Read this article in French German Italian Portuguese Spanish
Advances in battery technology can make it attractive compared to hydrogen
08 December 2024
German battery expert Maximilian Fichtner told a Mission Hydrogen webinar that advances in battery technology are driving the industry forward compared to alternatives such as hydrogen.
In a recent Mission Hydrogen webinar, Maximilian Fichtner, director of the Center for Electrochemical Energy Storage Ulm-Karlsruhe (CELEST) in Germany, noted that hydrogen fuel faces obstacles in competing with battery electric (BE) technology in vehicles and equipment. These include lifecycle greenhouse gas (GHG) emissions, energy efficiency across the supply chain and cost per kilometer.
In the interest of further explaining what those championing hydrogen are up against, Fichtner addressed the various technological advancements in batteries for vehicles and mobile equipment.
Lithium-Ion Trends
Addressing the well-known lithium-ion battery, he said, “Since the market introduction, which was in 1991, the energy density was raised by a factor of four. The costs went down by a factor of 18.”
Fichtner cited data from the Materials Research Society’s December 2015 issue of the MRS Bulletin that indicated growth in gravimetric energy density for lithium-ion batteries from approximately 75 Wh/kg in 1991 to about 250 Wh/kg in 2015. That same data showed costs declining from more than $3000/kWh in 1995 to approximately $400/kWh in 2015.
Fichtner added that over the last 10 years alone, lithium-ion costs have seen a 90 percent decline — a reduction that continues.
Improving Sustainability
According to Fichtner, it is developments like these that have had a significant impact on innovations made by the battery industry. One of these concerns sustainability.
“In the past, we were always driven to develop better batteries — more energy, faster charging, higher safety, longer lifetime — meaning we were looking for better materials and [to] develop better battery designs,” Fichtner said. “Meanwhile, because there are so many batteries and the [prospects are] enormous, we need to put that on a sustainable materials basis.”
According to Fichtner, much of the world is developing sustainable batteries based on nontoxic raw materials that can be recycled — a development that means completely new battery types.
Cathode Chemistry
For starters, Fichtner said that cobalt in the form of cobalt oxide (CoO2), which had initially been used in making cathodes for batteries, has since been phased out.
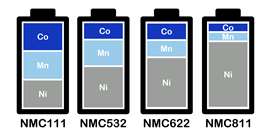
“You still have that in cell phones, sometimes laptops,” he said. “It’s not a good idea if you want to build large batteries, and this is because it’s expensive, it’s toxic, it comes particularly with [troublesome] mining conditions, and then it also can cause some critical safety situations.”
The U.S. Centers for Disease Control’s Toxic Substances Portal said cobalt can be harmful when individuals are exposed in large amounts. It also cited agencies around the world that have said the element is likely carcinogenic.
Additionally, information on the Global Battery Alliance website, which has introduced the idea of battery passports, said that cobalt mines in the Democratic Republic of the Congo have been linked to child labor and other human rights abuses.
To move away from cobalt, Fichtner said that battery makers have used nickel and manganese as a partial replacement, creating nickel/manganese/cobalt oxide (NMC) compounds that are commonly combined with lithium in battery creation.
“The first step was that there was only one-third cobalt left,” Fichtner said, referring to a composition typically referred to as NMC 111. “And then it was 20 percent left (NMC 622), and then 10 percent left (NMC 811).”
Other cathode formulations have been introduced since 2020 that have eliminated cobalt altogether, Fichtner said. These include lithium iron phosphate (LFP), so-called NMX layered oxide cathodes that use nickel and manganese and lithium manganese oxide (LMO) cathodes.
Evolving Anode Materials
Materials making up battery anodes have similarly changed. Fichtner said that while petrol coke and natural graphite had been and continue to be used, synthetic graphite has begun to make inroads.
“Synthetic graphite came into play because natural graphite comes mostly from China, and we want to make ourselves independent,” Fichtner said.
He added that the future will likely see pure carbon replaced in part by silicon.
“Silicon alloys with lithium, and has 10 times higher capacity than lithium,” Fichtner said. “However, it expands and shrinks, so you cannot use it in a pure form. But you can make composites out of it, and you can boost your capacity of the batteries by 40 percent.”
