Read this article in French German Italian Portuguese Spanish
Investing in Facility Features for Employee Satisfaction and Retention
10 January 2024
Every manufacturer wants facilities that are “state-of-the-art.” But what does that even mean? In this first of a three-part series, we examine what makes a facility an enjoyable place to work.
When Bobcat recently announced its plans to build a new manufacturing plant in Mexico, it described the planned manufacturing technology as “state-of-the-art.” John Deere used that same phrase in its August 2023 announcement of the new battery plant it is building in North Carolina. “State-of-the-art” is one of those catchphrases companies often use to imply they are investing in the latest and greatest technology — on the cutting edge. Regarding a manufacturing facility, however, what does “state-of-the-art” really mean?
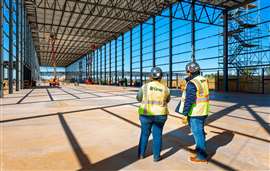
“I think it varies per sector, per person you talk to,” said Marcus Taylor, vice president of business development for Gray, a family-owned design-build firm based in Lexington, Ky. One of Gray’s projects is Kubota’s new manufacturing plant in Gainesville, Ga. “The one thing we see just with today’s market climate is that most decisions are easily revolving around a couple of things: either a company initiative or dealing with the actual workforce.”
Taylor added that for the latter, “state-of-the-art” relates to a facility that makes employees want to come into the building — something particularly important in today’s remote-work environment. It’s also important as manufacturers vie for skilled workers in an increasingly tight labor market.
“You’re trying to get people to actually want to come back to that environment, especially manufacturing, which is traditionally a very tough environment to work in,” Taylor said. “A lot of that is driven by what’s the actual feel of that manufacturing space. Does it feel like an old-line manufacturing facility, or does it feel like something that’s more modern, more innovative, that employees enjoy the work environment.”
Luxuries No More
According to Taylor, this reality means manufacturers today must invest in more capital-intensive building features to keep employees happy and avoid turnover — investments that in the past would have been considered luxuries. “Some are doing that in creative ways, whether they’re adding different forms of the old school cafeteria, which are vending-machine-type solutions to actually having full kitchens where you’re getting a fresh meal.”
On-site childcare is another benefit manufacturers are investing in. “It’s a big issue in today’s market,” Taylor said. “Whether that’s a shared solution within a region or industrial park or having some source there locally.” He added that for bigger manufacturers — those with 500 to 1000 employees, for example — finding a childcare solution can offset some of the challenges their employees face in coming into the workplace.
Plant Floor Particulars
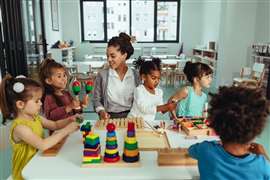
Not every employee has the option of working from home — namely those on the manufacturing floor who are the “boots on the ground” at the facility daily. Taylor said it’s important to provide them with amenities that make their work experience as enjoyable and comfortable as their counterparts in the office.
“It goes back to the environment,” he said, adding that items such as high-volume, low-speed (HVLS) fans, while not a replacement for air conditioning, do ensure superior air movement, “which makes it feel like it’s a much better place to be working in.”
Investing in more comfortable break areas is another trend on the manufacturing floor. “You’re seeing more spot break areas within the actual plant layout that are like, ‘Hey, your team has this area that you can do your team meetings, or when you have your downtime, this is your space to make your own.’”
Something for Everyone
Certain exterior amenities can benefit employees of all stripes, Taylor said. “You used to have a lot of walking trails and more physical spaces that you’re implementing that allow employees, either before or after, to have that so-called ‘sanity break’ to where they can go out and enjoy it before going back in on their shift change or after lunch. They’ve got a few minutes that they can decompress, so to speak, then get back to kind of the actual production side of things.”
He added that such exterior amenities are dependent upon a facility’s location.
Justifying the Cost
Given that there was a time when companies chose not to invest in such features, calling them luxuries instead of necessities, Taylor said it’s important to balance the cost of these investments with their return.
“You start running those cost models, and you try to have those tradeoffs,” he said. “So this is going to drive initial cost here, but if it does give you better employee retention, that does justify the additional capital request that you need to go back for or pull from some other bucket of money that was allotted for a different group.”
According to Taylor, Gray works through that balancing act with their customers, providing them with a menu of solutions they can implement based upon their goals. “If you kind of plug-and-play some of these items, you keep your total capital offer that you’re looking for in line.”
Check back for Part 2 of this series: a discussion of the kind of manufacturing technology that makes a manufacturing plant “state-of-the-art.”
POWER SOURCING GUIDE
The trusted reference and buyer’s guide for 83 years
The original “desktop search engine,” guiding nearly 10,000 users in more than 90 countries it is the primary reference for specifications and details on all the components that go into engine systems.
Visit Now
STAY CONNECTED



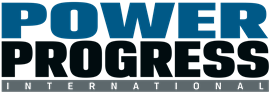
Receive the information you need when you need it through our world-leading magazines, newsletters and daily briefings.
CONNECT WITH THE TEAM
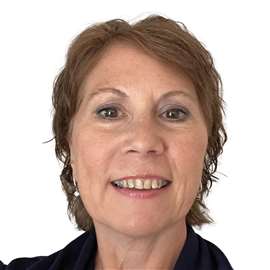
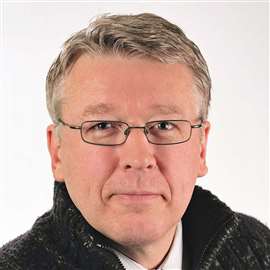
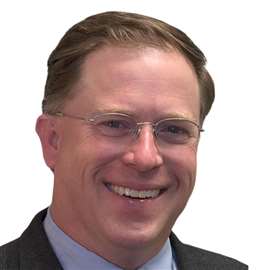
