Getting It Up And Running
25 April 2017
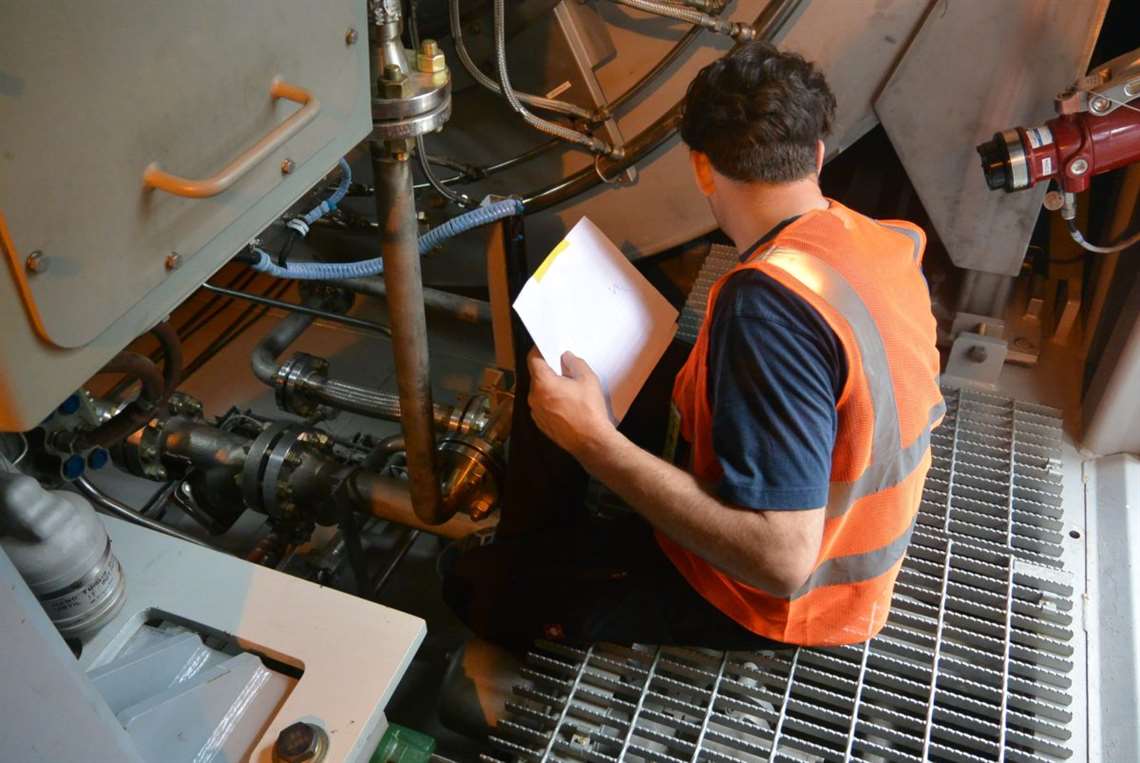
If there are words power plant operators don’t ever want to hear, it’s these: “We’re running behind schedule and we’re losing money every day.”
Yet that was the message that engineers at the Avion natural-gas fired power plant in the Philippines, had to give to their senior management last year.
The 97 MW Avion plant, located within the First Gen Clean Energy Complex in Barangay Bolbok, Batangas City, is the first plant in the Philippines to apply aero-derivative turbine technology, using GE’s LM6000PC turbines derived from the CF6-80C2 engines usually found on widebody aircraft. The turbines can operate on both natural gas or liquid fuel and Avion is the latest addition to First Gen’s portfolio of clean power generation plants, which comprise, gas, geothermal, hydro, wind and solar power generation technologies.
The First Gen plants provide a total of almost 3500 MW of capacity — approximately 30% of the Philippines’ gross power generation requirements — and the Avion facility with its 97 MW was certified as a fast-start, peak load generator that can immediately supply electricity during hours when power demand surges and there is a supply shortage to the grid. Avion was also designed for the flexibility to start and stop multiple times a day.
But all of that seemed unlikely when plant installation and commissioning efforts had come to a standstill and the original installation contractor was no longer able to complete the work. The only option at that point was for the plant operators to find a different service provider. And into the breach stepped MTU Maintenance.

