Read this article in French German Italian Portuguese Spanish
Tariffs, U.S. elections cause uncertainty for battery supply chains
18 August 2024
China has lately been in power industry news on both sides of the Atlantic. The European Union, for instance, recently imposed provisional duties on Chinese biodiesel as part of EU investigations into biodiesel dumping in the region.
Additionally, in May in the U.S., the Biden-Harris administration imposed higher tariffs on a variety of Chinese goods, including electric vehicles and lithium-ion batteries. At the time, the White House said that “for too long, China’s government has used unfair, non-market practices.” However, despite the U.S. having its own anti-dumping laws, it did not cite dumping as a particular reason for the tariffs.
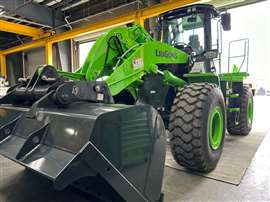
“I think there’s definitely a belief that it’s not always fair play when it comes to the pricing coming out of China and that it’s heavily subsidized in certain markets if it’s a strategic market for them that they want to really progress in,” said Alex Stapleton, chief commercial officer for Alexander Battery Technologies, a battery manufacturer based in the UK. He added that it was a move likely intended to drive battery solutions in the U.S. as well as support demand domestically.
“Right now, the tariff actually stands at 25 percent,” he said. “That’s for batteries supplied from China.” Stapleton added that the tariffs are not about delivering a battery without any components of Chinese origin. Instead, China cannot be the origin for the battery pack.
The tariffs could result in positive outcomes if they drive the behavior the U.S. government intends, Stapleton said. “A shorter supply chain where all those parts are coming from maybe not always the same country but certainly more local, less shipping, is a good start.”
Supply Chain Scrutiny
Nonetheless, the tariffs coupled with other uncertainties are making some companies look more closely at their existing supply chains.
“When it comes to supply chain risk management, it’s definitely on the table by those supply chain professionals,” he said. “You have to think about what could happen in different directions.” Stapleton cited the uncertainty of the U.S. presidential elections as well as the instability in Ukraine and the South China Sea as contributing to concerns about supply chains, saying it “keeps people on their toes and thinking about, really, can they get product?”
All of this has resulted in Alexander Battery having more conversations with clients about their supply chain. Stapleton said the company is “trying to encourage the wider market to really think about their supply chain over the coming period and think about [if] they need any diversification, where are they actually supplying to and what kind of track record does the supply chain currently have.”
Whether to Change
One question OEMs are going to have to ask themselves is if it makes sense to make a change to their battery supply chains, given the time and expense such a change could bring. One consideration is whether the battery can be recycled and if the supplier can help facilitate that process.
“We have examples whereby the battery life, the cycle life, of a battery pack might be five years,” he said. “It’ll be longer in an EV, but it might be five years. But the electronics might have a 15-year life. And throwing it all in the trash at the same time isn’t actually the smartest thing, environmentally or commercially.”
The choice to recycle is often driven by volume.
“It’s very difficult to do if you’re moving 500 pieces a year, but quite easy to do and worthwhile to do if you’re moving 50,000 pieces a year,” Stapleton said. “That’s probably where the challenge is.” He added that in volume, there are financial savings to be made on top of the environmental benefits.
Design for Recycling
“If you make that conclusion that you’re going to put the time and effort into that change, it would really make sense to look at the design of the pack,” Stapleton said, “because there are designs now and technologies now that allow you to make that battery pack more recyclable in its design.”
For example, Stapleton said a recyclable battery is one that can be taken apart relatively easily.
“You don’t want a welded pack, where everything’s welded together, which would be a very traditional way of making a battery,” he said. “These days, there are technologies that allow you to build a kind of unwelded pack, where no welding is necessarily used.”
Stapleton said this approach also means working with a supplier to have the battery casing removed, have the battery cells sent off to a third-party recycling specialist and retaining the expensive electronics for reuse.
When to Recycle
For manufacturers wondering how best to determine when a battery pack has reached the end of its life and is ready to be recycled, Stapleton said technology can help.
“With the strong IoT (Internet of Things) platforms that are in place now, ultimately if you do a bit of work at the front end, you can have an app,” he said. “You can have a QR code. You can have the battery telling you, hey, it’s time to send me back.”
In any case, Stapleton said that the second half of the year is the time for U.S. OEMs to be evaluating their battery supply chains.
“I don’t think people are going to make decisions before Nov. 5 [U.S. presidential election day], but I think you want to arrive at a planned destination, not an unplanned destination,” Stapleton said.
POWER SOURCING GUIDE
The trusted reference and buyer’s guide for 83 years
The original “desktop search engine,” guiding nearly 10,000 users in more than 90 countries it is the primary reference for specifications and details on all the components that go into engine systems.
Visit Now
STAY CONNECTED



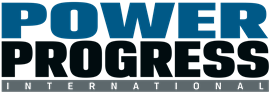
Receive the information you need when you need it through our world-leading magazines, newsletters and daily briefings.
CONNECT WITH THE TEAM
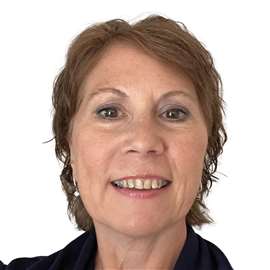
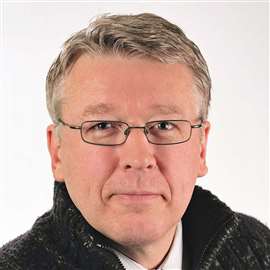
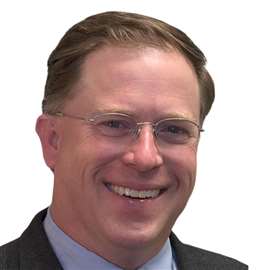
