Read this article in French German Italian Portuguese Spanish
Bollinger designs commercial EV truck from ground up
07 May 2024
A renovated, old three-bay garage in Hobart, N.Y., was the birthplace of a unique ground-up vehicle design from a small team of developers led by Robert Bollinger back in 2015. The team spent two years developing what would become Bollinger Motors’ first working electric truck prototype – the electric all-wheel-drive B1 Class 3 sport utility truck.
More than 3,000 orders were placed overnight following the design’s debut at a Classic Car Club Manhattan event in New York City, prompting the fledgling company to move to Oak Park, Mich. (just north of Detroit), to expand the engineering team and prepare a new design for production. The company developed second-generation B1 and B2 vehicles before shifting gears in favor of commercial truck development.
Bollinger Motors showed its first Class 5 vehicle platforms at the 2022 ACT Expo, and just months later, unveiled the B4 chassis cab, a Class 4 electric truck. A mere seven days after the unveil, on Sept. 8, it was announced that Mullen Automotive, an emerging electric vehicle (EV) manufacturer, had acquired a 60% controlling interest in the company.
Poised for production
With the acquisition, the two companies are now working together to put Class 3 through 6 commercial trucks into production. This will eventually be followed by the start of production of the B1 and B2 programs.
The B4 chassis cabs will be the first commercial trucks to roll off the assembly line, starting in Q3 2024. “We’ll have a limited production for the 2025 model year due to being in Q3, then we’ll be in full production for 2025,” said Jim Connelly, chief revenue officer, Bollinger Motors.
The B4 is a ground-up truck design offering maximum cargo volume, “unlimited adaptation capability” and a priority on safety, Bollinger stated. The cab-forward configuration ensures optimal visibility and frees up space behind the driver for additional cargo. The vehicle can be custom configured to a fleet’s duty cycle needs, with clean, unobstructed frame rails allowing for easy mounting and upfit adaptation. All drivetrain components are packaged inside the rails.
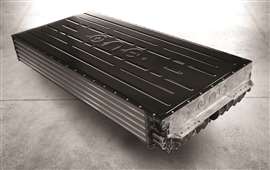
The B4 has a 15,500-lb. GVWR, a 158-in. wheelbase, comes in 16- to 18-ft. body lengths and can handle a payload of 7,325 lb. It is rated at 363 hp and 702 ft.-lb. of torque, with high-voltage components operating on an 800V platform derived from two battery packs with a combined 158 kWh of power. A range of 110 to 200 miles is available per charge, depending on the load. AC Level 2 charging (0-100%) is possible in nine hours with DC fast charging capability of 1.5 hours.
“We have regenerative braking so the range will depend on whether [the application is] city, urban type or highway,” Connelly explained. “If you’re on a highway and you’re not braking and recharging the battery, then you’re going to get less of a battery range on that vehicle than if you were in the city doing local stops and so forth.”
Finding the “sweet spot”
Connelly described the B4’s range of up to 200 miles as the “sweet spot” for medium-duty EV applications.
“The electric solution isn’t the solution for everybody. It’s going to depend on how the company uses those vehicles. If you’re off site in Utah and you drive 400 miles to get somewhere, it’s probably not a solution as of today,” he acknowledged.
However, he said data shows local delivery, landscaping and similar applications typically drive around 100 miles a day before returning the vehicle to the shop or yard at the end of the workday. “From a range perspective, based on what we see and the customers are targeting, it will fit that niche,” said Connelly. “Now, will they be able to convert 100% of their fleet? Probably not. If they’re a utility and they do urban and some rural customers and they end up being a couple hundred miles away from where they need to be, it’s probably not the solution.”
But a lot is dependent on available infrastructure. “Are there depots on your route where you can do kind of a fast recharge? There are providers that we partner with that provide mobile charging solutions,” Connelly noted. This could be a solution for contractors on jobsites, bringing charging services directly to projects. “It really all depends on the application. When we go in and talk to customers about our product, we also want to know about their driving patterns so we can provide some type of a recommendation for that charging solution.”
