Read this article in French German Italian Portuguese Spanish
Multiquip’s latest concrete finisher takes a two-engine approach
08 April 2025
The design of the MD105 trowel helps contractors get to work faster and provides flatter surfaces.
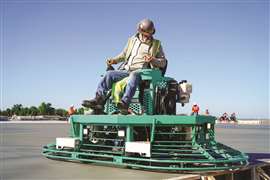
Warehouses are popping up everywhere along the Chicago area’s I-80 and I-55 corridors, and many of them are so long that they appear to follow the curvature of the Earth. But inside those facilities, armies of robotic narrow-aisle lift trucks and other machinery require concrete floors that are engineered to extremely high tolerances. When it comes to the construction of concrete slabs, there are flat floors and then there are super flat floors.
High F-Numbers
Architects use F-numbers to specify the flatness and levelness of the finished concrete slab. Floor flatness (FF, which counts bumps and grooves in the surface) and floor levelness (FL, which looks for slopes and pitches) are calculated from different measurements. The higher the final number the better the final product.
Lift trucks and similar machines are considered “defined traffic” and get their own set of floor specifications: F-min. They also require super flat floors, which according to the American Concrete Institute requires an F-min number greater than 100. For concrete finishing crews, having the right technique and selecting the right equipment is critical to achieving those F-numbers quickly and efficiently.
“Warehouses and distribution centers benefit from high tolerance concrete floors,” said Jon Williamson, director of Marketing, Multiquip Inc. “In addition to improved durability, the robotic forklifts that pick merchandise operate on software that directs the machine to a specific location to select an item. Deviations from specified tolerances impact their performance. Our engineering team at MQ Whiteman understands the role our machines have in helping contractors meet or exceed job requirements.”
Multiquip is a diversified manufacturer of construction equipment and generator sets. Through its Boise, Idaho-based MQ Whiteman brand, it produces a broad range of concrete finishing equipment. The company introduced its latest ride-on trowels, the mid-series 8-ft.-wide MD80 and 10-ft.-wide MD105, during January’s World of Concrete show in Las Vegas.
Dual Engines
Regarding the MD105, the company said it was designed to be a high-production finishing machine with a lower operating weight. The lower weight helps reduce downward pressure on the slab surface, giving contractors the benefit of an earlier entry onto the slab and a broader finishing window. The machine uses two gasoline engines to help make those claims a reality.

“Concrete gets laid out wet, screeded off and then crews have to wait for a certain period of time for the slab to set before it can support the weight of a trowel and begin the finishing process,” said Jordan Carmean, product manager at Multiquip. “As engines got heavier the machines got heavier, too, so that the entry time to the slab kept getting pushed back. That makes it difficult for these guys and puts them under a ton of pressure. So, we looked at how we could produce a lighter machine, allowing a contractor to get on the slab sooner and extend the working time. That’s where the dual engine concept came into play, and it got us where we needed to be with weight and horsepower.”
For the new model, Multiquip sourced two Honda iGX800 EFI gasoline engines rated 25 hp. The engines run two independent hydrostatic drive systems that operate two six-blade rotors, ensuring flatter floors. Electric linear actuators control the pitch and assure accurate blade angles. Besides saving weight, the company said that placing the engines on the left and right sides of the machine helped evenly distribute its weight and lower its center of gravity, reducing frame roll.
“The Honda engines helped us meet the horsepower requirement for that size of machine,” said Carmean, “and being able to displace that weight was very important because 10-ft. machines are historically very heavy units.”
An engine power management system controls both engines and the hydraulic pump that is connected to each one. Developed in-house, the electronic system automatically adjusts the pump’s strokes to allow the engine to operate at peak performance.
“The electronic system monitors the engine and drive system and adjusts from there,” said Carmean. “On the slab, both engines are running at the same time. The operator may not even know there are two engines because he’ll start the machine like normal. At startup, the system goes through a firing sequence, because to keep the weight low we have one starting battery that will fire one engine at a time. When the computer sees the first engine is fired up and running, it’ll go through a secondary firing sequence for the second engine. The program takes over from there. As it goes through the starting sequence, the foot pedal is deactivated for a short period of time. Once the second engine is running, the operator can take off and go to work.”
