Read this article in French German Italian Portuguese Spanish
Stapleton: battery gigafactories not always the right choice
15 July 2025
When it comes to making batteries for battery-electric (BE) vehicles and equipment, there are factories, and there are gigafactories. The latter, as the name suggests, are massive facilities designed to produce multiple gigawatt-hours (GWh) of batteries per year, often of the lithium-ion variety.
Modern gigafactories can exceed 100 GWh of output each year, with much of that capacity destined to supply the fast-growing EV sector.
In the U.S., some examples include Tesla’s Gigafactory Nevada and Ford’s BlueOval City in Tennessee. Sweden’s Northvolt Ett and CATL’s gigafactory in Germany are among Europe’s largest manufacturing sites.
Not Always a Fit
“Gigafactories are important,” said Alex Stapleton, chief commercial officer of Alexander Battery Technologies, a UK-based maker of custom battery packs for OEMs. “They are a big indicator of where investment is going, where the cash is flowing, where the projects are going to be happening.”
However, Stapleton said that the scale they provide isn’t necessarily appropriate for many commercial equipment and vehicle OEMs.
“If you’re talking about Tier 1 automotive or something, then absolutely those guys are well set up and that’s what they look to do,” he said. “But those are projects that go over years. They think, let’s start some production in 2030 or something, and they all start planning around it.”
For OEMs producing 1,000 to 5,000 vehicles per year, though — especially given their often six-figure price tags — the gigafactory model often isn’t appropriate.
“It means locking into specific cell formats, locking into production schedules and long-term programs,” Stapleton said. “That probably increases the risk.”
Flexibility, Customization Matter
Commercial equipment and vehicle OEMs also have unique needs that a gigafactory cannot effectively address.
“Often they require more flexibility, more customization, faster turnaround,” Stapleton said, “an easier runway, I would say, into their projects than that kind of gigafactory model allows.”
He added, “I think the gigafactory model really supports the supply side and doesn’t really touch deeply on the demand side, where there’s actually value in support. These companies need serious engineering support without the overhead, without the scale forecasts that come with those automotive programs.”
The Bespoke Advantage
That is what Stapleton said is driving many OEMs to consider bespoke batteries for their equipment. For electrified equipment and vehicles, there are few components as critical as the battery.
“Taking the time and care to work on that battery, it almost certainly provides value to your end customer,” he said.
Stapleton added, “With smaller volume applications, I think there’s a growth there because people want to access that differentiation.
Clear Process
For OEMs looking to develop batteries for their products, Alexander Battery Technologies has developed a robust process intended to help customers navigate the challenges.
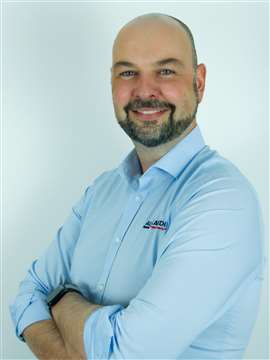
“The wireless earbud is very different to the vehicle, [but] the principles stay the same,” Stapleton said. “We have a very tight stage-gated engineering process.”
He explained that the first order of business is collaboratively developing a scope of work.
“That essentially drives a level of documentation at the start of the project where we have all the customer’s inputs and their target spec and what they’re trying to achieve,” Stapleton said. “Then we run that through things like regulatory considerations and compliance and everything else that has to go into that melting pot.”
According to Stapleton, the documentation phase for vehicle and equipment batteries can be time-consuming.
“If it’s from scratch, 18 months to two years is not unrealistic when it comes to documentation,” he said. “Because there are huge topics — like functional safety is a really big topic when it comes to these kinds of battery packs — and the documentation demands for functional safety are extremely high.”
While Stapleton said the documentation is the hardest part of the process, the result is a list of deliverables that address key milestones and metrics.
“They get a very transparent kick-off where we have our whole team there,” Stapleton said. “They get to meet everybody that’s working on the project at the front end, and they get that documented to know who everybody is.”
Repeatability vs. Novelty
Given Alexander Battery Technologies’ work in bespoke batteries for vehicles, Stapleton said that sometimes the documentation process can be streamlined via their previous experience.
“There’s a throughline in those battery packs which you can say it’s probably going to be modular, it’s going to want CANbus, it’s going to want thermal management,” he said. “There are definitely things that will be somewhere repeatable.”
However, there are novel aspects of batteries that cannot be predicted.
“We’ve been picking up new things with new chemistries — battery packs with things like lithium-titanate oxide,” Stapleton said. “We recently did an eVTOL — a vertical take-off and landing — definitely new stuff. So, the process has to be designed to answer the question, ‘How do you design something right every time when it’s the first time?’ That’s not an easy answer.”
Policy Support Needed
Stapleton said he hopes that policies around the world will give more consideration to those battery suppliers that fall outside of the gigafactory model.
“There’s kind of this middle class of design and batteries and OEM and everything else, which runs to the billions — it’s not a small industry — that needs to have policy focused on it, as well,” he said. “Not just policy at the gigafactory level.”
Stapleton reiterated the value that smaller battery suppliers can offer.
“There has to be the support at the ground-level support for the innovation, as well,” he said, “and I think that makes both sides more viable.”
POWER SOURCING GUIDE
The trusted reference and buyer’s guide for 83 years
The original “desktop search engine,” guiding nearly 10,000 users in more than 90 countries it is the primary reference for specifications and details on all the components that go into engine systems.
Visit Now
STAY CONNECTED



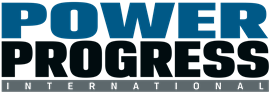
Receive the information you need when you need it through our world-leading magazines, newsletters and daily briefings.
CONNECT WITH THE TEAM
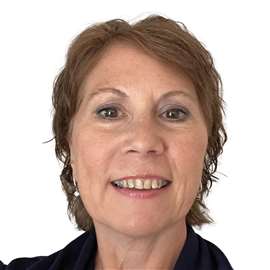
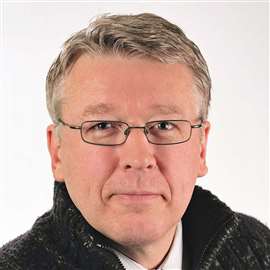
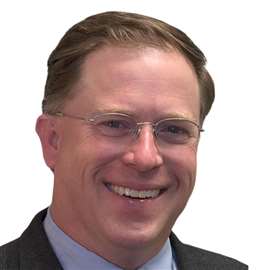
