines represent some diversification for the Canadian mining equipment OEM, as it has supplied utility equipment for underground mines for years.
Fortescue Zero in Detroit
Fortescue Zero was Williams Advanced Engineering (WAE), a UK-based specialist in electrification and a battery supplier to electric racing series and other high-performance applications.
When Fortescue purchased the company in 2022 for $232 million, it said it was a strategic move toward zero-emission technologies for heavy industry, and that it would build on the firm’s expertise in motorsports, tapping solutions created under stringent performance requirements and tight timelines. The investment by its parent company has permitted the firm to staff up as it continues to develop zero-emissions technology for Fortescue, as well as other customers in marine, rail, heavy-duty off- and on-highway equipment and passenger vehicles.
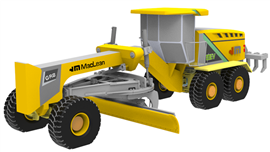
“We’re removing emissions by 2030, and that’s not net zero. It’s Real Zero,” said Andrew Carlisle, managing director, Mobility, Fortescue Zero. “In many ways, we are backing ourselves to deliver electrification solutions to our mining operations, which are worth tens of billion dollars a year in terms of revenue. It has to work in those applications. And from a financial stability standpoint we’ve now got very strong backing and support.
“When it comes to making a difference, I think companies will naturally want to create cleaner solutions, but because of their relative size many OEMs don’t have the necessary factory or engineering capabilities in-house. They rely on partners to deliver that because it’s fundamentally different from what they know. That’s where the 15 years of experience we’ve got doing electrification makes me proud. We’ve got the ability to provide these customized solutions quickly with standard building blocks.”
The day before The Battery Show kicked off in downtown Detroit in October 2024, Fortescue Zero employees and guests took a field trip to the city’s Milwaukee Junction neighborhood, considered the epicenter of America’s automotive heritage. Home to Henry Ford’s first Ford Model T automobile factory (now a museum), the neighborhood will soon be the location of Fortescue Zero’s U.S. Advanced Manufacturing Center.
The center is expected to become a production hub for automotive, marine and heavy industry batteries, fast chargers and other green technology. The company’s Scalable Battery Module (SBM) technology is expected to be the first component to come online in Detroit in Q4 2025.
Editor’s Note: This story first appeared in the January-February 2025 issue of Power Progress.
POWER SOURCING GUIDE
The trusted reference and buyer’s guide for 83 years
The original “desktop search engine,” guiding nearly 10,000 users in more than 90 countries it is the primary reference for specifications and details on all the components that go into engine systems.
Visit Now
STAY CONNECTED



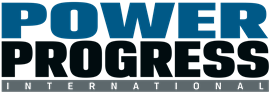
Receive the information you need when you need it through our world-leading magazines, newsletters and daily briefings.
CONNECT WITH THE TEAM
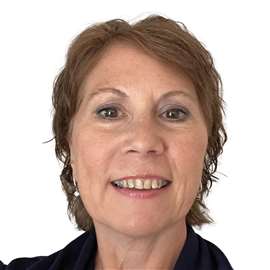
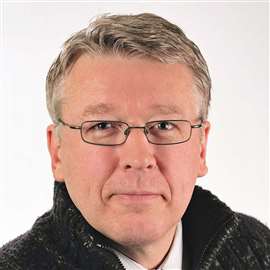
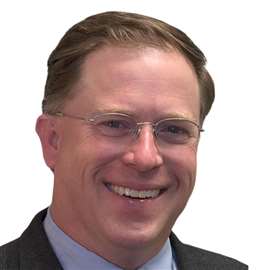