Fuel Choices Important
While the MD105 uses two gasoline engines, the new MD80 trowel uses a Vanguard EFI gasoline engine rated 40 hp to run its hydrostatic systems and pair of six-blade rotors. The upcoming MD82 trowel will get a Kubota engine rated 57 hp that is designed to run on gasoline or LPG.
The choice of fuel is a big one for end users as well as Multiquip, and there are a lot of factors that lead to making that decision. For example, when large data centers are built in Utah, the walls go up first so crews can work all year long regardless of the weather. That means that all the concrete pours and finishing will take place inside.
“Customers are looking for propane in a lot of instances, because they’re able to run a little bit longer without setting off all the air quality monitors. In our market, diesel was always preferred because of the torque, and diesel is much cleaner today. We still have some diesel lovers in the United States, and the UK was a big diesel market for us,” said Carmean.
“However, in trowels we see gasoline and propane taking over. Contractors are using propane in many areas because battery technology just isn’t there for the category of equipment we build. Ride-on trowels are under anywhere from 80% to 90% to even 100% engine load all the time. If you think about a car that must get over that initial demand for torque and then it’s rolling, going up and down hills, we’re going uphill 100% of the time.
“We can make battery-powered equipment, but you can’t have a trowel die out in the middle of the slab. There is also the weight of the batteries. We’re already fighting the constant weight gain of ride-on trowels, and when you put enough batteries on them to do the job that thing just sinks. When you look at what has been electrified in the market, such as lawn equipment, it makes sense, and there’s a place for it. But most of the large contractors that we’ve talked with don’t see the value in running batteries in our environment yet.”
The Whole Picture
“When you’re designing a trowel, there are so many different factors to take into consideration to make sure that the end product — a flat slab — is achieved,” said Carmean. “Engine selection and the placement of the engine are very important factors, but there’s 180 other important factors that must be considered to get everything to work cohesively together.”
Carmean started his career in Whiteman’s production department 20 years ago as a swing shift welder. From there he moved through various roles at the company, from a production lead on the assembly line to engineering and R&D. Much of that experience put him close to customers on job sites, which he said has provided him with a valuable base of knowledge about what customers need to be successful.
“We really pride ourselves on having flat-running machines. Other machines will rock and roll a little bit because of their center of gravity or because their component tolerances aren’t as tight as ours,” said Carmean. “Our machines run flat and true so they can produce flatter floors. On the big jobs, you’ll exclusively see our machines being used where they have high FF and FL number requirements.”
However, when designing a new machine, he said the engineering team takes a great amount of effort to consider the needs of another main customer: the people on Multiquip’s own factory floor. End users also benefit from that design methodology.
“We started from the ground up on these new trowels, and ensuring a commonality of parts to make sure our production was able to flow smoothly and easily as possible was very important,” said Carmean. “That benefits not only our assembly side but our customers, as well.
“We make sure you only need to grab one socket to take all the panels off versus having 10 different types of wrenches or a whole bag of tools to change an air filter. We pride ourselves on that attention to detail throughout the machine, and I think that’s what really, really sets us apart.”
POWER SOURCING GUIDE
The trusted reference and buyer’s guide for 83 years
The original “desktop search engine,” guiding nearly 10,000 users in more than 90 countries it is the primary reference for specifications and details on all the components that go into engine systems.
Visit Now
STAY CONNECTED



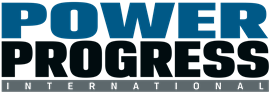
Receive the information you need when you need it through our world-leading magazines, newsletters and daily briefings.
CONNECT WITH THE TEAM
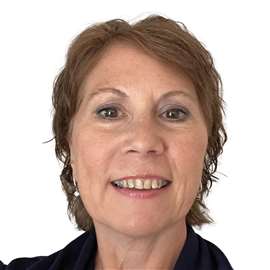
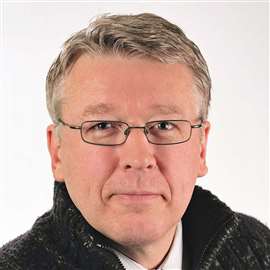
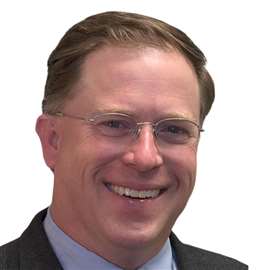