Battery Cell Improvements
These changes in battery chemistry have also made it possible to improve battery cell designs.
“It was found that the classical setup of a battery, which was kind of carved in stone for decades, can be changed,” Fichtner said.
One approach has been to eliminate the anode completely, as Fichtner said it had a relatively low storage capacity while occupying significant space. Called “anode-free” or “zero excess” cells, Fichtner said the lithium is placed directly on the copper collector, creating lithium metal.
“On the laboratory scale, the first cells already have energy densities of 710 or 712 Wh/kg,” Fichtner said, adding that this is roughly double the energy density of current lithium-ion batteries on the market, which come in at 340 to 350 Wh/kg. While no companies have yet commercialized this technology, Fichtner said a Chinese company, Tailan New Energy, has claimed to be working on it.
“Interestingly, if you take such a cell and put it in a regular battery design that we use at the moment — replace our battery cells, but by this kind of cell — you would have a driving range of 1900 km,” Fichtner said.
He added that Samsung is working on a new battery design that borrows the zero excess anode technology and combines it with what is called a cell-to-pack design.
“The cells are much more efficiently designed and packed,” Fichtner said. “And if you combine both, then they claim they get 500 Wh/kg. This is two times higher capacity compared to the state-of-the-art. They can charge a 900 km range in nine minutes. They claim a 20 year warranty [and] it contains no combustible liquids. They say it’s currently tested in battery vehicles, and they want to mass produce it from 2027.”
Cell-to-Pack Design
Regarding the advent of that cell-to-pack technology, Fichtner explained that today’s battery typically contains 12 modules of 12 battery cells each, with each cell being roughly the size of a large chocolate bar.
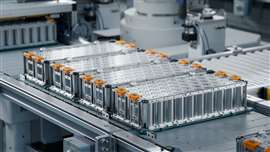
“The problem is this setup, this construction, contains only 25 to 30 percent active storage material,” Fichtner said. “The rest is packaging, containers, wires, whatever.”
Some Chinese manufacturers began addressing this issue by making the individual cells significantly larger, “not the size of a chocolate bar, but the size of a board,” Fichtner said. The result was the cell-to-pack design.
“You have 1.2 m-wide cells that are just clicked into a frame without extensive wiring,” he said. “They gain about 30 percent of space for the active material inside such a construction. At the same time, the number of parts that is required to fabricate the battery is reduced by 40 percent.”
Fichtner added that the more space-efficient design makes it possible to use other battery cell materials, such as LFP, which are sometimes less desirable in the current battery pack configuration.
This new cell-to-pack design was adopted in 2020 by Chinese automobile maker BYD with a 600 km range. China’s Geely has also introduced a car with this battery pack design having a 1000 km driving range.
POWER SOURCING GUIDE
The trusted reference and buyer’s guide for 83 years
The original “desktop search engine,” guiding nearly 10,000 users in more than 90 countries it is the primary reference for specifications and details on all the components that go into engine systems.
Visit Now
STAY CONNECTED



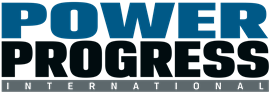
Receive the information you need when you need it through our world-leading magazines, newsletters and daily briefings.
CONNECT WITH THE TEAM
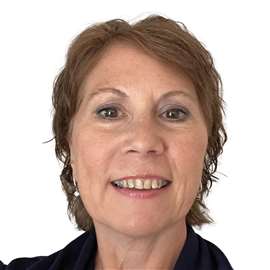
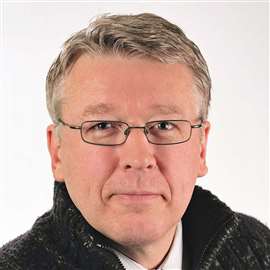
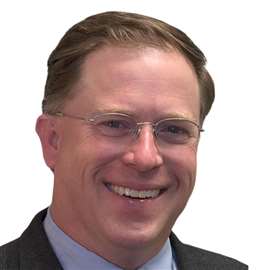