One of the world’s largest independent providers of commercial engine maintenance, repair and overhaul (MRO) services in terms of sales, MTU Maintenance specializes in maintenance and repair solutions for a wide variety of different engine types, including the LM series industrial gas turbine.
Within days of being called upon, an MTU Maintenance team arrived onsite, with the aim of getting the plant up and running as quickly — and safely — as possible. The process involved establishing the status of completion and commissioning of each unit, rectifying issues found, performing alignment and analysis and ultimately completing the works to enable the two LM6000PC dual fuel turbines to be successfully commissioned.
Avion was able to begin commercial operation on fuel gas in September of 2016 and then on liquid fuel in December 2016. Within six weeks of MTU arriving onsite, the plant was synchronized to the network and was generating energy into the Philippine grid.
In all, MTU Maintenance completed the entire job, which included further commissioning and testing after the plant began initial operation, in a total of 16 weeks.
As MTU Maintenance was not involved in the initial turbine installation work, the international and interdisciplinary team went back and checked every nut, bolt and component from scratch. Everything from the turbine, generator, various operating systems to the control the enclosures, tubing and connections was checked to make sure the final installation would meet with MTU’s internal engineering standards.
This thoroughness was appreciated by Colin J.D. Fleming, senior vice president, First Gen Corp. “It was great to be able to rely on the team’s professionalism, their strict application of process and procedure, and of course, the technical skills needed to get the job done,” Fleming said.
Issues that were found during the rigorous inspection process included tightening loose flanges, exchanging carbon filters that had been damaged by heavy rain, reconnecting mixed-up wiring and recalibration of valves and instrumentation. The MTU Maintenance team also carried out turbine alignment, vibration analysis, troubleshooting and performance optimization during test runs and the first hours of operation.

As the name implies, peak load generators are used to support the grid at times of peak demand, to compensate for fluctuations in the grid caused by renewables, or perhaps even as an emergency supply option during extreme conditions, such as typhoons. Aero-derivative turbines are often used as peak load generators because of their fast start-up, stop and response times – the LM6000PC for instance, can start up and achieve full load in less than 15 minutes. Furthermore, because of their advanced material construction and high compression ratios, aero-derivative turbines are generally more efficient than industrial gas turbines and offer fuel flexibility, as exemplified in the Avion plant.
While aero-derivative turbines are well-suited to peak load applications, this type of duty cycle can require more in the way of maintenance than typical baseload operations. MTU Maintenance has observed that components in turbines used in peak operation are more likely to exhibit signs of thermal distress and material fatigue. Fluctuating loads can also lead to disproportional pressure ratios between seal air and sump air, which can result in small oil leakages, deposit buildups or even damage to bearings. There can often be more wear on rotating seals, honeycombs and stationary seals.
Understanding those issues has allowed MTU Maintenance to develop plans and strategies to address them, which is part of the service the company offers to its customers.
Now that the Avion plant is operational, MTU Maintenance will be assisting plant operators through the next year and have supplied a resident engineer to the site. “MTU Maintenance is always looking for solutions to help us manage our plant to the best of its capability,” said Mark Alexander Bruce, Avion power plant manager. “Looking forward, I know we are in good hands.”
Click here for more information on MTU Maintenance.
POWER SOURCING GUIDE
The trusted reference and buyer’s guide for 83 years
The original “desktop search engine,” guiding nearly 10,000 users in more than 90 countries it is the primary reference for specifications and details on all the components that go into engine systems.
Visit Now
STAY CONNECTED



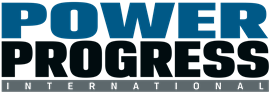
Receive the information you need when you need it through our world-leading magazines, newsletters and daily briefings.
CONNECT WITH THE TEAM
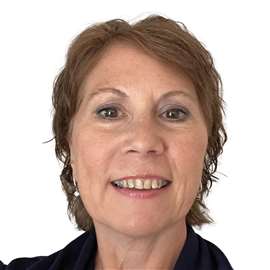
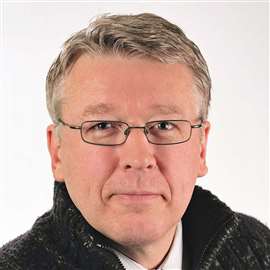
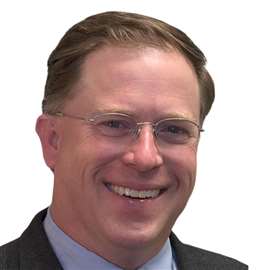