Supply partnerships
Bollinger’s all-electric platforms and chassis cabs for commercial vehicles are assembled by manufacturing partner Roush Industries, in Livonia, Mich., just 20 miles from Bollinger headquarters.
“We partnered with Roush to actually build our vehicle, but all of the technology is our design,” said Connelly. “The way we go to market is a little bit different than other startups. Some of the startups are trying to be everything for everybody. They try to build their own batteries and everything. We looked at who does those particular things [well] in the industry.”
That includes working with Our Next Energy (O.N.E.), in nearby Novi, as a battery pack supplier. “We use a lithium iron phosphate (LFP) battery, so all the stuff you hear about in the industry about thermal events happening in vehicles – you’re not going to have that type of issue,” Connelly said. The ONE Aries LFP chemistry also contains no nickel or cobalt for increased durability and to facilitate daily charging up to 100%.
“I think a lot of the other OEMs are moving to that kind of solution, but we’re already there,” Connelly said. “There are trade-offs. There are positives and negatives with every solution that you provide.”
Bollinger developed its own thermal management system for the battery packs. “The system is our own engineering,” Connelly said. “Our system does heating and cooling of the battery pack. It regulates the batteries from a temperature perspective so there isn’t really that extreme that could degrade your battery.” Bollinger also developed its own DC-DC charging solution.
However, rather than reinvent the axle, so to speak, the company chose to incorporate Dana e-axles into the new trucks. “Dana’s a reputable name in the business from the automotive perspective,” Connelly said. “From an engineering perspective, for [the B4], the e-axle’s probably over engineered. This particular e-axle would also be able to power a Class 6. So, as we move [upward in size class], it can handle that.
“From the durability of this system, for the capability of the B4, it definitely can handle whatever gets put on it,” he added.
A 10-kWh/13-hp Terzo e-PTO is an available option to handle hydraulic power assistance needs.
A positive start
In January, the B4 chassis cabs were still undergoing final tests prior to production but pre-orders had already gotten off to a positive start. Mullen Automotive announced that Bollinger Motors had already received orders for 40 of the B4 chassis cab electric trucks that month, with a total order value of roughly $6 million.
In March, the company added two more dealership groups with locations spanning seven states. And more recently, the company qualified for federal clean vehicle tax credits for the B4 chassis cab of $40,000 per vehicle under the Inflation Reduction Act, making the new electric vehicle an even more attractive option for fleets seeking to explore electric solutions.
POWER SOURCING GUIDE
The trusted reference and buyer’s guide for 83 years
The original “desktop search engine,” guiding nearly 10,000 users in more than 90 countries it is the primary reference for specifications and details on all the components that go into engine systems.
Visit Now
STAY CONNECTED



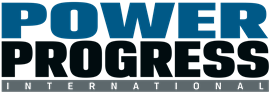
Receive the information you need when you need it through our world-leading magazines, newsletters and daily briefings.
CONNECT WITH THE TEAM
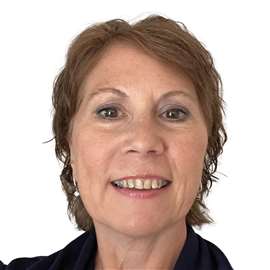
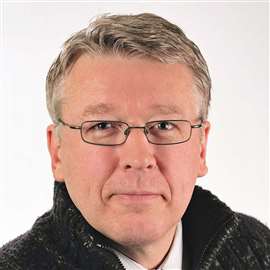
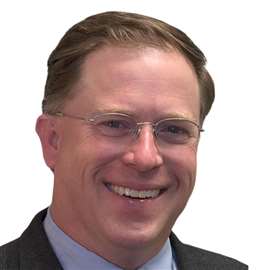
